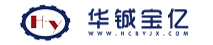
清潔生產(chǎn)是對產(chǎn)品和產(chǎn)品的生產(chǎn)過程、產(chǎn)品及服務采取預防污染的策略來減少污染物的產(chǎn)生,是將環(huán)保節(jié)能與工業(yè)生產(chǎn)進行有效結合,注重資源的循環(huán)利用,保證產(chǎn)品的清潔和工業(yè)生產(chǎn)過程的清潔,達到節(jié)能減排,保護環(huán)境的目的。
隨著現(xiàn)代機械加工制造業(yè)的高速發(fā)展,切削加工液(即去除加工)消耗量巨大,占到加工潤滑劑總消耗量的38%。然而切削液是現(xiàn)今機械加工制造業(yè)中主要的污染源,要從根本上解決污染問題,必須“預防為主”,將污染物消除在生產(chǎn)過程之中,實行工業(yè)生產(chǎn)全過程控制。必須采取有效凈化處理措施,才能提高生產(chǎn)效率和加工質(zhì)量,減小對操作人員健康及環(huán)境帶來負面的影響,以適應清潔生產(chǎn)的要求。國外發(fā)達 一直致力于清潔生產(chǎn)的工藝研究,以凈化再生水基切削液的新理念為基礎,研制出多種 的切削液凈化處理設備,采取相應的清潔生產(chǎn)凈化方案,已成功應用于金屬加工領域中,有助于企業(yè)實現(xiàn)清潔生產(chǎn)目標。
1 切削液污染的危害
在機械加工過程中,切削液發(fā)揮著良好的冷卻、潤滑、清洗和防銹等十分重要的作用,不僅可以優(yōu)化加工參數(shù)、降低廢品率,還能夠提高刀具切削能力、使用壽命和產(chǎn)品精度。但是切削液使用一段時間后,隨著金屬碎屑及粉末、微生物和繁殖物、油污等雜質(zhì)的不斷堆積,切削液潤滑和冷卻能力不斷下降,機床及刀具磨損加劇,導致加工精度降低,損壞供液系統(tǒng)閥和泵并堵塞設備,還會造成切削液黑臭變質(zhì)、惡化環(huán)境,刺激呼吸系統(tǒng)黏膜引起炎癥,使工人的呼吸道受到感染或產(chǎn)生皮炎,影響工人的身體健康。同時還會有很多導軌油、主軸油、液壓油等雜油泄漏混入切削液,使乳化液失去穩(wěn)定性,阻擋了乳化液和空氣的接觸,導致乳化液缺氧,使厭氧菌快速繁殖,加速乳化液的腐敗變質(zhì),造成切削液的分解和失效,使切削液的使用壽命縮短約65%~85%。通常企業(yè)會在切削液效率降低或者一出現(xiàn)管路堵塞時就將用過的切削產(chǎn)生的大量廢液置換掉并徹底清洗循環(huán)系統(tǒng),這樣不僅增加生產(chǎn)成本,也對環(huán)境造成污染,因此有必要通過對切削液污染源的分析,在生產(chǎn)過程中采取有效措施消除或減少污染。
2 切削液有效維護措施和凈化方法
隨著 對環(huán)境保護、三廢治理發(fā)展的要求,變質(zhì)后的切削液中含有 嚴禁直接排放的高危險廢棄物(HW09),且對廢水中的pH值、油脂、固體和金屬含量的排放都有嚴格限制,因此減排甚至不排放、循環(huán)使用應是企業(yè)遵循的發(fā)展方向。
根據(jù)使用經(jīng)驗,切削液中的乳化污油容納大量細菌且又是細菌的食物,當含量超過7%時,該切削液就不能繼續(xù)使用了。有相關研究發(fā)現(xiàn),將切削液中的固體顆粒污染物的粒徑從40μm降至10μm,可延長刀具使用壽命1~3倍。所以對切削液應當采取包括凈化、抑菌、維持合適的切削液和水的比例等有效維護措施。
凈化處理方法有:
(1)沉降法。在容器中放置一定時間,用撇油器撇除上部漂浮雜質(zhì),再去除底部顆粒雜質(zhì)。
(2)離心法。能同時去除密度大的固體顆粒和密度小的油類。
(3)過濾法。用濾紙或濾袋過濾其大顆粒的雜質(zhì)。
實踐表明,離心分離法是切削液較快速、經(jīng)濟和有效的凈化方法,能同時去除1~5μm微米級顆粒和冷卻液中的浮油,浮油回收率高,切削液壽命可延長6~8倍,甚至更長,經(jīng)過凈化后的切削液廢液排放和處理費用相應減少,更加符合環(huán)保要求。目前國內(nèi)外已有多款新型離心凈化處理設備成功地應用于金屬加工行業(yè)中。
3 離心分離技術在切削液凈化循環(huán)系統(tǒng)中的應用
3.1 離心分離工作原理
離心分離是在離心力場中進行非均勻物系的分離技術,具有高精度、良好的穩(wěn)定性和連續(xù)性,在許多工業(yè)生產(chǎn)過程中得到廣泛的應用。其工作原理是將帶固相細小顆粒和污油的切削液由污液管進入離心分離設備轉(zhuǎn)鼓內(nèi)部,并隨轉(zhuǎn)鼓一起高速旋轉(zhuǎn),靠高速旋轉(zhuǎn)而產(chǎn)生的離心力將固相細小顆粒甩向轉(zhuǎn)鼓,凈液由離心分離設備頂部排出。高速沉降離心機分離出的固體含濕量較低,一般情況下分離效率也較高。
離心力場包括離心力、分離因數(shù)、哥氏力以及離心液壓等。分離因數(shù)是離心機分離能力和性能的主要指標,數(shù)值愈大,物料受到的離心力愈大,分離效果也就越好。對于固體顆粒小、液相黏度大和難分離的懸浮液,要采用分離因數(shù)較大的離心設備。
3.2 新型離心分離設備的選用
根據(jù)處理不同類型物料要求,選用不同的離心分離方案。在金屬零件加工中的精磨,高速鋼、硬質(zhì)合金鋼、陶瓷等材料的刀具加工等場合,要同時去除切削液體中的微米級固體雜質(zhì)及浮油,則采用三相離心分離設備。被污染的液體被送入設備中進行凈化處理,可將1~5μm級的固體顆粒和雜油同時分離出來,凈化后的干凈液體被導回到冷卻液系統(tǒng)集液槽。這個操作可以在工作時間內(nèi)或停機以后完成,靈活方便,切削液不被破乳,保持其冷卻潤滑等作用。
4 切削液凈化循環(huán)使用系統(tǒng)中的清潔生產(chǎn)凈化方案
利用 的離心分離設備對切削液的凈化處理可以達到清潔生產(chǎn)的要求。一般單機凈化循環(huán)處理適用于機床數(shù)量不多或使用不同類型切削液的工況。對于采用濕式加工的大型機械加工廠,推薦采用集中凈化循環(huán)處理。在國外現(xiàn)代化生產(chǎn)車間里的自動化生產(chǎn)線上,切削液集中凈化處理系統(tǒng)被廣泛采用。
德國某過濾技術有限公司和瑞士某過濾設備有限公司都是在液體凈化技術領域的過濾凈化處理,已有數(shù)萬套設備和系統(tǒng)在很多領域得到成功應用。研究院曾與上述公司合作在國內(nèi)開展技術和產(chǎn)品推廣應用,根據(jù)液體的凈化量、所要求的純凈度、預計的固體量和場合進行配置,選擇可移動式的單機旁路處理、集中凈化旁路處理系統(tǒng)的液體凈化分離技術方案,取得了良好的效果。
4.1 可移動式單機旁路凈化處理方案
德國某公司生產(chǎn)的可以在旁路循環(huán)中運行的Clean-Boy移動式離心分離設備,結構緊湊,適用于不同場合的三相固液分離,加工企業(yè)可以根據(jù)各臺機床的切削液使用情況,在需要處理的機床邊外接旁路移動使用,靈活方便,可以極大地減少采購成本。
以某加工企業(yè)采用德國離心分離設備凈化處理后測試結果表明,取液體中含量90%、50%和10%被排除的顆粒的尺寸指標,原有系統(tǒng)只能去除切削液中含量10%的0.893μm,含量50%的4.477μm和含量90%的17.825μm的雜質(zhì)顆粒,而通過德國離心分離設備的凈化系統(tǒng)處理后,能夠?qū)⒑?0%的0.632μm,含量50%的1.958μm和含量90%的4.477μm的雜質(zhì)顆粒從液體中分離出去,保留在液體中的細微顆粒只占很小比例。這樣經(jīng)過凈化處理的切削液不僅達到很高的純凈度,同時排除污油,凈化后液體被回收到切削液系統(tǒng)中相應的凈液集液池再循環(huán)使用,分離出來的固體顆粒廢渣接近干燥狀態(tài),易于收集,可非常容易地定期采用人工卸除,這個過程只需要幾分鐘的時間,也可進行全自動卸料,極大程度杜絕切削液的浪費,達到清潔生產(chǎn)的要求。
4.2 集中旁路凈化處理系統(tǒng)方案
對于中等流量或大流量切削液的機械加工場合,可采用切削液集中旁路凈化處理方案,將加工車間的切削液進行集中供液、檢測、過濾、除油、增氧、殺菌,實現(xiàn)對其濃度、pH值和菌落數(shù)的控制。系統(tǒng)可以實現(xiàn)自動控制,運行維護方便。主要優(yōu)點有:
(1)集中系統(tǒng)可以減少切削液的總容量,集中對切削液進行除浮油、除雜質(zhì)、控溫,實現(xiàn)切削液長期使用的零排放目標。
(2)高精度的過濾效果可提高生產(chǎn)效率,改善工件表面加工質(zhì)量。
(3)降低生產(chǎn)成本、工人勞動強度、機床維護保養(yǎng)費用以及切削液消耗。
(4)減少中間環(huán)節(jié)和排屑裝置,實現(xiàn)對廢切削液的集中處理,減少對環(huán)境的污染。
(5)設備占地面積小,節(jié)省車間的使用面積,切削液處理中心也可以設置在離生產(chǎn)線較遠的地方,降低噪聲污染的影響。
德國某公司P220型全自動卸料離心分離機可用于多臺機械加工設備的冷卻液凈化系統(tǒng),根據(jù)不同流量需求對集液槽、泵、冷卻單元等進行配置和參數(shù)優(yōu)化選擇,單臺P220轉(zhuǎn)鼓轉(zhuǎn)速達到2450r/min,流量(與液體黏度有關)為250L/min,分離因數(shù)為1800g,容渣量為1.2×10-2m3,集液槽容積為15000L,在大流量需求的情況下,可以采用多臺組成集中系統(tǒng)。污液先從各加工機械集中到污液槽,然后再送到高速離心分離設備處理,系統(tǒng)可定期將1~5μm級的顆粒分離出來并實現(xiàn)自動卸料,經(jīng)過凈化處理的切削液再被送回供液槽,排出的油還能作為燃料出售。
瑞士某過濾設備有限公司的大型集中凈化系統(tǒng)為國內(nèi)外多家機床和刀具制造商用戶的不同需求提供了經(jīng)濟實用的解決方案。如MZF-T系列三相離心分離設備適用于各種類型的切削液和潤滑油,可以處理硬質(zhì)合金鋼、高速鋼、鋁合金及其他各種金屬材料等不同的過濾介質(zhì),能夠同時清除被污染的切削液中1~5μm級的固體顆粒和雜油。從加工機械產(chǎn)生的污液經(jīng)導向管自然由底部流入污液收集池,再用泵送給離心分離機進行固液分離,經(jīng)過離心分離機凈化處理的干凈液體利用自身壓力經(jīng)導向管流到凈液收集池,再由泵根據(jù)加工所需的流量和壓力要求送給加工機械使用。被分離出來的外來雜油利用壓力流動到集油箱,浮油被回收,乳濁液被重新送到離心機分離處理。被分離出來的金屬顆粒與粉末則附著在離心機轉(zhuǎn)鼓內(nèi)壁的卸料桶上,1~2天更換一次卸料桶即可,卸料只需3min,同時機床無需停機。
設備單機流量為250L/min,三相處理流量為5~15L/min,轉(zhuǎn)鼓轉(zhuǎn)速達到2880r/min,可以根據(jù)具體的流量要求組成集中供液與控制系統(tǒng),同時穩(wěn)定和連續(xù)不斷的過濾可以獲得高度純凈的切削液,還可以減少切削液的總容量,節(jié)省車間的使用面積。例如該公司為某刀具加工企業(yè)提供的由20臺T72組成的集中處理系統(tǒng),可為60多臺加工機床和加工中心提供2000L/min的切削液,集液池容量為20000L,每天24h連續(xù)正常運轉(zhuǎn),切削液無需更換,連續(xù)使用10年。集中供液凈化處理系統(tǒng)可以模塊化組裝,根據(jù)實際需要擴容及分期施工。特別在汽車動力總成的生產(chǎn)過程中,切削液的集中凈化處理系統(tǒng)被廣泛采用。
在特殊要求場合,在利用離心分離設備的同時,還可以采用濾芯作為附加的旁路凈化處理。離心分離和過濾相結合的旁路處理滿足更為嚴格的1~3μm的過濾精度要求。離心分離與過濾組合系統(tǒng)的優(yōu)點體現(xiàn)經(jīng)濟性和靈活性,可以實現(xiàn)更高精度要求,穩(wěn)定性和連續(xù)性好。
5 結語
在金屬加工過程中,切削液受到污染會降低冷卻和潤滑效果,影響工件表面加工質(zhì)量,增加刀具磨損以及大量廢液排放。為了達到清潔生產(chǎn)要求,在離心分離凈化技術應用于切削液的清潔生產(chǎn)的基礎上,采用新型離心分離設備對不同生產(chǎn)規(guī)模的切削液進行有效凈化循環(huán)使用的凈化工藝方案。生產(chǎn)實踐證明,上述凈化處理方案能夠清除1~5μm級以上的金屬碎屑及粉末顆粒、去除乳化污油、細菌的滋生也得到很好的抑制、延長切削液使用壽命和更換時間間隔,提高金屬加工精度和切削加工效率,還能有效地維護和延長刀具和切削液供應系統(tǒng)中泵、閥等機械零部件的使用壽命,減少能耗和切削液廢液排出量。采用切削液集中處理的凈化工藝大大地降低企業(yè)的生產(chǎn)綜合使用成本,改善工作環(huán)境,符合清潔生產(chǎn)和綠色生產(chǎn)要求,經(jīng)濟和社會效益顯著,具有廣泛的應用前景。