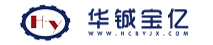
目前,油田產(chǎn)生的含油污泥主要來自兩個(gè)方面:一是在集輸、處理過程中沉積在各類容器、油水儲(chǔ)罐和回收水池等地面設(shè)施中,定期產(chǎn)生的含油污泥,這類設(shè)施一般包括:污水沉降罐、除油罐、油罐、電脫水器、回收水池、氣浮和過濾反洗等。二是由于油井作業(yè)、集輸油管道腐蝕穿孔等產(chǎn)生的落地污泥。
目前,油田污泥產(chǎn)生后基本上采取直接掩埋或就地固化的處理方式,由于含油污泥已被列入《國(guó)家危險(xiǎn)廢物目錄》中的含油廢物類,且污泥中往往含油重金屬等有害物質(zhì),如果不進(jìn)行無害化處理,不僅造成石油資源的浪費(fèi),同時(shí)也會(huì)對(duì)環(huán)境產(chǎn)生放射性污染。其中第一類污泥約占總量的85%以上,這里主要研究采出水處理站(水區(qū))處理過程中產(chǎn)生的污泥。
一、含油污泥特征及處置標(biāo)準(zhǔn)
采出水處理站具有采出水處理和注水功能,并管轄2條調(diào)水線,主要負(fù)責(zé)含油污水的凈化處理、調(diào)水以及注水任務(wù),采出水設(shè)計(jì)處理能力5500m3/d,目前處理量3500m3/d。該站采出水處理工藝為氣浮+流砂裝置,并配套負(fù)壓排泥、浮筒收油、電解鹽殺菌等輔助工藝。油區(qū)來水先進(jìn)入4具700m3沉降罐進(jìn)行沉降,沉降后進(jìn)入2具700m3調(diào)節(jié)罐,經(jīng)提升泵,進(jìn)入氣浮流砂過濾裝置進(jìn)行處理,合格污水進(jìn)入3具500m3注水罐;再經(jīng)喂水泵、注水泵、配水間、到單井,再由單井進(jìn)入地層。
油田含油污泥來源廣泛,組分也非常復(fù)雜,一般含有大量老化油、蠟質(zhì)、瀝青質(zhì)、膠體、固體懸浮液、細(xì)菌、鹽類等,還包括生產(chǎn)過程中投加的各種藥劑。在實(shí)驗(yàn)室條件下,將該站氣浮、過濾反洗和沉降、調(diào)節(jié)罐內(nèi)產(chǎn)生的含油污泥用石油醚進(jìn)行清洗后,經(jīng)干燥、稱重等過程,測(cè)試含油量、含水率和固含量。測(cè)試分析顯示,3種污泥每天產(chǎn)泥量大概為375m3,污泥含油在1%~15%,含水率在93%~98%,含固體懸浮物在1%~10%,其特點(diǎn)是含油、含固體懸浮物高且很不穩(wěn)定,雜質(zhì)多,處理難度大。
經(jīng)有機(jī)溶劑萃取后,用放射性射線分析儀對(duì)以上這幾種污泥來源中重金屬含量進(jìn)行測(cè)定,可以看出該站污泥中六種重金屬(Zn、Cu、Ni、Pb、Cd、Cr)含量均小于《農(nóng)用污泥中污染物控制標(biāo)準(zhǔn)》(GB 4284-1984)中相應(yīng)重金屬排放含量控制的限度,故在后續(xù)處理過程中無需考慮重金屬無害化處理。
取該站對(duì)應(yīng)區(qū)塊的普通原油與該采出水處理站污泥樣品中分離出的原油進(jìn)行對(duì)比,按照GB/T 2538-1998《原油實(shí)驗(yàn)法》、SY/T 5119《巖石中可溶有機(jī)物及原油族組分分析》中的測(cè)試方法對(duì)原油物性進(jìn)行測(cè)定。結(jié)果證明,污泥分離出的原油只是在含蠟量和膠質(zhì)瀝青含量上有所增多,造成密度、黏度和原油凝固點(diǎn)有所上升,但與原油品性質(zhì)差異不大,應(yīng)該對(duì)污泥進(jìn)行資源化處理,回收其中的油組分。
在《國(guó)家廢棄物》名錄中,雖然將含油污泥定為危險(xiǎn)固體廢物,但并沒有處理后定量的指標(biāo),現(xiàn)在含油污泥的處理多依照GB 4284-1984,要求土壤中含油量小于或等于3000mg/Kg(即3‰);黑龍江省地標(biāo)DB 23-2010《油田含油污泥綜合利用污染控制指標(biāo)》將處理標(biāo)準(zhǔn)分為兩種,其中農(nóng)用污泥與GB 4284-1984的要求一致,另外用于墊井場(chǎng)和通井路的污泥要求含油量小于或等于20000mg/Kg(即2%)。
二、主體工藝
采用熱洗+微生物+疊螺脫水處理技術(shù),整個(gè)處理工藝分為三個(gè)部分:預(yù)處理系統(tǒng)、生化處理系統(tǒng)和污泥脫水系統(tǒng)。
1.油泥分離劑室內(nèi)試驗(yàn)
含油污泥的熱洗藥劑種類很多,一般要求熱洗藥劑滿足兩個(gè)條件,一是在攪拌狀態(tài)下可降低油水界面張力,增加乳化效果;二是在靜置狀態(tài)下,加速油水分離。挨次選用十六烷基三甲基氯化銨、鹽酸、聚丙二醇溶于水中,恒溫反應(yīng)1~2h后加入過硫酸鹽溶液,在恒溫微波2~3h,得到油泥分離劑,通過攪拌等機(jī)械作用,使生物油泥分離劑與污泥充分混合均勻,加速油、水、泥三相分離。
①劑泥比對(duì)污泥分離效果測(cè)定。取污泥100g,分別按照1:1,2:1,3:1,4:1,5:1,6:1,7:1,8:1的劑泥比加入配置好的油泥分離劑,在實(shí)驗(yàn)溫度40℃,攪拌速率300r/min,攪拌時(shí)間30min后,再用石油醚清洗污泥,測(cè)定污泥中原油回收率及固含量。結(jié)果顯示,原油回收率先隨著油泥分離劑計(jì)量的增加而上升,而后逐漸下降,污泥中固含量先減少后增加,主要是由于隨著藥劑劑量增加,藥劑中的水含量越多,在攪拌的作用下會(huì)與污泥中的油形成水包油的狀態(tài),加速乳化,反而不利于油、泥、水的三相分離。在劑泥比3:1的情況下,原油回收率可達(dá)93%,固含量為3.6%,因此合適的劑泥比為3:1。
②不同實(shí)驗(yàn)溫度下污泥分離效果測(cè)定。不同的實(shí)驗(yàn)溫度對(duì)油、泥、水三相之間的界面結(jié)合力和界面強(qiáng)度影響很大。較攪拌速率和攪拌時(shí)間相比,對(duì)污泥的分離效果影響更大,在劑泥比3:1,攪拌速率300r/min、攪拌時(shí)間30min的情況下,選擇實(shí)驗(yàn)溫度30、35、40、45、50、55、60、65℃進(jìn)行測(cè)定。結(jié)果顯示,隨著溫度的升高,原油回收率逐步上升,而后趨于平穩(wěn),固含量逐步下降,在55℃以上又逐漸增加,主要是由于溫度的上升,有助于藥劑和污泥之間的結(jié)合。同時(shí),可加速破壞分子之間的氫鍵作用,但溫度上升到一定程度后,污泥的流動(dòng)性反而加強(qiáng),固相和液相的分離更加困難。結(jié)果還顯示,由于后期需用微生物進(jìn)行生物處理,微生物菌種的溫度不宜過高,否則會(huì)影響菌種的培養(yǎng)和生長(zhǎng),因此選擇攪拌溫度為45℃。
③不同攪拌速率、不同攪拌時(shí)間下的污泥分離效果測(cè)定。在劑泥比3:1、攪拌溫度45℃、攪拌時(shí)間30min的條件下,選擇300、400、500、600、700、800r/min這幾種攪拌速率進(jìn)行原油收率和固含量測(cè)定。結(jié)果顯示,攪拌速率在600r/min時(shí),原油回收率極高,可達(dá)90%,固含量極低為2.2%,隨著攪拌速率的上升,原油回收率有所下降,固含量有所提高,主要是因?yàn)閿嚢杷俾蔬^高會(huì)加速固相和液相的乳化程度,因此攪拌速率在600r/min左右即可。
在劑泥比3:1、攪拌溫度45℃、攪拌速度600r/min的條件下,選擇30、40、50、60、70、80、90min這幾種攪拌時(shí)間進(jìn)行分離效果測(cè)定。結(jié)果顯示,隨著攪拌時(shí)間的增加,固含量先是大幅降低,在70min后趨于平穩(wěn),原油回收率先上升,之后在60min也趨于平穩(wěn),因此合適的攪拌時(shí)間為60~70min。
針對(duì)上述室內(nèi)試驗(yàn),將劑泥比設(shè)置為3:1,攪拌溫度45℃,攪拌速度600r/min,攪拌時(shí)間60~70min。
2.熱洗處理系統(tǒng)
將氣浮刮渣、沉降罐和調(diào)節(jié)罐底部污泥排至收集池,如遇污泥流動(dòng)性不好,可與回?fù)剿旌希⑼ㄟ^蒸汽加熱,使污泥流態(tài)化,然后用泵打入預(yù)處理裝置,在預(yù)處理裝置中投加高效生物油泥分離劑進(jìn)行熱洗。分離的油上浮至表面,通過收油機(jī)收至回收油罐,由于過濾器反洗產(chǎn)生的污泥含水率較高,一般不單獨(dú)處理,而是與下層水和污泥混合后進(jìn)入生物處理系統(tǒng)。處理后可將原先含油15%左右的污泥處理至含油小于或等于3%。
3.生物處理系統(tǒng)
設(shè)置生物處理系統(tǒng),經(jīng)預(yù)處理系統(tǒng)處理后的污泥與過濾反洗水混合進(jìn)入污泥生物處理系統(tǒng),在生物反應(yīng)系統(tǒng)中投加“倍加清”專性微生物菌種,經(jīng)過曝氣生物反應(yīng)后,專性微生物把泥、水中油、有機(jī)類污染物進(jìn)行生物降解,保持在30℃、150r/min的條件下培養(yǎng),經(jīng)過好氧處理30天,污泥、水含油率達(dá)到此階段的設(shè)計(jì)要求,處理后的污泥中油含量小于或等于3000mg/Kg,滿足了GB 4284的含油量要求。水進(jìn)入回收水罐回?fù)街燎凹?jí)處理系統(tǒng)或泵至污水處理系統(tǒng),污泥進(jìn)入后級(jí)污泥脫水系統(tǒng)。
4.污泥脫水處理系統(tǒng)
經(jīng)前級(jí)生物系統(tǒng)處理后排放的污泥含油量已很低,但含水率仍然在95%,如果直接拉運(yùn),體積龐大且費(fèi)用昂貴,需要進(jìn)行脫水處理,減少污泥體積。
疊螺式污泥脫水系統(tǒng)主要由疊螺機(jī)和加藥裝置組成。疊螺機(jī)主體是由固定環(huán)和游動(dòng)環(huán)相互層疊,螺旋推力軸貫穿其中組成,分為濃縮區(qū)和脫水區(qū),固定環(huán)和游動(dòng)環(huán)之間的濾縫以及螺旋軸螺距,由濃縮區(qū)至脫水區(qū)逐漸變小,加藥裝置由計(jì)量槽、絮凝混合槽和加藥泵組成。
運(yùn)行過程中污泥通過外力提升被輸送至疊螺污泥脫水系統(tǒng)的計(jì)量槽內(nèi),加藥泵根據(jù)污泥流量,按設(shè)定加藥量向混合槽內(nèi)投加絮凝劑,通過攪拌使污泥與藥劑在絮凝混合槽內(nèi)充分作用,形成礬花的污泥自流進(jìn)入疊螺主體,液相在濃縮區(qū)通過游動(dòng)環(huán)和固定環(huán)之間的濾縫排出,固相物質(zhì)截留在腔體內(nèi)部;螺旋推力軸在電動(dòng)機(jī)的帶動(dòng)下,推動(dòng)軸圓周外的多重游動(dòng)環(huán)上下運(yùn)動(dòng),使?jié)饪s區(qū)截留的固相物質(zhì),被螺旋軸推至污泥脫水區(qū),利用螺旋軸矩的不斷收縮,增強(qiáng)內(nèi)壓,使濾餅含固量不斷提高,在螺旋推力軸連續(xù)運(yùn)轉(zhuǎn)推動(dòng)下,液相連續(xù)分離流出,污泥不斷受擠壓脫水排出,從而達(dá)到污泥濃縮脫水的目的。
濃縮處理后的污泥加入助凝劑后進(jìn)入疊螺污泥脫水機(jī)脫水,使泥水分離,脫水后的水收集后進(jìn)入回收水罐,經(jīng)疊螺機(jī)脫水后污泥含水率在75%~80%,處理前污泥含水率為93%~98%,取97%,脫水后含水率按80%計(jì)算,體積可降低6.666倍,大大降低了外運(yùn)體積,且含油率為2%已達(dá)到了資源化的標(biāo)準(zhǔn)。
三、效果評(píng)價(jià)和效益分析
分別取連續(xù)8天不同時(shí)間段的污泥進(jìn)行取樣檢測(cè),經(jīng)油區(qū)沉降后污泥來樣含油量相對(duì)穩(wěn)定,平均在11366mg/Kg左右,泥中含油波動(dòng)不是很大,經(jīng)生物+疊螺機(jī)脫水處理技術(shù)處理后,泥中含油平均為958mg/Kg,平均去除率達(dá)到91.55%,滿足GB 4284中含油量小于或等于3000mg/Kg的要求,達(dá)到了資源化利用的條件。
四、結(jié)論
1.經(jīng)過一系列的室內(nèi)試驗(yàn),對(duì)油泥分離劑進(jìn)行了工藝參數(shù)優(yōu)化,將劑泥比設(shè)置為3:1,攪拌溫度45℃,攪拌速率600r/min,攪拌時(shí)間60~70min。
2.經(jīng)熱洗+微生物+疊螺脫水技術(shù)處理后的污泥達(dá)到了減量化、無害化、資源化的處理要求,滿足了國(guó)家和當(dāng)?shù)丨h(huán)保要求。
3.下一步要繼續(xù)針對(duì)鉆井、油水井作業(yè)、管道泄漏等的廢液、廢渣實(shí)施不落地回收,并進(jìn)行集中處理。
4.含油污泥處理技術(shù)多種多樣,單一技術(shù)往往很難達(dá)到預(yù)期效果,下一步要考慮多種技術(shù)的耦合,對(duì)污泥進(jìn)行分級(jí)、分階段處理,形成不同種類污泥處理的標(biāo)準(zhǔn)化工藝。