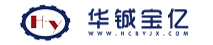
1 前言
臥螺沉降離心機作為一種高效的固液分離設(shè)備,被廣泛地應(yīng)用于石油、建筑、化工等行業(yè),利用固液兩相的密度差及離心作用力來實現(xiàn)固體與液體的分離。在離心脫水過程中,臥螺離心機的結(jié)構(gòu)參數(shù)、操作參數(shù)以及物料性質(zhì)都會對脫水效果造成影響。由于離心分離過程的復(fù)雜性、懸浮液特性的易變性、特別是固相顆粒的形狀和粒徑分布的多態(tài)性,給理論和試驗研究造成了極大的困難。對于物料性質(zhì)來說,污泥的調(diào)質(zhì)將會對后續(xù)的脫水工藝與設(shè)備產(chǎn)生較大影響,是污泥濃縮和脫水重要的前處理過程,其方法主要包括化學(xué)法、加熱法、淘洗法、冷凍法和加骨粒法等,新型調(diào)質(zhì)技術(shù)主要有超聲、微波、熱水解、磁場、電滲透、生物絮凝等。
為進一步提高脫水效果,降低污泥的含水量,國內(nèi)外學(xué)者進行了大量的理論和試驗研究。大量理論和試驗研究結(jié)果表明,可以從提高分離因數(shù)、增加機械擠壓和延長停留時間三個方面來改善脫水性能。但試驗研究因不能任意改變離心機的結(jié)構(gòu)尺寸,不能同時針對多個工藝參數(shù)進行,不能系統(tǒng)考慮調(diào)質(zhì)技術(shù)使用前后污泥脫水效率的變化而具有一定的局限性。
近年來,計算機技術(shù)與計算流體動力學(xué)(CFD)的發(fā)展為臥螺離心機流場的研究開辟了新的方向。本研究結(jié)合污泥調(diào)質(zhì)技術(shù)對臥螺離心機進行CFD模擬,旨在研究臥螺離心機的長徑比、螺旋及污泥黏度對分離性能的影響,同時考察不同粒徑的物料在不同轉(zhuǎn)速下的分離效率。
2 數(shù)值模擬方法
2.1 幾何模型和網(wǎng)格劃分
臥螺離心機中轉(zhuǎn)鼓和螺旋輸送器以一定的轉(zhuǎn)差運轉(zhuǎn),以實現(xiàn)懸浮液的分離和沉渣的排出。模擬所用臥螺離心機的主要尺寸如下所述:轉(zhuǎn)鼓圓柱段外直徑420mm,圓錐段長度325mm,錐角8°,液層深度45mm,進料管外直徑60mm,進料管長度1200mm。考慮螺旋的情況下,先通過NX6.0建立螺旋輸送器的模型,用螺旋輸送器切轉(zhuǎn)鼓實體即可得到液流區(qū)域,然后將模型轉(zhuǎn)換為CAD圖形,讀入Fluent進行模擬計算。
2.2 邊界條件和求解策略
計算所用液體密度為1015kg/m3,液體黏度為0.001003Pa·s。進料管入口設(shè)為速度入口邊界,指定入口處的液流速度為0.5m/s,入口湍流強度按經(jīng)驗公式來估算。臥螺離心機出口為溢流出口,設(shè)定出口為Outflow邊界條件。轉(zhuǎn)鼓外壁設(shè)定為無滑移固壁邊界條件,自由液面處壁面設(shè)定為滑移切應(yīng)力為0,給定臥螺離心機轉(zhuǎn)鼓的轉(zhuǎn)動角速度設(shè)為30~50rad/s,轉(zhuǎn)差設(shè)置為2~5rad/s。
應(yīng)用控制容積積分法離散控制方程組,各方程對流項的離散采用精度較高的QUICK差分格式,壓力與速度的耦合采用SIMPLE算法。臥螺離心機內(nèi)部流場為較為復(fù)雜的旋轉(zhuǎn)占優(yōu)流動,因此選取精度較高的RSM湍流模型封閉控制方程組。模擬固體顆粒的運動過程時選取DPM模型,考慮螺旋輸送器時選取滑移模型。
3 結(jié)果與分析
3.1 整體流場
選取離心機長徑比為4,轉(zhuǎn)鼓角速度為50rad/s,做z=500mm和y=0mm兩處截面的靜壓分布??梢钥闯?,靜壓沿徑向從中心向外逐漸增加,自由液面處靜壓小,在轉(zhuǎn)鼓壁面處達到極值。由于入口與溢流口都與大氣相連,所以此兩處的靜壓接近于零值。
選取離心機長徑比為4,入口速度升為0.5m/s,做整體速度場在截面y=0mm上的流場速度云圖,轉(zhuǎn)鼓軸向方向z=900mm截面的等速度線圖??梢钥闯觯黧w以一定的速度進入臥螺離心機,由于分料作用在分料口速度降低,然后隨高速旋轉(zhuǎn)轉(zhuǎn)鼓的帶動進入分離場,在接近轉(zhuǎn)鼓處速度開始升高,當(dāng)流體到達分離場中部時流場中心位置處的速度梯度??;流體接近溢流口處,流場中心近壁面的速度降低但速度梯度增大,由此可知此時固液仍可進行分離過程,這表明增加轉(zhuǎn)鼓長度的重要性。如果轉(zhuǎn)鼓長度不足,將嚴(yán)重影響分離過程的進行,甚至不能完成分離過程。因此,大長徑比有利于離心機的固液分離。
3.2 長徑比對臥螺離心機流場的影響
3.2.1 長徑比對流場壓力分布的影響
從靜壓力的徑向分布可以看出,不同長徑比下靜壓沿徑向的分布規(guī)律基本一致,即靜壓力沿徑向從中心向外逐漸增加,基本呈線性分布,自由液面處靜壓小,在轉(zhuǎn)鼓壁面處達到極值,說明增加液環(huán)層的厚度靜壓力值會顯著增大。當(dāng)長徑比從2.5增大到3.5時,同一徑向位置處的靜壓隨著長徑比的增大而減小,說明此時增大長徑比可以減小阻力損失。但是進一步增大長徑比,即長徑比由3.5增大到4.0時,同一徑向位置處的靜壓隨著長徑比的增大而迅速增大,說明此時增大長徑比將增加阻力損失。
從截面平均壓力沿軸向的分布可以看出,同一長徑比下截面平均壓力沿軸向的變化不大,但是同一軸向位置處截面平均壓力隨長徑比的變化較大,隨長徑比壓力的變化與徑向分布規(guī)律類似。
3.2.2 長徑比對切向速度分布的影響
臥螺離心機轉(zhuǎn)鼓內(nèi)液流的流動方向可以分為軸向、切向和徑向三個方向,其中軸向速度和切向速度可以表征離心機分離過程的效果。軸向速度是表征臥螺離心機生產(chǎn)能力的一個物理參量,軸向流速越大,表示生產(chǎn)能力越強,但軸向速度過大又會導(dǎo)致脫水效果下降,致使沉渣含濕率上升。
臥螺離心機的工作原理使分離液中的固體顆粒在離心力的作用下沿徑向向外運動并產(chǎn)生分離,切向速度是分離液中固液發(fā)生分離的關(guān)鍵,在研究臥螺離心機時一般采用旋轉(zhuǎn)角速度進行分析。轉(zhuǎn)鼓的轉(zhuǎn)動帶動液層一起旋轉(zhuǎn),但液體的旋轉(zhuǎn)和轉(zhuǎn)鼓的旋轉(zhuǎn)并不一致,存在滯后現(xiàn)象。
經(jīng)過模擬,結(jié)果顯示在液層深度、轉(zhuǎn)鼓轉(zhuǎn)速和入口流速不變的情況下,長徑比變化對切向速度影響不大,說明長徑比對切向速度滯后系數(shù)的影響不明顯。然而,長徑比增大會使分離空間增大,從而促進固液分離,因此增大長徑比有利于提高臥螺離心機的分離性能。與靜壓分布的研究相結(jié)合,繼續(xù)增大長徑比會使阻力損失顯著升高,因此選擇長徑比時應(yīng)綜合考慮分離性能和阻力損失兩方面的因素。
3.3 黏度對臥螺離心機流場的影響
3.3.1 黏度對壓力分布的影響
黏度升高對自由液面附近的靜壓力基本沒有影響,在轉(zhuǎn)鼓近壁面附近靜壓力隨黏度的升高而有一定的升高,本文考察的范圍內(nèi)黏度對阻力損失的影響不大。
3.3.2 黏度對切向速度分布的影響
在黏度變化相對較小時切向速度變化也較小,隨著黏度的增大,切向速度逐漸降低,因此流體的黏度對切向速度有一定影響。當(dāng)黏度大時切向速度相應(yīng)較小,而較低的切向速度對于分離過程是不利的,因此降低流體黏度更有利于固液分離。
3.4 污泥調(diào)質(zhì)對脫水特性的影響
目前已有多種調(diào)質(zhì)技術(shù),使用調(diào)質(zhì)技術(shù)如熱水解、超聲與微波等可以使污泥的特性如黏度與粒度等發(fā)生改變。下面將對有螺旋和無螺旋兩種情況進行對比,結(jié)合污泥的調(diào)質(zhì)分析懸浮液黏度、顆粒的粒徑分布及離心機中螺旋對分離效率的影響。
3.4.1 懸浮液黏度對脫水特性的影響
懸浮液的黏度主要取決于液相的黏度和懸浮液的濃度,通過理論分析和單相流場模擬可知,黏度對離心機分離效率有影響?,F(xiàn)選取本課題組污泥調(diào)質(zhì)特性研究測得的污泥黏度作為模擬數(shù)據(jù),分析調(diào)質(zhì)技術(shù)對污泥脫水效率的影響。
從結(jié)果可以看出,在無螺旋情況下,隨著黏度的增大,離心機分離效率略有降低,由于黏度變化值較小,所以分離效率的變化幅度不是很明顯。相同黏度下,分離效率隨著長徑比的增大而增大,說明大長徑比有利于固液分離,上述結(jié)果與單相流場的模擬結(jié)果以及理論分析結(jié)果相符合。而在有螺旋情況下,隨著黏度的增大離心機分離效率有增有減,這是由于黏度的變化幅度不大,而且在螺旋的作用下流場內(nèi)湍流變化明顯,與層流理論不相符合。但在相同黏度下,分離效率隨長徑比增大而增大,說明即使在有螺旋的情況下,大長徑比離心機也利于固液分離。有螺旋與無螺旋這兩種情況相比,由于螺旋的推進作用有促使顆粒向離心機圓錐段運動,其次螺旋還可阻擋部分回流的固體顆粒,因此離心機中的螺旋設(shè)計促進了固液兩相的有效分離。
3.4.2 粒徑分布對脫水效果的影響
粒徑分布是影響固液分離的重要因素之一,相同體積分?jǐn)?shù)下不同粒徑分布的污泥其脫水效率也有所不同。為了研究固液分離時的較佳粒徑分布及離心機中螺旋對分離效率的影響,指導(dǎo)污泥的調(diào)質(zhì)改性方向,采用DPM模型、滑移網(wǎng)格對不同粒徑下固體顆粒的運動過程進行模擬仿真,從長徑比為4.0、入口速度為0.5m/s時各轉(zhuǎn)速條件下顆粒的分離效率出發(fā),對于懸浮液中不同的固相粒度分布得出不同的分離效率。
從結(jié)果可以看出,隨著轉(zhuǎn)鼓轉(zhuǎn)速的增加,分離效率隨之增大,而懸浮液中顆粒粒徑越大,其分離效率越高,反之越低。這是由于轉(zhuǎn)速越大、顆粒粒徑越大,顆粒所受離心力越大,越有利于固液分離。根據(jù)粒徑分布來選擇合適的轉(zhuǎn)鼓轉(zhuǎn)速并選用有螺旋設(shè)計的機型,在降低離心機能耗的同時,也能保持臥螺離心機分離效率維持在較合理的水平。
4 結(jié)論
本文采用流體力學(xué)軟件FLUENT,將離心機三大基本方程與CFD仿真軟件有效結(jié)合,分析了理論和試驗中尚難以處理的結(jié)構(gòu)復(fù)雜的臥螺離心機旋轉(zhuǎn)流場。研究了流場速度和壓力分布的變化規(guī)律,并有針對性地得到了部分操作參數(shù)對分離場的影響規(guī)律。
(1)在單相無螺旋流場中,隨著長徑比的增大,轉(zhuǎn)鼓內(nèi)壁處壓力值先變小后增大,因此就本研究的研究范圍來看,大長徑比有利于固液分離,但過大會使阻力損失顯著升高,長徑比為3.5為較佳選擇。
(2)黏度的增加不利于離心機分離效率提高,在本文考察范圍內(nèi)由于污泥黏度較低且變化不大對分離效果總體影響不大。相同黏度下,分離效率隨長徑比增大而增大,說明大長徑比利于固液分離。
(3)離心機中螺旋的設(shè)計使得流場內(nèi)層流理論發(fā)生變化,模擬結(jié)果表明離心機的螺旋設(shè)計使分離效率明顯優(yōu)于無螺旋情況,因此螺旋的存在有利于固液分離。