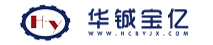
1 項目概述
現(xiàn)階段中韓石化煉油廠區(qū)的污泥處理系統(tǒng)僅采用污泥離心脫水工藝進行處理,脫水后污泥含水率高達84%左右,離心脫水后的污泥依舊具有流體化性質(zhì),污泥減量不夠充分,污泥后續(xù)處置難度和成本仍然較高,需要相當(dāng)高的后續(xù)處置費用,因此有必要進一步減量。
污泥種類中主要難處理的污泥為含油污泥,其一般組成方式為水包油(O/W)、油包水(W/O)以及由懸浮固體(SS)組成穩(wěn)定的懸浮乳狀液體系,脫水效果非常不好,污泥成分和物性均會受污水的水質(zhì)情況、處理方式、所加藥劑的種類等因素影響嚴(yán)重,差異性較大,處理成本高,且含油污泥含有許多PAHs、重金屬元素、揮發(fā)性物質(zhì)等有害物質(zhì),對環(huán)境還存在一定的放射性污染。由于含有污泥性質(zhì)特殊,降低含水率困難。含油污泥一般的處理工藝:焚燒法、生物去除法、溶劑萃取法、含油污泥調(diào)稠法、焦化法、含油污泥綜合利用法等。
本文主要闡述在原有系統(tǒng)的末端增設(shè)干化單元,對離心脫水后的三泥進一步干化,將污泥含水率從85%左右降低到40%以下,得到減量化處理,降低對環(huán)境的影響。本項目實施后,將含水率較高的含油污泥的含水率得到有效的降低,“三泥”外運量顯著減少,可以減少社會處理的壓力,提升煉油廠社會形象?,F(xiàn)在生產(chǎn)的基本要求要做到“三泥”減量化、無害化、資源化的處理,今后污泥處置的方法將會往污泥減量化、無害化、資源化處理技術(shù)發(fā)展,未來將逐步得到廣泛應(yīng)用。
2 污泥干化技術(shù)比選
現(xiàn)在污泥干化主流工藝基本采用間接熱干化工藝,主要有:槳葉干化工藝技術(shù)、射流干化工藝技術(shù)、薄層干化工藝技術(shù)、帶式干化工藝技術(shù)等。針對現(xiàn)有4種污泥干化工藝進行六個方面的對比,見下表所示:
序號 | 項目 | 槳葉干化工藝技術(shù) | 射流干化工藝技術(shù) | 薄層干化工藝技術(shù) | 帶式干化工藝技術(shù) |
1 | 能否干化油泥 | 能 | 不能 | 不能 | 不能 |
2 | 工藝的成熟性 | 成熟工藝,在污泥處理中廣泛應(yīng)用 | 新工藝,污泥處理中應(yīng)用少 | 成熟工藝,在污泥處理中廣泛應(yīng)用 | 老式工藝,在污泥處理中有所應(yīng)用 |
3 | 安全性評價 | 采用嚴(yán)格的防爆檢測及措施,高溫150~170℃干化 | 安全性高,一般采用低溫60℃左右干化 | 需采用嚴(yán)格的防爆檢測及措施,高溫150~170℃干化 | 需采用嚴(yán)格的防爆檢測及措施,高溫120~170℃干化 |
4 | 占地面積大小 | 一般 | 大(另需配套臭氣處理場地) | 較大 | 大(另需配套臭氣處理場地) |
5 | 運行費用多少 | 大約150~160元/噸 | 大約200~220元/噸 | 大約170~210元/噸 | 大約200~210元/噸 |
6 | 系統(tǒng)復(fù)雜性如何 | 工藝相對簡單,設(shè)備較少,運行操作簡單,維護量少 | 工藝相對簡單,設(shè)備較少,運行操作簡單,維護量少 | 設(shè)備較多,檢修維護工作量較大 | 設(shè)備較多,檢修維護工作量較大 |
綜上所述,根據(jù)四類干化工藝對比,本技術(shù)方案推薦使用槳葉干化工藝,其原理是先對油泥進行破乳除油后調(diào)理預(yù)處理,然后與活性生化污泥混合,濃縮后進行離心脫水,離心脫水后的污泥進入干燥機,采用蒸汽作為加熱源,蒸汽通過干燥機內(nèi)部的轉(zhuǎn)軸及楔形的空葉片,與其中污泥發(fā)生間接接觸對濕污泥進行一定的干燥,轉(zhuǎn)軸及楔形葉片可做到一邊加熱污泥,一邊將污泥往前推進,將干化過后的污泥從出口推出,實現(xiàn)整個污泥干化過程。本套工藝系統(tǒng)設(shè)備布置緊湊,占地面積較小。
3 污泥干化技術(shù)方案
3.1 工藝描述
本項目污泥采用“雙向自凈干化-尾氣治理一體化”污泥減量工藝。該干化單元主要配套相應(yīng)的污泥干燥機、干化進出料系統(tǒng)及相應(yīng)的尾氣處理系統(tǒng)。經(jīng)過離心脫水后油泥污泥含水率在85%左右,通過現(xiàn)場的污泥泵打入到可移動的儲泥槽,通過叉車定期運送到污泥干化現(xiàn)場(距離約500米)。油泥含量按一定配比定量地輸送至濕污泥料倉與生化污泥混合后,再通過進料螺旋輸送機送至雙向自凈干化機進料端,干化后污泥從干化機中排出,通過螺旋輸送機和斗式提升機輸送至干污泥料倉,干化后的污泥由干化料倉卸料閥控制,卸料至危廢公司專門的危廢運輸車。雙向自凈干化機以低壓蒸汽為加熱介質(zhì),將含水率小于85%的污泥在干化機葉片的不斷攪拌作用下與熱載體及熱表面得到相對充分的接觸,使內(nèi)部物料在升溫的過程中做到同時將表面水分進行蒸發(fā)。干化機內(nèi)的污泥在螺旋葉片的不斷往前推動下向污泥出料口的方向進行移動,在這個過程中污泥的水分沿軸線方向不斷蒸發(fā)至含水率小于30%,污泥重量達到縮減,真正實現(xiàn)污泥的減量。
污泥尾氣處理工藝主要是處理污泥在干化中蒸發(fā)出來的水分及分解或釋放的少量污染廢氣、微量的粉塵。利用尾氣引風(fēng)機的作用,以負壓形式,經(jīng)旋風(fēng)分離器將產(chǎn)生的粉塵去除,并通過噴淋塔做到降溫,并經(jīng)過活性炭預(yù)處理去除污染后,送入污水處理場原有的催化燃燒系統(tǒng)裝置。
3.2 雙向自凈干化系統(tǒng)
3.2.1 工藝簡介
干化機一般分為熱對流式和熱傳導(dǎo)式兩類。熱對流式即通過熱載體(如熱空氣)與被干燥的物料相互接觸并進行一定的干化;傳導(dǎo)式加熱過程中熱載體并不與被干燥的物料直接接觸,而是熱表面與物料之間相互接觸??紤]到現(xiàn)在石化企業(yè)所產(chǎn)生的污泥的復(fù)雜性,進料含水率較高,采用熱傳導(dǎo)(間接)加熱形式會更安全,效率也會更高。
雙向自凈干化系統(tǒng)為間接傳導(dǎo)加熱的方式,是一種在設(shè)備內(nèi)部設(shè)置攪拌自凈葉片,使?jié)裎锪显谌~片的攪動下,與熱載體充分進行接觸,從而達到干燥目的的低速攪拌干化機,結(jié)構(gòu)形式一般為臥式。干化機帶有刮刀的獨特葉片設(shè)計形式,能夠保證單位有效容積內(nèi)傳熱面積大,其中熱介質(zhì)可以采用低壓蒸汽作為熱源,更好地利用工業(yè)余熱,減少熱污染,降低整個項目的運行成本。雙向自凈干化機所用熱量均用來加熱內(nèi)部物料,熱量損失僅有的損失為通過器體保溫層和排濕向環(huán)境的散熱,說明熱量損失較少,節(jié)約能源。雙向自凈干化機圓盤葉片傳熱面具有自清潔功能,物料在設(shè)備整個腔體內(nèi)輸送的過程中,物料顆粒與葉片表面的相對運動會產(chǎn)生一定的分散力,具有清洗作用,能夠使附著于加熱斜面上的殘留污泥自動地清除,進而能夠保持葉片高效的傳熱功能,現(xiàn)場不需要人工清理,即可以達到內(nèi)部自凈的目的。這即為雙向自凈干化系統(tǒng)的優(yōu)越性。
3.2.2 工作原理
雙向自凈干化機是由帶有夾套的殼體、攪拌軸、機座以及一些傳動部分組成,污泥的整個干燥過程都在封閉狀態(tài)下進行,同時有機氣體及異味氣體在密閉條件下也送至尾氣處理裝置中,進而避免環(huán)境的污染。
本套干化機設(shè)備以蒸汽作為加熱能源,軸兩端裝有熱介質(zhì)導(dǎo)入和導(dǎo)出的旋轉(zhuǎn)接頭。加熱能源分為兩處,分別進入干化機殼體夾套中和葉片軸腔內(nèi),可將機器內(nèi)部全身和攪拌軸同時進行加熱,以傳導(dǎo)加熱的方式對泥料進行加熱干燥。被干燥的泥料由螺旋輸送機定量地連續(xù)送至干化機的加料口處,泥料進入到加料器后,通過葉片的不斷轉(zhuǎn)動使物料進行翻轉(zhuǎn)、攪拌,在這個過程中不斷更換加熱介面,讓器身和葉片充分接觸,做到充分加熱,使泥料所含的表面水分進行蒸發(fā)。同時,泥料隨攪拌軸的旋轉(zhuǎn)成螺旋軌跡向出料口方向進行輸送,在輸送過程中繼續(xù)攪拌,使污泥中滲出的水分不斷蒸發(fā)。干燥過后均勻的合格產(chǎn)品由出料口排出。
3.2.3 設(shè)備特點
本套設(shè)備采用的雙向自凈干化機存在一定的優(yōu)勢,具體如下面四點:
(1)設(shè)備整體結(jié)構(gòu)布置緊湊,占地面積小。由設(shè)備的整體結(jié)構(gòu)可知,干燥所需的熱量主要是由排列于空心軸上的葉片壁面所提供,此外夾套壁面也可提供部分傳熱量,所以單位體積設(shè)備的傳熱面大,可節(jié)省設(shè)備占地面積,減少基建投資。
(2)熱量利用率高。本設(shè)備雙向自凈干化機采用熱傳導(dǎo)的方式進行加熱,所有傳熱面均被泥料覆蓋,減少了一定熱量損失,熱量利用率可高達85%往上。設(shè)備內(nèi)部葉片為整體焊接,強度較好,葉片上的刮板可防止污泥粘結(jié)在葉片上,同時也能更好地破碎進料污泥,提高熱量的利用率。
(3)熱介質(zhì)可以采用低壓蒸汽作為熱源,對于石化企業(yè)能夠更好地利用工業(yè)余熱,減少熱污染,降低運行成本。
(4)設(shè)備葉片具有很好的自凈能力,這樣可提高葉片的傳熱能力。旋轉(zhuǎn)葉片的傾斜面與顆?;蚍勰拥穆?lián)合運動會產(chǎn)生一定分散力,使附著于加熱斜面的污泥自動地清除,保持葉片有著高效的傳熱能力。另外,由于兩軸葉片能夠反向旋轉(zhuǎn),交替分段進行壓縮和膨脹攪拌,傳熱能夠均勻,提高了傳熱效率。
因此,從上述特點中可以看出該套系統(tǒng)應(yīng)用于污泥干化的未來前景非常廣闊,具有很大的市場應(yīng)用潛力,是一種新型的、比較離心的污泥干化系統(tǒng)。
4 項目運行情況分析
4.1 干化后物料分析
含油污泥含水率在45%~70%之間時,屬于含油污泥的“黏滯區(qū)”,黏性較大,此時的油泥很容易黏壁,會造成干化效率低,這個含水率區(qū)間的油泥不利于進行干化處理。如果想要進一步降低含油污泥的含水率,將含水率控制在<35%時,干化后污泥的粉塵含量將得到一定提高,很容易發(fā)生爆炸。當(dāng)濕污泥含水率在35%~45%之間時,污泥黏性就開始逐漸降低了,水分起到凝塑的作用,污泥會呈現(xiàn)顆粒狀,即易于運輸,且熱值也較高,此區(qū)間很適合在工程中應(yīng)用。
經(jīng)過現(xiàn)場摸索,含油污泥含量與生化污泥含量配比值在1:5的情況下,出泥含水率較好。
2020年7月~10月期間,污泥干化設(shè)施混合污泥樣進出口泥樣數(shù)據(jù)如下表所示:
序號 | 油泥含量 | 進泥含水率 | 出泥含水率 | 減量化 |
1 | 20 | 86.4 | 35.4 | 78.95 |
2 | 85.3 | 34.3 | 77.63 | |
3 | 86.5 | 33.2 | 79.79 | |
4 | 86.7 | 35.4 | 79.41 |
經(jīng)過數(shù)據(jù)整理分析可得出:進口平均含水率為86.22%,出口平均含水率為34.58%,實現(xiàn)了污泥79%減量化目標(biāo),基本滿足了污泥干化后含水率要求,且干化后污泥便于后續(xù)運輸、存儲,同時可以考慮進CFB鍋爐摻燒。
4.2 廢氣治理情況分析
本項目中,廢氣治理的流程主要包括旋風(fēng)分離器、噴淋塔、活性炭吸附罐、催化燃燒裝置,由于干化過程中會形成少量的粉塵顆粒,在尾氣治理系統(tǒng)中增設(shè)旋風(fēng)分離器,可去除粉塵顆粒。其中在干化過程中產(chǎn)生的有機揮發(fā)氣體及異味在密閉氛圍中先通過洗滌吸收塔進行初步洗滌吸收,再經(jīng)過活性炭吸附裝置,進入催化燃燒裝置焚燒去除,經(jīng)過以上流程,基本可去除尾氣中的揮發(fā)性有機物(VOCs)和易揮發(fā)含氮、含硫惡臭有機污染物,尾氣排放達標(biāo)。
4.3 運行成本分析
該項目污泥脫水-干化項目按干化機實際處理量0.7t/h(平均含水率85%),每天運行24小時,污泥含水率≤35%進行成本核算。依據(jù)設(shè)計方案計算,本項目實際運行負荷約為71kW,功率因子取0.8,綜合電價暫取為0.6元/度。根據(jù)該項目的實際特點,蒸汽(0.6MPa· G)的使用以130元/噸計算,每小時消耗蒸汽量為1.5噸,根據(jù)項目經(jīng)驗,中水用量為10m3/h,水費按1.0元/噸計算,得出每噸污泥處理成本約341.55元。
5 存在問題及后續(xù)思路
(1)鑒于生化污泥目前正在開展鑒定工作,待鑒定為一般固廢后,可考慮后續(xù)將生化污泥干化后送入乙烯CFB鍋爐進行摻燒。煤粉鍋爐污泥摻燒技術(shù)是現(xiàn)有主流處理技術(shù),該技術(shù)工藝是先將污泥進行干化,干化后的污泥輸送至爐前,與煤進行混合進入制粉的系統(tǒng),再進入鍋爐內(nèi)燃燒,混燒比例控制在5%以內(nèi),摻燒少量的污泥,不會影響鍋爐環(huán)保指標(biāo)。
(2)目前污泥干化尾氣進催化燃燒裝置,但目前催化燃燒裝置處理量已處于高負荷,會影響其它系統(tǒng)的廢氣抽吸。生物法是處理污泥干化廢氣中惡臭氣體的常見的處置方法,使用菌液生物處理法對惡臭氣體進行吸收,效果可好于水噴淋吸收法。目前二污生化池的尾氣采用的是生物滴濾法,故后續(xù)計劃將干化后尾氣經(jīng)活性炭吸附后送入生物滴濾系統(tǒng)。
(3)考慮到項目運行成本問題,污泥干化設(shè)施進料口等區(qū)域未施行全封閉,故該干化設(shè)施無法干化油含量較高的含油污泥。現(xiàn)將含油污泥與生化污泥按照一定比例混合后干化,可提升含油污泥干化量。