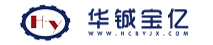
利用無(wú)機(jī)陶瓷膜濃縮分離技術(shù)及膜親水疏油的特性,在步需要破乳的情況下,可直接實(shí)現(xiàn)乳化懸浮液中的油和超細(xì)顆粒與它們存在的介質(zhì)的分離。但在實(shí)際工作中,過(guò)濾一段時(shí)間后由于濃差極化作用,使無(wú)機(jī)陶瓷超濾膜的表層附著一層污染物,這將會(huì)大大降低膜的滲透通量;同時(shí)也有可能由于非正常操作,導(dǎo)致膜的嚴(yán)重污染,需要合適的工藝進(jìn)行化學(xué)清洗。
目前,國(guó)內(nèi)外文獻(xiàn)對(duì)無(wú)機(jī)陶瓷膜處理懸浮液的報(bào)道較多,但很少涉及到陶瓷膜污染后再生的研究。南京化工大學(xué)趙宜江等對(duì)陶瓷微濾膜回收偏鈦酸過(guò)程中膜的清洗問(wèn)題進(jìn)行了研究;撫順石油學(xué)院孫杰等在陶瓷微濾膜處理鈦白廢水過(guò)程中采用反沖方式對(duì)膜進(jìn)行清洗;中北大學(xué)劉有智、高松平等在探討用陶瓷超濾膜對(duì)乳化懸浮液的凈化處理時(shí)提及用滲透液清洗污染膜的再生工藝,但未對(duì)其進(jìn)行系統(tǒng)的研究。因此,本文以膜處理催化劑生產(chǎn)過(guò)程中廢氨液后的再生工藝為例,分別采用物理和化學(xué)方法,對(duì)被污染的陶瓷超濾膜進(jìn)行了再生工藝研究;并通過(guò)探討清洗工藝如動(dòng)態(tài)清洗、溫度、清洗劑濃度、操作方式等對(duì)膜層清洗效果的影響,確定其適宜的再生工藝參數(shù)。
1 實(shí)驗(yàn)
1.1 膜的選擇
采用自制的19通道管式α-Al2O3陶瓷膜,內(nèi)徑3.5mm,有效過(guò)濾面積為0.2㎡,管長(zhǎng)為1m,膜孔徑為0.08μm。
1.2 實(shí)驗(yàn)料液
由某廠提供催化劑生產(chǎn)過(guò)程中的廢氨液,是一種含有超細(xì)固體顆粒的白色不透明渾濁乳化懸浮液,含有以乳化油和溶解油形式存在的礦物油、表面活性劑以及粒度為0.01~0.1μm的超細(xì)氫氧化鋁和氨水,pH值為13.5。
1.3 試驗(yàn)裝置及流程
儲(chǔ)料罐中的原料液以一定的流量進(jìn)入膜組件中,在壓差的推動(dòng)下錯(cuò)流過(guò)濾,清液從膜組件的側(cè)面經(jīng)透過(guò)液出口流出,濃縮后的料液返回儲(chǔ)料罐中循環(huán)過(guò)濾。由閥門(mén)調(diào)節(jié)控制料液的流速和過(guò)濾壓差;壓力表測(cè)量膜進(jìn)口壓力和膜的出口壓力。
1.4 檢測(cè)方法
原料液的固含量用重量法檢測(cè),透過(guò)液的固含量用分光光度法檢測(cè);原料液和透過(guò)液的含油量通過(guò)測(cè)定其COD來(lái)判定。
2 試驗(yàn)結(jié)果和討論
2.1 動(dòng)態(tài)膜清洗工藝研究
在超濾中,濃差極化不可忽視。用陶瓷膜處理含有超細(xì)顆粒的乳化懸浮液,過(guò)濾效果和過(guò)濾阻力主要受由濃差極化而形成的動(dòng)態(tài)膜控制,因此在對(duì)此類膜進(jìn)行再生時(shí),不應(yīng)該將動(dòng)態(tài)膜破壞。普通的直接用水反沖的物理方法或用化學(xué)方法直接清洗的方法都是不合適的,而應(yīng)根據(jù)逆向濃差極化對(duì)其動(dòng)態(tài)膜的外層部分進(jìn)行清洗,首先選擇用透過(guò)液(或稀料液交替過(guò)濾)進(jìn)行物理清洗的方法。
在0.15MPa的操作壓力下,先過(guò)濾0.72%的料液后再過(guò)濾0.35%料液。當(dāng)過(guò)濾濃度為0.72%的料液時(shí),膜通量逐漸衰減,當(dāng)換成濃度為0.35%的料液過(guò)濾時(shí),發(fā)現(xiàn)膜通量逐漸恢復(fù)到過(guò)濾濃度為0.72%料液的初始通量,且透過(guò)液澄清透亮;對(duì)過(guò)濾液進(jìn)行分析可知,固含量去除率達(dá)到98%,去油率達(dá)到99.6%。
當(dāng)過(guò)濾濃度為0.78%料液后再過(guò)濾濃度0.41%的料液,膜通量逐漸恢復(fù)至初始通量的96%以上,去油率達(dá)99.2%。這些現(xiàn)象充分說(shuō)明用于稀濃度料液過(guò)濾的過(guò)程就是膜清洗的過(guò)程。
膜通量之所以能基本恢復(fù)是因?yàn)榈蜐舛鹊牧弦哼M(jìn)入膜內(nèi),其本體濃度小于前次過(guò)濾高濃度的料液因濃差極化而積累到膜面上形成極化層的濃度。所以,高濃度料液過(guò)濾完后,再過(guò)濾低濃度料液,一方面,不可能出現(xiàn)因濃差極化而造成的膜污染;另一方面,正因?yàn)榈蜐舛鹊牧弦旱臐舛刃∮谀っ鏄O化層的濃度,所以膜面上高濃度極化層上的顆粒向低濃度的料液的本體相擴(kuò)散,減小了過(guò)濾阻力,膜通量逐漸增大,低濃度的料液對(duì)膜面起了清洗作用,當(dāng)料液本體濃度與膜面上積累的顆粒濃度再達(dá)到平衡后,膜通量趨于穩(wěn)定。
2.2 溫度對(duì)膜清洗效果的影響
經(jīng)研究發(fā)現(xiàn),膜被嚴(yán)重污染后在溫度為35~40℃和常溫兩種條件下用相同的清洗液清洗膜層,膜通量有著明顯的差距。在0.15MPa的操作壓力下,在常溫(18℃)條件下循環(huán)清洗后,膜通量始終是11.7L/㎡/h,洗40min膜通量都沒(méi)變化;在溫度為35~40℃的清洗液中循環(huán)清洗后,膜通量比在常溫時(shí)明顯上升。在實(shí)驗(yàn)中還發(fā)現(xiàn),經(jīng)常溫清洗后,透過(guò)液澄清透明;而在溫度為35~40℃的清洗液中循環(huán)清洗時(shí)透過(guò)液上面浮有油脂。這說(shuō)明升高溫度有益于油脂的流動(dòng)性能增強(qiáng),穿透膜的能力增強(qiáng),有益于膜的清洗,但從整體清洗效果來(lái)說(shuō),對(duì)膜通量的恢復(fù)沒(méi)有明顯效果,35~40℃下洗液通量?jī)H有20L/㎡/h,與正常通量相比小得多(一般膜的正常通量為85L/㎡/h)。因此在工業(yè)化應(yīng)用中,選擇常溫下進(jìn)行清洗較為適宜。
2.3 后處理工藝
2.3.1 清洗劑濃度對(duì)清洗效果的影響
量取200mL的0.5%、1%、2%、3%的氫氧化鈉溶液倒入盛有相同質(zhì)量的上述油污的三角瓶中,劇烈搖動(dòng)大約20min,大片白色絮狀油脂分散成不溶的渾濁的小顆粒,靜止一會(huì)沉于下部。說(shuō)明清洗時(shí),用低濃度的堿液就可以。因此選用0.5%和1%的堿液作為堿性清洗劑。
在劇烈搖動(dòng)下,堿與油脂結(jié)合后,酸就很容易與無(wú)機(jī)鹽氫氧化鋁反應(yīng)。把上述渾濁液分別用漏斗過(guò)濾洗滌成中性,用0.1mol/L、0.2mol/L、0.5mol/L、1mol/L的鹽酸進(jìn)行中和反應(yīng),渾濁液都變成清亮溶液。說(shuō)明用酸清洗時(shí)用低濃度的鹽酸就可以了,選用0.1mol/L鹽酸和1%的檸檬酸作為酸性清洗劑。
2.3.2 操作方式對(duì)清洗效果的影響
量取3份200mL的1%的氫氧化鈉溶液,分別放入盛有相同質(zhì)量上述油污的瓶中,采用不同的操作方式,對(duì)比效果如下:
編號(hào) | 操作方式 | 現(xiàn)象 |
1 | 劇烈搖動(dòng) | 大片白色絮狀油脂分散成不溶的渾濁的小顆粒 |
2 | 靜止放置7天 | 大片白色絮狀油脂仍存在,狀態(tài)沒(méi)有改變 |
3 | 靜止放入55℃烘箱內(nèi)4h | 大片白色絮狀油脂仍存在,狀態(tài)沒(méi)有改變 |
由上表可知,短時(shí)間的劇烈搖動(dòng)比長(zhǎng)期靜止和升溫處理的效果都要好。
同時(shí)做了放大實(shí)驗(yàn),放大的堿洗操作方式對(duì)清洗效果影響如下:
操作方式 | 膜通量的變化 |
膜在1%堿液中浸泡一次 | 膜通量基本保持在浸泡前的通量 |
由泵循環(huán)1%堿液沖洗膜一定的時(shí)間 | 膜通量由24.6L/㎡/h恢復(fù)到103.5L/㎡/h |
由上表可知,短時(shí)間循環(huán)堿液沖洗膜層的清洗效果明顯優(yōu)于在堿液中長(zhǎng)期浸泡。這是因?yàn)椋簤A洗對(duì)油污的作用主要是通過(guò)堿液高速流動(dòng)對(duì)膜面上的油污進(jìn)行剪切沖洗,破壞油污的紊凝狀態(tài),使油污變成小顆粒狀;一方面有利于堿液與油污的充分作用,化解油污;另一方面,有利于高速流動(dòng)的堿液夾帶走小顆粒油污,達(dá)到清洗的目的。因此,應(yīng)選擇堿液在高速流動(dòng)狀態(tài)下來(lái)清洗油污較為適宜。
酸洗操作方式對(duì)膜層清洗效果的影響如下:
操作方式 | 膜通量的變化 |
膜在0.5mol/L的酸中浸泡一夜 | 初始膜通量為94L/㎡/h,然后逐漸恢復(fù)到103.5L/㎡/h |
泵循環(huán)0.5mol/L酸沖洗膜一定時(shí)間 | 初始膜通量為94L/㎡/h,然后逐漸恢復(fù)到103.5L/㎡/h |
由上表可知,酸洗的操作方式對(duì)清洗效果影響不大。這可能因?yàn)閴A液沖洗掉一定的油脂后,酸就比較容易和氫氧化鋁接觸進(jìn)行比較快速的、有效的反應(yīng),從而酸洗操作方式的影響顯得不太明顯。
2.3.3 混合清洗工藝
由0.15mol/L堿液、0.15mol/L鹽酸和1%的檸檬酸組成混合清洗劑。先用堿液在0.15MPa的操作壓力、高膜面流速下剪切污染物一定時(shí)間,然后用清水洗成中性,再用酸浸泡或循環(huán)一定時(shí)間,然后用清水洗成中性,測(cè)量其通量,若膜通量未恢復(fù),繼續(xù)加入清洗劑交替清洗?;旌锨逑磩┻M(jìn)行交替清洗,效果良好。清洗后膜通量可恢復(fù)到原穩(wěn)定膜通量的95%以上。
3 結(jié)論
(1)用透過(guò)液或低濃度料液清洗受污陶瓷膜,操作簡(jiǎn)單方便,不產(chǎn)生二次污染;又由于此類清洗對(duì)動(dòng)態(tài)膜的影響較小,所以這樣不但可以恢復(fù)膜通量,而且也可顯著延長(zhǎng)膜的使用壽命,確保膜超濾的穩(wěn)定運(yùn)行,是既經(jīng)濟(jì)有效,又實(shí)現(xiàn)了生產(chǎn)過(guò)程連續(xù)化的適宜方法。
(2)升溫操作有益于膜的清洗,但從整體清洗效果來(lái)說(shuō),對(duì)膜通量的恢復(fù)沒(méi)有明顯效果,35~40℃下洗液量?jī)H有20L/㎡/h,與膜正常通量85L/㎡/h相比小的多,因此在工業(yè)化應(yīng)用中,選擇常溫下進(jìn)行清洗較為適宜。
(3)膜停止工作后的后處理工藝中,酸堿清洗劑的濃度對(duì)陶瓷膜清洗效果的影響不大,可選用0.5%和1%的堿液作為堿性清洗劑,選用0.1mol/L鹽酸和1%的檸檬酸作為酸性清洗劑。酸堿液的操作方式對(duì)清洗效果有很大的影響,劇烈搖動(dòng)的清洗效果明顯優(yōu)于長(zhǎng)期浸泡和升溫清洗,因此應(yīng)選擇酸堿液在高速流動(dòng)狀態(tài)下來(lái)清洗油污較為適宜。采用0.15mol/L堿、0.15mol/L鹽酸和1%的檸檬酸組成混合清洗劑進(jìn)行交替清洗,既可減少油脂對(duì)膜的污染,也可對(duì)膜通量起到一定的恢復(fù)作用。