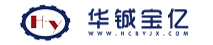
油脂精煉中使用的離心分離機主要從國外進口的兩大品牌:韋斯伐里亞和阿爾法拉伐。雖然國產也有兩大品牌相似產品,但離心機是油脂精煉的核心設備,其功能與質量對生產效率和產品質量起決定性作用,故目前國內油脂生產企業(yè)仍以選用國外的 兩個品牌為主。一般國內企業(yè)訂購成套設備包括機體和控制柜,使用幾年后一旦控制系統(tǒng)發(fā)生故障,往往需要國外生產廠家派技術人員來國內技術服務,不便于操作與維護。
1 離心機工作原理介紹
油脂行業(yè)中使用的是沉降式離心機,用于分離難分離的物料(粘性液體與細小固體顆粒組成的懸浮液或密度相近的液體組成的乳濁液等)。碟式分離機以其結構緊湊,占地面積小,生產能力大等特點,因而在油脂加工行業(yè)的生產部門獲得廣泛應用,離心分離機是利用混合液(混濁液)中具有不同密度且互不相溶的輕、重液和固相,在離心力場中獲得不同的沉降速度的原理,達到分離分層或使液體中固體顆粒沉降的目的。分離機中的碟式分離機是應用較廣的沉降離心機。
碟式分離機是立式離心機,轉鼓是離心機主要動作部件,位于立軸上端,由轉鼓體、上分配器、下分配器等主要組件組成,通過傳動裝置由電動機驅動而高速旋轉,高速旋轉部件通過高精度的錐度配合與立軸相連獲得動力,立軸部分是傳遞動力,并裝有增速齒輪(小螺旋齒輪),橫軸是將電機的動力傳遞到立軸和轉鼓的主要部件,由電機、聯(lián)軸器、壓力耦合器、傳動軸、大螺旋齒輪和剎車輪等零件組成,起到過載保護作用(液力耦合器)大螺旋齒輪在運轉中將潤滑油飛濺到各傳動軸承,使軸承潤滑,當油溫超過110℃時,橫軸的液力耦合器上的易溶合金保護塞自動溶化,使分離機失去源動力。轉鼓內有一組互相套疊在一起的碟形零件——碟片,若干層由定距條間隔成碟片組,裝于碟片與碟片之間留有很小的間隙。待分離物料由位于轉鼓中心的進料管加入轉鼓。下分配器的作用是使進入轉鼓的懸浮液和沖洗液隔開,并將沖洗液引向轉鼓壁,以稀釋和沖走沉積在轉鼓上的雜質。當混合液(混濁液)流過碟片之間的間隙時,固體顆粒在離心機作用下沿碟片下表面滑動而脫離碟片并積聚在轉鼓內直徑大的部位形成渣層,通過排渣機構(人工、連續(xù)、間隙)排出轉鼓;輕相液體沿碟片上表面向轉鼓中心運動,通過離心力從轉鼓上部出液口排出轉鼓;轉鼓頂端裝有向心泵,向心泵的作用是將液體旋轉動能轉化為壓力排出機外。即借助于向心泵分別引出輕相和重相。被分離的物料在強大的離心力場作用下,經一組碟片束的分離間隔中,以碟片中性孔 為分界面,比重大的液體(重相)沿碟片壁向中心孔外運動,其中重渣積聚區(qū),皂腳等則流向大的向心泵處。比重小的液體(輕相)沿碟片壁向內向上運動,匯聚到小的向心泵處,輕、重相分別由小向心泵和大向心泵輸出。
離心機電控部分主要有啟動電機、6只氣動電磁閥(分別是密封水閥、排渣閥、沖水閥、活塞閥、注水閥、冷卻水閥)。主要檢測參數(shù):啟動電流、出口壓力、振動幅度、液體流量及循環(huán)運行步序時間的設定與顯示。
2 離心機的使用要點及控制方案
以韋斯伐里亞離心機的控制程序為例作詳細說明。
(1)分離機采用液力耦合器和一對螺旋齒輪傳動,利用液體傳遞動力,既增速平穩(wěn)又能進行過載保護?;瑒踊钊呐旁鼊幼饔沙绦蚩刂?,一般電機功率為15~20kW,可采用Y-△或變頻器啟動,高速約達6600r/min,啟動電機一般為15~20kW,由于分離機的高速運行,啟動到正常運行,需要時間30s以上且啟動電流大,啟動時出口壓力檢測不投入聯(lián)鎖保護和報警,啟動時間在上位機上可設定,并顯示運行時間。啟動過程中檢測啟動電流,設定啟動電流報警值,以防止飛車,做好應急處理程序。
(2)啟動準備:
①加潤滑油到油箱內。
②檢查操作水壓力,打開手動操作水供水閥。
③啟動電機電流不超過65A,全速后不超過30A。啟動時間一般設定5min,達到全速后,指示盤65r/min,啟動過程控制系統(tǒng)會自動檢測電流、溫度、振幅等狀態(tài)參數(shù),如果不滿足正常運行條件,則報警或停機。如果滿足則再加速至額定轉速,具備正式投入工作狀態(tài)。正常運行按生產周期時序圖要求由PLC程序控制,正常生產周期是自動循環(huán)過程,各閥控制根據(jù)系統(tǒng)時序圖動作,動作的時間由計算機界面設定并顯示運行參數(shù)。
(3)在畫面上設置好時間參數(shù)?!皢訒r間”為電機的啟動時間內不投入開閥和排渣,是電機的啟動和檢測過程的時間。“密封周期”、“密封時間”是密封水閥、注水閥間隔時間和打開時間,在排渣周期前進行的反復活塞注水保持密封水,以防止出水口漏油,在渣聚結區(qū)域還有部分污油聚結在此,加密封水后由于油密度比水輕而被排到此區(qū)域外,并封住出水口。注水閥也同時間斷補水,置換出從油中分離的污水,由出水口排出機外。運行一定時間后進入排渣時間,可設置“排渣時間”大小,部分排渣時間包含在一個生產周期中,設定的“排渣周期”即進入部分排渣程序,這時打開沖水閥進行預先沖洗,同時打開活塞閥,利用氣壓推動活塞,保持一定水壓,滑動活塞下移而打開離心機下部的排渣口?;瑒踊钊蜷_排渣口的時間不宜太短,應大于排渣閥的開啟時間。預沖時間(可設定“預沖時間”)到后,打開排渣閥(“排渣時間”可設定),部分排渣閥打開的時間一般為1s,時間較短,打開排渣閥后進行排渣。排渣沖洗后進入“關閉延時時間”(可設定)計時,計時過程中密封時間到,密封水閥關閉?!瓣P閉延時時間”2s后打開注滿水閥進行注水,為下次排渣沖水用。“關閉延時時間”到后,關閉注滿水閥和密封水閥。并沖水閥仍打開,直到并沖時間(可設定)到關閉。部分排渣打開的時間過程結束后,一個循環(huán)周期結束,又重新循環(huán)一個新的循環(huán)周期。
(4)下盒為排渣的主要通道,并設計有專用于拆裝的小活塞、閥體的通孔。進水罩是用專分配操作水的不銹鋼焊接殼體,通過與其連接管道排出機外。
(5)全排渣為手動操作,按下“全排”按鈕,程序執(zhí)行全排渣過程,閥的開啟按全排渣時序執(zhí)行,過程與部分排渣基本相同,只是排渣閥和注水閥開啟的時間長些。全部排渣是手動操作,當“全排”按鈕按下,進入全排渣的控制程序,各控制閥具體由上述時序圖順序控制。全排渣時離心機暫停進料,打開排渣沖水閥約10s,同時打開注滿水閥和并沖水閥,這樣沖洗強度大。排渣沖水閥關閉后打開密封水閥約5s,5s后同時關閉密封水閥和注滿水閥,這時并沖水閥仍打開,直到并沖時間(可設定)到關閉。這時運行等待間隔時間,等待間隔時間結束后,即全部排渣程序結束,離心機恢復進料。全排渣是通過將轉鼓內殘渣、油腳等重相排出機外,由操作員間隔一定時間(一般半天或一天)進行一次全排渣。生產過程中可按下“部排”、“全排”按鈕,隨時執(zhí)行手動的部分排渣和全部排渣操作。
(6)正常生產過程中PLC不斷檢測機器的狀態(tài)參數(shù),可通過各自模擬量畫面,查看歷史記錄曲線,設置高低限值,當實際參數(shù)超限值,報警或轉入待機狀態(tài)。離心機再循環(huán)運行排渣周期,所有上述控制流程由PLC和計算機編制控制程序自動控制運行。動作的時間參數(shù)由計算機界面設定,同時計時運行時間,這樣完全集成于總工藝流程,操作方便,顯示直觀。
控制系統(tǒng)硬件可采用西門子PLC模塊,一般在大的油脂精煉整個系統(tǒng)配置一塊數(shù)字量輸入(DI)模塊、一塊數(shù)字量輸出(DO)模塊、一塊模擬量輸入模塊(AI),電機和氣動電磁閥由數(shù)字量按程序控制其開關。通過模擬量輸入模塊(AI)和各種模擬量變送器(在訂購機器時選配)檢測離心機的運行狀態(tài)的參數(shù):如電流、振幅等。調試時先不啟動主電機,主要模擬運行各開關閥是否按時序要求運行正常,運行正常后可啟動電機正式試運轉。
3 結語
上述離心分離機控制程序的編寫,能夠克服單機設備單獨操作的設置及操作不方便的缺點,同時可設置各種非正常狀態(tài)的報警,隨時掌握機器的運行參數(shù),發(fā)現(xiàn)異常及時排除,在油脂精煉生產線中實際應用效果較好。