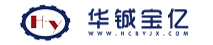
含油污泥主要包含石油石化行業(yè)的煉化“三泥”,即煉油廠廢水處理過程中產(chǎn)生的隔油池底泥、溶氣浮選浮渣及剩余活性污泥;煤制油、煤制氣、煤制烯烴等煤化工行業(yè)產(chǎn)生的生化污泥、氣化廢水預(yù)處理污泥等;制藥行業(yè)等其他化工行業(yè)污水處理過程中產(chǎn)生的含油或有機溶劑的污泥。
含油污泥含有大量的苯系物、酚類、重金屬、氮磷等營養(yǎng)物及致病菌和病原菌等,《 危險廢物名錄》明確將其列為危險廢物,外委有資質(zhì)的危廢處理中心進行處置,處理費用高。污泥的終端處置方式包括填埋、焚燒、土地利用、建材利用等,但污泥脫水后含水率為75%~90%,必須通過干化深度脫水才能將含水率降低至可再利用的水平(40%~50%)。
含油污泥干基熱值高,干化過程中易產(chǎn)生可揮發(fā)性有機氣體,易發(fā)生安全事故。且含油污泥較一般污泥更為粘黏,附著力強,容易粘結(jié)在傳熱壁上影響傳熱效果甚至引起抱軸卡料等機械故障,所以研究和開發(fā)安全可靠的污泥干化技術(shù)十分必要。
1 真空圓盤污泥干化系統(tǒng)工藝流程
真空圓盤干化系統(tǒng)由熱源供給系統(tǒng)、密封進料系統(tǒng)、真空圓盤干化機、密封出料系統(tǒng)、尾氣處理系統(tǒng)等子系統(tǒng)組成。工藝流程如下:
濕污泥料倉具有短期暫存功能,同時保證污泥干化機的連續(xù)進料。上游脫水污泥經(jīng)管道或污泥運輸車運送至料倉,緩存,運行時污泥經(jīng)過大口徑螺桿泵對干化機勻速給料,且螺桿泵能在一定程度上保證整個系統(tǒng)的密閉性。進料速度通過變頻控制。
主機經(jīng)蒸汽加熱后,通過間接傳熱的方式對污泥進行干化,通過變頻控制污泥在主機的停留時間,污泥干化后,通過旋轉(zhuǎn)卸料閥排出,閉鎖干化機出料時空氣的吸入,保證系統(tǒng)密閉性。
干污泥先經(jīng)過水冷出料螺旋降溫后,再經(jīng)斗提機輸送至干污泥料倉。
尾氣處理系統(tǒng)通過“2級除塵+2級冷凝”降低尾氣的含塵、含濕、有機揮發(fā)分的含量。尾氣被高壓風(fēng)機抽出干化倉體后,在恒溫旋風(fēng)分離器實現(xiàn)降塵過程。氣體溫度不變,防止水氣凝結(jié)造成除塵內(nèi)部的粘結(jié)。旋風(fēng)分離器底部通過旋轉(zhuǎn)卸料閥出灰,保證密閉。之后尾氣從噴淋塔底部進入,通過填料層和噴淋區(qū)實現(xiàn)快速降溫,去除尾氣中絕大部分粉塵、揮發(fā)性油分和少部分蒸汽。冷凝器將尾氣迅速冷卻到45℃以下,尾氣中的絕大部分水汽、有機氣體被冷凝凝結(jié),冷凝液經(jīng)泵送至噴淋塔水箱,作為噴淋塔補水,避免噴淋塔底部積泥,摒棄外部補水從而降低外排污水量。
2 干化過程中“三廢”排放情況
廢水:污泥中水分經(jīng)過液相-氣相-冷凝相”的轉(zhuǎn)變,完成從污泥向污水的轉(zhuǎn)移,真空圓盤干化系統(tǒng)的污水排放量等同于污泥蒸發(fā)水量,沒有新增污水排放。
廢氣:經(jīng)過除塵-噴淋-冷凝-除霧之后的不凝氣體,需要經(jīng)過生物除臭或焚燒才能排放。由于本系統(tǒng)采用全密閉形式,采用相對潔凈的尾氣作為循環(huán)載氣且循環(huán)比例大于50%,尾氣排放量大大減少,污泥蒸發(fā)水量1t,尾氣排放少于500m3。
廢渣:干化后的污泥含水率30%~40%,外觀為直徑3~5mm顆粒狀,便于運輸和后續(xù)處置。
3 安全分析和控制措施
3.1 安全分析
含油污泥熱干化過程中可能存在的安全隱患主要如下:
(1)濕污泥儲存過程中會釋放甲烷、硫化氫等有毒有害氣體。
(2)污泥干化過程中有粉塵爆炸的危險。
(3)含油污泥干化過程中易產(chǎn)生可揮發(fā)性有機氣體,濃度達到一定閾值后,有閃爆的危險。
(4)隨著含水率的降低,污泥熱值逐漸升高,干化過程中由于熱源高溫、機械摩擦、靜電等產(chǎn)生點火能量,可能會引起污泥燃燒。
(5)干污泥儲存過程中由于緩慢氧化等因素有悶燃的風(fēng)險。
(6)污泥熱干化一般選擇蒸汽作為熱源,具有較高溫度和壓力,有泄漏和燙傷員工的風(fēng)險。
(7)含油污泥更加粘黏,有卡料抱軸等機械故障的風(fēng)險。
因此污泥干化工程中安全控制措施設(shè)計是一項重要設(shè)計內(nèi)容。
3.2 安全控制措施
3.2.1 有毒有害氣體風(fēng)險控制
系統(tǒng)全密閉且整體供貨設(shè)備都較傳統(tǒng)設(shè)備做了加強處理,以確保系統(tǒng)有一定的真空度,避免空氣吸入確保系統(tǒng)內(nèi)低氧環(huán)境,同時避免干化過程中產(chǎn)生的有毒有害氣體逸散至車間。
進料:系統(tǒng)進料采用大口徑螺桿泵,螺桿泵擠壓進料,有效隔離進料端空氣的滲入。進料端主機連接處采用軟性墊片,加強了系統(tǒng)的密封效果。
主機:2根軸兩端伸出筒體部分采用“氮氣密封+填料密封”方式,盡可能降低軸承的泄漏。所有法蘭密封面均開密封槽嵌入硅橡膠密封條,自動控制引風(fēng)機的運行風(fēng)量,使引風(fēng)量稍大于蒸發(fā)水分所需的抽氣量,從而使干燥機始終處于微負壓狀態(tài),減少空氣泄漏量(負壓越小泄漏量越小)。倉蓋采用法蘭密封,連接處雙槽嵌硅橡膠。
出料:旋轉(zhuǎn)出料閥+出料螺旋。抽氣口是使料倉負壓大于干燥機內(nèi)負壓,保證空氣不進入干燥機,用旋轉(zhuǎn)出料閥來閉鎖干化機出料時空氣的吸入。
濕污泥料倉頂部配備臭氣風(fēng)機,將惡臭氣體抽送至生物除臭系統(tǒng)或臭氣焚燒系統(tǒng)。
3.2.2 粉塵爆炸風(fēng)險控制
污泥干化采用半干法,污泥含水率控制在30%~40%,避免運送干泥產(chǎn)生大量揚塵。
干化機通過變頻電機或減速機的調(diào)節(jié),轉(zhuǎn)速控制在3~6r/min,低速攪拌推送,干化機內(nèi)粉塵含量可控制在<15mg/Nm3,大大低于污泥粉塵爆炸下極限60g/Nm3。
同時干化機倉體內(nèi)大量水汽存在,亦降低了粉塵爆炸的風(fēng)險。
3.2.3 有機揮發(fā)分閃爆風(fēng)險控制
含油污泥中的部分油氣組分和揮發(fā)性有機成分在干化過程會揮發(fā)出來,濃度持續(xù)升高時,系統(tǒng)的危險系數(shù)快速增大。有效控制有機組分,是系統(tǒng)安全的重要保障。
系統(tǒng)高負壓:系統(tǒng)尾端設(shè)有壓力約為-14kPa的高壓離心風(fēng)機,經(jīng)過多級壓降后,干化倉體保持-2~-2.5kPa的高負壓程度,可以有效地將揮發(fā)分載出,避免濃度蓄積。
低氧載氣循環(huán):系統(tǒng)將降溫后的尾氣預(yù)熱后作為載氣,再次通入反應(yīng)倉體內(nèi)。預(yù)熱后的低氧載氣提高了氣流置換速度,防止有機物的蓄積。
3.2.4 干化機內(nèi)污泥燃燒風(fēng)險控制
燃燒三要素:可燃物、氧氣、點燃能量。含油污泥熱值較高,干化到一定程度后能夠自持燃燒,通過控制低氧、低溫避免污泥燃燒。
(1)氧含量控制系統(tǒng)。
分區(qū)域氧含量監(jiān)測:干化倉設(shè)有2組氧含量探頭,分區(qū)域檢測干化機內(nèi)部氧含量。
氧含量限制和氮氣保護連鎖:系統(tǒng)設(shè)置氧含量為2%(體積比),當(dāng)倉體內(nèi)部氧氣超過該限值時,系統(tǒng)打開氮氣連鎖裝置,將系統(tǒng)快速恢復(fù)低氧環(huán)境。
(2)溫度控制系統(tǒng)。
分區(qū)域溫度監(jiān)測溫度:干化選用150~170℃的飽和蒸汽作為熱源,既保證了系統(tǒng)的干化效果,同時保證了干污泥的熱值。主機干化區(qū)設(shè)有2組溫度探頭,分區(qū)域檢測系統(tǒng)的溫度,系統(tǒng)設(shè)定高于熱源溫度15%為極限溫度值。
(3)極限溫度值與噴淋系統(tǒng)連鎖
當(dāng)干化機內(nèi)部溫度超過設(shè)定極限限度時,主機停機、蒸汽停止,主機倉蓋配備噴淋水系統(tǒng)啟動,快速降溫。檢修時,可以手動打開噴淋系統(tǒng),進行倉體內(nèi)部清理。
3.2.5 干污泥悶燃風(fēng)險控制
干污泥悶燃主要是由于干泥初始溫度過高及緩慢氧化放熱導(dǎo)致。干污泥必須經(jīng)過水冷出料螺旋降溫后才能輸送至料倉儲存,且料倉設(shè)置溫度監(jiān)測及噴淋系統(tǒng),有效控制悶燃風(fēng)險。
3.2.6 蒸汽泄漏及燙傷風(fēng)險控制
熱源的安全性:蒸汽供給系統(tǒng)將高壓力熱源降低到0.5~0.6MPa(G)的安全壓力范圍內(nèi)。
倉體壓力限值與安全泄爆系統(tǒng):當(dāng)蒸汽泄漏、后端尾氣處理系統(tǒng)出現(xiàn)堵塞、風(fēng)機故障時,倉體積聚壓力,無法外泄。系統(tǒng)設(shè)有倉體正壓為0.01MPa(G),當(dāng)系統(tǒng)超過此壓力時,系統(tǒng)配備泄爆閥迅速開啟,實現(xiàn)安全泄壓。
3.2.7 機械故障風(fēng)險控制——差速推流技術(shù)
含油污泥較常規(guī)市政及其他行業(yè)化工污泥更為粘黏,極易在干化過程粘結(jié)在傳熱壁上。同時,高黏度造成污泥難以分散,增大了污泥在傳熱擴散過程的難度。為此采用差速推流技術(shù),提高污泥粘滯區(qū)的分散性,通過特殊設(shè)計降低對干化機的影響,降低卡料抱軸等機械故障的風(fēng)險。
污泥干化過程經(jīng)歷了預(yù)熱階段、恒速干燥階段、降速干燥階段。對應(yīng)污泥干化過程分為黏稠區(qū)、粘滯區(qū)、顆粒區(qū)。針對不同階段,物料表現(xiàn)出不同的特性。不同的特性需要不同的干化條件。
黏稠區(qū)(含水率>55%):黏稠區(qū)物料含水率較高,體積較大。黏稠段污泥溫度不斷提高,蒸發(fā)速度快速提升。針對本段污泥以攪拌、換熱為主。本階段輸送盤片設(shè)置刮刀以平刀和反推刀為主,提高破碎率,降低擴散難度,提高換熱效果。
粘滯區(qū)(含水率45%~55%):粘滯區(qū)污泥自由水、吸附水已基本蒸發(fā)殆盡,污泥中細胞體開始破裂,組織液滲出,污泥黏度不斷增大,傳熱效率下降,蒸發(fā)速率降低。針對本階段,主機以推流、分散為主。主機以推送刀為主,提高推送速度,提升污泥分散性,保障干化效果。
顆粒區(qū)(含水率<45%):本階段污泥以顆粒狀態(tài)出現(xiàn),分散性良好,但蒸發(fā)速度極低。為了保障出料的干化效果,本段以停留時間,將揮發(fā)性氣體揮發(fā)殆盡。本段主軸以平刀為主,提高停留時間和攪拌。設(shè)有擋料板,側(cè)邊溢流出料,保障干化效果。
4 干化機的工作原理及特點
4.1 干化機的工作原理
真空圓盤污泥干化系統(tǒng)采用雙軸圓盤主機。干化機為臥式結(jié)構(gòu)形式,設(shè)備內(nèi)部設(shè)置對向旋轉(zhuǎn)的2根空心軸,空心軸上密集排列著圓盤型葉片,蒸汽經(jīng)空心軸均勻流向盤片,加熱盤片。濕物料在圓盤的攪動下,與盤片熱表面充分接觸,污泥中水分完成擴散、蒸發(fā)過程,產(chǎn)生的水蒸氣聚集在干化機的穹頂,由載氣帶出干化機,從而達到干化目的。
4.2 干化機的特點
干化機具有以下特點:
(1)結(jié)構(gòu)緊湊,占地面積?。徊钏偻屏骷夹g(shù)能有效降低污泥空倉率,提高盤片熱面積利用率。
(2)運行過程負壓程度高,能夠降低水分蒸發(fā)臨界溫度,提高熱效率。
(3)圓盤之間的刮取距離0.5cm,能夠保證圓盤自凈,保障傳熱效果。
(4)重力分配更均勻,保障軸的應(yīng)力結(jié)構(gòu),減少軸的形變量。
5 工程應(yīng)用
真空圓盤污泥干化系統(tǒng)在多個含油污泥干化項目得到應(yīng)用,運行效果良好,差速推流技術(shù) 性及安全可靠性得到充分驗證。應(yīng)用案例見下表:
分類 | 編號 | 項目名稱 | 處理規(guī)模(t/d) | 污泥種類 | 項目時間 |
石油石化 | 1 | 中石油呼和浩特石化項目 | 15 | 含油污泥 | 2019年 |
2 | ?;瘓F福州危廢中心項目 | 60 | 含油污泥 | 2018年 | |
3 | ?;瘓F福海創(chuàng)石油化工項目 | 80 | 含油污泥 | 2018年 | |
4 | 中石化勝利油田東營危廢中心 | 50 | 含油污泥 | 2018年 | |
5 | 中石油大慶石化水氣廠 | 120 | 含油污泥 | 2016年 | |
6 | 中石化金陵石化總廠項目 | 25 | 含油污泥 | 2016年 | |
7 | 中石化金陵石化烷基苯廠項目 | 25 | 含油污泥 | 2015年 | |
煤化工 | 1 | 陜西神木富油能源項目 | 30 | 含油污泥 | 2018年 |
2 | 山西潞安180煤化工項目 | 120 | 含油污泥 | 2017年 | |
3 | 伊泰化工杭錦旗煤化工項目 | 60 | 含油污泥 | 2016年 |
6 結(jié)束語
(1)真空圓盤污泥干化系統(tǒng)安全性高,適用于含油污泥的干化處置。
(2)差速推流技術(shù)能夠有效解決含油污泥的粘黏問題。
(3)差速推流技術(shù)熱效率高,能耗低,廢水、廢氣排放量小,更節(jié)能環(huán)保。
(4)雙軸圓盤干化機結(jié)構(gòu)形式合理,穩(wěn)定耐用,使用壽命長。