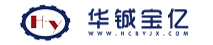
高莊煤業(yè)有限公司是年入洗能力3.3Mt的礦井型煉焦選煤廠,主要產(chǎn)品為六級冶煉精煤。該廠于2014年開始改造,分兩期建設(shè)完成。一期改造生產(chǎn)工藝流程為原煤預(yù)先脫泥,50~1mm粒級采用無壓三產(chǎn)品重介旋流器分選,1~0.25mm采用TBS粗煤泥分選機分選,0.25~0mm粒級采用XJM型浮選機分選,浮選精礦選用臥式沉降離心機脫水回收,尾礦進(jìn)入濃縮池沉淀后壓濾。二期改造增加二次浮選,臥式沉降離心機濾液進(jìn)入浮選機再次浮選,二次浮選精礦利用快開壓濾機處理。
1 存在問題及原因分析
一期改造完成后,即投入正式生產(chǎn),但在生產(chǎn)中發(fā)現(xiàn)臥式沉降離心機脫水回收效果差,固體回收率僅有50%,不僅造成精煤回收率低、濾液濃度大,還在進(jìn)入煤泥水系統(tǒng)時,增加系統(tǒng)細(xì)煤泥循環(huán)量,惡化濃縮效果。
1.1 處理量低
高煤公司選煤廠浮選精煤脫水回收設(shè)備采用臥式沉降離心機,該機理論處理量40~50t/h。按照日常生產(chǎn)過程中積累數(shù)據(jù)計算,按浮選機入料量約為30t/h,浮選產(chǎn)率為68%計算,浮選精煤量僅為20.4t/h。離心機入料三通閥開度僅為40%,設(shè)備利用率低。
1.2 浮選精煤極細(xì)粒含量高
選煤廠浮選入料由水力分級旋流器溢流、弧形篩篩下水組成。對浮選精煤進(jìn)行全級小篩分試驗后可知,粗煤粒級組成較細(xì),<0.045mm含量占42.14%,而臥式沉降離心機要求<0.045mm粒級不能>40%。
1.3 固體回收率低
按照選煤廠技術(shù)檢查標(biāo)準(zhǔn)對臥式沉降離心機進(jìn)行單機檢查,采樣時間2h,間隔20min,采樣量1L/次。由檢查結(jié)果可以看出:固體回收率僅為50.3%,濾液濃度高達(dá)12.83%,相當(dāng)于有一半的細(xì)粒級物料又重新進(jìn)入系統(tǒng)再次循環(huán)。循環(huán)煤泥量的增加,加大了煤泥水系統(tǒng)的壓力。
2 改進(jìn)措施
為解決臥式沉降離心機處理效果不佳的問題,綜合考慮分析處理能力、入料粒級、工藝流程等,提出將一期重介系統(tǒng)干擾床分選(一種粗煤泥分選設(shè)備)的部分精礦摻入浮選精煤,共同進(jìn)入臥式沉降離心機。改進(jìn)后,首先降低入料中<0.045mm粒級的含量,滿足該設(shè)備的入料粒級要求;其次可增加處理量,提高設(shè)備利用率;節(jié)省干擾床分選精礦的脫水回收設(shè)備,節(jié)能降耗。
(1)入料粒級:對混料后精礦進(jìn)行全級小篩分試驗,確定物料摻和后<0.045mm粒級含量為26.55%,滿足設(shè)備要求。
(2)處理能力:一期重介系統(tǒng)干擾床分選精礦采用煤泥立式刮刀離心機脫水回收,按日常生產(chǎn)過程中積累數(shù)據(jù)計算,干擾床分選精礦量約為15.6t/h。如摻和浮選精煤后,臥式沉降離心機入料量約為35.6t/h,符合設(shè)備要求。
(3)工藝流程:將干擾床分選精礦摻入浮選精煤,一起進(jìn)入臥式沉降離心機。
3 應(yīng)用效果
改造完成后,按照選煤廠技術(shù)檢查標(biāo)準(zhǔn)對臥式沉降離心機進(jìn)行單機檢查,采樣時間2h,間隔20min,采樣量1L/次。
(1)改造后固體回收率提高23.62%,濾液濃度降至4.47%,精煤回收率明顯提高,灰分未見明顯變化。
(2)固體產(chǎn)物外在水分由24.3%降至18%,水分明顯降低。
(3)臥式沉降離心機三通入料閥由40%開度提高至70%,設(shè)備利用率提高近30%。
4 經(jīng)濟效益
改造完成后,精煤產(chǎn)率增加約為1.38%,按照年入洗330萬t,多產(chǎn)精煤45540t。按照當(dāng)前市場價格精煤490元/t、煤泥170元/t,年增加效益約1457.3萬元。