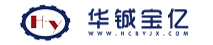
1 引言
含油污泥主要是石油勘探開發(fā)和石油化工行業(yè)產(chǎn)生的油泥、油砂(其中顆粒粒徑大于等于74um的為油砂,小于74um的為油泥),具有產(chǎn)生量大、含油量高、重質油組分高、綜合利用方式少、處理難度大等特點。含油污泥若不加以處理,不但污染環(huán)境,而且造成資源的浪費。含油污泥一直是困擾油田生產(chǎn)和發(fā)展的一大難題。
2 含油污泥的特點和處理現(xiàn)狀
2.1 含油污泥的來源
含油污泥的來源主要有3種途徑。
2.1.1 原油開采
原油開采過程中產(chǎn)生的含油污泥主要來源于地面處理系統(tǒng),采油污水處理過程中產(chǎn)生的污泥,再加上污水凈化處理中投加的凈水劑形成的絮體、設備及管道腐蝕產(chǎn)物和垢物、細菌(尸體)等組成了含油污泥。
2.1.2 油田集輸過程
含油污泥主要來源于接轉站和聯(lián)合站的油罐、沉降罐、隔油池底泥,煉廠含油水處理設施、天然氣凈化裝置清除出來的油砂、油泥,鉆井、作業(yè)、管線穿孔而產(chǎn)生的落地原油及含油污泥。
2.1.3 煉油廠污水處理場
煉油廠污水處理場產(chǎn)生的含油污泥主要來源于隔油池底泥、浮選池浮渣、原油罐底泥等。
2.2 含油污泥的特點
油田含油污泥的組成成分極其復雜,一般由水包油、油包水以及懸浮固體雜質組成,是一種極其穩(wěn)定的懸浮乳狀液體系,含有大量的老化原油、蠟質、瀝青質、膠體、固體懸浮物、細菌、鹽類、酸性氣體、腐蝕產(chǎn)物等,還包括生產(chǎn)過程中投加的大量絮凝劑、緩蝕劑、阻垢劑、殺菌劑等水處理劑。因此含油污泥乳化充分,黏度較大,固相難以徹底沉降,給污泥處理帶來很大的難度。
2.3 含油污泥的危害
含油污泥是油田開發(fā)和儲運過程中產(chǎn)生的主要污染物之一,含油污泥得不到及時處理,將會對生產(chǎn)區(qū)域和周邊環(huán)境造成不同程度的影響:一是含油污泥中的油氣揮發(fā),使生產(chǎn)區(qū)域內(nèi)空氣質量存在總烴濃度超標的現(xiàn)象;二是散落和堆放的含油污泥污染地表水甚至地下水,使水中COD,BOD和石油類嚴重超標;三是含油污泥含有大量的原油,造成土壤中石油類超標,土壤板結,使區(qū)域內(nèi)的植被遭到破壞,草原退化,生態(tài)環(huán)境受到影響。另外,一部分污泥在脫水和污水處理系統(tǒng)中循環(huán),造成脫水和污水處理工況惡化,致使污水注入壓力越來越大,損耗能量巨大。由于含油污泥中含有硫化物、苯系物、酚類、蒽、芘等有惡臭的有毒有害物質,而且原油中所含的某些烴類物質具有致癌、致畸、致突變作用,因而油田含油污泥已被列為危險固體廢棄物(HW08),納入危險廢物進行管理。
此外,含油污泥對油田生產(chǎn)造成了極大的影響。
(1)含油污泥的存在使回注水中懸浮物含量嚴重超標,堵塞地層,造成油層吸水能力下降,注水壓力不斷升高;同時,使水井增注措施(主要是酸化)有效期下降,增加了處理費用和工作量。
(2)為確保注水水質,防止懸浮物在系統(tǒng)中惡性循環(huán),每天被迫外排大量的污水,既造成水資源浪費又污染了環(huán)境。
(3)由于大顆粒在沉降罐、凈化污水罐、污水池中不斷沉積,使清罐周期縮短,清出的大量污泥含水率高,無處堆放,污染環(huán)境,增加了成本投入。
2.4 含油污泥的處理現(xiàn)狀
國內(nèi)外處理含油污泥的方法一般有焚燒法、生物處理法、熱洗滌法、溶劑萃取法、化學破乳法、固液分離法等。其中焚燒法耗能大、產(chǎn)生二次污染、油資源也沒得到回收利用;生物處理法需將含油污泥混以松散劑、肥料和培菌液,經(jīng)常顫動并自然通風,歷時41d才能將97%的石油烴生物降解,同樣油資源也沒有得到回收利用;溶劑萃取法存在的問題是流程長,工藝復雜,處理費用高,只對含大量難以降解的有機物的含油污泥適用;化學破乳法對乳化嚴重的含油污泥需另加破乳劑和加熱;固液分離法對于含油高、污染嚴重的含油污泥,油回收率低??梢姡@些方法由于投資、處理效果及操作成本等原因,未能在國內(nèi)普及應用。目前,我國含油污泥處理問題一直難以得到有效解決。
3 含油污泥處理技術的進展
3.1 含油污泥調質-機械分離技術
濃縮、化學調節(jié)(即調質)、脫水是含油污泥處理系統(tǒng)必不可少的3個環(huán)節(jié)。高含水量的含油污泥不能直接進行機械脫水操作,必須先進行調質;通過調質-機械分離,使含油污泥實現(xiàn)油-水-泥的三相分離。污泥脫水過程實際上是污泥的懸浮粒子群和水的相對運動,而污泥的調質則是通過一定手段調整固體粒子群的性狀和排列狀態(tài),使之適合不同脫水條件的預處理操作。
調質要根據(jù)含油污泥的性質、脫水機械的性能和濾餅的后續(xù)處理方法等因素選擇合適的調節(jié)劑。研究發(fā)現(xiàn),無機絮凝劑中,聚合氯化鋁(PAC)的效果較好;有機絮凝劑中,陽離子型聚丙烯酰胺(PAM)由于具有正電荷中和與吸附架橋的雙重作用,絮凝效果比非離子型聚丙烯酰胺(CPAM)好。有機和無機絮凝劑都有投加量適度的問題,投加量過大會使污泥比阻升高,水分難以去除。經(jīng)絮凝處理的含油污泥,加入合適的助濾劑CaO可降低污泥的比阻。
脫水的關鍵是通過解吸附和破乳來降低含油污泥中油的含量。因此,含油污泥的調質,除投加混凝劑、助凝劑外,還必須投加表面活性劑、破乳劑、pH調節(jié)劑等,同時輔以加熱等強化手段,以改善污泥的脫水性能。Bock等、Srivatsa等、Corti等分別發(fā)明了通過調質-機械脫水工藝回收油的專利技術:通過投加表面活性劑、稀釋劑(葵烷等)、電解質(NaCl溶液)或破乳劑(陰離子或非離子)、潤濕劑、pH值調節(jié)劑等,并輔以加熱減黏(50℃以上)等調質手段,實現(xiàn)了油-水-泥三相分離。
機械脫水主要技術有真空過濾、加壓過濾、滾壓過濾和離心過濾,其原理是在過濾介質兩面產(chǎn)生壓差,使固體顆粒被截留而水分通過。目前國內(nèi)主要使用板框壓濾機和帶式壓濾機,而國外廣泛使用的是帶式壓濾機和臥式螺旋卸料沉降離心機。集污泥濃縮、油水分離于一體的三相臥螺沉降離心機是今后含油污泥處理設備的發(fā)展方向。帶式壓濾機在使用中取得較好的脫水效果,調質污泥依次經(jīng)過重力區(qū)、楔形區(qū)、中壓區(qū)和高壓區(qū),先在重力區(qū)脫除部分水,接著在楔形區(qū)脫去大部分水,進入中壓區(qū)和高壓區(qū),脫除油和水,脫水后的泥餅外運。
調質-機械分離技術是一種比較成熟的含油污泥處理技術,油的回收率較高。由于不同地區(qū)含油污泥成分不同,需要藥劑和脫水機械相適應,同時要優(yōu)化藥劑的種類、投加數(shù)量及脫水機械的運行參數(shù)。
3.2 溶劑萃取處理工藝
溶劑萃取作為一種用以除去污泥所夾帶的油和其他有機物的單元操作技術而被廣泛研究,溶劑包括丙烷三乙胺、重整油和臨界液態(tài)CO2等。油類從污泥中被溶劑抽提出來后,通過蒸餾把溶劑從混合物中分離出來循環(huán)使用。經(jīng)萃取后大多泥渣都能達到BDAT(美國環(huán)保局指定的示范有效技術的處理標準)要求,回收油則用于回煉。
張秀霞等介紹了一種使用三氯甲烷溶劑萃取蒸汽蒸餾處理含油污泥的工藝實驗。含油污泥脫水后,自然風干去除雜物,粉碎。用三氯甲烷將污泥溶解,經(jīng)攪拌和離心后回收萃取液。含有殘余重油和溶劑的污泥,進入下一步蒸汽蒸餾處理。該方法可使油泥脫油率高達90%以上,比單一的溶劑萃取和直接蒸餾處理的效果好,但尚未在工廠中得到檢驗。
3.3 高溫裂解工藝
高溫裂解技術是指含油污泥在絕氧的條件下加熱到一定溫度(一般為450℃左右,甚至更高),使烴類物質在復雜的水合和裂化反應中分離出來,并冷凝回收。該工藝對含油污泥處理得比較徹底,處理后的高溫污泥含油達0.01%(100mg/kg),可以直接填埋或拋灑。
高溫裂解與通常的帶壓過濾、離心作用和細菌處理等工藝相比具有三大優(yōu)點:一是由于高溫裂解設備與其他工藝的生產(chǎn)設備類似,可利用現(xiàn)有的部分生產(chǎn)設備,經(jīng)過改造就能滿足要求;二是通常的工藝過程,易揮發(fā)有機組分會溢出到大氣中,而高溫裂解工藝通過冷凝對烴蒸汽加以回收,使污泥中的油(烴類物質)回收率較高;三是高溫裂解工藝的整個過程是在一個密閉的環(huán)境下進行,減少了外圍設施受污染的幾率,而且占地面積相對較小。缺點是熱消耗大,投資較高。
3.4 生物處理技術
目前,生物處理是比較有效的一種含油污泥處理技術,也是今后發(fā)展的方向之一。生物處理的主要原理是微生物利用石油烴類作為碳源進行同化降解,使其完全礦化,轉變?yōu)闊o害的無機物質(CO和HO)的過程。污油微生物降解可以按過程機理分為兩個方向:一是向油污染點添加具有高效油污降解能力、自然形成并經(jīng)選擇性分離出的細菌、化肥和一些生物吸附劑;二是曝氣,向油污染點投加含氮磷的化肥,刺激污染點微生物群的活性。
生物處理技術操作方便,作用持久,無二次污染(產(chǎn)物為CO2和H2O),處理成本低,已在國內(nèi)得到廣泛的商業(yè)化應用,并將成為未來含油污泥無害化處理的主要方式之一,但目前仍存在著選擇合適的菌種困難,處理周期長,對環(huán)烷烴、芳烴、雜環(huán)類處理效果差,對高含油污泥難適應等問題。
4 新型含油污泥處理工藝
4.1 工藝流程
工藝流程是將污泥送入加熱池,在水力攪拌下加入破乳劑進行加熱攪拌,加熱均化后泵入一級超聲波反應器,而將曝氣設備安裝在反應器中解決了油泥進入反應器后迅速沉降的缺點,使超聲波更好地作用在油泥上,提高了除油效率;經(jīng)過反應分離后的原油通過反應器上部的出油口排出;然后將剩余的油泥混合物在泵入二級超聲波反應器再除油;經(jīng)二次超聲處理后除油率能達到90%以上,將二次除油后的油泥泵入離心機進行固液分離,處理出的泥可達標排放或回用,而液體(水、少部分油)直接循環(huán)利用。也可將液體送入凈化罐利用氣浮技術再次進行油水分離,使水能夠達標排放。
4.2 工藝特點
4.2.1 超聲波技術
該工藝流程主要以調質-機械分離技術和超聲技術為核心對含油污泥進行處理。目前應用調質-機械分離技術對油泥進行處理的實例較多,而超聲技術在油泥處理上的應用則屈指可數(shù)。超聲技術具有能耗低、效率高、反應時間短、設備簡單、占地面積小等優(yōu)點而被廣泛應用于工業(yè)、農(nóng)業(yè)、醫(yī)學、生物學、化學化工等領域。而近幾年對超聲波處理含油污泥進行了大量實驗,取得了良好的處理效果。
4.2.2 曝氣設備和氣浮裝置
該工藝采用的是獨特的曝氣設備和氣浮裝置。曝氣設備的風源采用國內(nèi)先進的ZSLR型羅茨風機供風。釋放器正反旋轉,形成一個氣液強化漩流區(qū),而且是連續(xù)進行3次切割碰撞,加速氣液面的更新,提高曝氣效果。該釋放器采用了耐酸堿、抗腐蝕的合成樹脂材質,具有抗污染效果好、使用年限長的特點;氣浮裝置主要特點是采用了高效溶氣機,產(chǎn)生的氣泡直徑在15~40um之間,達到理想氣泡的標準,是目前其他各種產(chǎn)氣方法難以達到的。此微細氣泡附著力強,分離速度快,能夠有效地實現(xiàn)液液、固液分離,分離后油的去除率高達95%以上,懸浮固體去除率高達80%以上。出水油含量小于10mg/L,懸浮物含量小于30mg/L。
4.3 超聲波處理含油污泥原理
超聲波發(fā)生器產(chǎn)生的高頻震蕩信號由超聲波換能器轉換成高頻機械震蕩波傳播到介質——含有污泥的溶液中,超聲波在含有污泥溶液中疏密相間地向前輻射,使液體流動而產(chǎn)生數(shù)以萬計的小氣泡。這些氣泡在超聲波縱向傳播的負壓區(qū)形成、生長,而在正壓區(qū)迅速閉合。在這種被稱為“空化效應”的過程中,氣泡瞬間閉合可形成超過1000個大氣壓的高壓,就像“小爆炸”連續(xù)不斷地沖擊污泥的表面,使污泥表面上的油迅速剝落,從而達到迅速清潔的目的。
5 結語
國內(nèi)污泥處理技術尚處于起步階段,而國外由于其發(fā)展較早和環(huán)保政策嚴格,在含油污泥處理技術和工藝方面比較成熟,具有比較豐富的設計和運行管理經(jīng)驗,值得借鑒。
含油污泥的處理工藝多樣,各有所長,僅靠單一的處理工藝很難達到環(huán)保要求。將各種工藝結合起來,取長補短,是實現(xiàn)含油污泥徹底無害化的發(fā)展方向之一。從目前來看,以離心分離技術為核心多種預處理和后續(xù)處理技術相結合的工藝比較可行,而超聲波技術也將在未來含油污泥處理中發(fā)揮更大的作用。