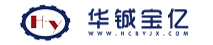
煉油廠產生的含油污泥(如浮渣、油泥等)中含有的苯系物、酚類、蒽、芘等物質有惡臭味和毒性,如不認真處理,將產生污染。但含油污泥的性質特殊,其脫水和處理技術難度大,成本高,一直是困擾我國煉油行業(yè)的環(huán)保難題。近年來,由于我國環(huán)保法規(guī)的逐步完善和企業(yè)技術進步的要求,含油污泥的污染治理技術已日益引起人們的關注和重視。
國外對含油污泥處理的環(huán)保要求已有較為完善的法規(guī)。如1990年1月,美國環(huán)保局在資源保護和回收法令以及危險和固體廢物修正案的基礎上對煉油廠含油污泥溶氣浮選除油工藝所產生的浮渣、API隔油池污泥等5種特殊廢渣(代號K049-K052,稱為“K廢物”),規(guī)定了特殊要求:在蒽、苯、苯并芘等19種化學組分低于極限含量前提下,不準堆積在排渣場;并提出了較佳的示范可用技術的處理標準。嚴格的法規(guī)迫使煉油廠改進或淘汰傳統(tǒng)的含油污泥處理工藝,故從90年代初以來,發(fā)達 的含油污泥處理技術得到了很快發(fā)展。
1 機械脫水技術
經重力沉降脫水后的含油污泥是黑色粘稠狀液體(含水率一般小于96%),稱為污泥濃縮液,其年產生量往往達萬噸以上,必須進行機械脫水減容。污泥脫水前,需進行調質。
1.1 污泥的調質
污泥脫水過程實際上是污泥的懸浮粒子群和水的相對運動,而污泥的調質則是通過一定手段調整固體粒子群的性狀和排列狀態(tài),使之適合不同脫水條件的預處理操作。污泥調質能顯著改善脫水效果,提高機械脫水性能。
由于含油污泥粘度高、過濾比阻大,多數(shù)污泥粒子屬“油性固體”(如瀝青質、膠質和石蠟等),質軟。隨著脫水的進行,濾餅粒子變形,進一步增加了比阻。而且在過濾過程中,這些變形粒子極易粘附在濾料上,堵塞濾孔;在離心脫水時,還因其粘度大、乳化嚴重,固-固-液粒子間粘附力強和密度差小等原因導致分離效果差。
Jonathan Zall等人曾分別研究過一般市政污水處理廠的污泥和含油污泥的過濾脫水性能。他們測定了含油3%、含總懸浮固體4%的含油污泥(浮渣)和含總懸浮固體1%~2%的一般污泥的比阻和可壓縮性系數(shù),證實含油污泥與一般污泥相比,其比阻大40倍,其可壓縮性系數(shù)大20倍。
用投加絮凝劑的化學調節(jié)法,就能使一般污泥中的懸浮微粒凝聚并順利進行脫水。但對于含油污泥來說,還必須加上破乳劑和加熱等其它強化手段。
含油污泥調質方法的選擇:一是根據(jù)其性質和特點;二要適應所用脫水機械的性能;三要考慮其脫水泥餅如何處理或利用。
Bruno Sander認為,含油污泥調質應分為兩個步驟,首先以適當方式投加飛灰、煤粉等固體粉末調節(jié)劑,并混合均勻;其次再投加有機絮凝劑,這樣才能順利進行含油污泥的脫水。
用硅藻土、石灰和飛灰等微細粉末作為調節(jié)劑,可使易變形的含油污泥粒子形成有剛性的污泥骨架,使泥餅呈毛細結構。從而提供更多的微細水流通道。此外,這些固體粉末調節(jié)劑還能增加污泥粒子和水相的密度差,有利于機械脫水。
為減少固體粉末調節(jié)劑的投加量,Fluch H W等人提出了可采用濾餅部分回流到含油污泥調節(jié)段的工藝。
要通過調質-機械脫水使含油污泥實現(xiàn)油-水-固(無機固體)的三相分離,關鍵是使其中粘度大的吸附油解吸和破乳。為促使油從固體粒子表面分離,Surendra K Mishra認為加入合適的電解質可增加系統(tǒng)的電荷密度,使它們取代油組分優(yōu)先吸附在粒子表面,并使粒子更分散,為油從固體顆粒表面脫附創(chuàng)造更好的條件。Jan Bock,Sanjay R Srivatsa,Aldo Cotri等人分別發(fā)明了通過含油污泥調質-機械脫水工藝回收油的有關專利技術:通過投加表面活性劑、稀釋劑(葵烷等)、電解質(NaCl溶液),或破乳劑(陰離子或非離子)、潤濕劑(可增加固體微粒表面和水的親合力)和pH值調節(jié)劑等,并輔以加熱減粘(較佳為50℃以上)等調質手段,實現(xiàn)水-油-固三相分離。
調質方法的選擇應在測試含油污泥性質的基礎上進行。Aldo Corti建議,在含油量大于10%時,宜用親水性表面活性劑;含油量小于4%時,則宜用親油性表面活性劑。在用前者時,分離后水和固體在下層,而油在上層;用后者時,下層為含油固體,而上層為水(水層中均含有可溶性油和微乳化油)。
美國煉油廠含油污泥的機械脫油脫水費用約為每噸泥餅(泥餅含水50%)USD200,其中相當部分為調質費用。
1.2 機械脫水
要使含油污泥的機械脫水效果好,還應按具體情況和要求選擇污泥脫水機械和設計脫水系統(tǒng),包括污泥物料性質的測試、脫水機械及其參數(shù)的選擇等。目前國外應用較廣的脫水機械還是帶式壓濾機和臥式螺旋沉降式離心機。
Bruno Sander報道的用上述兩步調質技術(投加飛灰100kg/m3,4% FeCl3溶液33 L/m3,絮凝劑100~150 ug/g)在帶式壓濾機上對含油污泥的脫水除油工藝是將機內分重力區(qū)、楔區(qū)和壓力區(qū)3個區(qū)域。調質污泥送入后,先在重力區(qū)脫除大部分水;接著在楔區(qū)與FeCl3溶液混合,以提高絮體的抗壓能力;然后進入壓力區(qū),脫除約80%的油。其脫水效果是:含油污泥含固體12%,油20%和水68%;濾后液體中含固體1.5%,油13.7%和水84.8%;濾餅中含固體45.8%,油11.7%和水42.7%。
如采用Nelco化學公司的專利技術調質(加4000μg/g破乳劑,1000μg/g絮凝劑),用帶式壓濾機對含油17.1%,水79.7%和固體2.6%的污泥進行脫水時,油回收率為13.6%。
臥式螺旋沉降式離心機具有設備緊湊、占地面積小、調節(jié)劑耗量少和處理效率高等優(yōu)點,已得到越來越廣泛的應用。要獲得較好的分離效果和水質好的離心液(懸浮物濃度低),則在對含油低的污泥脫水時,應使泥中的少量油進入泥餅,即離心因數(shù)應小,一般取1000;反之,要求泥餅含油盡量低時,離心因數(shù)宜大,一般取2500~2700;此外,還必須注意離心機的離心因數(shù)、泥餅層厚度和污泥停留時間的平衡和調節(jié)。
目前,Alfa-laval公司和Flottweg公司等廠商開發(fā)了用可調葉輪工藝的三相臥式螺旋沉降式離心機,該機械可根據(jù)不同水油密度差進行調節(jié)。Flottweg三相離心機分別在德國OMW公司的煉油廠和武漢鋼鐵公司能源總廠用于油泥脫水,兩者效果的比較見下表:
項目 | 煉油廠 | 鋼廠 |
脫水前含油污泥 | ||
固(%) | 10.0 | 40.0 |
水(%) | 40.0 | 45.0~48.0 |
油(%) | 50.0 | 11.0~13.0 |
脫水后三相組成 | ||
泥餅相 | ||
固(%) | 36.0 | 80.0~85.0 |
水(%) | 54.0 | 14.0~16.0 |
油(%) | 10.0 | 0~3.0 |
污水相 | ||
固(%) | 1.0 | 0.3~0.4 |
水(%) | 97.0 | 99.5 |
油(%) | 2.0 | 0.05~1.00 |
油相 | ||
固(%) | 0.5 | 0.88~1.20 |
水(%) | 4.5 | 1.2~1.3 |
油(%) | 95.0 | 97.5~97.9 |
由上表可見,鋼廠含油污泥的三相離心分離效果明顯優(yōu)于煉油廠含油污泥,這是由于前者的固相主要由無機物鐵和氧化鐵組成,它和液相的密度差大;而后者在三相離心分離后還需用碟片式離心機再次分離油相,且污水水質差,需進一步處理才能送污水處理系統(tǒng)。
2 脫水泥餅的處理
含油污泥機械脫水所得泥餅中仍含一定量的油和其它有機物,需進一步脫油及無害化處理,主要手段有熱處理和生物處理等。
2.1 熱處理和熱解吸技術
熱處理或熱解吸技術是90年代初國外迅速發(fā)展并獲得應用的工藝。主要有Heuer等開發(fā)的包含低溫(107~204℃)-高溫(357~510℃)加熱蒸發(fā)-冷凝步驟的含油污泥處理工藝(已在歐洲多個 申請了專利),Krebs,Geory等人利用鍋爐排放熱廢氣干燥含油泥餅的專利技術以及Term Tech熱解吸工藝。該熱解吸工藝是在一個裝有密鋼葉片轉子的反應器中,把污泥從299℃加熱至399℃,并通入蒸汽,使烴類在復雜的水合和裂化反應中分離,并冷凝回收。這些工藝都能從泥餅中回收油,并使泥渣達到直接填埋的要求。在路易斯安那煉油廠投運的熱解吸裝置,把含水50%的“K廢物”用鋼帶輸送到一密閉的溫度分布為121~954℃的干燥裝置內。年處理泥餅1400t,可回收300t油和120t可燃氣。
Richard J Ayen等人1992年報道的“低溫熱處理”工藝,是通過一密閉的溫度為250~450℃的旋轉加熱器把“K廢物”中的有機物和水蒸發(fā)出來,并用氮氣作為載氣送至蒸發(fā)物處理系統(tǒng),殘留物作燃料用。其處理效果見下表:
項目 | 進料 | 處理后泥渣 |
熱值(kJ/g) | 16.72 | 22.28 |
油類的質量含量(%) | 34 | 30 |
固含率(%) | 41 | 68.4 |
水的質量含量(%) | 25 | 1.6 |
該工藝能使“K廢物”處理后達到BDAT標準,已商業(yè)化應用。
熱處理或熱解吸工藝費用為每噸泥餅USD500~800。因該工藝顯著減少了泥餅體積,故節(jié)約了大部分運輸和填埋費用(后者為USD183/t)。據(jù)Patricia Broussard-Welther報道,路易斯安那煉油廠1993年使用脫水-熱解吸-泥餅填埋工藝處理含油污泥的總費用為1990年前全部采用脫水-泥餅填埋法的109.5%,但只有1991年使用脫水-泥餅摻混作燃料工藝總費用的61.5%。
2.2 生物處理技術
自1992年美國Gulf Coasts煉油廠建成污泥生物處理示范裝置以來,生物處理裝置已商業(yè)化并廣泛應用。
Ramin Abrishamian等報道,如進料中的碳環(huán)化合物、芳烴和油的濃度控制在合適范圍內,則生物處理的運行成本比焚燒處理費用低40%;只要在生物反應器內保持合適的pH值、足夠的溶解氧和營養(yǎng)鹽濃度以及良好的混合狀態(tài),絕大多數(shù)有機物都能被降解,而逸出的少量有機物也容易用活性炭吸收。
Valero煉油廠1995年建成了設計能力為2.0kt/a的污泥生物處理裝置。含水50%的泥餅被輸送到一臺生物反應罐中。罐內通入氧或空氣,同時進行機械攪拌,并不斷加入氨和磷酸等營養(yǎng)物,以促進好氧微生物的生長,使其轉化為CO2和H2O。處理后的殘液進入罐中濃縮,在加入石灰后(旨在穩(wěn)定鎳),再次進入離心機脫水,泥餅能直接填埋。該技術處理效果好,作業(yè)安全(因是常溫常壓),經濟合理,處理每噸泥餅的運行費為USD189,總成本為USD624。接近或低于熱處理或熱解吸工藝的總成本USD500~800。并且在提高氧利用率、降低藥品消耗和改進泥餅脫油效果等方面仍有降低成本的潛力。
2.3 溶劑萃取技術
溶劑萃取工藝中的超臨界流體萃取技術,是去除含油污泥中的油和其它有機物的有效手段。超臨界流體溶劑有丙烷、三乙胺、重整油和臨界液態(tài)CO2等。為了降低成本,Paspek C開發(fā)了溶劑萃取-氧化處理含油污泥的專利技術: 步萃取采用粘度低、碳原子少(較佳為2~4)的如丙烯、環(huán)丙烷、丁烷等輕質烴為溶劑;萃取后殘留泥中仍含一些聚合芳烴等有機物,需用相對分子質量較高的烴進行第二步萃取,而該專利技術則用濕法氧化工藝代替。氧化劑用空氣、氧氣和硝酸鹽等(HNO3較佳),污泥中保持一定水分,以促進氧化反應。在溫度200~375℃、壓力0.1MPa的條件下,經一段時間后,有機物被氧化為CO2和H20,殘渣可符合直接填埋的要求。
3 含油污泥的資源化
在無機固體含量低,煉油工藝條件和產品質量許可等情況下,把含油污泥直接作為資源是可行的。
3.1 回收輕質油及瀝青
Kuriakose A P等1994年報道,Cochin煉油公司處理含水25%,無機物5%和烴類70%的原油罐底泥,在回收17%的輕質油后,把剩余物在催化劑AlCl3的作用下加熱處理,使瀝青軟化點上升,滲透率下降。并通過調節(jié)溫度和AlCl3催化劑的比例,生產了不同等級的瀝青。
3.2 污泥浮渣作為催化裂化裝置分餾塔的油漿
美國Navajo公司把浮渣注入FCC裝置作為分餾塔的急冷油漿,使浮渣大部分轉化為燃料油。由于其注入比例很低,對催化裂化過程沒有影響。Mobil公司Solomon M開發(fā)了把含油污泥作為FCC裝置原料的技術。該技術把含水量高的污泥首 行機械脫水,再對脫水后粘稠的泥餅加熱,并投加非離子表面活性劑等乳化劑,使水包油型乳化油轉化為油包水型,因而易與其它原料油充分混合,流動性好?;旌衔锪陷斎隖CC裝置反應器,經裂化反應生成汽油。
3.3 作焦化裝置原料
90年代起,國外許多煉油廠就采用Mobil油泥焦化工藝來處理API隔油池油泥:用冷焦水與污泥調合后,作為驟冷介質在清焦前對熱焦炭進行冷卻,污泥中的水作為冷焦水或切焦水回用,烴類則循環(huán)回裝置。該技術涉及到焦化裝置的改造,比較復雜。
Scaltech公司開發(fā)的技術較好地解決了焦化塔注入污泥所帶來的可能堵塞焦孔、產生熱點而延緩冷焦過程使操作波動等問題。其核心是使用專門設計的Guinard Dc 6離心分離器,并加破乳劑,從平均組成為含油15%,水80%和固體5%的含油污泥中分離出清潔油以及不含油和固體的水供循環(huán)回用,而剩下的是清潔的固體微粒(粒徑從28μm降到4μm)和水的濃漿液(其量相當于原污泥的一半),用來代替部分冷焦水。該工藝的不利之處是:無機固體的增加使焦炭難以達到電極焦質量標準;泵、混合器和罐因處理污泥而受到磨損,導致維修費用增加。如美國阿瑟港煉油廠在1992年8月前用Mobil技術處理平均含固體2.5%的污泥,此后的5個月內采用Scaltech技術處理平均固體10%~12%的污泥,注入量由8月以前的2.1%(泥和焦炭之比)增加到5.8%,焦炭的灰分含量由0.5%上升到0.86%。
Godino,Rino L等人開發(fā)了把濕含油污泥直接輸送到焦化裝置上部急冷罐來處理污泥的工藝,在此罐內污泥和從焦炭塔出來的熱油混合?;旌衔镆徊糠炙腿虢固克D化成焦炭,其余循環(huán)。進入裝置的含油污泥先用分餾塔等的低溫位熱能預熱,再利用循環(huán)的其余混合物進一步加熱和干燥。蒸發(fā)的水分可作為冷焦水或切焦水。該工藝優(yōu)點是投資少,不足之處是污泥注入量有限,當其水含量高時,處理總量很少。
4 建議
我國對含油污泥等廢渣處理的法規(guī)尚有待完善,在處理技術上也和發(fā)達 有差距。在充分吸收國外技術的基礎上,結合國情開發(fā)含油污泥脫水和處理的適用技術是當務之急。
4.1 重視含油污水機械脫水
含油污泥的機械脫水是污泥處理技術的關鍵,只有實現(xiàn)“水清、泥干、油純”的三相分離,才能顯著減少后處理費用。污水處理過程實際上是污染物的相轉移,如脫水后的污水相水質差,會影響污水處理系統(tǒng)的正常運行,甚至發(fā)生惡性循環(huán)。而預處理乳化油、固體和COD濃度高的離心液或濾后液既難處理,處理費用又高。因此,把好機械脫水關和改善污水相水質是較好的選擇。
提高固體回收率和減少泥餅含水率對降低含油污泥處理總成本意義更大,如泥餅含水從85%降至50%時,體積可減至前者的30%,可大大節(jié)約運輸及后處理費用。
4.2 重視含油污泥調質技術
要把好含油污泥機械脫水關,僅僅靠 設備是不行的,國內已有此類教訓。必須根據(jù)含油污泥的性質,研究開發(fā)相應的調質技術,如武漢鋼鐵公司用進口三相離心機所取得的分離效果,是在自行開發(fā)熱軋含油污泥調質技術(投加適當?shù)谋砻婊钚詣⒓訜岬揭欢囟炔⒃谝欢ǖ臄嚢杷俣认绿幚硪欢〞r間)的前提下取得的。因此,應重視煉油廠含油污泥調質技術的研究,除篩選合適的絮凝劑外,還需大力開發(fā)固體粉末調理劑、破乳劑、表面活性劑和固體增濕劑等產品和相應的調質技術。
4.3 開發(fā)經濟合理的適用處理技術
從含油污泥處理經濟成本考慮,應優(yōu)先考慮在煉油工藝上消化利用含油污泥的可能性,使之資源化,并進行清潔生成審計,把廢物的削減及治理與總體生產工藝結合起來。如美國路易斯安那煉油廠建立的煉油廠廢物管理系統(tǒng),就是從整體上考慮能量的平衡和充分利用,從而降低了污泥熱處理的成本。
此外,應注重因地制宜地開發(fā)適用技術。如生物處理工藝具有管理方便(可建在污水處理廠內 管理)、設施簡單可靠、運行安全和處理費用較低等優(yōu)點,應予以關注,組織研究和開發(fā)。
4.4 發(fā)展含油污泥處理專業(yè)化服務產業(yè)
國外煉油廠的含油污泥處理作業(yè),有許多是由專業(yè)承包商來完成的,由于含油污泥是煉油工藝及其污水處理終端的產物,其收集、脫水、運輸和處理不僅操作難度大、技術含量高,還具有臨時性和批量性的特點,如原油罐底油泥的清出、收集和處理利用等;此外,從規(guī)模效益考慮,發(fā)展含油污泥處理的專業(yè)化服務產業(yè)是大有可為的。這不僅指開發(fā)新產品和新設備,還包括如調質技術開發(fā)等技術服務,可有效地防止含油污泥的二次污染,減少處理成本。