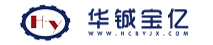
生物處理不僅是過去、現(xiàn)在盛行的污水處理方法,也將代表著未來。故而,污水處理副產(chǎn)物——剩余污泥是始終繞不開的問題。污泥處置方式,從開始的填埋、農(nóng)用、綠化,一直到現(xiàn)在的堆肥、消化乃至焚燒,這其中,污泥“丟棄”(如填埋、農(nóng)用)顯然是較為簡單和經(jīng)濟(jì)的方式;在相對“地大物博”的中國、美國和英國的污泥“丟棄”所占比例較高,分別達(dá)到76%、59%和63%。但是,在人均國土面積較小的一些歐洲國家和日本,丟棄應(yīng)用比例持續(xù)下降,從法國的46%,到德國的27%,直至日本的16%、荷蘭的11%(未農(nóng)用),繼而增加了厭氧消化甚至焚燒的路徑。
縱觀歐洲等發(fā)達(dá)國家剩余污泥處理、處置歷史,污泥“丟棄”越來越受到空間和農(nóng)業(yè)的限制,以至于很快變成一條“死胡同”。從省事、省力、省錢角度,我國固然想繼續(xù)走污泥“丟棄”的路線,然而,現(xiàn)實(shí)情況表明,我國沒有足夠可持續(xù)接納污泥的填埋場地,農(nóng)民亦不稀罕污泥中的肥效,園林綠化恐也難以長期接納污泥。這就形成了目前我國剩余污泥“成災(zāi)”的嚴(yán)重局面。因此,污泥堆肥、消化、焚燒技術(shù)路線也相繼提到議事日程并開始工程應(yīng)用。通常認(rèn)為,焚燒投資與運(yùn)行費(fèi)用太高,一般首先考慮堆肥和消化。污泥堆肥出路有限,厭氧消化后仍有50%~70%的污泥有機(jī)物殘留,不得不再增加焚燒環(huán)節(jié)進(jìn)行處置。
鑒于此,污泥采取“低端”丟棄方式變得日益艱難,不如直接走向“高端”,即焚燒。當(dāng)然,污泥焚燒需要將含水率降至一定范圍(40%~70%)。所以,污泥脫水后仍需要進(jìn)一步干化至目標(biāo)含水率,而傳統(tǒng)的厭氧消化則完全可以省略。污泥干化后焚燒不僅可以較大程度地回收污泥有機(jī)能量(發(fā)電、供熱),而且焚燒后灰分是回收污水中磷(P)的較有效方式,甚至還可以回收重金屬。
基于這一思路,需要對污泥干化、焚燒建議工藝進(jìn)行能量平衡、投資成本、運(yùn)行費(fèi)用匡算,并與傳統(tǒng)厭氧消化為主的焚燒工藝進(jìn)行技術(shù)經(jīng)濟(jì)比較,以揭示建議工藝在能量、投資以及運(yùn)行方面的優(yōu)勢所在。
1 干化+焚燒建議工藝
污泥直接干化、焚燒建議工藝包括機(jī)械脫水、熱媒干化與單獨(dú)焚燒三個(gè)單元。含水率≥99%的原污泥采用機(jī)械脫水方式將含水率降至80%;常用機(jī)械脫水方式有壓濾(帶式、板框)、真空吸濾和離心等,但較常用壓濾。近年來,國內(nèi)外也研發(fā)出一些新的脫水方式,如電滲析脫水工藝。總之,將原污泥脫水至80%選擇方案較多。
機(jī)械脫水至80%含水率的污泥雖已呈泥餅狀,可裝車外運(yùn),但距離自持燃燒(無需輔助外部燃料)含水率(40%~70%)還有一定距離,主要取決于污泥中的有機(jī)質(zhì)含量。這就需要在80%含水率脫水污泥的基礎(chǔ)上實(shí)施熱媒干化,主要形式有熱對流干燥系統(tǒng)和熱傳導(dǎo)干燥系統(tǒng)。熱對流干燥系統(tǒng)(轉(zhuǎn)鼓式干化與流化床干化)適用于全干化工藝,可使含水率從80%降至15%及以下。從焚燒角度看,全干化并不可取,一是能耗高,二是后續(xù)焚燒難以形成流化狀污泥顆粒。因此,半干化熱傳導(dǎo)干燥系統(tǒng)(轉(zhuǎn)盤式干化與多層臺(tái)階式干化)較適用于干化污泥,可使污泥含水率降至35%~50%。
根據(jù)污泥有機(jī)質(zhì)含量,含水率為40%~70%的干化污泥已具有自持燃燒的能力,利用常規(guī)焚燒爐在800~900℃下將污泥有機(jī)物完全燃燒并氧化至CO2,包括磷在內(nèi)的無機(jī)物形成灰分。污泥焚燒釋放出的熱量可以用來發(fā)電或回收高溫廢氣用于污泥再次干化或熱交換供熱,灰分中的磷甚至重金屬可以通過化工工藝回收,殘留灰分可用作生產(chǎn)建筑材料。國內(nèi)外常用焚燒爐有流化床爐、立式多膛爐、噴射焚燒爐等。
2 建議工藝能力衡算
2.1 機(jī)械脫水
國內(nèi)外常用機(jī)械脫水方式及其能耗列于下表:
項(xiàng)目 | 板框壓濾 | 帶式壓濾 | 真空吸濾 | 雙輥擠壓 | 離心分離 |
脫水污泥含水率(%) | 55~90 | 65~90 | 60~90 | 60~80 | ~80 |
總能耗(kW·h/tDS) | 157~179 | 37~81 | 37~81 | 37~59 | 15~37 |
能耗均值(kW·h/tDS) | 169 | 61 | 61 | 39 | 26 |
其中,板框壓濾能耗較高,帶式壓濾與真空吸濾次之,離心和雙輥擠壓能耗較低。本研究以能耗折中且常用的帶式壓濾法為例進(jìn)行能量衡算,平均能耗約60kW·h/tDS。
2.2 污泥干化
2.2.1 理論能耗計(jì)算
污泥干化過程能耗由污泥固體升溫及所含水分吸熱組成,故從這兩方面入手,理論能耗計(jì)算分別如下。
(1)污泥固體升溫所需熱量
污泥固體升溫所需熱量可根據(jù)下式計(jì)算:
Es=(T2-T1)×Cs×Ms×100
式中:Es——污泥固體升溫所需熱量,kJ/tDS
T1、T2——脫水污泥初始溫度(20℃)和干化溫度(100℃)
Cs——污泥比熱容,3.62kJ/(kg·℃)
Ms——污泥干固體質(zhì)量,10kg/t濕泥(99%含水率)
(2)污泥中水分吸收熱量
污泥中水分吸收熱量分為:
①水從常溫升溫到顯熱;
②水蒸發(fā)過程汽化潛熱。
熱媒干化又分高溫干化(100℃)和低溫干化(20~80℃),分別可利用高溫?zé)煔?、過熱蒸汽、燃油和熱水及太陽能、低溫?zé)崮艿葘?shí)現(xiàn)。目前,高溫干化較為盛行,本研究也以高溫干化為例(100℃),這部分干化熱量計(jì)算如下:
Ew=Cw×[Ms×w1/(1-w1)]×(T2-T1)×100+Qg×Mw
Mw=[Ms/(1-w1)-Ms/(1-w2)]×100
式中:Ew——污泥中水分吸收的熱量,kJ/tDS
Cw——水的比熱容,4.2kJ/(kg·℃)
w1、w2——污泥干化前、后含水率,分別為80%和40%~70%
Qg——水在100℃時(shí)的汽化潛熱,為2260kJ/kg
Mw——干化過程蒸發(fā)的水量,kg/tDS
上述計(jì)算中較為重要的參數(shù)是污泥干化后的含水率w2,其表征污泥自持燃燒所需的較高含水率,計(jì)算公式為:
QsH=QsL×(1-w2)-Qg×(w2+9wH)
式中:QsH——污泥高位熱值,即污泥的潛能值,kJ/tDS
QsL——污泥低位熱值,取污泥自持燃燒限值3.36GJ/tDS
wH——污泥干固體中氫元素含量,取2%
2.2.2 實(shí)際能耗計(jì)算
因污泥干燥機(jī)自身存在熱損失,污泥干化實(shí)際能耗(E’r)顯然要比理論能耗Er高;不同干燥機(jī)熱損失亦存在一定差異,熱損失效率∑干為10%~20%;本研究取高值(20%)計(jì)算。污泥干化實(shí)際能耗可按下式計(jì)算:E’r=Er(1+∑干)
2.3 污泥焚燒
2.3.1 理論釋能計(jì)算
污泥有機(jī)質(zhì)完全焚燒至灰分釋放的熱量體現(xiàn)在污泥的干基熱值上,污泥干基熱值計(jì)算如下:
Q=2.5×105×(100pv-5)
式中:Q——污泥干基熱值,J/kgDS
2.5×105、5——系數(shù)
pv——污泥中有機(jī)質(zhì)含量
我國污泥有機(jī)質(zhì)含量在30%~65%之間,比歐美等發(fā)達(dá)國家低15.2%~37.7%。以我國有機(jī)質(zhì)含量為基準(zhǔn),分別取30%和65%,代入計(jì)算得污泥燃燒熱值為6.3~15.0GJ/tDS。本研究取污泥有機(jī)質(zhì)含量pv為53%,污泥高位熱值,即焚燒理論釋能為11.9GJ/tDS,與我國污泥平均熱值一致。以實(shí)現(xiàn)自持燃燒為目的,污泥干化含水率w2需達(dá)到57.7%。這樣,從脫水污泥80%含水率干化至57.7%,所需干化能耗為9.1GJ/tDS,與實(shí)際工程的11.7GJ/tDS近似;轉(zhuǎn)化為電當(dāng)量為2529kW·h/tDS(1kW·h=3600kJ)。
干化污泥實(shí)現(xiàn)自持燃燒所需含水率w2取決于污泥中有機(jī)質(zhì)含量。根據(jù)公式可得出污泥有機(jī)質(zhì)含量與干化目標(biāo)含水率的關(guān)系。顯然,污泥有機(jī)質(zhì)含量越高,污泥干化目標(biāo)含水率w2便可以提高,也就是說,干化污泥自持燃燒含水率隨有機(jī)質(zhì)含量的增加而升高。
2.3.2 焚燒過程中的能量損失
污泥焚燒過程中會(huì)因固體、氣體不完全燃燒或者鍋爐自身散熱造成一定熱量損失,所以,污泥焚燒釋能計(jì)算需要扣除這部分熱量損失,可按下式計(jì)算:
Q損=Qa+Qb+Qc+Qd+Qe
式中:Q損——污泥焚燒損失總能量,kJ/tDS
Qa——焚燒爐自身輸出熱量(爐內(nèi)掛壁損失),kJ/kg
Qb——?dú)怏w不完全燃燒損失熱量,kJ/tDS
Qc——固體不完全燃燒損失熱量,kJ/tDS
Qd——鍋爐散熱損失熱量,kJ/tDS
Qe——鍋爐鼓入空氣電能損壞,kJ/tDS
本計(jì)算中焚燒爐以國內(nèi)外常用鼓泡流化床為例,爐內(nèi)不設(shè)置水冷壁(Qa=0)。焚燒所產(chǎn)生的熱量以煙氣形式為載體,排煙熱量占總熱量的93%,即,污泥焚燒損失熱量占總熱量的7%,所以污泥焚燒能量損失Q損=11.9×7%=0.8GJ/tDS。
2.3.3 實(shí)際產(chǎn)能計(jì)算
理論釋能值與焚燒能量損失之差即為污泥焚燒實(shí)際產(chǎn)能值:Q’=Q-Q損=11.1GJ/tDS。污泥焚燒產(chǎn)能主要以煙道氣和水蒸氣為載體,可利用熱電聯(lián)產(chǎn)技術(shù)(CHP)對這部分能量進(jìn)行回收與利用。如果熱電聯(lián)產(chǎn)效率取80%,則污泥焚燒后通過CHP實(shí)際可轉(zhuǎn)化的電當(dāng)量為2480kW·h/tDS。
2.4 能量衡算
根據(jù)上述能量計(jì)算,可以看到建議工藝的能量赤字為109kW·h/tDS。
3 建議工藝成本分析
本研究以處理規(guī)模為50×104m3/d的傳統(tǒng)活性污泥法污水處理廠為例計(jì)算投資與運(yùn)行成本。該案例廠剩余污泥產(chǎn)量為8000t/d(含水率為99%),脫水污泥產(chǎn)量為400t/d(含水率為80%),干污泥為80t/d(含水率為零)。
工藝投資成本由基建成本和設(shè)備成本組成(均為一次性投資),設(shè)備成本根據(jù)污泥產(chǎn)量進(jìn)行選型。污泥脫水以帶式壓濾機(jī)為例,還包括污泥泵、加藥裝置、加藥泵、計(jì)量裝置、輸送機(jī)等設(shè)備投入。機(jī)械脫水全投資成本以2400元/t濕泥(99%含水率)計(jì)算。污泥干化系統(tǒng)設(shè)備主要包括計(jì)量、存儲(chǔ)、進(jìn)料系統(tǒng)、干燥器(以轉(zhuǎn)盤式干燥器為例),投資成本以30萬元/t濕泥(80%含水率)計(jì)算。污泥焚燒系統(tǒng)設(shè)備主要包括焚燒爐(以鼓泡式流化床為例)、煙氣凈化系統(tǒng)、飛灰處理系統(tǒng)等,投資成本以40萬元/t濕泥(80%含水率)計(jì)算。
污泥脫水、干化、焚燒運(yùn)行全成本由電費(fèi)、水費(fèi)、藥劑費(fèi)、工資福利費(fèi)和固定資產(chǎn)折舊費(fèi)、大修費(fèi)、檢修維護(hù)費(fèi)等費(fèi)用構(gòu)成。動(dòng)力費(fèi)以電費(fèi)為主,水費(fèi)指沖洗水等用水費(fèi)用,藥劑費(fèi)主要指污泥脫水所用藥劑(混凝劑)費(fèi)用;固定資產(chǎn)折舊費(fèi)為固定資產(chǎn)原值與綜合基本折舊率的乘積;檢修維護(hù)費(fèi)則是固定資產(chǎn)原值與檢修維護(hù)率的乘積。
根據(jù)以上匡算原則,可計(jì)算出建議工藝各單元投資與運(yùn)行成本,結(jié)果如下:
項(xiàng)目 | 機(jī)械脫水 | 污泥干化 | 污泥焚燒 | 總計(jì) |
投資成本(萬元/tDS) | 24 | 150 | 200 | 374 |
運(yùn)行成本(萬元/tDS) | 148 | 1000 | 1515 | 2663 |
4 對比傳統(tǒng)工藝能耗與成本
傳統(tǒng)污泥處理、處置工藝一般由重力濃縮、厭氧消化、機(jī)械脫水、熱媒干化、污泥焚燒5個(gè)單元完成。剩余污泥經(jīng)過重力濃縮后,污泥含水率從99%降為97%,污泥體積可減少2/3,相應(yīng)地可降低厭氧消化運(yùn)行負(fù)荷。在厭氧消化過程中,污泥中有機(jī)質(zhì)轉(zhuǎn)化效率(至CH4)一般為30%~50%,厭氧消化產(chǎn)生的能量一般用于消化池自身加熱。由于厭氧消化降低了污泥有機(jī)質(zhì)含量,也就降低了污泥干基熱值,從而會(huì)減少污泥焚燒過程的能量輸出。
4.1 能量衡算
污泥厭氧消化前含水率為97%,消化后熟污泥含水率略有升高,但相差不大,計(jì)算中取97.5%。厭氧消化過程化學(xué)能轉(zhuǎn)化(CH4)可以產(chǎn)生能量,產(chǎn)能為5.7GJ/tDS,通過CHP轉(zhuǎn)化電當(dāng)量為1284kW·h/tDS,所以,實(shí)際可輸出電當(dāng)量為556kW·h/tDS。經(jīng)厭氧消化后干固體量Ms降為8.41kg/t濕泥(99%含水率),厭氧消化后污泥中有機(jī)質(zhì)含量減少到37%,這就降低了污泥的高位熱值,使得污泥自持燃燒含水率也隨之降低為41.3%。熟污泥經(jīng)厭氧消化后溫度升高至35℃,即T1=35℃,計(jì)算得出厭氧消化后污泥干化實(shí)際能耗為2459kW·h/tDS。熟污泥有機(jī)質(zhì)含量減量為37%,相應(yīng)污泥理論焚燒產(chǎn)能值降為8.0GJ/tDS,污泥焚燒能量損失同前,則污泥干化焚燒后燃燒實(shí)際產(chǎn)能為7.4GJ/tDS,通過CHP轉(zhuǎn)化電當(dāng)量為1653kW·h/tDS。
上述能量衡算表明,傳統(tǒng)處理、處置工藝總能耗為3261kW·h/tDS,總產(chǎn)能為2937kW·h/tDS,能量赤字為324kW·h/tDS。
4.2 成分分析
99%含水率剩余污泥經(jīng)重力濃縮(97%)、厭氧消化污泥含水率變?yōu)?span style="font-family: Arial;">97.5%,污泥體積可減少3/5,機(jī)械脫水污泥處理量減少為3200t/d,可大大降低機(jī)械脫水投資成本;以1800元/t濕泥(99%含水率)計(jì)算,則機(jī)械脫水投資成本降為18萬元/tDS。機(jī)械脫水運(yùn)行成本主要體現(xiàn)在電費(fèi)的降低上,為140元/tDS。經(jīng)厭氧消化后濃縮污泥干固體減量,使得干化、焚燒設(shè)備規(guī)模減小,干化、焚燒投資成本可降至280萬元/tDS。設(shè)備規(guī)模減小必然也會(huì)降低運(yùn)行成本,主要體現(xiàn)在電費(fèi)、檢修費(fèi)、維護(hù)費(fèi)的節(jié)省上。因此,干化、焚燒運(yùn)行成本可降至2264元/tDS。雖然厭氧消化使得機(jī)械脫水、干化、焚燒投資及運(yùn)行成本都有所降低,但仍需考慮重力濃縮、厭氧消化基建和設(shè)備投資以及相應(yīng)的運(yùn)行成本;重力濃縮投資及運(yùn)行成本分別以40萬元/tDS和100元/tDS計(jì)算;厭氧消化投資和運(yùn)行成本分別按250萬元/tDS和200元/tDS計(jì)算。這樣傳統(tǒng)污泥處理、處置工藝的投資成本為588萬元/tDS,運(yùn)行成本為2704元/tDS。
4.3 熱水解對傳統(tǒng)工藝的影響
污泥單獨(dú)厭氧消化有機(jī)物降解、轉(zhuǎn)化效率很低,只有30%~50%;當(dāng)剩余污泥中不含初沉污泥時(shí)厭氧消化有機(jī)物轉(zhuǎn)化率更低,可能只有20%~30%。為提高厭氧消化有機(jī)物轉(zhuǎn)化能源效率,熱水解技術(shù)被用作厭氧消化的預(yù)處理工藝,并獲得一些應(yīng)用。污泥熱水解是在一定溫度和壓力下,將污泥在密閉的容器中進(jìn)行加熱,使污泥細(xì)胞部分發(fā)生破壁,以增加污泥后續(xù)厭氧消化有機(jī)物轉(zhuǎn)化率,但提高厭氧消化有機(jī)物轉(zhuǎn)化率后的消化污泥后續(xù)焚燒能源釋放量會(huì)相應(yīng)較少,況且,熱水解設(shè)備投資與運(yùn)行費(fèi)用價(jià)格不菲。因此,需要對接入熱水解的傳統(tǒng)污泥處理、處置工藝進(jìn)行能量平衡以及成本核算。
污泥經(jīng)重力濃縮和預(yù)脫水(預(yù)處理)含水率可降至85%,能耗約60kW·h/tDS。經(jīng)熱水解預(yù)處理后進(jìn)行厭氧消化,有機(jī)物降解率可從30%提高至50%,導(dǎo)致厭氧消化產(chǎn)能升至9.58GJ/tDS,利用CHP轉(zhuǎn)化為電當(dāng)量是2130kW·h/tDS。熱水解亦消耗能量,約為厭氧消化產(chǎn)能的60%,即為1278kW·h/tDS;熱水解后污泥冷卻可釋放一定熱量(經(jīng)熱交換器),約為厭氧消化產(chǎn)能的20%,即426kW·h/tDS,可用于污泥干化。由于熱水解污泥升溫至180℃,所以,厭氧消化過程消化池?zé)o需加熱,只需熱水解后降溫至35℃。這樣,污泥干固體量Ms降低為7.35kg/t濕泥(99%含水率),消化后污泥有機(jī)物含量降低至26.5%,使得后續(xù)污泥干基熱值降低、污泥自持燃燒含水率也相應(yīng)降至21.1%(接近全干化水平)。實(shí)際上,這種已成干泥塊狀的污泥很難在流化床焚燒爐中流化焚燒。因此,干化污泥含水率按可流化的41.3%考慮,污泥干化能耗為2153kW·h/tDS,但這樣含水率(41.3%)的污泥無法實(shí)現(xiàn)自持焚燒,需要投加外部輔助燃料,約429kW·h/tDS。因厭氧消化熟污泥有機(jī)質(zhì)含量減少,導(dǎo)致污泥焚燒產(chǎn)能降低為5.0GJ/tDS,轉(zhuǎn)化電當(dāng)量為1111kW·h/tDS。
能量衡算表明,熱水解介入傳統(tǒng)污泥處理、處置工藝后總能耗為3980kW·h/tDS,總產(chǎn)能為3241kW·h/tDS(14.58GJ/tDS),熱水解冷卻水釋放熱量(426kW·h/tDS)可用于污泥干化,但能力赤字為313kW·h/tDS。
熱水解介入傳統(tǒng)污泥處理、處置工藝后固然使總的能量赤字(324kW·h/tDS)有所降低,并且使得厭氧消化后污泥進(jìn)一步減量,從而降低后續(xù)機(jī)械脫水、干化、焚燒的投資及運(yùn)行成本。但是,熱水解設(shè)備高昂的投資成本(75萬元/tDS)和較大的運(yùn)行成本(389元/tDS),導(dǎo)致整個(gè)工藝投資與運(yùn)行成本分別達(dá)到615萬元/tDS和3029元t/DS。
4.4 與建議工藝綜合對比
與傳統(tǒng)工藝及熱水解介入傳統(tǒng)工藝相比較,污泥干化、焚燒建議工藝的能量赤字較低,僅為109kW·h/tDS。在投資以及運(yùn)行成本上,建議工藝顯然也是較低的,分別為374萬元/tDS和2663元/tDS。其他兩種工藝投資與運(yùn)行成本分別為:588萬元/tDS和2704元/tDS以及615萬元/tDS和3029元/tDS。
建議工藝能量赤字較其他兩種比較工藝(324kW·h/tDS與313kW·h/tDS)可分別降低66.4%和65.2%;建議工藝投資成本(374萬元/tDS)較其他兩種工藝(588萬元/tDS和615萬元/tDS)分別降低36.4%和39.2%;建議工藝運(yùn)行成本(2663元/tDS)較其他兩種工藝(2704元/tDS和3029元/tDS)分別降低1.5%和12.1%。
5 結(jié)語
通過對污泥直接脫水、干化、焚燒建議工藝能量衡算以及投資與運(yùn)行成本匡算顯示,其能量赤字僅為109kW·h/tDS,投資與運(yùn)行成本也只有374萬元/tDS和2663元/tDS,與傳統(tǒng)及介入熱水解預(yù)處理污泥處理、處置工藝相比,污泥干化焚燒建議工藝在能量赤字及投資與運(yùn)行成本上均較低,能量赤字分別減少66.4%和65.2%,投資成本分別減少36.4%和39.2%,運(yùn)行成本分別減少1.5%和12.1%??梢?,污泥干化后直接焚燒建議工藝在污泥全生命周期(LCA)處理/處置方面較佳,同時(shí)還能較為有效地從焚燒灰分中回收磷等無機(jī)資源。
如果污水余溫可以通過水源熱泵(WSHP)加以原位利用,污泥干化所需熱量則可以大大減少甚至無需外部能源。因此,污水廠內(nèi)分散式干化,集中到某一適宜地點(diǎn)焚燒發(fā)電、供熱將有可能實(shí)現(xiàn)并將污水余溫低品位能源間接轉(zhuǎn)換為可發(fā)電的高溫?zé)崮堋N鬯鄿鼐徒糜诟苫杀苊馕鬯幚韽S“有能輸不出”的現(xiàn)實(shí)問題,從而使污水處理廠成為能源工廠,不僅實(shí)現(xiàn)自身碳中和運(yùn)行,而且還可以向外輸電。簡言之,省略污泥厭氧消化單元還能較大限度避免甲烷(CH4)這種強(qiáng)溫室氣體逸散的問題以及運(yùn)行安全隱患。