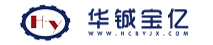
1 引言
含油污泥是指石油開采,存儲(chǔ)及生產(chǎn)過程中產(chǎn)生的大量的廢棄油泥,油泥是指含石油烴、水、無機(jī)物固體等的混合物,是一種高危污染物,我國已經(jīng)將油泥列入《國家危險(xiǎn)廢物目錄》,含油污泥常伴有惡臭氣體產(chǎn)生,含油重金屬,及苯系類等有害物質(zhì),若不及時(shí)處理,對環(huán)境有污染隱患。
目前,國內(nèi)外對含油污泥的處理方法主要有焚燒法、熱解析法、生物處理法、熱化學(xué)洗滌法、溶劑萃取法、固化處理法等,其中熱解與溶劑萃取法技術(shù)雖然回收率較高,但工藝復(fù)雜,技術(shù)不成熟,設(shè)備投資費(fèi)用高。其中熱化學(xué)洗滌法污泥產(chǎn)量大,回收率較低。固化處理法是應(yīng)用較為普遍的技術(shù),但存在以下缺點(diǎn):固化劑加量大,固化時(shí)間長,存在環(huán)境風(fēng)險(xiǎn)。同時(shí),固化劑的穩(wěn)定性也有時(shí)效性。生物處理法周期長,占地面積大,易受氣候影響限制,對高含油污泥及含油生物毒性成分的污泥不適用。
本研究是針對浮渣油泥與氟化鈣油泥的混合泥作為研究對象,根據(jù)混合油泥特性,通過考察油泥混合比例,確定脫水比例。同時(shí),以SXZJ-60型雙向自凈污泥漿葉干化系統(tǒng)為研究對象,通過對脫水后含油污泥進(jìn)一步干化,大大降低了危廢污泥的產(chǎn)生量,減輕了進(jìn)一步處置壓力。同時(shí)對干化過程中存在的問題進(jìn)行了分析,提出了解決辦法。
2 工藝流程
混合油泥經(jīng)疊螺式脫水機(jī)初步脫水后,污泥含水率降至85%左右,然后經(jīng)帶式輸送機(jī)送至雙向自凈干化機(jī)。污泥干化過程中產(chǎn)生的廢氣和粉塵被引風(fēng)機(jī)抽出干化主機(jī)系統(tǒng),其中粉塵經(jīng)過旋風(fēng)分離器時(shí)被收集,尾氣依次經(jīng)過噴淋塔、活性炭吸附罐,處理后達(dá)標(biāo)排放。雙向自凈干化機(jī)出泥含水率≤35%。
3 脫水時(shí)浮渣油泥與氟化鈣油泥混合比例的確定
3.1 試驗(yàn)
(1)試驗(yàn)樣品
試驗(yàn)用的油泥為烷基苯廠浮渣油泥及氟化鈣油泥,泥樣呈黑色,并伴有氣味,油泥的含水率、含油率均較高,難以與水分離。
(2)試驗(yàn)過程及方法
試驗(yàn)過程主要是油泥絮凝,考察合適的絮凝劑,浮渣油泥與氟化鈣油泥混合比例。試驗(yàn)步驟:將浮渣油泥、氟化鈣油泥分別充分搖勻,取100g。加入絮凝劑,其中加量以試驗(yàn)為準(zhǔn),以120rpm快速攪拌2min,并以30rpm速率慢速攪拌1min,絮凝形成的固液兩相1mm×1mm濾網(wǎng)進(jìn)行過濾,直至沒有水的濾出,其中絮凝效果的好壞根據(jù)過濾后的絮體大小、濾出液含固率進(jìn)行綜合判斷。
3.2 小試試驗(yàn)結(jié)果討論
(1)絮凝劑的篩選
依次選用陽離子PAM,陰離子PAM,非離子PAM三種絮凝劑,分別考察其脫水效果,其中絮凝劑加量為5mg/L,以120rpm快速攪拌2min,并以30rpm速率慢速攪拌1min,試驗(yàn)結(jié)果如下:
絮凝劑種類 | 試驗(yàn)現(xiàn)象 |
陽離子絮凝劑 | 絮體大,密度大,沉降速度快 |
陰離子絮凝劑 | 絮體小,沉降速度慢 |
非離子絮凝劑 | 絮體一般,沉降速度快 |
從上表可以看出:向油泥中加入陽離子絮凝劑,都有很好的分離效果,脫出水清澈。加入陰離子絮凝劑,泥水分離困難,水相中會(huì)出現(xiàn)細(xì)小顆粒,渾濁。非離子絮凝劑絮體大小一般,沉降速度快。
(2)絮凝劑的加量
陽離子絮凝劑投加量分別按2mg/L,5mg/L,8mg/L的不同比例加入到油泥中,考察其對絮凝效果影響以120rpm快速攪拌2min,并以30rpm速率慢速攪拌1min,試驗(yàn)結(jié)果如下:
絮凝劑加量 | 試驗(yàn)現(xiàn)象 |
2mg/L | 絮體小,沉降速度慢 |
5mg/L | 絮體大,沉降速度快 |
8mg/L | 絮體大,水粘性大,攪拌后容易松散 |
(3)浮渣油泥與氟化鈣油泥混合比例
采用陽離子絮凝劑,投加量按照5mg/L,單獨(dú)對氟化鈣油泥進(jìn)行絮凝試驗(yàn),效果差,沒有絮凝效果,采用浮渣油泥與氟化鈣油泥摻合處理,逐步提高浮渣油泥與氟化鈣油泥的混合比例,當(dāng)達(dá)到5:1體積比后,絮凝效果顯著,出現(xiàn)大的礬花,滿足疊螺脫水要求。通過試驗(yàn)后發(fā)現(xiàn):在陽離子絮凝劑投加量為5mg/L的情況下,浮渣油泥與氟化鈣油泥的混合比例為5:1時(shí),污泥絮凝效果良好,具備脫水壓濾條件。
4 干化過程中存在問題及對策
4.1 干化后污泥含水率確定
由于雙向自凈漿葉干化機(jī)初次在本裝置使用,沒有現(xiàn)成的經(jīng)驗(yàn)可以借鑒。干化前污泥的含水率均在85%左右,污泥干化后含水率控制在什么范圍才是較佳狀態(tài)還是未知數(shù)。為了摸索經(jīng)驗(yàn),在污泥含水率均在85%的條件下,對干化機(jī)運(yùn)行參數(shù)進(jìn)行調(diào)整,具體分析數(shù)據(jù)和成品如下:
序號(hào) | 變頻器轉(zhuǎn)速(Hz) | 進(jìn)口溫度(℃) | 出口溫度(℃) | 進(jìn)口含水率(%) | 出口含水率(%) | 進(jìn)口含油率(%) | 出口含油率(%) |
1 | 12 | 135 | 98 | 84.2 | 0.7 | 2.16 | 13.62 |
2 | 15 | 135 | 98 | 84.4 | 3.1 | 2.08 | 13.49 |
3 | 15 | 115 | 86 | 84.1 | 7.2 | 2.12 | 13.62 |
4 | 18 | 115 | 82 | 84.4 | 10.2 | 2.21 | 12.67 |
5 | 18 | 105 | 78 | 84.3 | 15.1 | 2.18 | 11.17 |
6 | 21 | 105 | 72 | 84.2 | 2.07 | 2.11 | 9.18 |
由上表可以看出:干化后污泥含水率在5%以下時(shí),污泥成粉末狀,現(xiàn)場干化環(huán)境粉塵較大,不利于環(huán)境保護(hù)。污泥含水率在5%~10%之間,污泥成顆粒狀,不僅屬于較好的理想狀態(tài),也有利于進(jìn)一步處置。污泥含水率超過10%以上,污泥成膠乳狀,水分脫除不徹底,增加了運(yùn)行成本。綜上所述,通過控制干化機(jī)主機(jī)轉(zhuǎn)速和進(jìn)口溫度,將干化后污泥含水率控制在5%~10%之間是比較合理的狀態(tài)。
4.2 運(yùn)行過程中的其他問題
由于危廢污泥含有大量石油類,含有可燃性有機(jī)物。同時(shí),污泥輸送口為半封閉,與空氣接觸,也就是說在污泥輸送入口處可能形成爆炸性油氣混合物,一旦遇到明火或機(jī)器本身機(jī)械摩擦產(chǎn)生的火花,極易發(fā)生爆炸危險(xiǎn)。為了避免事故的發(fā)生,可在污泥輸送入口處增設(shè)氮封,保持入口處處于微正壓,阻止空氣進(jìn)入干化機(jī)內(nèi)部,這樣就可以有效避免安全事故的發(fā)生。
另外,在干化機(jī)運(yùn)行過程中由于污泥含有大量石油類,干化污泥輸送皮帶極易打滑和跑偏,為了避免皮帶打滑和跑偏,在皮帶兩側(cè)增設(shè)糾偏擋板,在皮帶上部增設(shè)壓緊羅盤,有效避免了上述問題。
5 經(jīng)濟(jì)效益和社會(huì)效益
危廢污泥經(jīng)雙向自凈漿葉干化機(jī)干化后,含水率由干化前的85%降至干化后的10%左右,危廢污泥總重量下降80%。按照目前危廢處置費(fèi)4500元/噸計(jì)算,裝置內(nèi)共有1000噸危廢污泥,全部干化處理后經(jīng)濟(jì)效益顯著。另外,危廢污泥干化處理后,大大降低了危廢量,保護(hù)了環(huán)境,同時(shí)避免了運(yùn)輸過程中的拋、灑,社會(huì)效益顯著。
6 結(jié)語
(1)陽離子絮凝劑投加量為5mg/L的情況下,浮渣油泥與氟化鈣油泥的混合比例為5:1時(shí),污泥絮凝效果良好,具備脫水壓濾條件。
(2)干化后污泥含水率控制5%~10%之間,污泥成顆粒狀,不僅屬于較好的理想狀態(tài),也有利于進(jìn)一步處置和節(jié)約成本。
(3)通過在干化機(jī)出口和尾氣引風(fēng)機(jī)之間增加一臺(tái)固定管板式換熱器,不僅降低了尾氣排放溫度,同時(shí)尾氣的排放量也得到相應(yīng)減少。通過控制活性炭的更換周期和噴淋塔的溢流,在實(shí)現(xiàn)尾氣達(dá)標(biāo)排放的基礎(chǔ)上,降低了現(xiàn)場異味的產(chǎn)生。
(4)通過在污泥輸送入口處增設(shè)氮封裝置,可以有效避免安全事故的發(fā)生。