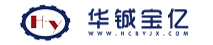
浙江巨化股份有限公司硫酸廠有兩套硫酸生產(chǎn)系統(tǒng),其中60kt/a裝置采用水洗凈化工藝,120kt/a裝置采用酸洗凈化工藝,兩系統(tǒng)凈化工序及其他生產(chǎn)裝置產(chǎn)生的酸性污水經(jīng)電石渣中和、沉降后送污水處理廠,經(jīng)進(jìn)一步處理后達(dá)標(biāo)排放。電石渣處理法所產(chǎn)生的污泥量較大,過去該廠將一部分污泥送至礦渣熄滅器,代替清水對(duì)礦渣進(jìn)行增濕,然后共同作為水泥配料外運(yùn);其余部分用槽車送到污泥處理場(chǎng)處理,經(jīng)沉淀、晾干后作為磚瓦添加劑。幾年來的運(yùn)行情況表明,該廠污泥處理裝置雖然基本能滿足需要,但污泥處理場(chǎng)占地面積大(15000㎡),處理費(fèi)用高,勞動(dòng)強(qiáng)度大,還存在一定的污染。
為了進(jìn)一步降低污水處理費(fèi)用,提高外排水質(zhì)量并取消污泥處理場(chǎng),該廠決定尋找新的污泥處理途徑。在對(duì)幾種污泥處理技術(shù)及設(shè)備進(jìn)行調(diào)研分析的基礎(chǔ)上,該廠開展了采用臥式螺旋卸料沉降離心機(jī)對(duì)硫酸裝置污泥進(jìn)行脫水的攻關(guān)項(xiàng)目。經(jīng)過不斷地改進(jìn)和完善,裝置運(yùn)行良好,脫水后的污泥混入礦渣外運(yùn),現(xiàn)將情況介紹如下:
1 離心機(jī)的工作原理及裝置流程
臥式螺旋卸料沉降離心機(jī)主要利用物料中各組成密度的差異對(duì)物料進(jìn)行脫水、濃縮、澄清及固體顆粒分級(jí)等操作,具有對(duì)物料適應(yīng)性強(qiáng)、處理量大、連續(xù)作業(yè)、無濾布、操作簡(jiǎn)單、運(yùn)行費(fèi)用低、占地面積小等優(yōu)點(diǎn)。
在分離過程中,懸浮液由進(jìn)料管加入,經(jīng)螺旋推料器內(nèi)的物料加速器進(jìn)入轉(zhuǎn)鼓,在離心力的作用下,密度較大的固相被拋向旋轉(zhuǎn)的轉(zhuǎn)鼓內(nèi)壁,再由螺旋推料器上的葉片推至轉(zhuǎn)鼓右端排渣口排出,密度較小的液相則通過轉(zhuǎn)鼓左端的溢流孔流出。螺旋與轉(zhuǎn)鼓同向回轉(zhuǎn),但具有一定的轉(zhuǎn)速差。由于沉渣在排出轉(zhuǎn)鼓之前經(jīng)過一段脫水區(qū)域進(jìn)一步脫水,因此沉渣含濕量較低,且在一定的進(jìn)料流量變化范圍內(nèi)保持不變。通過改變主、副機(jī)的轉(zhuǎn)速等技術(shù)參數(shù),該機(jī)可用于分離不同要求的物料。
該廠污泥脫水裝置的工藝流程為:沉淀池底的污泥用立式污泥泵送至離心機(jī)進(jìn)料口,脫水后的污泥(固相)從離心機(jī)下料口放至渣灰皮帶上隨礦渣一起外運(yùn),含有部分細(xì)小污泥顆粒的水(液相)從離心機(jī)溢流口連續(xù)排至污水處理裝置的吸水井,用污水泵送至沉淀池再次進(jìn)行沉淀。
2 裝置運(yùn)行及整改情況
根據(jù)該廠污泥的特性、主要成分、處理量等工藝參數(shù),生產(chǎn)廠家對(duì)原有定型離心機(jī)做了適當(dāng)改進(jìn),在此基礎(chǔ)上該廠進(jìn)行了污泥脫水試驗(yàn),對(duì)設(shè)備出現(xiàn)的問題進(jìn)行診斷,并進(jìn)行相關(guān)的改進(jìn)和完善。
硫酸裝置的污泥處理是困擾企業(yè)的環(huán)保難題。據(jù)調(diào)查,國(guó)內(nèi)未見用這類臥式螺旋卸料沉降離心機(jī)處理硫酸裝置污泥的報(bào)道。該廠在使用初期出現(xiàn)的問題主要有:
(1)運(yùn)行中經(jīng)常出現(xiàn)離心機(jī)內(nèi)葉結(jié)死,造成超負(fù)荷跳閘或脫水效率嚴(yán)重下降,必須將離心機(jī)解體沖洗干凈才能恢復(fù)運(yùn)行。
(2)分離液含固率太高,即脫水效率不高。
為此,該廠于離心機(jī)生產(chǎn)廠家一起多次進(jìn)行試驗(yàn)及改進(jìn)。針對(duì)硫酸裝置污泥粘度和密度較大的特點(diǎn),將離心機(jī)型號(hào)由LW500改為L(zhǎng)W400,將轉(zhuǎn)鼓的工作長(zhǎng)度由1500mm縮短到860mm,差速器功率由7.5kW改為11kW,副電機(jī)功率由5.5kW改為7.5kW,主機(jī)轉(zhuǎn)速?gòu)?300r/min調(diào)整為2100r/min,主、副機(jī)的差速比從23:1調(diào)整為28:1,下渣口也作了適當(dāng)改進(jìn)。
這些改進(jìn)較好地解決了離心機(jī)的易堵問題,確保了離心機(jī)的穩(wěn)定運(yùn)行,脫水效率也有一定的提高。裝置運(yùn)行穩(wěn)定后,其污泥處理量在8m3/h左右,脫水后污泥脫水率為13.5%左右,滿足了與礦渣一起外運(yùn)的要求。
離心機(jī)運(yùn)行正常后又出現(xiàn)了另一個(gè)問題——分離液中含有大量的細(xì)小顆粒,這樣就增大了沉淀池污水中懸浮物的含量,使其難以沉降,故而外排污水的懸浮物含量達(dá)不到國(guó)家一級(jí)排放標(biāo)準(zhǔn)(SS≤70mg/L)。對(duì)此,該廠在實(shí)驗(yàn)室試驗(yàn)的基礎(chǔ)上,開始了向污水中添加陰離子聚丙烯酰胺絮凝劑的試驗(yàn)。從試驗(yàn)情況看,效果較為明顯,外排污水中懸浮物含量的合格率由前3個(gè)月的37.5%上升到87.5%。
3 效益分析
通過整改,該廠成功地將臥式螺旋卸料沉降離心機(jī)應(yīng)用于硫酸裝置的污泥脫水,收到了 較好的環(huán)境效益和經(jīng)濟(jì)效益。離心機(jī)運(yùn)行正常后,大大減少了去污泥處理場(chǎng)的污泥槽車數(shù)量;處理后污水中的懸浮物含量符合污水處理廠的進(jìn)水要求,從而確保了污水處理廠的穩(wěn)定運(yùn)行及外排水的質(zhì)量。
按離心機(jī)處理能力8m3/h、污泥(漿)密度1310.3kg/m3、每年運(yùn)行時(shí)間300d、每輛槽車裝污泥50t、每輛槽車運(yùn)費(fèi)250元計(jì),每年可減少污水處理費(fèi)用37.4萬元,同時(shí)污泥回收作為礦渣出售,一年可增加收益5萬元,除去離心機(jī)每年運(yùn)行費(fèi)用5萬元,經(jīng)濟(jì)效益十分可觀。
4 結(jié)語
通過多次的試驗(yàn)和整改,臥式螺旋卸料沉降離心機(jī)在我廠污泥脫水中得到了成功的應(yīng)用,從而為硫酸裝置的污泥處理又找到了一種方法。為了完全取消污泥處理場(chǎng),減小污泥處理裝置的占地面積,該廠決定再上一臺(tái)臥式螺旋卸料沉降離心機(jī)。對(duì)沉淀池中細(xì)顆粒含量增高繼而使處理后污水懸浮物含量增高的問題,該廠將從兩方面入手:一方面繼續(xù)進(jìn)行添加聚丙烯酰胺絮凝劑的試驗(yàn),以確定合適的絮凝劑加量及絮凝工藝;另一方面,將離心機(jī)脫水后產(chǎn)生的分離液送入焙燒工序的礦渣增濕器而不是返回沉淀池,以確保外排污水懸浮物含量達(dá)到國(guó)家一級(jí)排放標(biāo)準(zhǔn)。