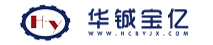
1 引言
對(duì)于液相為煤瀝青、油漿、礦漿,固相為催化劑顆粒或其它微米級(jí)球狀顆粒的高粘度物料,固液分離設(shè)備的開(kāi)發(fā)是需要解決的問(wèn)題之一。高粘度物料固液分離設(shè)備可用于外甩油漿除催化劑、井下控砂、原油除砂、廢高分子材料回?zé)挸暗阮I(lǐng)域。隨著世界經(jīng)濟(jì)的快速增長(zhǎng),煉油技術(shù)朝著重油輕質(zhì)化和清潔汽油燃料生產(chǎn)及多產(chǎn)低碳烯烴的方向發(fā)展。催化裂化已成為加工重油(常壓渣油、減壓渣油、焦化蠟油)的重要手段。為解決催化裂化操作條件惡化,熱負(fù)荷加大,易生焦,處理能力反而下降的問(wèn)題,許多煉油廠采用外甩油漿技術(shù)。由于外甩油漿中通常含有一定量的固體催化劑粉末,而灰分含量較高,必須采取措施脫除,以滿足油漿進(jìn)一步利用的要求。油井出砂會(huì)造成砂子在集輸管道及集輸設(shè)備(沉降罐、分離器、電脫水器和計(jì)量裝置等)中沉積,這將減小管道的流通面積使井口回壓上升,分離器和電脫水器有效容積和工作效率下降,也會(huì)增加設(shè)備的磨損,使儀表的計(jì)量精度降低。
固液分離設(shè)備根據(jù)物料的分離特征可分為兩種類型:一種是分離物料中的液相受到限制,固體顆粒處于運(yùn)動(dòng)狀態(tài)的浮選,重力沉降和離心沉降。另一種是固相受到限制,液相則處于流動(dòng)狀態(tài)的濾餅過(guò)濾,深層過(guò)濾,離心分離和篩濾。前者取決于固體顆粒和液體間的密度差,而后者則以具有過(guò)濾介質(zhì)為前提,深層過(guò)濾只適用于固體顆粒相當(dāng)小的場(chǎng)合,篩濾則是借重力使液體得以分離的設(shè)備。對(duì)于高粘度液體中的固體的分離,由于常溫下物料的粘度很大,過(guò)濾分離阻力大,沉降分離效率低,普通的沉降或過(guò)濾很難將微顆粒去除,所以通常需要將油漿加熱以降低粘度。
2 過(guò)濾分離
2.1 高溫過(guò)濾法
過(guò)濾分離法具有操作簡(jiǎn)單、分離效率穩(wěn)定,催化裂化裝置操作條件或原料性質(zhì)變化對(duì)分離效果影響不大,設(shè)備簡(jiǎn)單,且宜于高溫條件下分離等優(yōu)點(diǎn)。但一般說(shuō)來(lái),過(guò)濾阻力大,特別是油漿中膠狀物含量過(guò)大時(shí),會(huì)加劇過(guò)濾阻力,采用高溫過(guò)濾面臨介質(zhì)難以選擇的問(wèn)題,而普通過(guò)濾則很難將微米級(jí)的顆粒去除。高溫過(guò)濾法是將高粘度固液混合物換熱至300~350℃,使物料的粘度隨溫度的升高而降低后,再進(jìn)入過(guò)濾系統(tǒng)進(jìn)行過(guò)濾分離。
2.2 篩濾法
篩濾法主要采用多孔金屬篩分反洗系統(tǒng)。多孔金屬篩分反洗系統(tǒng)一般由多個(gè)體積相當(dāng)?shù)膲毫θ萜鹘M成,每個(gè)容器內(nèi)都裝有面積相當(dāng)?shù)膹?fù)合不銹鋼絲網(wǎng)篩,以圓筒形排布,各個(gè)容器之間并排。處理油漿溫度可為204℃~371℃,催化劑濃度可達(dá)6000×10-6(6000ppm)。
3 靜電分離法
靜電分離法是近年來(lái)發(fā)展起來(lái)的一種新型液固體系分離技術(shù),適用于固體顆粒直徑很小(10-5~10-6m)、顆粒濃度相對(duì)較低且液相電阻率又較大的液固體系。靜電分離法是當(dāng)含微顆粒的液流流經(jīng)電場(chǎng)作用下的填料床層時(shí),微顆粒在高壓電場(chǎng)中被極化,并被吸附在填料上(如玻璃球),從而使液流得以凈化,當(dāng)填料床層因吸附微顆粒達(dá)飽和后,采用反沖洗液流經(jīng)床層使填料得以再生,然后再進(jìn)行下一輪的吸附操作。
4 沉降分離
4.1 重力沉降
重力沉降法包括自然沉降和化學(xué)沉降法。
4.1.1 自然沉降法
自然沉降法具有設(shè)備簡(jiǎn)單、運(yùn)行成本低、操作容易等特點(diǎn),被很多煉油廠采用,但其凈化效率不高,小于20μm的顆粒去除十分困難,不僅分離時(shí)間長(zhǎng),而且設(shè)備也很龐大。如當(dāng)溫度為250℃時(shí),沉降深度為60cm,催化劑微粒去除率達(dá)85%時(shí),所需的沉降時(shí)間為20000多小時(shí),顯然沉降時(shí)間太長(zhǎng),無(wú)法工業(yè)化。
4.1.2 沉降劑沉降法
在油漿中加入一種添加劑,使催化劑能夠快速沉降。國(guó)外于20世紀(jì)80年代初期完成開(kāi)發(fā),目前已有50多家煉油廠使用。用化學(xué)沉降助劑改善油漿催化劑粉末分離技術(shù)的突出優(yōu)點(diǎn)是工藝和設(shè)備簡(jiǎn)單。
4.2 離心分離
離心沉降法的主要設(shè)備是高溫試管沉降離心機(jī)。離心沉降法的主要設(shè)備是GC5高溫試管沉降離心機(jī)。GC5高溫試管沉降離心機(jī)是利用油漿在高溫時(shí)流動(dòng)性明顯增大的粘溫特性研制的,該離心機(jī)的離心腔周?chē)渲糜屑訜岷捅卦O(shè)備,同時(shí)為便于操作還配有控溫、控時(shí)和控制轉(zhuǎn)速的裝置。將油漿經(jīng)換熱器換熱至30℃~150℃,進(jìn)入高溫離心分離機(jī)進(jìn)行分離,離心時(shí)間約2~10min,離心轉(zhuǎn)速為3000~5000r/min,脫固率為92%~98%,得到固含量為0.02%的脫固油。GC5高溫試管沉降離心機(jī)技術(shù)指標(biāo)為:轉(zhuǎn)速5000r/min,容量60mL,溫度達(dá)300℃,定時(shí)范圍0~6min。
4.3 旋流分離技術(shù)
4.3.1 旋流分離技術(shù)簡(jiǎn)介
旋流分離技術(shù)由旋流分離器、旋流分離流程系統(tǒng)、泵送系統(tǒng)和檢測(cè)控制系統(tǒng)四大部分組成,其中關(guān)鍵部分是旋流分離器。旋流分離法具有設(shè)備結(jié)構(gòu)簡(jiǎn)單、工藝流程簡(jiǎn)單和操控容易等優(yōu)點(diǎn),因而成為固液分離方法中簡(jiǎn)單可行的技術(shù)路線。
用旋流器作為固液分離設(shè)備,具有結(jié)構(gòu)簡(jiǎn)單、易操作、可靠性高、投資和操作費(fèi)用低、節(jié)能、環(huán)保、安全等特點(diǎn)。作為分離設(shè)備在煉油和石油化工過(guò)程中有很大的應(yīng)用潛力。對(duì)于旋流器在高粘度物料固液分離方面的應(yīng)用,國(guó)內(nèi)已有了一定的研究成果。
4.3.2 粘度對(duì)旋流器分離過(guò)程的影響
隨著液相粘度增大,旋流器分離效率會(huì)降低,主要有以下三個(gè)原因:液相粘度大,會(huì)減小液相與固相的密度差;顆粒遷移阻力增大;旋流場(chǎng)旋轉(zhuǎn)衰竭加快。
旋流器在高粘度流體中的運(yùn)用,主要是解決粘度增大導(dǎo)致的分離效率降低的問(wèn)題,可以從以下三個(gè)方面考慮:增大沉降速度;增加停留時(shí)間;減小沉降距離。
當(dāng)物料是處于牛頓流體范疇礦漿粘度與剪切速率無(wú)關(guān)。粘度同樣會(huì)影響水力旋流器的水----底流分率R的大小,R中的所有顆粒不管形狀和大小如何都進(jìn)入到底流,旋流器中的液體速度在粘度增大及粘度阻力增加時(shí)下降,因此造成R增加。
4.3.3 高粘度物料旋流分離實(shí)驗(yàn)研究
對(duì)于旋流器在高粘度液體中分離固體方面的應(yīng)用,國(guó)內(nèi)已有了一定的研究成果。張士瑞等人用模擬實(shí)驗(yàn)裝置,初步研究了應(yīng)用微型旋流器脫除催化裂化油漿殘留固體的可行性。實(shí)驗(yàn)操作條件為常溫,以水為液相,固相為催化裂化催化劑粉末。采用的單管旋流器,其公稱直徑為10mm。進(jìn)行5個(gè)進(jìn)料速度、4個(gè)底流分率、4種進(jìn)料固體含量的全方位正交實(shí)驗(yàn),共操作試驗(yàn)方案80種,采集并分析樣品143個(gè),獲取作為分析結(jié)果的數(shù)據(jù)文件295份,經(jīng)整理計(jì)算,獲得完整數(shù)據(jù)68組。實(shí)驗(yàn)對(duì)于底流分率、進(jìn)料固體含量、進(jìn)料速度對(duì)分離效率的影響做了詳細(xì)的研究,并得出結(jié)論。在不考慮其他因素的情況下,采用所開(kāi)發(fā)的旋流器脫除催化裂化油漿殘留催化劑微粒在技術(shù)上是可行的,分離效果能夠滿足其絕大多數(shù)下游利用過(guò)程對(duì)固體含量的規(guī)格要求。
杜海洋等人用實(shí)驗(yàn)的方法研究了用高溫旋流分離裝置分離加氫裂化尾油中甲苯不溶物、膠質(zhì)、瀝青等物質(zhì)的分離效果。實(shí)驗(yàn)對(duì)不同溫度下的分離效率做了研究,并得出結(jié)論,在較低溫度下旋液分離器對(duì)甲苯不溶物、膠質(zhì)、瀝青等物質(zhì)的分離效率很低,但隨著溫度的升高,油漿粘度顯著降低,分離效率顯著提高。實(shí)驗(yàn)還對(duì)不同粘度下旋液分離器的進(jìn)出口尾油密度、物料粘度和樣品顆粒進(jìn)行了測(cè)定,同時(shí)對(duì)進(jìn)出口尾油密度、粘度和顆粒的比較,來(lái)進(jìn)一步對(duì)旋流分離器的分離效果進(jìn)行說(shuō)明。
華東理工大學(xué)根據(jù)多年的研究和工程經(jīng)驗(yàn),采用微型旋流器分離工藝對(duì)催化裂化外甩油漿進(jìn)行分離,并設(shè)計(jì)了公稱直徑為10mm的專用微型旋流管。該旋流管采用單錐、雙入口結(jié)構(gòu)。白志山等人通過(guò)試驗(yàn)研究,以催化外甩油漿為對(duì)象,在1.8×106t/s重油催化裂化裝置上開(kāi)發(fā)了外甩油漿微型旋流凈化工業(yè)實(shí)驗(yàn)裝置,考察了微型旋流芯管壓力、分離效率和流量的相互關(guān)系。結(jié)果表明,在合適的操作條件下分離效率可以達(dá)到60%以上,分離后油漿中固體含量低,僅為680mg/L。凈化油漿催化劑顆粒的平均粒徑采用先灼燒后庫(kù)爾特粒度儀分析,3μm粒徑的催化劑顆粒去除率達(dá)到75%。
5 結(jié)論
當(dāng)物料粘度大時(shí),采用過(guò)濾分離進(jìn)行固液分離時(shí)阻力大,容易堵塞。旋流分離器內(nèi)無(wú)有形介質(zhì),不會(huì)堵塞,靠無(wú)形的超重力場(chǎng)分離。當(dāng)不能通過(guò)升溫將粘時(shí),開(kāi)發(fā)用旋流分離是一種選擇。
目前國(guó)內(nèi)高粘度物料固液旋流分離設(shè)備研究主要處于試驗(yàn)階段。對(duì)比分析上述幾種分離方法,在各種高粘度物料分離方法中旋流分離法具有設(shè)備低成本、低能耗、結(jié)構(gòu)簡(jiǎn)單、工藝流程簡(jiǎn)單和操控容易等優(yōu)點(diǎn),因而成為簡(jiǎn)單可行的技術(shù)路線。
選擇適當(dāng)?shù)牟僮鳁l件,應(yīng)用固液旋流分離器實(shí)現(xiàn)高粘度物料固液分離在技術(shù)上有望可行,分離效果可滿足絕大多數(shù)下游利用過(guò)程的要求,實(shí)際工業(yè)操作對(duì)處理能力的要求可通過(guò)將多個(gè)旋流器并聯(lián)實(shí)現(xiàn)。