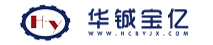
隨著經濟的發(fā)展,能源在人類生活中所占的比重越來越大。近年來,海洋石油資源的開采力度也在不斷加大,但因前期保護措施的不充分,造成石油泄漏事件時有發(fā)生。海洋油污染絕大部分來自人類活動,其中主要為船舶運輸、海上油氣開采及沿岸工業(yè)排污等。由于石油產地與消費地的分布不均,世界年產石油的半數(shù)以上將通過油輪運輸?shù)礁飨M地。這就給占地球表面71%的海洋帶來了油污染的威脅。特別是油輪相撞、海洋油田泄漏等一系列突發(fā)性事件,更是給人類社會造成了難以估量的損失。近年來,僅僅在我國境內發(fā)生的重大石油泄漏事故就高達多起,因其造成的經濟損失與海洋環(huán)境污染更是觸目驚心。
每年海上溢油量約占世界總產量的0.5%,因航運產生的石油污染物更是高達200萬噸,其中約1/3為海上油輪失事造成。我國每年海上溢油事故均超過500起,沿海地區(qū)海水含油量達標準水質6倍以上,海洋油污治理迫在眉睫。
傳統(tǒng)的油水分離技術主要有重力沉降法、液-液旋流法、氣浮法、吸附法、聚結法等。
傳統(tǒng)油水分離技術較注重浮油的清理,對環(huán)境造成的二次污染尚有欠缺。面對漏油造成的環(huán)境污染,必然會越來越受關注,發(fā)展新的漏油回收技術有望成為一個新的發(fā)展方向。近年來,隨著高分子薄膜、脂肪晶體、多孔疏水/親油材料(PHOMs)等新型高效的介質運用于油水分離,這類新型分離材料在外接泵的情況下,利用材料自身的疏水親油性能實現(xiàn)連續(xù)的油水分離,在修復溢油的同時,還能進行回收。傳統(tǒng)的做法是利用吸附材料吸附水面的油層,因此,吸附量受限于吸附材料自身的體積。新型分離材料可以很大程度上節(jié)約成本,油水分離效率更高,且不會造成二次污染。
1 傳統(tǒng)油水分離技術
油水分離過程大致可分為兩個步驟:
(1)從油水混合液中提取原油的原油除水過程。
(2)從含油污水中去除油和其他雜質的含油污水(含油率<1%)處理過程。傳統(tǒng)分離技術利用油的密度比水小(油浮于水的上方),先通過重力沉降、離心旋轉或氣浮法實現(xiàn)初步分離,再結合波紋板或活性炭進行二次分離。但儀器造價高、能源消耗量大且工作效率低,不適合大規(guī)模處理。
1.1 重力沉降法
重力沉降式油水分離法是利用油水密度差及不相溶性,在靜止或平衡流動狀態(tài)下油滴會以Stokes進行上浮。油滴上浮速度與油水兩相密度差和油滴粒徑平方成正比,所以傳統(tǒng)重力式分離器常通過結合波紋板對油滴的聚結作用增大油滴粒徑和在水中添加NaCl提高水相密度,增大油水兩相密度差,來提高油滴的上浮速度,從而提高分離效率。Pintor等通過測量植物煉油廠廢水分離過程中24h油脂和化學需氧量(COD)的濃度變化曲線,發(fā)現(xiàn)剛開始沉降時油脂和COD濃度下降非??欤?h左右達到平衡,能夠去除廢水中58%~90%的油脂,COD可降低90%以上。但重力式分離設備體型龐大且造價昂貴,分離效率相對較低,一般不作為單獨的油水分離手段。
1.2 液-液旋流法
液-液旋流油水分離法也是借助油水兩相的密度差,在油水混合液以一定壓力進入旋流器后,油水兩相由于受到不同程度的力,借助離心沉降作用達到分離目的。油滴粒徑與油水兩相密度差越大,越容易被分離。Xu等研究脫氣水力旋流器中氣泡聚結和破裂對分離效率的影響,當氣泡直徑從30μm變到100μm時,分離效率從29.67%增加到99.53%。液-液旋流法經過國內外專家多年的研究,取得了重大進展,正趨于成熟化規(guī)范化,在未來研究發(fā)展趨勢中,不僅要進一步的改進它的特性,如設備特性、介質特性及操作特性,也要提高分離系統(tǒng)的工作效率。
1.3 氣浮法
氣浮油水分離法是向水中通入微氣泡(有時還需要加入浮選劑或混凝劑),微氣泡進入水相后,使粒徑為0.25~25μm的油滴附著在氣泡上形成氣泡—油滴聚合體,這些聚合體在浮力作用下上升到液面,通過刮去表層泡沫實現(xiàn)油水分離。根據(jù)微氣泡產生的方式,氣浮法可細分為電解法、分散空氣法和加壓溶氣氣浮法。Al-Sabagh等采用溶氣氣浮法配合自制的乙氧基化破乳劑,研究pH、破乳劑濃度、進給速度和飽和壓力等因素對從天然氣中提取凝析油的影響,得出在pH值=2、150mg/L的破乳劑濃度、0.1L/min的進給速度和10psi的飽和壓力下,除油率高達99.9%。氣浮法的分離效率取決于氣泡與浮油的碰撞幾率,為了在較短的停留時間內能與浮油充分接觸,須增大氣泡的比表面積。因此,怎樣實現(xiàn)微氣泡粒徑的減小將成為研究方向之一。
1.4 聚結法
聚結油水分離法可分為三個處理階段:
(1)懸浮油滴接近已附著于聚結器之上的油滴。
(2)懸浮油滴與聚結器之上的油滴相黏附。
(3)油滴體積增大到一定程度,從聚結器表面脫落。
波紋板提供了油水兩相來回流動的曲折通道,使分散液滴產生聚結。油水混合物在板內流動時,其中的小油滴在運動時聚結變大,通過潤濕、吸附、聚結在波紋板的下表面形成油膜,沿表面脫落。Hou等對進液分布器的形式和傾角進行了研究。其試驗結果表明,在各種角度中,45°傾角安裝時液流較為平穩(wěn),而且此情況下液流寬度與容器寬度相當,較好地利用了封頭處容器的空間,提高了容器的有效利用率和油水分離效率。在聚結過濾裝置的設計改造方面仍要加強,對影響設備流動特性和分離特性的內部結構仍要不斷創(chuàng)新,例如在入口、布液和集液等構件上要減小液體的流動阻力。
1.5 吸附法
吸附油水分離法是將表面具有活性的親油粉末投入油水乳液中破壞乳液穩(wěn)定,將浮油吸入其中后實現(xiàn)油水分離?;钚蕴績炔亢写罅靠紫督Y構,其比表面積高達2000㎡/g,粉體活性炭是分離效果較好的吸附劑,在4、6、8m/h三種濾速下,吸附柱內粒狀活性炭對機油的吸附量為其吸附飽和量的20%~30%,在投加量達到12mg/L時,水中除油率可達90%以上。馬偉等采用聚乙烯醇與甲醛反應,結合發(fā)泡致孔法制備出三維網絡狀活性炭/有機復合材料。在工藝條件下吸附量達到活性炭的1.5倍左右,相對于粉末活性炭和塊體活性炭,所制柔性復合材料密度?。?.1977g/cm3),使用過程中可以完全漂浮在水面上,有利于吸附漂浮的油膜,方便回收再利用。傳統(tǒng)吸附法大多使用粉體活性炭,其分離效率固然較高,但從中回收漏油困難。因此,利用高分子泡沫基體承載粉體活性炭的復合技術,將成為制備新型分離材料的一種途徑。
2 新型油水分離技術
現(xiàn)基于高分子薄膜、脂肪晶體、多孔疏水/親油材料(PHOMs)的新型油水分離技術,可直接達到二次分離的效果,且基體材料體積小、成本低、效率高。其中基于PHOMs和外部泵的原位抽取分離技術,可實現(xiàn)連續(xù)從水表面采集原位油。這種自我控制的集油系統(tǒng)不僅大量節(jié)省技術成本、制備工藝簡單、反應條件溫和,同時具有優(yōu)良的兩相分離和石油收集能力,易于工業(yè)化生產。
2.1 膜分離法
膜油水分離技術是借助半透膜的選擇滲透作用,依據(jù)油水混合物中油滴分子的粒徑大小,在外加壓力或化學位差的推動作用下對混合物中油相或水相進行分離。按油滴在水中的粒徑大小劃分,可將其分為浮油(粒徑150μm),分散油(粒徑20-150μm),乳化油(粒徑<20μm),溶解油(粒徑<10μm)。
20世紀50年代以來,膜分離技術進入工業(yè)應用,在含油污水處理中,微濾膜(MF)(≥0.1mm)、超濾膜(UF)(10~100nm)、納濾膜(NF)(1~10nm)和反滲透膜(RO)(≤1nm)技術的應用越來越受到重視。常見的油水分離膜有超濾膜和微濾膜,均能截留乳化油及溶解油。Ullah等采用寬4μm、長400μm的鎳膜去除水中原油,鎳膜在不同頻率的振動下,其表面的剪切強度可變。測量結果表明,液滴運動程度與剪切強度成線性比例,分離效率高達92%。膜分離技術除以上兩種,還有一種復合膜,其將有機聚合材料與膜制造技術相結合。隨著科技的進步,膜分離技術在實際應用中不斷增加。其特點主要體現(xiàn)在精度高,易自動化,局限在于膜本身,膜在壓力下不可避免地會被栓塞、污染、斷絲,必須定期清潔舒塞,后期運營成本很高,且易二次污染。
2.2 冷凍/解凍法
冷凍/解凍油水分離法是利用水相中油相內含有脂肪晶體,該脂肪晶體具有深入水相刺破水液滴界面膜的特性,使得液體易于聚結,再借助油的冰點低于水的特點,在溫度為-20~-10℃時實現(xiàn)油水分離。其要求混合液穩(wěn)定性高、連續(xù)相黏度大,并且工藝較繁瑣,因此其不適用于工業(yè)油水分離,而適用于食品工程中的油水乳狀物的破乳。
在北方地區(qū),由于冬季低溫,生化處理的能耗非常高,且廢水中的有毒物質會對微生物的處理效果產生不利影響。作為一種廢水處理方法,冷凍法已有多名學者對其進行研究和探索。試驗中發(fā)現(xiàn)冷凍法對廢水的COD和色度有良好的去除效果。Mao等采用多級冷凍法處理含油廢水。在初始廢水中CODCr和p(NH3-N)分別為36400mg/L和73mg/L的條件下,經過8級冷凍處理,CODCr和p(NH3-N)分別降至430mg/L和2mg/L,去除率分別可達98.82%和97.72%;在相同COD的條件下,p(NH3-N)較高時,COD去除率較高。由此可知,無機鹽離子(如NH4+)的存在有利于有機物的去除。相對于其他水處理方法,冷凍法在環(huán)境影響、能耗、可靠性等方面均有優(yōu)勢。冷凍/解凍法的局限在于周期長,運用液氮速凍技術又對破乳不利,只有乳珠生長到足夠大尺寸時,才會在冷凍/解凍后徹底破乳、分相,達到理想分離效果。
2.3 原位抽取法
原位抽取法是在多孔疏水/親油材料(PHOMs)中插入一根導管結合外部泵抽取實現(xiàn)油水分離,這就要求材料具備一定的力學強度。其中PHOMs充當了過濾器的作用,富集水中的油相,并通過導管收集油相。聚氨酯(PU)海綿開孔率高且具有優(yōu)異的機械強度和獨特的耐水、耐油、抗溶劑的特性,常規(guī)PU海綿內部網絡孔洞約為1.2~1.5mm,其表面粗糙,可通過化學噴涂、原位聚合等方法構筑疏水表面制備出一種微型油水過濾器。Ge等將海綿浸泡于納米SiO2粒子改性的聚二甲基硅氧烷(PDMS)中一定時間后取出,在室溫靜置固化后,得到一種多孔疏水/親油功能海綿。通過納米SiO2-PDMS將親水性內表面修飾為憎水性,再結合外部泵的抽取能夠實現(xiàn)的連續(xù)油水兩相分離。Ge等將0.02g疏水性納米二氧化硅與0.02g聚氟蠟(PFW)超聲分散在20mL乙醇中,立即將聚氨酯海綿放入上述溶液。5min后,取出海綿,在130℃下干燥0.5h,就得到一種親油疏水的功能海綿(對水的接觸角為142°、對油的接觸角為0°)。該功能海綿在吸收黏度不同的油相時具有較高的選擇性,并且在持續(xù)400個周期的壓縮試驗后仍不失其優(yōu)良的疏水性能,具有耐久性、堅固性和高彈性。王倡春通過石蠟微球改性硅橡膠,運用原位聚合法將其修飾于PU海綿內表面,形成三維互穿網絡型疏水/親油材料。利用該材料結合外部泵抽取,可實現(xiàn)從水表面連續(xù)收集浮油,突破了傳統(tǒng)油水分離材料吸附的局限,漏油收集效率得到較大提高。在油水兩相分離同時,還能修復溢油對環(huán)境與生態(tài)的傷害。材料自身價格便宜、制作成本低廉,可大規(guī)模生產,且無二次污染,實際應用價值高。
三種油水分離技術比較如下:
油水分離技術 | 特點 | 適用性 | 使用成本 |
膜分離法 | 精度高、易自動化 | 工業(yè)污水處理 | 成本較高 |
冷凍/解凍法 | 精度高、工藝耗時 | 食品工程破乳 | 成本較低 |
原位抽取法 | 效率高、易自動化 | 海洋漏油回收 | 成本較低 |
油水分離過程:在PHOMs中間開一小孔,用導管將其與外部泵相連,將PHOMs置于油水混合物中,啟動自吸泵即可不斷地向外抽取油相。
3 研究發(fā)展趨勢與展望
油水分離技術是處理海洋石油泄漏的關鍵技術之一,傳統(tǒng)分離技術不能一次達到規(guī)定含油廢水的允許排放濃度(10mg/L),需將兩種及以上的技術相結合,如:波紋板聚結器(重力沉降法+聚結法)、浮升聚結器(氣浮法+聚結法)。膜分離、冷凍/解凍分離或原位抽取分離等新型油水分離技術可直接達到處理要求,其中基于PHOMs與外部泵的原位抽取分離技術,可持續(xù)地從水表面快速消除油膜(特別是薄的低黏度油),在處理海洋溢油以及工業(yè)油水分離領域展現(xiàn)了巨大的潛在應用前景。利用疏水物質進一步改性PHOMs的基體材料,增強材料對油類物質的選擇性,可進一步地改善原位抽取分離技術的分離效果。因此,制備出成本低廉、無二次污染的超疏水/超親油PHOMs將是油水分離領域的研究熱點之一。