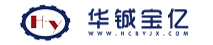
老化油又被稱為油田絮凝物、油水中間過渡層、油水中間乳化層等,是原油生產(chǎn)、處理過程中,在藥劑、機械雜質(zhì)、膠質(zhì)瀝青質(zhì)、細菌、空氣、循環(huán)剪切等因素的作用下形成的。老化油在形成過程由于化學反應、固體顆粒雜質(zhì)、高分子化合物、污水處理藥劑及增產(chǎn)增注化學劑等乳化劑的混入,使其界面活性物質(zhì)增加,并隨時間的延長在油水界面不斷富集,使界面膜的強度和厚度增加形成穩(wěn)定性很高的原油乳狀液,對油水分離造成較大影響。
老化油來源主要為二次、三次采油形成的乳化液顆粒;鉆井作業(yè)及原油輸送過程中形成的乳化液;污水處理回收的污油;回收的落地油;細菌作用下產(chǎn)生的含油懸浮物等。
近年來隨著XM油田開發(fā)進入中后期,站外酸化壓裂、調(diào)剖調(diào)驅(qū)等增油措施逐漸增多,油井采出液組成越來越復雜,導致XM油田聯(lián)合站一直被老化油的問題所困擾,直接影響聯(lián)合站脫水系統(tǒng)的穩(wěn)定性,造成外輸原油經(jīng)常含水超標。常規(guī)熱化學沉降脫水和熱化學電場處理老化油效果較差,因此,急需尋找新技術和新處理工藝解決老化油問題,以提高脫水系統(tǒng)穩(wěn)定性,提高原油商品率。
1 XM油田聯(lián)合站老化油現(xiàn)狀
XM油田聯(lián)合站外輸原油35萬t/a,各儲罐外排老化油約為8000t/a。為了減少老化油對脫水主系統(tǒng)的影響,2010年XM油田聯(lián)合站通過流程改造,實現(xiàn)各儲罐內(nèi)老化油定期收集、單獨處理。聯(lián)合站老化油處理主流程為:定期將各儲罐中間層老化油定期泵抽到1000m3老化油沉降罐,通過循環(huán)加藥、提壓、加熱循環(huán)等操作流程,儲罐內(nèi)老化油經(jīng)長時間高溫熱化學沉降后,儲罐頂部原油含水達標后去外輸系統(tǒng)直接外輸,罐底污水去污水處理系統(tǒng)進一步處理。
但是,由于老化油處理采用常規(guī)熱化學沉降脫水工藝流程,儲罐內(nèi)老化油循環(huán)加藥至70℃,加藥濃度達到200mg/L,沉降超過72h后,沉降罐高液位出口原油含水率仍為10%以上,遠遠高于0.5%,滿足不了直接外輸要求,影響站內(nèi)正常生產(chǎn)。
2 室內(nèi)化驗結果分析
經(jīng)過現(xiàn)場取樣和室內(nèi)化驗分析,XM油田聯(lián)合站1000m3油罐老化油是含有大量固體物質(zhì)的油水強乳化液,其中,固體含量約為20%,水含量約為35%,原油含量約45%。老化油20℃時密度為0.932g/cm3,主系統(tǒng)凈化油20℃時密度為0.868g/cm3;老化油50℃時黏度為400mPa·s,主系統(tǒng)凈化油50℃時黏度為45mPa·s,老化油與主系統(tǒng)外輸凈化油物性差別大。老化油密度大、黏度高,導致原油流動性差,油水分離困難。
老化油組分分析結果:瀝青質(zhì)含量為5.89%,膠質(zhì)含量為17.28%,蠟含量為69.98%,芳香化合物含量為4.78%,機械雜質(zhì)含量為1.13%。組分中蠟、膠質(zhì)和瀝青質(zhì)含量較高,而芳香化合物含量低,說明老化油中重質(zhì)組分較多,輕烴類組分較少。
老化油固相分析結果:兩種老化油固體雜質(zhì)成分主要分為3類:一是,混入的砂土成分,包括石英、黏土等;二是,可能的結垢產(chǎn)物CaCO3;三是,腐蝕產(chǎn)生的鐵和硫的化合物。具體分析結果如下表所示:
固相組分 | 含量(%) | 固相組分 | 含量(%) |
石英(α-SiO2) | 18 | 硫復鐵礦(Fe3S4) | 8 |
斜長石(NaAlSi3O8) | 10 | 石鹽(NaCl) | 9 |
方解石(CaCO3) | 16 | 黏土 | 30 |
黃鐵礦(FeS2) | 9 |
從上表可以看出老化油中鐵和硫的化合物(FeS2和Fe3S4)含量為17%,老化油中鐵和硫的化合物粒徑分布為3.86~50.46μm,呈膠體狀態(tài),因而,其活性較強。鐵和硫的化合物作為界面活性物質(zhì),有助于油水乳化,促進油-水中間過渡層生成。
老化油水相分析結果:關鍵指標Fe2+,凈化油水相Fe2+含量僅為36mg/L,而老化油水相Fe2+含量高達179~195mg/L;凈化油水相中S2-含量僅為26mg/L,而老化油水相S2-含量高達161~202mg/L。老化油中含有較多的Fe2+、S2-,可見這兩種離子對老化油的形成作用較大,初步判斷FeS為老化油形成的主要原因。
根據(jù)老化油、密度、黏度、組成分析、固相分析和水相分析結果,可以判定XM老化油物性差、組分中重質(zhì)組分多、固相中鐵和硫的化合物含量高,水相中Fe2+和S2-含量高,這些綜合因素導致XM老化油處理困難。
3 老化油室內(nèi)離心分離試驗
實驗中使用濃度為2g/100mL的高錳酸鉀溶液作為FeS去除劑,取15mL離心管,加入13mL同種老化油和0.5mL的高錳酸鉀溶液。離心油樣測定含水率為21%,升溫至65℃后,選定不同的離心機轉(zhuǎn)速和離心時間進行離心脫水對比實驗,測定離心后各層體積。
從老化油離心8min后兩層的含水率數(shù)據(jù)可以看出,離心力越大,油層的含水率越低,離心力1000g時,油層的含水率已低于0.5%,達到了合格原油的標準;離心力1500g時,油層中已檢測不出含水。油水過渡層的含水率隨離心力的增大同樣呈現(xiàn)先增大后減小的趨勢,1000g時為極值。
室內(nèi)離心分離試驗初步證明XM老化油離心分離具有可行性,合理的離心參數(shù)為離心力1000g、時間8min。
4 離心分離裝置的構成
該離心分離裝置主要由臥螺式離心分離系統(tǒng)、碟片式離心分離系統(tǒng)和加藥系統(tǒng)3部分組成:老化油首先進入臥螺式離心分離機,在絮凝劑的作用下,實現(xiàn)固、液分離,分離出來的含水油進入碟片式離心機,在破乳劑的作用下實現(xiàn)進一步脫水。
5 現(xiàn)場試驗情況
5.1 裝置現(xiàn)場安裝情況
老化油處理橇裝設備處理量為150t/d,裝置于2013年11月10日運至XM聯(lián)合站現(xiàn)場,裝置位置距離原油儲罐、泵房值班室等構筑物均滿足安全防火技術規(guī)范要求,經(jīng)過現(xiàn)場組裝連接并調(diào)試,于2014年1月15日具備現(xiàn)場試驗開工條件。裝置來油為聯(lián)合站站內(nèi)1000m3老化油儲罐,裝置出口合格原油去站內(nèi)外輸油泵出口,裝置出口污水去站內(nèi)污水處理系統(tǒng),裝置殘渣出口直接用防滲密封袋打包。
5.2 現(xiàn)場試驗情況
正式現(xiàn)場試驗于2014年2月20日開始,至3月5日結束,試驗過程中每天現(xiàn)場跟蹤運行情況,監(jiān)測節(jié)點指標變化,發(fā)現(xiàn)異常及時提醒現(xiàn)場施工人員進行調(diào)整。試驗期間進裝置老化油溫度為45℃,含水率約為35%,裝置平穩(wěn)運行時加藥濃度為100mg/L,裝置加熱爐出口溫度為65℃。
5.3 現(xiàn)場運行效果
現(xiàn)場試驗歷經(jīng)14天,合計處理老化油量1000m3,試驗過程中裝置運行平穩(wěn)、無漏油、觸電等安全事故,裝置出口原油含水率,污水油含量,廢渣含水,廢渣油含量各項指標均達到預期要求。
5.4 運行費用
試驗過程中共處理老化油1000m3(折合930t),消耗天然氣2500m3,消耗電能5500kW·h,消耗破乳劑100kg,天然氣價格按2.36元/m3,電價為0.55元/kW·h,破乳劑價格為2.0元/kg計算,若不含人工費,老化油離心分離綜合運行費用為9.8元/t,運行費用較低。
6 結語
老化油離心脫水技術在油田聯(lián)合站現(xiàn)場應用可行,裝置實現(xiàn)連續(xù)平穩(wěn)運行,處理后原油含水、污水油含量、污泥含水率及廢渣含水率均能滿足生產(chǎn)需求。老化油離心分離技術提高了原油商品率,處理后的廢渣作為建筑空心磚原料,提高了原料利用率,有利于環(huán)境保護。采用離心分離處理后的老化油可直接外輸,提高了原油商品率,經(jīng)濟效益良好,具有廣闊的應用前景。