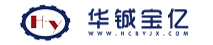
某公司起初的漂粉精生產(chǎn)裝置,采用間歇批料、連續(xù)分離的方式生產(chǎn),以氯氣、燒堿、消石灰為原料,反應生成含次氯酸鈣晶體的漿料,從漿料中分離出晶體后得到的濾餅經(jīng)過干燥、造粒、篩分,制得顆粒均勻的漂粉精。
整個生產(chǎn)過程分為氯化結(jié)晶、分離干燥、母液回收、尾氣處理、精加工等工序。早期的工藝流程中分離工序采用了回轉(zhuǎn)真空過濾機對氯化反應后的漿料進行抽濾、分離。由于回轉(zhuǎn)真空過濾機的濾布易跑邊、破裂,造成漿料損失,使整個生產(chǎn)無法順利進行;而且物料的粘性較大,濾布易被堵塞,在再生和清理濾布時,壓縮空氣和漿料中殘余的Ca(OH)2容易反應生成少量的CaCO3。上述兩個問題導致產(chǎn)品的產(chǎn)量、質(zhì)量均達不到設計值,該分離工序成了整個生產(chǎn)過程中的“瓶頸”。鑒于這種情況,對該工序進行了技術改造,選用LW460臥式螺旋卸料沉降離心機替代回轉(zhuǎn)真空過濾機進行漿料的分離。
1 改進后的工藝流程
來自氯化反應釜的漿料自流到中間貯罐,再用泥漿泵送至高位緩沖罐,經(jīng)緩沖罐流入離心機進行分離,分離出來的濾餅與粉狀的干燥漂粉精進行混合后,進入干燥器進行干燥。分離出來的母液流入貯槽,再返回到二次反應釜回收利用。
此工藝具有流程短、操作方便、分離效率高等特點。
2 新增的主要設備
2.1 鈦制LW460型離心機
根據(jù)要分離的漿料晶體的特性、產(chǎn)量的大小,綜合現(xiàn)場生產(chǎn)情況及機器的使用特點等因素,選定了鈦制LW460型離心機作為漂粉精的分離設備。在設計選型時,確定了轉(zhuǎn)鼓的形狀為筒錐形,并確定了長徑比、錐角、雙頭螺旋及螺距的尺寸、差速器的速比等設計制造參數(shù)。
LW460型離心機為臥式螺旋卸料沉降離心機,它能在全速運轉(zhuǎn)的狀態(tài)下完成連續(xù)進料、分離、螺旋輸送卸料等工藝操作。適用于分離固、液相密度差較大,固相顆粒較細的懸浮液。對懸浮液的澄清、固相的濃縮和脫水、固相離子的分級等有很好的效果。其工作原理為:轉(zhuǎn)鼓全速旋轉(zhuǎn)后,漿料通過中心進料管連續(xù)進入機內(nèi),經(jīng)過螺旋輸送器內(nèi)筒加料隔倉的進料口進到轉(zhuǎn)鼓內(nèi)。在離心力的作用下,轉(zhuǎn)鼓內(nèi)形成一個環(huán)形液池,密度較大的晶體顆粒(重相)離心沉降到轉(zhuǎn)鼓內(nèi)表面形成濾餅,由于螺旋葉片與轉(zhuǎn)鼓的相對運動,濾餅被螺旋葉片推送到轉(zhuǎn)鼓小端的干燥區(qū),從排渣口排出;而密度較小的澄清液(母液)則處于沉積層內(nèi)側(cè),由螺旋葉片形成的通道流向轉(zhuǎn)鼓大端蓋上的4個溢流孔流出,經(jīng)機殼的排液室排出,從而完成漿料的分離。
由于次氯酸鈣具有較強的腐蝕性,離心機體與物料接觸部分全部采用質(zhì)輕且耐腐蝕的鈦材制造,對易磨損的螺旋推料面和出料孔口襯耐酸堿陶瓷進行硬化處理,大大延長了機器的使用壽命。LW460型離心機具有可自動連續(xù)操作、維修方便、單機處理量大、操作費用低、占地面積小、功率消耗低等優(yōu)點,是理想的分離設備。
2.2 高位緩沖罐
從泥漿泵來的漿料沖力大,流量經(jīng)常波動,離心機進料不均勻,造成離心機運轉(zhuǎn)不平穩(wěn),增加了1臺高位罐,該罐為平蓋錐底型,漿料從周向切線方向進入,類似攪拌形成漩渦,漿料從漩渦中心即罐的錐底中心孔流出,防止?jié){料中固體顆粒沉淀在罐壁上。同時使罐保持恒定的液位,靠重力使?jié){料均勻流動,保證離心機進料流量恒定,運行平穩(wěn)。
3 問題及解決方法
(1)在技改完成后的試運行過程中,高位緩沖罐的液位波動較大,經(jīng)常出現(xiàn)溢流倒回中間貯罐的現(xiàn)象,漿料在循環(huán)過程中,其中的晶體多次被泥漿泵的葉輪切削、破碎,導致從離心機出來的濾餅變稀而且量少。為了較好地控制高位緩沖罐的液位,給泥漿泵的電機配備了1臺變頻調(diào)速器,通過調(diào)速器來控制泵的轉(zhuǎn)速,使罐維持一個恒定的液位,有效地保證了進料均勻,因而從離心機出來的濾餅狀況較好,含水量穩(wěn)定在40%~45%,為后面的干燥工段提供了工況溫度的物料,漂粉精的產(chǎn)量、質(zhì)量得到了保障。
(2)在生產(chǎn)過程中,靠手動調(diào)節(jié)閥門的開度,很難準確地控制離心機的進料量。為此在離心機和緩沖罐之間加裝了1臺自動調(diào)節(jié)閥和1臺流量計,利用裝置的DCS對流量計的讀數(shù)和設定的流量值進行比較,然后對自動調(diào)節(jié)閥實行控制,確保流量維持在設定值,實現(xiàn)了離心機進料流量的自動控制,工人的操作難度大大降低。
(3)在實現(xiàn)自動調(diào)節(jié)流量并能平穩(wěn)進料后,發(fā)現(xiàn)在正常運轉(zhuǎn)約20天后,離心機的振動逐漸加大,經(jīng)過仔細查找原因并進行分析,認為是離心機轉(zhuǎn)鼓的內(nèi)壁和外壁以及螺旋輸送器表面結(jié)垢所致。每周對離心機進行酸洗和水洗,并且打開機殼,對轉(zhuǎn)鼓的外壁進行除垢;同時檢查出渣口位置的轉(zhuǎn)鼓上刮刀的磨損情況,必要時更換。采取這些措施后,離心機正常運行時間大大延長。
(4)在試運行中,確定了離心機的轉(zhuǎn)鼓轉(zhuǎn)速及差轉(zhuǎn)速、母液溢流擋板的位置及過載保護作用扭矩及分離流量等運行參數(shù),使離心機處于較佳的運行狀態(tài)。
4 運行效果
(1)使用LW460型臥式螺旋卸料沉降離心機后,大大簡化了操作程序,降低了員工的勞動強度,改善了操作環(huán)境,同時也減少了動力消耗及物料的浪費,取得了一定的經(jīng)濟效益。經(jīng)核算,漂粉精成本比原來降低125元/t,按產(chǎn)能5000t/a計算,每年可節(jié)約成本60多萬元。
(2)有效生產(chǎn)時間有了顯著的提高,經(jīng)統(tǒng)計比較,每年有效生產(chǎn)時間多了約22天,按每天生產(chǎn)15t計算,每年可多生產(chǎn)產(chǎn)品330t。
(3)產(chǎn)品質(zhì)量上了一個新的臺階,漂粉精產(chǎn)品合格率為100%,優(yōu)級品率可達85%以上,提高了產(chǎn)品的競爭力。