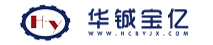
脫硫廢水含有較高質(zhì)量分數(shù)的懸浮物(約1%~3%,高時達到5%),對其處理一般采用混凝澄清工藝。脫硫廢水處理過程中投加了凝聚劑和石灰,所產(chǎn)生的沉淀物主要成分為硫酸鈣和亞硫酸鈣,還有部分氟化鈣、二氧化硅、碳酸鈣及氫氧化鎂、硫化汞等多種重金屬。經(jīng)澄清器濃縮后,所排污泥固體質(zhì)量分數(shù)(含固率)可提高至5%~8%。為進一步減少污泥體積,方便處置,需對污泥進行脫水處理。目前國內(nèi)各電廠脫硫廢水污泥處理設(shè)備主要有板框式壓濾機和離心式脫水機2種。某電廠脫硫廢水處理系統(tǒng)原污泥處理采用離心式脫水機,由于故障頻繁,長期無法正常運行;后改用板框式壓濾機,并輔以污泥緩沖罐、污泥循環(huán)泵和污泥給料泵等,運行效果良好。下文以該電廠為例,對脫硫廢水污泥脫水方式進行比較和研究。
1 污泥脫水設(shè)備脫水原理簡介
污泥中水的存在形式包括空隙水、毛細水、表面吸附水和內(nèi)部結(jié)合水。其中空隙水和顆粒間隙中的毛細水約占70%。污泥脫水主要是采用擠壓或離心甩脫的方式將污泥中的空隙水和毛細水分離出來。污泥脫水使用的設(shè)備種類較多,比較常用的有板框式壓濾機和離心式脫水機2種。
板框式壓濾機是間歇操作的過濾設(shè)備,混合液通過泥漿泵抽至過濾介質(zhì)(濾布)的空腔內(nèi),固體停留在濾布上,并逐漸在濾布上堆積形成過濾泥餅,經(jīng)過進料泵出口壓力擠壓,濾液滲透過濾布,稱為不含固體的清液。其優(yōu)點為濾餅含固率高,分離效果較好。
離心式脫水機利用離心沉降原理進行污泥脫水,離心沉降是將泥水以較高的角速度旋轉(zhuǎn),當(dāng)角速度達到一定值時,因離心加速度比重力加速度大得多,固相和液相很快分層。
2 某電廠污泥脫水系統(tǒng)改造實例
2.1 原污泥脫水系統(tǒng)簡介及存在問題
某電廠脫硫廢水處理系統(tǒng)采用經(jīng)典的石灰-混凝工藝,出力約為15m3/h。
經(jīng)實驗檢測,澄清器底部濃縮后的污泥沉降比SV(混合液在量筒內(nèi)靜置30min后所形成沉淀污泥的容積占原混合液容積的體積分數(shù),以百分比表示)約60%,該指標(biāo)能夠相對反應(yīng)污泥凝聚、沉淀性能。該澄清器底部濃縮后的濕污泥懸浮物質(zhì)量濃度、濕污泥濾液某些指標(biāo)及干污泥(80℃溫度下烘干24h)中有害物質(zhì)分析結(jié)果如下:
檢測項目 | 分析結(jié)果 |
懸浮物(g/L) | 79.75 |
Cl-(mg/L) | 8090 |
pH值 | 8.87 |
總?cè)芙庑怨腆w(mg/L) | 26200 |
電導(dǎo)率(mS/cm) | 26.90 |
硫酸根(mg/L) | 18303.85 |
干污泥總汞(10-6) | 1.995 |
干污泥總鉛(10-6) | 1.158 |
干污泥總鉻(10-6) | 1.234 |
干污泥總砷(10-6) | 1.003 |
干污泥總鎳(10-6) | 0.854 |
經(jīng)計算,該脫硫廢水系統(tǒng)產(chǎn)生的干污泥量約為3.6t/d。電廠原有污泥脫水系統(tǒng)采用的國產(chǎn)離心式脫水機主要參數(shù)如下:
項目 | 數(shù)值 |
轉(zhuǎn)鼓直徑(mm) | 360 |
轉(zhuǎn)鼓轉(zhuǎn)速(r/min) | 4200 |
外形尺寸(mm) | 2890×1580×1040 |
電機功率(kW) | 22 |
差轉(zhuǎn)速(r/min) | 2~20 |
分離因數(shù) | 3550 |
整機質(zhì)量(kg) | 2340 |
離心式脫水機投運2年以來,運行狀況不佳,主要缺陷有以下幾點:
(1)設(shè)備運行噪聲過大,接近或超過國家相關(guān)標(biāo)準要求。
(2)設(shè)備運行時對污泥濃度均勻性要求較高,離心脫水機運行過程中經(jīng)常因污泥濃度過高或過低跳閘,轉(zhuǎn)鼓磨損嚴重,設(shè)備后期維護投入較大。
(3)污泥經(jīng)脫水后泥餅含水率大于80%,呈半流體狀,塑性較差,裝卸運輸中造成二次污染。
2.2 污泥脫水系統(tǒng)改造
經(jīng)過經(jīng)濟和技術(shù)比較,某電廠決定將國產(chǎn)離心脫水機更換為某進口品牌板框式壓濾機,并新增污泥緩沖罐,配套設(shè)置污泥循環(huán)泵和污泥給料泵;壓濾機系統(tǒng)配套濾布清洗裝置和壓縮空氣反吹裝置。
改造后的污泥脫水工藝流程如下:
(1)脫硫廢水污泥經(jīng)澄清器濃縮后進入污泥緩沖罐進一步混合濃縮。污泥緩沖罐設(shè)循環(huán)泵2臺,讓污泥從底部抽出從上部進入,如此反復(fù)循環(huán),將泥質(zhì)調(diào)和均勻,保證進入板框壓濾機的污泥性質(zhì)穩(wěn)定,同時污泥循環(huán)可避免緩沖罐內(nèi)污泥沉積堵塞管道。
(2)污泥給料泵將污泥輸送至板框壓濾機。給料泵采用1大1?。ù蟊酶吡髁康蛽P程,小泵低流量高揚程)變頻控制。隨著壓力的升高,低壓泵停運,只剩下高壓泵穩(wěn)壓,至壓濾機內(nèi)部壓力維持在設(shè)定值一段時間。
(3)壓濾機濾液的濁度較小,水質(zhì)優(yōu)于脫硫廢水系統(tǒng)來水,將其直接回收至脫硫廢水處理系統(tǒng)進水端。
(4)壓濾機配套高壓清洗裝置,與清洗水箱、高壓清洗泵配套使用。運行中污泥黏附和堵塞濾布,降低了濾布過水能力,故設(shè)備運行一段時間必須對濾布進行清洗。建議清洗周期不低于每周1次。
脫硫廢水污泥處理系統(tǒng)的核心設(shè)備為板框式壓濾機,主要參數(shù)如下:
項目 | 數(shù)值 |
濾板尺寸(mm) | 800×800 |
干泥量(t/d) | 3.6 |
工作周期(次/d) | 4 |
室腔數(shù)(個) | 67 |
廂式濾板數(shù)(個) | 68 |
室腔厚度(mm) | 32 |
濾室容積(L) | 1045 |
過濾面積(㎡) | 74 |
濾板材質(zhì) | 聚丙烯 |
濾布材質(zhì) | 聚丙烯 |
與污泥接觸部分材質(zhì) | 聚丙烯 |
外形尺寸(mm) | 7515×2120×2290 |
重量(kg) | 6800 |
壓濾機每天運行4個周期,每個周期工作約90min(進料時間50min,反吹約2min,穩(wěn)壓滴水時間約5min,卸泥時間約30min)。過濾時壓濾機處于關(guān)閉帶壓狀態(tài),污泥由給料泵(變頻控制)輸送至壓濾機腔室,固體截留在濾布上面,濾液在高壓強的作用下透過濾布,經(jīng)導(dǎo)管排出設(shè)備外。當(dāng)污泥給料泵出口壓力達到設(shè)定值后,壓濾機自動關(guān)閉給料泵和進水閥,沖洗進料管路并啟動中心反吹,待反吹結(jié)束,整個過濾操作即為完成。卸料時壓濾機打開,壓緊板返回。在控制面板上點擊“卸料”后左右小車啟動,將濾板拉回,泥餅自然脫落至槽車,卸料完成后外運填埋或摻燒。
與原離心式脫水機相比,板框式壓濾機的優(yōu)勢主要表現(xiàn)在以下幾點:
(1)污泥經(jīng)板框式壓濾機脫水后泥餅呈固態(tài),含固率在30%以上,方便運輸,不存在二次污染問題。
(2)設(shè)備運行穩(wěn)定,噪聲小,工作環(huán)境良好。
(3)設(shè)備運行不需要繼續(xù)投加藥品,節(jié)約了運行成本。
(4)故障率相對較低,檢修方便。
綜上所述,針對脫硫廢水水質(zhì),板框式壓濾機具有泥餅含固率高和穩(wěn)定性好的特點。
2.3 二種污泥脫水設(shè)備特點及能耗對比
根據(jù)改造前后脫水系統(tǒng)運行情況,二種污泥脫水設(shè)備主要特點如下:
項目 | 板框式壓濾機 | 離心式脫水機 |
工作狀態(tài) | 間斷式 | 連續(xù)式 |
環(huán)境衛(wèi)生條件 | 較好 | 封閉式,相對較好 |
運行噪聲(dB) | 70-75 | 80以上 |
輔助設(shè)備 | 空氣反吹、濾布高壓沖洗系統(tǒng) | 不需要 |
自動化程度實現(xiàn)難易程度 | 較容易 | 容易 |
濾餅含固率(%) | >30 | ≈20 |
濾液含固率(%) | ≈0.02 | ≈0.05 |
泥餅穩(wěn)定性 | 好 | 較差 |
由于二種脫水機脫水原理不同,造成2者性能差異較大。離心機是靠轉(zhuǎn)鼓的離心力高速旋轉(zhuǎn)將污泥中的空隙水甩出,迫使其進入外層殼體排出,需要克服的是水分子和固體顆粒之間的粘附力,這時水分子重力起反作用。除此之外在轉(zhuǎn)動過程中還有大量的能量因高速轉(zhuǎn)子磨損而消耗,所以相對能耗較高,但能持續(xù)工作。板框壓濾機脫水經(jīng)歷進料、擠壓、卸料的周期性間斷操作,進料、擠壓過程中能耗較大,主要克服的是濾液從濾布過濾的阻力,水分子重力起正面作用,且是周期性工作,所以能耗較低。按1天的處理量計算,離心機需工作8h,板框機需工作4個周期。2者耗電量和能耗比較如下:
(1)離心脫水機系統(tǒng):離心機功率22kW,進料泵功率3.0kW,兩設(shè)備每天運行8h,每天總能耗200kW·h。
(2)板框壓濾機系統(tǒng):板框機由液壓缸驅(qū)動,液壓缸功率為5.5kW,每天運行4個周期約為4h;進料泵2臺分別為5.5kW和11kW,每天運行時間4h;高壓清洗水泵37kW,每周工作1次約2h,折算約每天運行時間0.3h;合計每天總能耗99.1kW·h。
由計算結(jié)果可知,離心脫水機系統(tǒng)和板框壓濾機系統(tǒng)每噸干污泥能耗分別為55.5kW·h和27.5kW·h。
板框壓濾機工作規(guī)律為周期性,為了提高脫水效率,一次壓榨處理的污泥量較大,所需的濾布濾板較多,因此相對占據(jù)空間要比離心機大;另外,板框壓濾機系統(tǒng)每工作1個周期,即需用壓縮空氣反吹,還需根據(jù)濾布透水能力進行濾布清洗(約每周1次),配套設(shè)備較多,所需自動化控制水平較離心脫水機要高。
3 結(jié)語
本文研究結(jié)果表明:與離心式脫水機相比,板框式壓濾機更適合某電廠脫硫廢水污泥處理工藝,脫水后的泥餅含固率大于30%,且設(shè)備運行穩(wěn)定,噪聲低。污泥進入離心式脫水機或板框式脫水機之前有必要設(shè)置污泥緩沖罐及配套裝置,以便對污泥的性質(zhì)和流量進行調(diào)和緩沖。板框式壓濾機比離心脫水機能耗低,但配套設(shè)備較多,需要的空間相對較大,用戶可根據(jù)實際情況選擇脫硫廢水污泥脫水方式。