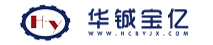
1 前言
氧化鋁是近年來國內(nèi)外研究較為廣泛的一種無機分離膜材料。它的出現(xiàn)與迅速應(yīng)用,一方面是由于膜分離過程在高溫、腐蝕性環(huán)境的實際需要;另一方面是由于近年來發(fā)展起來一些新的陶瓷膜材料制備工藝,使得晶粒細(xì)小、孔徑均勻、質(zhì)量可靠陶瓷膜的制備成為可能。目前已商品化的多孔陶瓷膜的構(gòu)形主要有平板、管式和多通道3種。多通道陶瓷微濾膜由于其較高的通量、優(yōu)異的機械性能和良好的截流能力,已日益顯示出其極強的競爭力。
面向應(yīng)用體系的陶瓷膜過程設(shè)計主要包括膜微觀結(jié)構(gòu)、膜材料性質(zhì)、過程操作參數(shù)的優(yōu)化設(shè)計。無機陶瓷膜的分離性能與其結(jié)構(gòu)、材料性質(zhì)是密切相關(guān)的。多孔陶瓷膜的結(jié)構(gòu)參數(shù)主要包括平均孔徑和孔徑分布、膜厚度、孔隙率、孔形狀、曲折因子等決定了膜的滲透分離性能;膜材料性質(zhì)包括膜的化學(xué)穩(wěn)定性、熱穩(wěn)定性、表面性質(zhì)及機械強度等,它們不僅影響膜的滲透分離性能,更與膜的使用壽命密切相關(guān);操作參數(shù)主要包括膜面流速、操作壓力、溫度等,影響膜過程的濃差極化和膜污染程度,對滲透通量和分離性能都有影響。無機陶瓷膜經(jīng)過多年的發(fā)展,加上本身具有耐高溫高壓、耐腐蝕、耐有機溶劑等優(yōu)點,并且膜通量高、清洗方便、使用壽命長,在眾多領(lǐng)域獲得了廣泛的應(yīng)用,成為膜領(lǐng)域發(fā)展較為迅速、也是較有發(fā)展前景的品種之一。
2 陶瓷分離膜制備方法
無機陶瓷膜的主要制備技術(shù)有:采用溶膠-凝膠法制備超濾膜;采用化學(xué)氣相沉積技術(shù)制備微孔膜或致密膜;采用陽極氧化制備陶瓷分離膜和固態(tài)粒子燒結(jié)法及假凝膠法制備膜載體及微濾膜。
2.1 溶膠-凝膠法
以金屬醇鹽及其化合物為原料,在一定介質(zhì)和催化劑存在的條件下,進行水解-縮聚反應(yīng),使溶液由溶膠變成凝膠,再經(jīng)干燥、熱處理而得到合成材料的方法稱為溶膠-凝膠法。目前,該方法已成為陶瓷分離膜的主要制備方法,它不僅操作方便、設(shè)備簡單,更重要的是孔徑分布狹窄(0.001~0.1μm),孔徑大小可通過調(diào)節(jié)溶膠和熱處理過程來控制,分離效率高。
2.2 化學(xué)氣相沉積技術(shù)
化學(xué)氣相沉積技術(shù)(CVD)已在半導(dǎo)體集成電路的制造等領(lǐng)域得到廣泛的應(yīng)用,它也同樣適用于氧化鋁分離膜的制備,其特點是可以控制改變微孔膜的孔徑。CVD法制備氧化鋁分離膜,需要載體孔徑3~10nm以上,反應(yīng)應(yīng)在高溫下進行,反應(yīng)物先吸附在載體表面或微孔內(nèi),再發(fā)生表面反應(yīng),即其機理為吸附-表面反應(yīng)。
2.3 陽極氧化法
微孔氧化鋁分離膜的研制,先前多以陽極氧化法,近十多年來這種工藝得到了不斷完善,其制備方法是以高純度金屬箔為陽極,在酸性電解質(zhì)溶液中進行陽極氧化。陽極氧化法制備的膜包含兩個區(qū)域,一個是大面積的微孔層,另一個是屏障層。屏障層是毗連的,實際起著支撐作用,陽極氧化法制備的膜呈很規(guī)則的直徑,孔徑均勻,形成六角形微孔網(wǎng)絡(luò)。
2.4 固態(tài)粒子燒結(jié)法
燒結(jié)法是選擇氧化鋁為原料,添加適量助溶劑、粘合劑、增塑劑等,經(jīng)成形在一定溫度下燒結(jié)而成。燒結(jié)過程中,粉末顆粒間相互接觸部分被燒結(jié)在一起,粉末顆粒間相互接觸部分被燒結(jié)在一起,粉末間的空隙形成相互貫通的微孔,孔徑范圍為0.1~600μm,適應(yīng)于微孔過濾,所以該法被用來制備多層復(fù)合膜中的大孔陶瓷支撐體及中間層。陳艷林等以淀粉作造孔劑,利用普通陶瓷原料為主,適當(dāng)添加高溫粘結(jié)劑,用燒結(jié)法制備出氣孔率較大,氣孔分布均勻、抗壓強度較大的多孔陶瓷。
2.5 假凝膠法
假凝膠法是將溶膠和一定量的微細(xì)粉配制成穩(wěn)定的懸浮液,將懸浮液涂覆在一定孔徑的載體上而制備無機分離膜的方法,該方法適用于制備微濾膜,適宜在醫(yī)藥、食品、純水制備等領(lǐng)域中應(yīng)用。李月明等利用Al(NO3)3為前驅(qū)體,以氨水水解制備勃姆石溶膠,在溶膠中添加一定量PVA溶液和不同粒徑的微粉末制備出Al2O3假溶膠,采用浸漬法涂膜,在一定溫度下燒成制備出孔徑分布均勻,無缺陷的微濾膜。
3 陶瓷分離膜的過濾機理
陶瓷分離膜的過濾機理包括靜態(tài)過濾和動態(tài)過濾。
3.1 靜態(tài)過濾
靜態(tài)過濾或稱“死端”過濾,是一種傳統(tǒng)過濾方式。對陶瓷膜來說,其過濾是集吸附、表面過濾和深層過濾結(jié)合。對液-固、氣-固系統(tǒng)的過濾與分離來講,其過濾機理主要是慣性沖撞、擴散和截留。
3.2 動態(tài)膜過濾
動態(tài)膜過濾又稱十字流過濾。十字流過濾的原理是使原料液從很高的流速平行流過膜表面,以限制溶質(zhì)向膜面的沉聚;同時還有助于強化膜面已沉積的溶質(zhì)向主體流擴散,從而有效地削弱濃差極化,實現(xiàn)高速連續(xù)過濾操作。
3.2.1 反滲透
反滲透亦稱逆滲透(RO)。是用一定的壓力使溶液中的溶劑通過反滲透膜(或稱半透膜)分離出來。因為它和自然滲透的方向相反,故稱反滲透,根據(jù)各種物料的不同滲透壓,就可以使大于滲透壓的反滲透法達(dá)到分離、提取、純化和濃縮的目的。
3.2.2 超濾
超濾的作用原理為濾膜的篩除作用,即在一定壓力作用下,超濾膜的孔隙能通過溶液及由溶液帶走的小于濾膜孔隙尺寸的溶質(zhì)(如無機鹽類),而截留大于孔隙尺寸的溶質(zhì)(如有機物膠體等)。超濾膜主要應(yīng)用于液體中的顆粒物、膠體和大分子與溶劑等小分子物質(zhì)的分離,如溶液中細(xì)菌、熱源、病毒以及膠體蛋白質(zhì)、大分子有機物,分別實現(xiàn)凈化分離和濃縮的功能。
3.2.3 納濾
納濾(NF)膜早期稱為松散反滲透(Loose RO)膜。納濾膜介于反滲透與超濾膜之間,NF膜主要去除直徑為納米級的溶質(zhì)粒子,截留分子量為100~1000,幾乎對所有的溶質(zhì)都有很高的脫除率,其操作壓力一般小于1.5MPa。
3.2.4 微濾
微濾與超濾和反滲透膜技術(shù)相比,微濾的過濾速率要高2~4個數(shù)量級,特別是進料的懸液已不再是超濾和反滲透的單相流體,一般都是固液兩相流體。
4 陶瓷分離膜的應(yīng)用研究
4.1 膜的微觀結(jié)構(gòu)對滲透通量的影響
4.1.1 膜孔徑的影響
膜孔徑是影響通量和載體截留率等分離性能的主要因素,一般說來,孔徑越小,對粒子或溶質(zhì)的截留率越高而相應(yīng)的通量往往越低。
4.1.2 膜厚度的影響
膜厚度對膜性能的影響主要表現(xiàn)在滲透通量上,由于膜厚度的增加必然使流體通過的路程增加,因此過濾阻力增加,通量下降。
4.1.3 膜孔隙率的影響
孔隙率高的膜具有較多的開孔結(jié)構(gòu),所以在相同的孔徑下具有高的滲透通量。一般來說,多孔無機膜特別是陶瓷膜,其膜層的孔隙率在20%~60%之間,支撐體孔隙率高于分離層,對微濾膜而言,孔隙率大于30%。
4.2 膜材料性質(zhì)的研究
膜材料的親水性和膜表面荷電性對實際體系的分離性能有很大影響,膜表面性能的電化學(xué)性質(zhì)會對膜和流體之間的作用本質(zhì)和大小產(chǎn)生影響,從而影響溶質(zhì)和溶劑(或大分子顆粒)通過膜的滲透通量。通常表征膜表面電化學(xué)性質(zhì)是膜的ξ電勢和等電點,也有用表面電荷和零電荷點等來表征。
4.3 溶液性質(zhì)對膜過程的影響
溶液性質(zhì)是指液粘度、pH、離子強度、電解質(zhì)成分等。這些性質(zhì)直接影響到與之接觸的膜的表面性質(zhì),同時溶液性質(zhì)的變化還會改變其中所含的待分離的顆粒或大分子溶質(zhì)的性質(zhì),造成膜與溶劑、與顆粒溶質(zhì)等之間的作用發(fā)生變化,從而影響到膜的分離性能。一般認(rèn)為,pH及離子強度的變化會改變體系性能如膠體。
4.4 操作參數(shù)對膜分離過程的影響
操作條件的優(yōu)化是膜應(yīng)用過程研究的另一個重要方面。不同操作條件下(過膜壓差、膜面流速和溫度等)對膜分離性能的影響很顯著。相同的膜裝置在優(yōu)化的操作參屬下工作,能提高膜的擬穩(wěn)定通量(在膜過濾過程中,當(dāng)通量不再衰減時,此時膜過濾處于擬穩(wěn)定態(tài),該階段對應(yīng)的通量即為擬穩(wěn)定通量),減少膜面積,降低能耗,節(jié)約工業(yè)生產(chǎn)成本,因此,確定一套合適的操作參數(shù)是決定膜過濾過程的一個主要方面。所有膜過濾過程都應(yīng)該工作在較優(yōu)操作條件下,操作條件的滲透通量臨界值為研究者所關(guān)注。
4.4.1 操作壓差對膜分離過程的影響
在微濾過程中,一般隨著操作壓力的升高,膜通量開始上升較快,當(dāng)壓力超過一定值后,膜通量隨壓力的變化趨于平緩,對有些體系膜通量甚至隨壓力的升高下降。這是由于操作壓差升高雖然增加了過濾推動力,但同時也增加了污染的可能性。黃江麗等在利用陶瓷膜微濾技術(shù)濃縮草漿黑液的研究中發(fā)現(xiàn),開始膜通量隨壓力變化較大,但當(dāng)壓力大于0.2MPa后,膜通量隨壓力的變化不大。
金珊等在陶瓷微濾膜濾除骨架鎳催化劑微粒的研究中發(fā)現(xiàn),在溫度為58℃、膜面流速4.6m/s的條件下,測得壓差在小于0.25MPa范圍內(nèi),隨著過濾壓差的增大,膜通量隨著增大。在大于0.25MPa的壓差下,隨著過濾壓差增大,膜通量的變化趨于平緩。曾堅賢等在陶瓷膜處理肌苷發(fā)液的研究中發(fā)現(xiàn),當(dāng)壓差低于0.1MPa時,膜的擬穩(wěn)定通量隨壓差的增大而增大,并達(dá)到極大值。超過0.1MPa后,膜的擬穩(wěn)定通量隨壓差的增大而逐步下降。鐘璟等在陶瓷膜處理煉油廠“三泥”水相的研究中發(fā)現(xiàn)壓力是膜過濾時的傳質(zhì)推動力,也是影響膜過濾的重要因素之一。壓差≤0.135MPa時,膜的初始通量和擬穩(wěn)定通量隨壓力升高而增加;壓差>0.135MPa時,初始通量和擬穩(wěn)定通量隨壓力升高變化很小。
Wang等人在作軋鋼廢水中試驗發(fā)現(xiàn),過膜壓差增大到0.2MPa時,滲透通量逐漸增大;超過0.2MPa時,滲透通量有變小的趨勢,過膜壓差對于這種乳化油體系存在臨界值。Zhao等人在用陶瓷膜處理鈦白廢水體系時也發(fā)現(xiàn)這種現(xiàn)象,操作壓差在0.2MPa出現(xiàn)極大值,膜面流速在3.0m/s也有這種極大值。隋賢棟等在硅藻土梯度陶瓷微濾膜的飲用水凈化中發(fā)現(xiàn),在0.05MPa水壓下,膜通量為1.31m3/(m2·h),隨著水壓的增加,通量逐漸增大,在0.3MPa水壓下,膜通量達(dá)到6.59m3/(m2·h)。
4.4.2 操作溫度對膜分離過程的影響
一般情況下,溫度的升高,會使溶液粘度下降,懸浮顆粒的溶解度增加,傳質(zhì)擴散系數(shù)增大,可以促進膜表面溶質(zhì)向主體運動,減薄了濃差極化層,從而提高過濾速度,增加膜通量。稀溶液過濾時,通量隨溫度的變化可由粘度與溫度的關(guān)系來預(yù)測。趙宜江等在對陶瓷膜精制菜油的工藝研究中發(fā)現(xiàn),當(dāng)膜厚為0.2μm,錯流速度5m/s,操作壓力0.1MPa,粘土用量10%時,脫色率的變化與單純吸附的變化規(guī)律基本一致,在90℃以下,溫度升高,脫色率增加,這主要是溫度升高,植物油粘度降低,更有利于有色物質(zhì)向粘土表面的傳質(zhì)作用;當(dāng)進一步升高溫度后,脫色率反而下降,這是因為溫度過高,已吸附的有色物質(zhì)發(fā)生脫附現(xiàn)象又回到油中,同時高溫下油中有些物質(zhì)加酚類的氧化作用增強,也會使油的色澤有所加深。對于稀溶液的過濾,Cheryan等實驗發(fā)現(xiàn),當(dāng)溫度從303K升高到318K時,使?jié)B透通量提高了一倍,Bhave等在油水分離中發(fā)現(xiàn),當(dāng)溫度從293K上升至323K時,膜通量增加了兩倍。當(dāng)過濾過程屬濃差極化控制,溫度對膜通量的影響將取決于液相傳質(zhì)系數(shù)和粘度之間的關(guān)系是非線性的。
Deschampes在催化劑回收中發(fā)現(xiàn)溫度升高,通量升高比預(yù)計的還要高,認(rèn)為溫度升高使大分子物質(zhì)形成的動態(tài)膜減薄所致。溫度對膜通量及肌苷的降解都有著較重要的影響,因此溫度的優(yōu)化即要能較大提高膜通量,又要盡量避免肌苷的降解。曾堅賢等在用陶瓷膜處理肌苷發(fā)酵液的研究中,分別在40,50,60,70,80,90℃下,測定溫度對膜通量的影響,考慮運行成本及肌苷的收率等因素,適宜的操作溫度為70℃。黃江麗等用陶瓷膜微濾技術(shù)濃縮草漿黑液時發(fā)現(xiàn),在實驗壓差為0.2MPa的條件下,溫度較低時,隨著溫度升高,膜通量加大;當(dāng)溫度接近50℃以后,膜通量變化緩慢;當(dāng)溫度大于58℃后,膜通量下降。金珊等在用陶瓷微濾膜濾除骨架鎳催化劑微粒時發(fā)現(xiàn),當(dāng)料液濃度為1.5%、膜面流速為4.6m/s、操作壓差為0.20MPa時,溫度對膜通量的影響顯著,通量與溫度基本呈直線上升關(guān)系。徐南平等對陶瓷膜在鈦硅分子篩固液分離過程中的應(yīng)用研究中發(fā)現(xiàn),鈦硅分子篩水溶液所謂粘度明顯受溫度影響,23℃時物料粘度為1.9mPa·s,溫度升高到80℃時粘度降為1mPa·s,因此溫度升高將有利于提高膜的滲透通量。
4.4.3 膜面流速對膜分離過程的影響
在陶瓷膜過濾體的應(yīng)用中,膜面流速是影響膜滲透通量的重要因素之一。理論上講,提高膜面流速將有利于減輕濃差極化和減少膜表面的沉積的影響。一般的文獻認(rèn)為膜面速度越大,膜通量越高,但是膜面速度的提高意味著能耗的提高,膜的操作壓力高等弊端,同時對有些體系,膜面流速的增加還會造成滲透通量的下降,對實驗體系為顆粒體系,錯流速度增大對膜通量的影響有兩方面。一方面帶走膜表面的顆粒使沉積層減薄而使膜通量增大,另一方面是首先帶走了粗顆粒,使表面沉積層上細(xì)顆粒比例增高、比阻增大而使膜通量見效,因此研究膜面速度對過濾性能的影響很有必要。
鐘璟等在陶瓷膜處理煉油廠“三泥”水相的研究中發(fā)現(xiàn)流速小于1.17m/s時,流速對通量的影響較為顯著,當(dāng)流速高于1.17m/s后,隨流速的增大,通量增大的幅度降低,通過計算不同流速所對應(yīng)的雷諾數(shù)Re證實了這一點。流速從0.58m/s變化到1.17m/s的過程中,流型是從過渡區(qū)發(fā)展到湍流區(qū),因此流速對膜通量的影響明顯;而流速大于1.17m/s后,流動進入湍流區(qū),無流型的變化,所以流速對通量的影響減小。金珊等在用陶瓷微濾膜濾除骨架鎳催化劑微粒時發(fā)現(xiàn),在溫度45℃,操作壓力為0.15MPa條件下,膜面流速選在2.0m/s以下比較適宜。曾堅賢等在陶瓷膜處理肌苷發(fā)液的研究中發(fā)現(xiàn)當(dāng)膜面流速超過3.25m/s時,膜的擬穩(wěn)定通量已達(dá)到極大值,超過該流速,擬穩(wěn)定通量保持不變,因此,選用3.25m/s的膜面流速,有利于提高膜通量和節(jié)省耗能。黨亞固等在陶瓷膜過濾洗毛廢水回收羊毛脂的研究中發(fā)現(xiàn),在流速很低時,隨著輪流速的增加,濾液通量也增加,在4m/s時達(dá)到極大值,以后隨錯流速度的增加,濾液通量反而減小。
5 展望
膜材料與高效分離技術(shù)是當(dāng)代新型高效分離技術(shù),是多學(xué)科交叉的產(chǎn)物,亦是化學(xué)工程學(xué)科發(fā)展的新增長點。與傳統(tǒng)的分離技術(shù)比較,它具有高效、低能耗、過程簡單、操作方便、不污染環(huán)境、便于放大、便于與其它技術(shù)集成等突出優(yōu)點。它適合于現(xiàn)代工業(yè)對節(jié)能、低品位原材料再利用和消除環(huán)境污染的需要。在近幾十多年來獲得了極其迅速的發(fā)展,已廣泛而有效地應(yīng)用于石油化工、制藥、生化、環(huán)境、能源、電子、冶金、輕工、食品、航天、海運、人民生活等領(lǐng)域,形成了獨立新興的技術(shù)產(chǎn)業(yè)。特別是在中藥領(lǐng)域的應(yīng)用,隨著我國加入WTO,我國的制藥工業(yè)正面臨著全面的挑戰(zhàn),根據(jù)聯(lián)合國 衛(wèi)生組織的要求,符合現(xiàn)代化、國際化的中成藥優(yōu)良品種的標(biāo)準(zhǔn)是“安全、有效、穩(wěn)定、均一、經(jīng)濟”,而其技術(shù)開發(fā)關(guān)鍵仍是獲取與中醫(yī)復(fù)方的作用機理相吻合的“藥效物質(zhì)基礎(chǔ)”。因此現(xiàn)代陶瓷膜分離技術(shù)被國際上認(rèn)為是21世紀(jì)較有發(fā)展前途的一項重大高新技術(shù)。
然而陶瓷膜分離技術(shù)畢竟是一門年輕的發(fā)展中的綜合性學(xué)科,正處于發(fā)展和上升階段,無論是理論上還是應(yīng)用上都有許多工作要做,如:
(1)材料的脆性。
(2)缺乏完整材料的大規(guī)模生產(chǎn)系統(tǒng)。
(3)缺乏對材料的孔徑大小、形狀分布等的 控制方法。
(4)缺乏將孔結(jié)構(gòu)與力學(xué)性能相聯(lián)系的有效模型。
(5)膜通量提高。
(6)膜污染及其清除。
(7)對某些成分的吸附。
綜合以上分析可知,陶瓷膜的制備方法有待于進一步的完善,它的分離機理還需要進一步的研究,尤其是膜材料的傳質(zhì)結(jié)構(gòu)模型的研究,同時還要達(dá)到按應(yīng)用過程進行材料設(shè)計與過程優(yōu)化的目的。