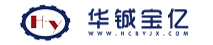
1 污泥干化設(shè)備工藝類型及工作原理
1.1 熱對流干燥系統(tǒng)
早期的直接熱干燥系統(tǒng)是將外部熱介質(zhì)(熱空氣、燃?xì)饣蛘羝龋┘訜岷笸ㄈ敫稍锲髋c污泥直接接觸,蒸發(fā)污泥中的水分并運(yùn)送污泥。熱介質(zhì)離開干燥器后與干污泥顆粒分離,經(jīng)除塵、熱氧化除臭后排放。由于系統(tǒng)所需熱風(fēng)量很大,故尾氣處理成本較高。目前該工藝采用了氣體循環(huán)回用的設(shè)計(jì),使尾氣處理成本高這一缺陷得到明顯改善。在其干燥工藝中,熱介質(zhì)經(jīng)除塵、冷凝、水洗后,只需對15%的熱介質(zhì)進(jìn)行熱氧化除臭并排放,其余的85%可直接返回干燥器。這不僅減小了尾氣處理的負(fù)擔(dān),更重要的是大大降低了外部熱介質(zhì)的引入量,將干燥器內(nèi)的氧氣含量維持在較低水平,從而大幅提高了系統(tǒng)的安全性能。直接加熱轉(zhuǎn)鼓式干燥機(jī)是較常用的熱對流干燥設(shè)備。熱對流干燥系統(tǒng)具有如下優(yōu)、缺點(diǎn):
(1)熱對流工藝對污泥進(jìn)行全干化時(shí)傳熱傳質(zhì)效率較高,對污泥進(jìn)行半干化時(shí)能耗較高,因此該干燥系統(tǒng)更適于全干化工藝。
(2)熱對流干燥系統(tǒng)的強(qiáng)擾動和機(jī)械作用對污泥顆粒的堅(jiān)硬外殼具有較強(qiáng)的破壞能力,可使內(nèi)部的潮濕污泥外露,提高熱傳輸效率及蒸發(fā)速率。
(3)后續(xù)冷凝洗滌廢水量大,處理費(fèi)用較高。
(4)系統(tǒng)的額外能耗增加。這是由于熱對流干燥系統(tǒng)采用的是氣體循環(huán)回用設(shè)計(jì)實(shí)際上是對循環(huán)載氣進(jìn)行反復(fù)的加熱、冷凝和洗滌,致使熱損失很大。
(5)該系統(tǒng)內(nèi)部的氣體流動量大,粉塵濃度高,因此安全性較低。
(6)整個(gè)系統(tǒng)龐大、復(fù)雜,給操作和管理帶來一定的麻煩。
1.2 熱傳導(dǎo)干燥系統(tǒng)
熱傳導(dǎo)干燥系統(tǒng)不存在大量工藝載氣的循環(huán),系統(tǒng)僅抽取相當(dāng)于蒸發(fā)量的部分進(jìn)行冷凝,通常采用抽取微負(fù)壓方式,也有部分工藝采用少量載氣的方式,因此尾氣處理的負(fù)擔(dān)較輕,且載氣熱損失也較低。目前國內(nèi)外常用的熱傳導(dǎo)干燥機(jī)主要有多層臺階式干燥機(jī)、轉(zhuǎn)盤式干燥機(jī)等。
熱傳導(dǎo)干燥系統(tǒng)具有如下優(yōu)、缺點(diǎn):
(1)熱傳導(dǎo)工藝系統(tǒng)進(jìn)行全干化時(shí)能耗高、效率低,更適于半干化工藝。
(2)無需載氣或所需載氣量較小,因此氣體產(chǎn)量少,后續(xù)尾氣處理費(fèi)用較低。
(3)系統(tǒng)內(nèi)部氣體流動性小,因此粉塵濃度低,系統(tǒng)安全性較高。
(4)干燥器內(nèi)部的運(yùn)動部件較多,維修費(fèi)用較高。
目前歐美等 常用的干化系統(tǒng)主要以直接干燥轉(zhuǎn)鼓式工藝、多層臺階式干化工藝、轉(zhuǎn)盤式干化工藝、流化床干化工藝等為主。此外還有碟片式、帶式、日光式等干化工藝,但在大型工程中的應(yīng)用很少。
1.3 干料返混工藝
為避免全干化過程中的污泥粘結(jié)、干燥效率低等問題,目前多采用干料返混工藝手段,該工藝具有如下特點(diǎn):
(1)由于城市污泥干燥過程存在“膠粘相”階段(含水率為60%左右),在此過渡段內(nèi)污泥極易結(jié)塊,具有表面堅(jiān)硬、難以粉碎而里面卻仍是稀泥的特點(diǎn),這給污泥的進(jìn)一步干燥和滅菌帶來較大困難。而干料返混方式可以使污泥的含水率降至50%左右,使其直接越過“膠粘相”,大大減輕了污泥在干燥器內(nèi)的粘結(jié),從而提高了熱傳輸效率及蒸發(fā)速率。
(2)干料返混工藝還可改善初始進(jìn)料濕污泥含水率變化的敏感性。一般干燥系統(tǒng)在運(yùn)行過程中,供熱量及其相關(guān)的工藝氣體量已經(jīng)確定,當(dāng)進(jìn)料含水率變化而進(jìn)料量不變時(shí),系統(tǒng)內(nèi)部的濕度平衡被破壞,從而引發(fā)如下問題:
①濕度增加可能導(dǎo)致干化不均。
②濕度減少則意味著粉塵量的增加和顆粒溫度的上升,使系統(tǒng)安全性大大降低。
而采用干料返混工藝則能夠擴(kuò)大可允許的濕泥波動范圍。干料返混實(shí)際上就是用5~10倍的絕干物質(zhì)來混合初始污泥,例如用5倍含固率為90%的干泥顆粒混合濕泥,則當(dāng)濕泥的含固率為10%~20%時(shí),混合物你的含固率為50%~55%,可見干料返混可擴(kuò)大濕泥波動范圍,提高系統(tǒng)的安全性和穩(wěn)定性。
(3)干料返混工藝的熱損失能耗高。這是由于濕泥的含固率一般較低,致使返混比例較高,從而形成對大量干污泥載體的反復(fù)加熱、冷卻造成的。干料返混工藝的熱損失由兩個(gè)因素決定:
①返混的目標(biāo)含固率。含固率越高則所需返混干泥的比例越高,形成熱損失的物質(zhì)總量越高。
②干燥器進(jìn)口混合料和出口產(chǎn)品的溫差。該值決定了單位質(zhì)量物質(zhì)的熱損失幅度,由此可以計(jì)算干料返混工藝的熱損失。
2 干燥工藝的技術(shù)要點(diǎn)
2.1 能耗
污泥干燥是一個(gè)能量凈支出的過程,耗能費(fèi)用在一個(gè)標(biāo)準(zhǔn)干化系統(tǒng)運(yùn)行成本中的比例>80%,因此對熱能損耗的研究是干化系統(tǒng)研究及改進(jìn)的重點(diǎn)。
干化的熱損失主要來自熱源和干燥工藝兩方面。不同類型熱源的熱利用效率不同,傳輸距離、保溫狀況均對熱源的熱利用效率產(chǎn)生較大影響,減少這部分熱損失的原則是:優(yōu)化熱源,優(yōu)化選擇和組合換熱器,縮短傳輸距離,強(qiáng)化保溫效果。
不同的工藝類型對熱損失的影響很大,含水率較高時(shí)熱傳導(dǎo)通過傳熱面發(fā)生固液傳熱,傳熱效率高于熱對流的氣液傳熱,干燥后期污泥進(jìn)入“膠粘相”階段,此時(shí)熱對流的傳熱效率較高;全干化工藝干燥載氣的反復(fù)冷凝、洗滌、加熱過程具有較大的熱損失;此外干料返混工藝的特點(diǎn)也決定了其熱損失較大。減少這部分熱損失的原則是:合理降低產(chǎn)品含固率,使之優(yōu)化并適應(yīng)污泥的處置要求;選擇適合產(chǎn)品含固率的工藝類型;改善冷凝條件如減少載氣量、分步冷凝等,減少工藝步驟、縮短工藝路線,優(yōu)化運(yùn)行參數(shù)以提高干燥效率。
2.2 安全性
老式干燥器存在起火或爆炸頻繁的缺點(diǎn),使污泥干燥設(shè)備的安全性能倍受質(zhì)疑。對工藝安全性具有重要影響的要素包括:粉塵濃度,一般要求粉塵濃度<60g/m3;工藝允許的含氧量(燃燒氣氛的惰性化),一般要求氧氣含量<12%;顆粒溫度(點(diǎn)燃能量);濕度(氣體的濕度和物料的濕度對提高或降低粉塵爆炸下限具有重要影響)。
由于污泥的粉塵爆炸濃度下限值較低,當(dāng)含氧量條件具備時(shí),污泥顆粒的點(diǎn)燃溫度較低。因此,降低污泥顆粒溫度并不是排除粉塵爆炸的根本性條件。此外,提高干燥器內(nèi)的濕度,易使水蒸氣的平衡分壓增大,導(dǎo)致濕污泥中水分的干燥速率降低,同樣也不是提高干燥器安全性的主要手段。這表明保障系統(tǒng)的安全性應(yīng)從降低粉塵濃度和降低含氧量兩方面考慮,對干燥器內(nèi)的粉塵濃度和含氧量進(jìn)行實(shí)時(shí)監(jiān)測,并采取針對性措施來完善設(shè)計(jì)和加強(qiáng)管理。
3 結(jié)語
(1)降低污泥含水率是解決目前污泥處理所面臨困難的關(guān)鍵。污泥干化處理是污泥處理、處置重要的“ 步”,為后續(xù)的污泥處理處置及資源化提供了多種選擇。
(2)目前國內(nèi)外污泥干燥工藝主要分為熱對流工藝和熱傳導(dǎo)工藝兩種類型。熱對流工藝更適合污泥的全干化,熱傳導(dǎo)則更適合污泥的半干化。與熱傳導(dǎo)相比,熱對流具有對尾氣、洗滌水等二次污染處理費(fèi)用高、系統(tǒng)安全性低、循環(huán)載氣導(dǎo)致的熱損失大等缺點(diǎn)。但熱傳導(dǎo)干燥器內(nèi)部較多的運(yùn)動部件將導(dǎo)致系統(tǒng)的維修費(fèi)用很高。
(3)干料返混工藝是目前許多干燥工藝常用的操作單元,可以避免干化過程污泥粘壁、干燥效率低等問題,同時(shí)可改善初始進(jìn)料濕污泥含水率變化的敏感性,但干料返混單元導(dǎo)致的系統(tǒng)熱損失能耗較大。
(4)污泥干燥是一個(gè)能量凈支出的過程,干燥工藝的能量消耗高低是衡量一種干燥工藝優(yōu)劣的關(guān)鍵因素,而整個(gè)干燥系統(tǒng)的安全性則是干燥工藝的首要控制條件。
(5)目前干燥工藝技術(shù)均引自化工行業(yè)的熱干燥技術(shù),而污泥與晶體物質(zhì)的干燥特性有較大的差異,因此需對污泥的熱干燥特性、污泥干燥過程的形態(tài)變化、干燥過程的有機(jī)物反應(yīng)機(jī)理等加以深入研究,以期為適合污泥干燥的設(shè)備開發(fā)和研究提供必要的理論基礎(chǔ)。