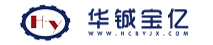
一、工藝流程
煤在高溫?zé)捊範(fàn)t中產(chǎn)生焦炭、煤焦油、氨水、苯、煤氣等產(chǎn)物,焦炭經(jīng)冷卻后直接煉鋼,而煤焦油、氨水、苯、煤氣等物質(zhì)經(jīng)除冷器降溫后進(jìn)入水汽分離器,將煤焦油、氨水、煤氣分離。由于煤氣的主要成分是硫化氫,煤氣進(jìn)預(yù)冷塔降溫至25~30℃后進(jìn)入再生塔,加催化劑、曝氣,產(chǎn)生泡沫硫,使用離心機(jī)泵將泡沫硫打進(jìn)臥螺離心機(jī)進(jìn)行固液分離,分離后的清液排入再生塔循環(huán)使用,分離后的硫膏經(jīng)加熱釜生產(chǎn)出成品硫膏。
二、離心機(jī)配置、工作原理、技術(shù)特性
1.1 LW520×2080離心機(jī)配置
1.1.1 組成
LW520×2080離心機(jī)是專門針對(duì)硫泡沫固液分離研發(fā)生產(chǎn)的臥式螺旋卸料沉降離心機(jī),離心機(jī)主要由主電機(jī)、副電機(jī)、轉(zhuǎn)鼓部件、螺旋部件、軸承座部件、機(jī)座部件、行星齒輪差速器等部分組成。其主要技術(shù)參數(shù)如下:
轉(zhuǎn)鼓內(nèi)直徑:520mm。
設(shè)計(jì)轉(zhuǎn)速:3000r/min。
分離因素:2620。
工作轉(zhuǎn)速:1800r/min。
主電機(jī)功率:55kW。
副電機(jī)功率:18.5kW。
1.1.2 工作原理
離心機(jī)的工作原理為利用離心力的作用,使具有不同比重的物體分開。含懸浮硫的硫泡沫經(jīng)由進(jìn)料泵,經(jīng)進(jìn)料管進(jìn)入離心機(jī)轉(zhuǎn)鼓內(nèi)部,在高速旋轉(zhuǎn)所產(chǎn)生的離心力的作用下,因固液二相存在比重差,而實(shí)現(xiàn)分層,比重較大的固體顆粒沉積在轉(zhuǎn)鼓內(nèi)壁上被螺旋輸送器不斷推出轉(zhuǎn)鼓出渣口,而分離后的清液則經(jīng)液層調(diào)節(jié)板開口溢流出轉(zhuǎn)鼓,螺旋與轉(zhuǎn)鼓之間的轉(zhuǎn)速差是通過差速器來實(shí)現(xiàn)的,轉(zhuǎn)速差的大小通過副電機(jī)進(jìn)行調(diào)節(jié),因此實(shí)現(xiàn)了離心機(jī)硫泡沫的連續(xù)分離。
1.2 技術(shù)特性
1.2.1 采用大長徑比技術(shù)
大長徑比可增加物料的沉降區(qū)域,延長物料在離心機(jī)內(nèi)的停留時(shí)間,使固形物去除率提高。
1.2.2 獨(dú)特的渦流式出料部位設(shè)計(jì)
螺旋卸料器的出料部位采用渦流式結(jié)構(gòu),符合液體力學(xué)的“雙S”結(jié)構(gòu)設(shè)計(jì)原理,可加速物料快速進(jìn)入轉(zhuǎn)鼓,縮短物料與液池接觸距離,減少進(jìn)料對(duì)已形成的分離固相的擾動(dòng),提高處理能力,避免螺旋內(nèi)的堵塞和進(jìn)料管抱死現(xiàn)象。在物料出口處堆焊碳化鎢硬質(zhì)合金,增加了螺旋體的使用壽命。
1.2.3 獨(dú)特的泡沫破碎裝置
由于大量泡沫的存在,直接影響了固體的回收率,針對(duì)這一特性,離心機(jī)配備了泡沫破碎裝置——漂浮物捕捉器。泡沫氣泡破碎后,附著在氣泡表面的固體顆粒發(fā)生了沉降,固體顆粒被螺旋體從渣相推出,從而提高了液相的回收率。
1.2.4 關(guān)鍵部件采用高性能不銹鋼材料
針對(duì)泡沫硫物料顆粒較細(xì)小、硫酸粒子含量較高等特性,為保證離心機(jī)運(yùn)行穩(wěn)定性和使用壽命,轉(zhuǎn)鼓部件采用高強(qiáng)度、耐腐蝕性更好的SAF2205,而螺旋部件采用316L材料。
1.2.5 先進(jìn)的雙電機(jī)雙變頻共直流母線和恒扭矩控制技術(shù)
離心機(jī)的主副電機(jī)各采用一臺(tái)高性能矢量變頻器控制,副電機(jī)在差速作用下始終處于發(fā)電機(jī)狀態(tài),由于采用變頻器共直流母線技術(shù),副變頻器能很好地將副電機(jī)產(chǎn)生的電能通過轉(zhuǎn)化供主電機(jī)使用,從而達(dá)到節(jié)能降耗目的。通過雙電機(jī)雙變頻控制技術(shù),可實(shí)現(xiàn)對(duì)離心機(jī)差速的無級(jí)可調(diào),具有反應(yīng)速度快,扭矩檢測準(zhǔn)確,扭矩控制穩(wěn)定,故障率低等優(yōu)點(diǎn)。
三、影響離心機(jī)分離效果的因素
1.1 轉(zhuǎn)速對(duì)離心機(jī)分離效果的影響
理論上,轉(zhuǎn)速越高,物料受到離心力越大,固體顆粒沉降速度越快,分離效果就越好。但對(duì)于硫泡沫物料,因其物料中所含灰份為70%左右,過高的轉(zhuǎn)速會(huì)加快螺旋葉片對(duì)分離物料的擾動(dòng),從而影響到渣、液二相的分離效果。經(jīng)過測試,較佳的轉(zhuǎn)速在1800r/min為宜。
1.2 液層深度對(duì)分離效果的影響
提高液層深度會(huì)降低液相中的含固率,增加固相中的含水率;降低液層深度則反之。對(duì)液層深度的調(diào)整需要從離心機(jī)分離后的渣相含水率與清液含固率綜合考慮。經(jīng)過測試,液層深度控制在159mm檔位,硫膏的含水率與清液的含渣率在較佳狀態(tài)。
1.3 轉(zhuǎn)鼓與螺旋轉(zhuǎn)速差對(duì)分離效果的影響
轉(zhuǎn)鼓與螺旋轉(zhuǎn)速差也就是差轉(zhuǎn)速度,差轉(zhuǎn)速?zèng)Q定了螺旋推料器的排料速度,在轉(zhuǎn)速恒定的情況下,差轉(zhuǎn)速增大,清液在被排出離心機(jī)之前經(jīng)過的路徑將增加,可以降低液相的含固率,但由于螺旋排料速度會(huì)加快而減少了固相部分在離心機(jī)內(nèi)的停留時(shí)間,從而影響到分離出的硫膏的干度。經(jīng)過測試,差轉(zhuǎn)速控制在14~16r/min,硫膏的含水率與清液的含渣率在較佳狀態(tài)。
1.4 處理量對(duì)分離效果的影響
處理量的調(diào)整是一個(gè)綜合過程,要根據(jù)處理效果和主機(jī)負(fù)荷來決定;經(jīng)現(xiàn)場分離調(diào)試,LW520×2080離心機(jī)的處理量在25m3/h時(shí),渣相含水率與液相含固率都處于較佳的分離狀態(tài)。
四、優(yōu)勢對(duì)比
與板框壓濾機(jī)相比較,臥螺離心機(jī)具有以下優(yōu)勢:
①板框壓濾機(jī)占地面積大,安裝調(diào)試復(fù)雜,維修費(fèi)用較高;而臥螺離心機(jī)占地面積小,安裝調(diào)試簡單,現(xiàn)場維護(hù)方便。
②板框壓濾機(jī)為間歇性工作,需要定期排渣和清潔濾布,工作效率低;而臥螺離心機(jī)在工作時(shí)的進(jìn)料、分離、卸料等工序是在密閉的環(huán)境中連續(xù)自動(dòng)進(jìn)行,工作效率高,現(xiàn)場環(huán)境好。
③板框壓濾機(jī)壓濾出的硫膏含水率在45%左右,液相含固率0.5%~0.8%;而臥螺離心機(jī)分離出的硫膏含水率≤40%,由于采用了特殊結(jié)構(gòu)的漂浮物捕捉器,分離出的液相含固率≤0.02%。
五、結(jié)語
通過在河北遷安中化煤化工、唐山達(dá)峰焦化等幾家國內(nèi)煤化工企業(yè)的分離實(shí)踐證明,無論從分離效果、處理量、液相純凈度,還是運(yùn)營成本、離心機(jī)穩(wěn)定性、可靠性,臥螺離心機(jī)都是一種較為理想的選擇。