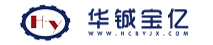
1 引言
錦西石化含油污泥主要來源于污水處理場和生產(chǎn)裝置的罐底油泥。含油污泥中一般含油率在70%~75%,含水率在20%~25%,含無機(jī)物5%。含油污泥中的原油罐底泥的含油量高,可達(dá)到75%。如將其回?zé)捘軜O大的節(jié)約資源。然而由于其中含泥沙量高,裝置回?zé)掃^程中很容易堵塞塔盤,從而只能將其排放到下水,循環(huán)往復(fù)于污水處理系統(tǒng)中,增大了污水處理難度,而且造成油資源的浪費(fèi)。污水處理車間根據(jù)現(xiàn)有的工藝流程,采用離心分離技術(shù),并運(yùn)用脫水劑對污泥進(jìn)行調(diào)質(zhì),使含油污泥中的固體組分得到有效去除,從而使污油較大程度的回?zé)?,變廢為寶,實(shí)現(xiàn)含油污泥的資源化利用。
2 煉油廠含油污泥的特點(diǎn)及其危害
煉油廠含油污泥主要來源于隔油池底泥、浮選池浮渣、原油罐底泥,俗稱“三泥”,這些含油污泥組成各異,通常含油率在10%~75%之間,含水率20%~90%之間,同時(shí)伴有一定量的固體。含油污泥中含有大量的病原菌、寄生蟲(卵)、銅、鋅、鉻、汞等重金屬,鹽類以及多氯聯(lián)苯、二惡英、放射性核元素等難降解的有毒有害物質(zhì)。污泥體積龐大,若不加以處理直接排放,不但占用大量耕地,而且對周圍土壤、水體、空氣都將造成污染。
3 含油污泥資源化利用的必然性
含油污泥處理與應(yīng)用是國內(nèi)外石油生產(chǎn)領(lǐng)域環(huán)境保護(hù)的重要內(nèi)容,是較難解決而急需解決的問題之一,也是制約石油化工環(huán)境質(zhì)量持續(xù)提高和經(jīng)濟(jì)可持續(xù)發(fā)展的一大難題。據(jù)不完全統(tǒng)計(jì),我國石油化工領(lǐng)域產(chǎn)生油泥量達(dá)(10~44)×104t/a。根據(jù)國家新排污標(biāo)準(zhǔn),未經(jīng)處理的含油污泥排放收費(fèi)標(biāo)準(zhǔn)為1000元/噸,這將大大增加企業(yè)的生產(chǎn)成本,同時(shí)石油煉制過程中所產(chǎn)生的隔油池底泥、罐底泥、浮渣以及剩余活性污泥中含有苯系物、酚類、蒽、芘等具有惡臭味和毒性的物質(zhì),是國家明文規(guī)定的危險(xiǎn)廢物,含油污泥已被列入《國家危險(xiǎn)廢物目錄》中的含油廢物類,《國家清潔生產(chǎn)促進(jìn)法》要求必須對含油污泥進(jìn)行無害化處理。含油污泥中富含大量烴類,實(shí)施油泥資源化符合可持續(xù)發(fā)展的戰(zhàn)略方針和循環(huán)經(jīng)濟(jì)的要求。
4 含油污泥的離心分離試驗(yàn)
4.1 試驗(yàn)原理
含油污泥通過離心機(jī)中心進(jìn)料管被引入轉(zhuǎn)子,在離心力的作用下很快分為兩層,較重的固相(泥沙)沉積在轉(zhuǎn)鼓內(nèi)壁上形成沉渣層,由螺旋輸送器推出,送固廢場填埋或焚燒;而較輕的液相(污油和水的混合物)則形成內(nèi)環(huán)分離液層,從濾液管線排出,送往污油罐進(jìn)行加溫脫水,送裝置回?zé)?,從而完成污油回收的過程。
4.2 離心機(jī)原理
污泥懸浮顆粒在離心機(jī)內(nèi)的沉降速度和其粒徑的平方、粒徑和水相的密度差、離心機(jī)的離心因數(shù)成正比,而和污泥混合液的粘度成反比。因此,污泥粒子與水相之間存在密度差是含油污泥離心分離的前提,要提高和保證離心分離效果,應(yīng)從增大污泥顆粒粒徑和密度,減少粘度,提高離心速度著手。
4.3 含油污泥的化學(xué)調(diào)質(zhì)
含油污泥的化學(xué)調(diào)質(zhì)主要是通過投加助劑、加溫和投加絮凝劑等手段改變含油污泥性質(zhì),使高度分散的污泥顆粒、油珠或乳化油進(jìn)行電中和、網(wǎng)聯(lián)架橋,從而使污泥顆粒間發(fā)生凝聚,變成大顆粒以至大塊凝聚體,從而改善其固液分離性能。
4.3.1 加溫預(yù)處理
將儲(chǔ)存有含油污泥的污油儲(chǔ)罐T-12/1~3通過罐底蒸汽蛇管加溫至70~80℃,破壞乳化油(W/O,O/W)的乳化狀態(tài),進(jìn)行脫水操作。同時(shí),通過加溫可降低石油烴類物質(zhì)的粘度,有利于油、水、固三相分離。
4.3.2 絮凝劑的選擇
該試驗(yàn)用無機(jī)絮凝劑聚合鋁和有機(jī)絮凝劑聚丙烯酰胺對含油污泥分別進(jìn)行絮凝試驗(yàn),分子量PAM3>PAM2>PAM1>聚合鋁,試驗(yàn)結(jié)果如下:
藥劑型號(hào) | 極性 | 質(zhì)量分?jǐn)?shù)(%) | 用量(ml) | 靜止后液相體積(ml) | ||
5min | 10min | 15min | ||||
聚合鋁 | 陽性 | 0.25 | 100 | 80 | 100 | 110 |
PAM1 | 陰性 | 0.25 | 100 | 120 | 150 | 190 |
PAM2 | 陽性 | 0.25 | 100 | 200 | 220 | 250 |
PAM3 | 陽性 | 0.25 | 100 | 170 | 180 | 230 |
由上表可知,陽離子絮凝劑好于陰離子絮凝劑,這是因?yàn)殛栯x子能中和含油污泥膠體表面所帶的負(fù)電荷,使體系脫穩(wěn)。有機(jī)高分子絮凝劑的絮凝效果要好于無機(jī)絮凝劑,是因?yàn)榉肿恿吭龃?,分子鏈增長,有利于對膠體顆粒的捕集和橋連。但分子鏈太長,也不利于對膠體顆粒的網(wǎng)捕和吸附。
4.3.3 絮凝劑投加濃度
投加絮凝劑的溶質(zhì)濃度太大,絮凝劑在污泥中的分散效果明顯降低不利于撲俘粒子;而濃度太小又會(huì)使絮凝速度減慢而導(dǎo)致絮凝劑的用量增加以及增加離心機(jī)的容積負(fù)荷。經(jīng)反復(fù)試驗(yàn),確定投加絮凝劑的溶質(zhì)濃度以0.2%~0.3%為宜。
4.3.4 絮凝劑的投加量
絮凝劑的投加一定要有準(zhǔn)確的可調(diào)手段。投加量小起不到作用,絮凝效果差,而投加量大一方面造成浪費(fèi),另一方面加藥量超過一定的限度會(huì)形成反膠體,使得介質(zhì)無法分離。絮凝劑主要是通過架橋和電中和產(chǎn)生作用。當(dāng)絮凝劑用量過大時(shí),會(huì)產(chǎn)生兩個(gè)副作用:一是使電荷中和過量而逆轉(zhuǎn);二是對膠粒表面產(chǎn)生保護(hù)作用。所以在生產(chǎn)過程中選用流量可調(diào)的計(jì)量泵,并在藥泵的出口安裝小流量流量表進(jìn)行準(zhǔn)確投加是必要的。藥劑投加量與離心機(jī)入口含油污泥的固含量有關(guān)。如果油泥固含量較高,藥劑投加量較大;如果油泥固含量較低,藥劑投加量較小。藥劑的投加量是否合適,在其他條件不變的情況下,主要根據(jù)出口泥餅含水率(一般在70%~80%)的高低和濾液固含量的濃度確定。藥劑投加量一般控制在300~500L/h。
4.3.5 使用化學(xué)藥劑調(diào)質(zhì)
該實(shí)驗(yàn)向含油污泥中投加脫水劑,破壞含油污泥中膠體的穩(wěn)定性,使水、固、油三相有效分離,提高離心效果。在保證藥劑的投加不增加離心機(jī)容積負(fù)荷的前提下,確定投加量為100~200L/h為佳。
4.4 離心機(jī)參數(shù)的選擇
4.4.1 轉(zhuǎn)鼓轉(zhuǎn)速
根據(jù)離心機(jī)的工作原理,一般情況下,轉(zhuǎn)速越高分離效果越好,濾餅越干,濾后液越清,軸功率亦越大。但并不是轉(zhuǎn)速越高越好,對于易沉降的介質(zhì),轉(zhuǎn)速越高,軸功率越大,容易引起固料來不及推出,造成物料堵塞;對于不易沉降的含油污泥,轉(zhuǎn)速高到一定的數(shù)值后,會(huì)出現(xiàn)分離效果下降,產(chǎn)泥量減少,濾液中固含量上升的現(xiàn)象。主要因?yàn)橛湍嗤ㄟ^絮凝劑作用而凝結(jié)成的膠合物不很穩(wěn)定,在一定的外力作用下又會(huì)分開。因?yàn)楹臀勰鄡?nèi)部包含由架橋作用和范德華力牽引而成的兩部分----高分子絮凝劑和含油較高的膠粒。雖然作為整體后,其終合密度略大于油水混合物,然而作為內(nèi)部個(gè)體,含油較高的膠粒的密度小于高分子絮凝劑的密度,因此隨著離心機(jī)轉(zhuǎn)速增大,含油較高的膠粒和高分子絮凝劑的密度差引起的離心力隨之增大,當(dāng)該離心力大于相對穩(wěn)定的膠合物內(nèi)部兩組成之間的架橋作用和范德華力合力時(shí),絮凝作用失敗,膠合物穩(wěn)定系統(tǒng)被破壞。因而出現(xiàn)分離效果下降,產(chǎn)泥量減少的現(xiàn)象。在靜置時(shí)間相同的情況下,PAM2比其他絮凝劑效果要好,故選擇作為離心試驗(yàn)的絮凝劑,同時(shí)做空白試驗(yàn)。經(jīng)試驗(yàn)發(fā)現(xiàn)只有當(dāng)離心機(jī)的轉(zhuǎn)速在2000r/min以上時(shí)污泥絮體才能形成明顯的固液分層現(xiàn)象。測定轉(zhuǎn)速在2000、2500及3000r/min時(shí)絮凝體系的固液分離情況,測試表明分離效率隨著轉(zhuǎn)速的增大而顯著提高。
4.4.2 差轉(zhuǎn)速
差轉(zhuǎn)速的大小主要取決于離心機(jī)所需排渣量的大小,污泥脫水時(shí),離心機(jī)差轉(zhuǎn)速不能過高,因?yàn)椴钷D(zhuǎn)速過高時(shí),由于轉(zhuǎn)鼓內(nèi)流體的撓動(dòng)加快會(huì)增大流體對濕沉渣的沖刷,增大分離液中的含固量,降低固體回收率從而影響分離效果。差轉(zhuǎn)速過低又會(huì)明顯降低螺旋的輸送效率,使差速器受到的扭矩過大損壞差速器。由于含油污泥粘度大,固液難分離,和絮凝劑反應(yīng)時(shí)間長,因此差轉(zhuǎn)速不宜過大。試驗(yàn)研究證明,用于含油污泥脫水時(shí),離心機(jī)的差轉(zhuǎn)速以3~5r/min為宜。
4.4.3 離心機(jī)處理量
離心機(jī)的處理量是指能達(dá)到分離要求的進(jìn)機(jī)流量。當(dāng)進(jìn)料流量過大時(shí),離心機(jī)轉(zhuǎn)鼓內(nèi)的渣層增厚,沉渣層表面松散的微粒容易被沖刷,從而明顯降低分離效果。離心機(jī)油泥的固含量和處理油泥的量有較大的關(guān)系。離心機(jī)入口油泥固含量較高,雖然在一定程度上提高了離心機(jī)的處理量,但是必須選用較高的藥劑溶解濃度,不利于油泥與藥劑的快速混合,影響分離效果??刂戚^低的油泥處理量,就可以選用較低的藥劑溶解濃度,有利于藥劑與油泥的快速混合,可以得到較好的分離效果。處理含油污泥時(shí)離心機(jī)處理量一般控制在3~5m3/h。
4.5 工藝參數(shù)確定
為保證達(dá)到處理效果的同時(shí),又能節(jié)約成本,節(jié)省 水、電、蒸汽藥劑等,本試驗(yàn)確定了較佳的處理工藝參數(shù),如下:
項(xiàng)目 | 指標(biāo) |
泥渣溫度(℃) | 70~75 |
進(jìn)料量(m3/h) | 3~5 |
絮凝劑濃度(%) | 0.25 |
絮凝劑量(L/h) | 350~450 |
脫水劑量(L/h) | 100 |
離心機(jī)轉(zhuǎn)鼓轉(zhuǎn)速(r/min) | 3265~3266 |
離心機(jī)差轉(zhuǎn)速(r/min) | 3~4 |
4.6 回收油品質(zhì)分析
離心機(jī)濾液線流出的分離液(污油)送往裝置回?zé)?,該污油?jīng)濾液線送往集油井,再經(jīng)泵揀到污油罐進(jìn)行加溫脫水?;厥沼筒蓸臃治鰯?shù)據(jù)如下:
樣品編號(hào) | 含油率(%) | 含水率(%) | 灰分(%) |
1 | 90.3 | 8.97 | 0.73 |
2 | 88.6 | 10.92 | 0.48 |
3 | 90.2 | 9.36 | 0.44 |
4 | 87.2 | 12.28 | 0.52 |
5 | 85.4 | 14.21 | 0.39 |
平均值 | 88.34 | 11.15 | 0.51 |
5 結(jié)論
(1)通過對含油污泥進(jìn)行加溫,投加化學(xué)藥劑調(diào)質(zhì)等預(yù)處理,可有效降低含油污泥的粘性,從而實(shí)現(xiàn)固液快速分離。
(2)通過對含油污泥投加有機(jī)高分子絮凝劑,可使高度分散的污泥顆粒、油珠或乳化油進(jìn)行電中和、網(wǎng)聯(lián)架橋,使污泥顆粒間發(fā)生凝聚,從而改善其固液分離性能。
(3)經(jīng)過臥螺式兩相離心機(jī)處理過的含油污泥,分離液含油可達(dá)88%,可送往生產(chǎn)裝置回?zé)?,泥餅可進(jìn)行填埋或焚燒。
(4)錦西石化污水處理車間運(yùn)用離心分離技術(shù)處理含油污泥成功解決了長期困擾企業(yè)的高含泥污油無法回?zé)挼碾y題,實(shí)現(xiàn)污油回?zé)捈昂臀勰嗟馁Y源化利用,避免了企業(yè)資源浪費(fèi)和能源損失,在取得環(huán)境效益的同時(shí),又產(chǎn)生一定的經(jīng)濟(jì)效益。