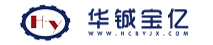
在污水處理過程中,活性污泥是常見的工藝,活性污泥法的基本原理是利用微生物在污水中的有機(jī)物分解成CO2(好氧工藝)或CH4(厭氧工藝)和水的同時、自身也得到不斷繁殖增長,即剩余污泥是活性污泥法的必然產(chǎn)物。剩余污泥不能得到妥善處理將會產(chǎn)生二次污染,因此,剩余污泥的處理決定了污水處理工藝是否完善。利用離心、帶式壓榨、板框壓榨等工藝將剩余污泥脫水后,再經(jīng)過干化處理后填埋或焚燒是一種很好的污泥處理途徑。
1 干化工藝簡介
在天津100萬噸/年乙烯及配套項(xiàng)目建設(shè)中,新建了一套污泥干化裝置,屬于配套環(huán)保設(shè)施。裝置由濕污泥輸送及儲存系統(tǒng)、干化系統(tǒng)、干泥輸送及儲存系統(tǒng)等幾部分組成,采用薄層干燥工藝處理污水處理裝置產(chǎn)生的剩余活性污泥。
2 濕污泥進(jìn)料及儲存
含水率為85%的脫水后活性污泥,用卡車運(yùn)送至現(xiàn)場后卸入活性污泥料倉。濕泥儲存設(shè)活性污泥料倉兩座,每座容積100m3,均為全地下料倉,料倉下部設(shè)有滑架和螺旋給料機(jī),滑架受液壓裝置驅(qū)動,在料倉的平底上往復(fù)運(yùn)動,將倉內(nèi)濕污泥平穩(wěn)地推送入螺旋給料機(jī)。螺旋給料機(jī)為有軸雙螺旋,可產(chǎn)生足夠的擠壓力,將濕污泥壓入污泥輸送泵。污泥輸送泵為螺桿泵,共2臺,可將濕污泥送到干化系統(tǒng)。料倉頂部設(shè)有臭氣風(fēng)機(jī),將料倉內(nèi)的惡臭氣體抽出送至位于污水場內(nèi)的催化燃燒脫臭系統(tǒng)。
在控制上,濕泥料倉不僅設(shè)置了保證自身安全的儀表和控制程序,還和干化機(jī)的運(yùn)行有互為因果的控制程序。比如,當(dāng)兩個儲料倉都裝滿后,系統(tǒng)會給出報警信號,通知操作員停止繼續(xù)卸料;這時,裝卸料艙門不能打開,喂料螺旋和輸送泵不能啟動。在運(yùn)行一段時間、當(dāng)一個存儲料倉排空后,系統(tǒng)自動切換到另外一個料倉。當(dāng)兩個料倉都排空后,向干化系統(tǒng)發(fā)送連鎖信號,由干化系統(tǒng)的控制系統(tǒng)判斷干化機(jī)停機(jī)時間。另外,在脫水活性污泥料倉裝有料位檢測傳感器和硫化氫氣體檢測傳感器。在此料倉裝滿的情況下,給系統(tǒng)發(fā)出報警提示,通知操作員停止卸料,裝卸料倉艙門不能打開。當(dāng)檢測到硫化氫氣體超標(biāo),給系統(tǒng)發(fā)出報警提示,裝卸料倉艙門不能打開,同時給臭氣風(fēng)機(jī)信號,風(fēng)機(jī)啟動強(qiáng)制排風(fēng)將硫化氫排出。
3 污泥干化單元
3.1 設(shè)計能力數(shù)據(jù)
干化機(jī)設(shè)計額定蒸發(fā)量為1000kg/h,折合設(shè)計處理含固率為15%的脫水污泥量為1250kg/h,設(shè)計干化后污泥含固率為75%,干化污泥量為250kg/h。同時,考慮了一定富余能力,設(shè)計蒸發(fā)量可以達(dá)到1200kg/h,即處理含固率為15%的脫水污泥量為1500kg/h,相應(yīng)含固率75%干污泥300kg/h。
3.2 熱源及其他配套條件
加熱介質(zhì)為飽和蒸汽,正常入口蒸汽壓力0.8MPa,入口蒸汽溫度180℃。至于其他公用工程條件,除了電外,還需要新鮮水和二沉池出水作為冷卻水、氮?dú)庾鳛楸Wo(hù)氣和一定量的儀表風(fēng)。污泥干化過程中,從氣體洗滌和冷凝段排出的具有需要進(jìn)行處理的污水,還要排出一些空氣與不可凝工藝氣體組成的廢氣。
3.3 工藝流程簡述
在污泥干化單元,活性污泥被干燥至含固率約70%~75%,工藝過程可分為污泥干化、干化產(chǎn)品輸送、工藝氣體冷凝及排放等三個部分。
(1)污泥干燥器
污泥的干燥是基于渦輪技術(shù),污泥通過單螺桿泵被送到臥式圓柱體渦輪干燥器的喂料倉,再由雙螺旋以1m3/h左右定量送入渦輪干燥器。干燥器的污泥入口也是工藝氣體的入口,即工藝氣體與污泥在干燥器內(nèi)同向運(yùn)動。污泥進(jìn)入干化機(jī)后,渦輪轉(zhuǎn)子將其高速離心到內(nèi)壁上,緊貼著圓柱形的內(nèi)壁形成一個薄層,這種薄層可以得到很高的換熱效率和熱利用效率。污泥在干燥器內(nèi)很強(qiáng)的渦流作用下,緊貼著圓柱形的內(nèi)壁,連續(xù)地移動和很好地混合。
干燥器內(nèi)的熱交換主要是依靠污泥與圓柱形容器同軸的夾套中的蒸汽熱傳導(dǎo)實(shí)現(xiàn)的,經(jīng)過預(yù)熱的循環(huán)氣體進(jìn)入干燥器后對污泥起到輸送和輔助加熱的作用。預(yù)熱氣體在干燥器內(nèi)與污泥的接觸、并流運(yùn)動,不會引起污泥的化學(xué)分解。事實(shí)上干燥器的進(jìn)口處的熱氣體與高含濕量的冷產(chǎn)品接觸,可以避免干泥的過熱。污泥在渦輪干燥機(jī)中的停留時間很短,因此干燥器內(nèi)的干泥量只有數(shù)十公斤(根據(jù)工作狀態(tài)略有變化)。渦輪的外緣的旋轉(zhuǎn)速度大約在20~30m/s之間。即使發(fā)生突然斷電,整個工廠停頓的情況下,旋轉(zhuǎn)渦輪的機(jī)械慣性也可以保證渦輪干燥器基本清空,避免了干燥器內(nèi)因留存物料而影響設(shè)備重啟,從而保障系統(tǒng)安全。
干燥器渦輪是由旋轉(zhuǎn)軸和鍍有耐磨材料的特殊形狀的槳葉構(gòu)成。渦輪安裝在兩個法蘭連接端板中心線上的懸架軸承上。渦輪支撐和轉(zhuǎn)動的軸承組安裝在蒸發(fā)室外,因此沒有污損和過熱的風(fēng)險。干燥的污泥離開渦輪干燥器后,與水蒸氣一起進(jìn)入分離段,通過旋風(fēng)分離器進(jìn)行固體和氣體的分離。
(2)氣固分離
經(jīng)過渦輪干燥器干化的污泥和工藝氣體一起進(jìn)入旋風(fēng)分離器,旋風(fēng)分離器外部進(jìn)行絕熱處理以避免蒸汽產(chǎn)生冷凝。在旋風(fēng)分離器內(nèi)固形物和氣體因密度差別而被分離,干燥后的污泥產(chǎn)品被收集在底部,而氣體從頂部離開。在旋風(fēng)分離器中收集的細(xì)顆粒落入具備冷卻功能的螺旋輸送機(jī),約100℃的干化污泥被冷卻至40℃以下,再提升到干泥料倉。
旋風(fēng)分離器出口的工藝氣體被送往濕法除塵器進(jìn)行粉塵分離,除塵器裝備外部進(jìn)行絕熱處理以避免蒸汽產(chǎn)生冷凝。氣體從立式靜態(tài)分離器底部進(jìn)入,與填料接觸產(chǎn)生聚結(jié),固體被從氣相中分離出來。洗滌水由頂部噴入,捕捉固體和液體物質(zhì),并起到對填料進(jìn)行清潔的作用。液體/固體混合物收集在底部,液態(tài)物收集在底部由離心泵循環(huán)回到除塵器以保證洗滌效率,濃縮的粉塵定時用泵排到廢水池。
氣相從頂部排出,捕霧器將氣相流可能攜帶出的液滴去除后,工藝氣體將重新回到閉環(huán)循環(huán)。循環(huán)工藝氣體由離心風(fēng)機(jī)抽取并循環(huán)到閉環(huán)干燥回路中,該循環(huán)氣體被送入以蒸汽為熱源的熱交換器中,加熱后的氣體返回渦輪干燥器。
(3)工藝氣體冷凝及排放
在濕污泥被干化的過程中,蒸發(fā)處理的水汽及氣體揮發(fā)性氣體必須及時從循環(huán)氣體中分離出來,以實(shí)現(xiàn)系統(tǒng)的平衡的微負(fù)壓。
由風(fēng)機(jī)抽取的水蒸氣和氣體揮發(fā)性氣體首先被引入冷凝塔進(jìn)行冷凝,在冷凝塔內(nèi)氣體通過一個頗爾環(huán)填料層被水逆向淋洗,冷凝液被收集在冷凝塔底部,泵送到廢水池。液體由離心泵循環(huán)輸送至冷凝塔的頂部之前,通過板式換熱器將循環(huán)液進(jìn)行冷卻。為節(jié)約水耗,冷卻介質(zhì)采用含油污水處理系統(tǒng)的二沉池出水。經(jīng)過洗滌后的不凝氣體,再進(jìn)入除霧器處理后,用廢氣風(fēng)機(jī)引至污水場的脫臭裝置處理。
(4)工藝的控制
渦輪薄層污泥干化工藝的上述三個部分采用一套PLC對工藝進(jìn)行自動控制。在基本條件設(shè)定后,可以通過在線儀器儀表,準(zhǔn)確地實(shí)現(xiàn)對工藝的控制。
渦輪薄層的工藝控制主要是對干燥器出口工藝氣體溫度的控制。蒸汽進(jìn)入換熱器,加熱工藝氣體,使工藝氣體不斷升溫。當(dāng)達(dá)到設(shè)定工藝溫度后,系統(tǒng)開始定量喂入濕泥,濕泥與熱壁和熱介質(zhì)接觸,產(chǎn)生蒸發(fā)。隨著濕泥喂入量分步到位,干燥器出口溫度穩(wěn)定在一個合適的溫度區(qū)間,該溫度與產(chǎn)品含固率有較為準(zhǔn)確的對應(yīng)關(guān)系。干泥的含固率變化可以通過多種調(diào)節(jié)方式來進(jìn)行,其中除了槳葉角度為冷機(jī)機(jī)械調(diào)整外,均為熱機(jī)在線調(diào)整。因濕泥狀況變化而需要作出的臨時調(diào)整可由操作人員現(xiàn)場隨時進(jìn)行。
(5)運(yùn)行安全的控制
干化系統(tǒng)的開機(jī)和關(guān)機(jī)均按照一個預(yù)先設(shè)定好的程序進(jìn)行。開機(jī)的目標(biāo)是在確保安全和溫度合適的條件下,建立系統(tǒng)內(nèi)的物料和熱平衡。關(guān)機(jī)的目標(biāo)是在確保安全和阻斷濕泥進(jìn)料的同時,實(shí)現(xiàn)干燥器的緩慢降溫和冷卻。
對避免臭氣和粉塵泄漏到環(huán)境中,干化系統(tǒng)為微負(fù)壓狀態(tài),但微負(fù)壓可能造成周邊環(huán)境中少量空氣進(jìn)入系統(tǒng),使氣體中氧含量增加。為確保工藝回路獲得必要的惰性化,防止干化過程出現(xiàn)爆燃,污泥干化采用測氧儀作為安全運(yùn)行監(jiān)測的重要手段。工藝氣體中的氧含量將設(shè)置兩個探頭連續(xù)監(jiān)測,當(dāng)氧含量超過限值時,將產(chǎn)生報警,安全用氮?dú)膺M(jìn)氣閥將打開,在風(fēng)機(jī)和換熱器之間噴入氮?dú)?,直至氧含量減少到正常水平。當(dāng)處于非常高位時,干燥工廠將會緊急停車,安全氮?dú)忾y將處于持續(xù)打開狀態(tài)。
4 干泥輸送及儲存
冷卻至40℃以下的干泥由提升機(jī)提升送入干泥料倉。干泥料倉容積為30m3,設(shè)置在戶外。料倉底部裝有破拱器防止污泥架橋,并有閘板閥,控制干泥的出料量。需裝車時,打開閘板閥,干污泥經(jīng)卸料機(jī)斜至車內(nèi)。
在現(xiàn)場設(shè)控制按鈕箱,可以手動操作設(shè)備的啟動、停止。干泥料倉內(nèi)裝溫度傳感器和可燃?xì)怏w傳感器。當(dāng)達(dá)到危險值時,啟動氮?dú)獗Wo(hù)裝置。打開氮?dú)廨斔烷y門并報警通知操作工。干泥料倉安裝料位傳感器,當(dāng)倉位高時,向干化系統(tǒng)發(fā)出停車連鎖信號并報警。同時干污泥提升停止運(yùn)行。干泥料倉裝有破拱器,當(dāng)卸料時,卸料閥打開的同時,破拱器工作。
5 結(jié)論
天津石化污泥干化系統(tǒng)于2010年11月開工,2011年10月26日開始投料試車,12月12日~14日完成了性能考核。性能考核期間,此套裝置實(shí)際處理污泥含水率11.3%的脫水污泥為1535kg/h,實(shí)際蒸發(fā)能力達(dá)到了1296kg/h,干化污泥產(chǎn)品的含水率為27.3%。目前,裝置根據(jù)污水處理系統(tǒng)排泥量的多數(shù)間歇運(yùn)行,即將濕泥料倉用脫水污泥裝滿后即投入運(yùn)行,2012年每個月的運(yùn)行時間都在10天以上。