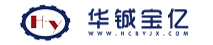
云南磷化集團(tuán)??诹讟I(yè)有限公司(簡稱公司)磷酸裝置年產(chǎn)磷酸(w(P2O5)≥46.5%,w(固)≤8%)66萬t,在陳化裝置沉降后被分離成2種不同品質(zhì)磷酸,即上部清酸(w(P2O5)≥47%,w(固)<2%)約54萬t和底部渣酸(w(P2O5)≥42%,w(固)≤30%)約12萬t。其中上部清酸作為高養(yǎng)分、高附加值66%磷酸一銨(MAP)和磷酸二銨(DAP)產(chǎn)品的原料。渣酸的主要成分是磷酸化合物、石膏和氟硅酸等,在2017年6月以前都是和w(固)8%的磷酸混合后用于傳統(tǒng)法裝置生產(chǎn)55%~60%的粒狀磷酸一銨(GMAP)產(chǎn)品,或通過與磷礦粉混合、熟化后生產(chǎn)重過磷酸鈣產(chǎn)品。但隨著近年來GMAP和重過磷酸鈣產(chǎn)品供大于求,其銷售價(jià)格即使低于成本價(jià)也難以銷售,生產(chǎn)的唯一目的就是消耗渣酸。因此渣酸的處理,成為公司生產(chǎn)經(jīng)營和持續(xù)發(fā)展的瓶頸。
1 渣酸——液態(tài)非均相物系的分離方法簡介
液態(tài)非均相物系的分離方法分為機(jī)械分離、傳質(zhì)分離和反應(yīng)分離,由于渣酸分離的主要目的是將其中的固體顆粒物與液體相分離,本文重點(diǎn)討論機(jī)械分離的可行性。
1.1 重力沉降
重力沉降是依靠地球引力的作用,利用顆粒與流體的密度不同,使之發(fā)生相對(duì)運(yùn)動(dòng)而沉降。一般分為自由沉降和斜管沉降。自由沉降在公司濕法磷酸生產(chǎn)的陳化工序已經(jīng)使用,其主要作用是將經(jīng)過濃縮的濃磷酸(w(P2O5)≥46.5%,w(固)≤8%)在陳化槽分離;斜管沉降是在自由沉降槽中增加斜管,以提高沉降分離效果,降低沉降槽高度,由于濕法磷酸結(jié)垢嚴(yán)重,所以在濕法磷酸陳化工序未采用。從以上情況可知,再次采用重力沉降法,將第一次重力沉降渣酸實(shí)現(xiàn)液固分離并不可行。
1.2 過濾
過濾是分離懸浮液較普遍和較有效的單元操作之一。但經(jīng)現(xiàn)場調(diào)研,立式全自動(dòng)壓濾機(jī)過濾渣酸存在如下問題:濾布跑偏頻繁、泄漏量大、導(dǎo)輥軸承進(jìn)酸損壞頻繁、濾布再生效果差、使用周期短、濾板隔膜損壞頻繁等。
1.3 離心分離
離心分離分為離心過濾和離心沉降。離心過濾原理:過濾式離心機(jī)轉(zhuǎn)鼓壁上有許多孔,轉(zhuǎn)鼓內(nèi)表面覆蓋過濾介質(zhì),加入轉(zhuǎn)鼓的懸浮液隨轉(zhuǎn)鼓旋轉(zhuǎn)產(chǎn)生巨大的離心壓力,在壓力作用下懸浮液中的液體透過過濾介質(zhì)和轉(zhuǎn)鼓壁上的孔流出,固體被截留在過濾介質(zhì)表面,從而實(shí)現(xiàn)固體與液體的分離。其優(yōu)點(diǎn)為懸浮液在轉(zhuǎn)鼓中產(chǎn)生的離心力為重力的千百倍,使過濾過程得以強(qiáng)化,獲得水含量較低的濾渣。缺點(diǎn)是需要頻繁更換濾布等過濾介質(zhì)。
離心沉降原理:離心沉降是依靠離心力場將固液密度差擴(kuò)大幾千倍,使之發(fā)生相對(duì)運(yùn)動(dòng)而沉降。其優(yōu)點(diǎn):分離效率高,可以分離出比較小的固體顆粒。缺點(diǎn):離心機(jī)轉(zhuǎn)速高,轉(zhuǎn)動(dòng)件加工精度要求高,離心設(shè)備結(jié)構(gòu)復(fù)雜,制造成本和投資費(fèi)用高。
2 臥式螺旋卸料沉降離心機(jī)的應(yīng)用
為從渣酸中分離液相部分,提高產(chǎn)品的附加值,公司組織人員對(duì)液態(tài)非均相物系的分離設(shè)備進(jìn)行調(diào)研,選用離心沉降原理制造的臥式螺旋卸料沉降離心機(jī)。它具有連續(xù)生產(chǎn)、自動(dòng)化控制、封閉操作、單機(jī)生產(chǎn)能力大、設(shè)備結(jié)構(gòu)較緊湊、耐磨性和耐腐蝕性好、運(yùn)行周期長等特點(diǎn)。
臥式螺旋卸料沉降離心機(jī)的結(jié)構(gòu)中,外轉(zhuǎn)子即轉(zhuǎn)鼓,由電機(jī)通過皮帶傳動(dòng);內(nèi)轉(zhuǎn)子即螺旋,由差速器將轉(zhuǎn)鼓轉(zhuǎn)速和輸入軸轉(zhuǎn)速合成一個(gè)轉(zhuǎn)速傳給螺旋,使螺旋獲得一個(gè)比轉(zhuǎn)鼓慢5~60r/min的差轉(zhuǎn)速,于是轉(zhuǎn)鼓和螺旋便構(gòu)成了一副具有微小差轉(zhuǎn)速的同向高速旋轉(zhuǎn)的螺旋輸送機(jī)構(gòu)。懸浮液通過進(jìn)料口進(jìn)入轉(zhuǎn)鼓內(nèi),被置于比重力場大數(shù)千倍的離心力場中而形成空心液環(huán)。由于固相密度大于液相,即固相所受的離心力大于液相,于是固相便沉降到轉(zhuǎn)鼓內(nèi)壁上,然后被螺旋輸送到轉(zhuǎn)鼓小端的排渣口,借助離心力將其拋到機(jī)殼的沉渣收集室。液相則通過螺旋形通道向轉(zhuǎn)鼓大端流動(dòng),并通過事先調(diào)整好的溢流孔進(jìn)入澄清液收集室。
沉渣在螺旋輸送過程中,由沉降區(qū)進(jìn)入脫水區(qū),此時(shí)沉渣逐漸密集并通過離心力的徑向壓實(shí)作用和螺旋葉片的軸向擠壓作用,將其中的部分液體擠壓出來,通過螺旋通道或螺旋葉片與轉(zhuǎn)鼓內(nèi)壁的間隙流回沉降區(qū)。該機(jī)的沉降區(qū)長度調(diào)節(jié)可以通過改變溢流擋板的位置(即溢流直徑)而實(shí)現(xiàn),增大沉降區(qū)長度可以得到較清澈的液相,而固相水含量較大;反之,會(huì)得到水含量較小的固相,但液相的固含量較多。
該設(shè)備特別適宜分離固相粒度0.005~2.000mm、w(固)1%~30%、溫度0~90℃、固相密度大于液相的懸浮液。由于采用螺旋卸料,對(duì)固相顆粒有一定的破壞作用,對(duì)沉渣的洗滌效果差。從渣酸中分離出來的固相物將返回溶解槽與硫酸進(jìn)行再次反應(yīng),因此對(duì)固相物的洗滌要求不高。公司選用的臥式螺旋卸料沉降離心機(jī)的具體參數(shù)如下:型號(hào)W520×2184-NB,轉(zhuǎn)鼓內(nèi)徑520mm,額定轉(zhuǎn)速3000r/min,機(jī)器重量8000kg,轉(zhuǎn)鼓長度2184mm,電機(jī)功率75kW,外形尺寸5550mm×1400mm×1820mm。
3 臥式螺旋卸料沉降離心機(jī)在渣酸處理中的應(yīng)用
該項(xiàng)目自2017年6月使用以來,渣酸處理效果較好,裝置正常運(yùn)作情況下,每天可處理渣酸(w(P2O5)42%,w(固)26%左右)約30m3,可產(chǎn)生清液(w(P2O5)46%,w(固)5%左右)約10.5m3,大大緩解了磷酸渣酸脹槽的情況,增加了高品質(zhì)磷酸產(chǎn)量。
4 項(xiàng)目取得的主要經(jīng)濟(jì)效益和社會(huì)效益
(1)經(jīng)濟(jì)效益。增加渣酸分離項(xiàng)目后,不僅能處理積壓的渣酸,還增加成品酸量。按每天平均產(chǎn)生清液10.5m3,清液相對(duì)密度1.6計(jì)算,每噸酸利潤200元,每年按裝置正常運(yùn)行時(shí)間300d計(jì)算,則節(jié)約成本為100.8萬元。
(2)環(huán)境效益。增加渣酸分離項(xiàng)目,能有效解決裝置因渣酸脹槽造成的停車風(fēng)險(xiǎn),提升萃取/濃縮裝置運(yùn)行率,減少因裝置開停車造成的泄露和排放指標(biāo)波動(dòng),確保環(huán)保指標(biāo)達(dá)標(biāo)。