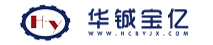
二次采油(水驅(qū)采油)是目前油田廣泛采用的開采方法,原油經(jīng)脫水分離后的采油廢水含油量、固體懸浮物濃度(SS)較高,直接排放會造成嚴(yán)重的水體污染。將采出水進(jìn)行處理后再回注地層,滿足了環(huán)境保護(hù)的客觀要求,同時大大減少了對水資源的浪費。目前對采油廢水的處理方法主要為水力旋流、重力分離及氣浮等物理方法,這些方法處理后的水質(zhì)已經(jīng)不能達(dá)到低滲透率地層回注的需要。為了能夠?qū)崿F(xiàn)更高的處理效果,膜分離技術(shù)被引入到石油開采廢水處理中。徐俊等采用聚偏氟乙烯超濾膜對大慶油田含油廢水進(jìn)行處理,結(jié)果表明,膜濾出水的油和懸浮物質(zhì)均小于1.0mg/L,去除率可達(dá)95%,濁度低于1.0NTU,去除率達(dá)90%以上。潘振江等采用聚醚砜中空纖維超濾膜組件處理油田采出水,探討超濾用于油田回注水處理和采出水回用預(yù)處理效果。傳統(tǒng)的有機膜易于堵塞,膜污染后難于清洗,其耐高溫、抗酸堿腐蝕性較差,并且壽命較短。無機陶瓷膜的主要成分為三氧化二鋁,較有機膜具有更好的熱力學(xué)穩(wěn)定性、機械強度、抗腐蝕性。丁慧等采用管狀無機陶瓷膜過濾技術(shù)處理油田采出水,分析不同操作參數(shù)對處理效果的影響。Mehrdad Ebrahimi等研究了經(jīng)過裝有不同陶瓷膜組件(膜通量不同的各種陶瓷微濾、超濾和納濾膜)的脫水槽后,油田采出水的出水情況。
本研究利用陶瓷平板膜實現(xiàn)對采油廢水中油和固體懸浮物的高效去除,并對膜污染及清洗方法進(jìn)行研究,旨在為陶瓷平板膜在油田回注水中的應(yīng)用提供理論依據(jù)。
1 實驗
1.1 實驗水質(zhì)
實驗裝置安裝在沈陽采油廠某聯(lián)合站內(nèi)。直接利用生產(chǎn)中的原水進(jìn)行實驗,以保證各種參數(shù)與實際污水保持一致。該廠回注水處理原始方案采用脫水、除油、浮選、粗濾、精濾5個步驟達(dá)到預(yù)期處理效果。本實驗主要研究利用陶瓷平板膜對浮選前(方案一)及浮選后(方案二)含油廢水的處理效果。
根據(jù)實驗的需要,原水分別取自浮選機前和浮選機后的取樣口。原水的水質(zhì)指標(biāo)見下表:
取樣口 | p(油)/(mg/L) | p(SS)/(mg/L) | pH | t/℃ |
浮選機前 | 15~35 | 30~60 | 7.2~8.0 | 47~50 |
浮選機后 | 5~20 | 10~40 | 7.2~8.0 | 47~50 |
A1級注水水質(zhì)指標(biāo) | <5 | <1 | - | - |
1.2 陶瓷平板膜參數(shù)
實驗所用陶瓷膜是由日本明電舍公司提供的板狀無機膜。在陶瓷平板膜的內(nèi)部設(shè)有集水豎管,膜兩端設(shè)有集水橫管。一端的集水橫管口與抽吸泵相連,在泵的抽吸作用下,原水從膜兩側(cè)的表面進(jìn)入,其中的懸浮物、油等雜質(zhì)被截留下來。處理水經(jīng)集水豎管在集水橫管匯合,被泵抽出。陶瓷平板膜各參數(shù)見下表:
參數(shù) | 內(nèi)容 |
過濾方式 | 抽吸方式 |
材質(zhì) | 陶瓷部分:主要分三氧化二鋁 集水部分:高分子聚乙烯 |
膜的種類 | 精密過濾膜(MF膜) |
膜孔徑 | 公稱孔徑0.1μm |
粒子捕捉性能 | 0.1μm粒子捕捉率95%以上 |
初期純水透過流速 | 100kPa、25℃時,1670LMH(40m3/㎡·d) |
單片有效膜面積 | 0.04㎡ |
陶瓷部分的強度 | 破壞強度200~300N |
1.3 實驗裝置及流程
處理水量為0.6~1.8L/h,在主反應(yīng)槽內(nèi)安裝膜片,利用空壓機在主反應(yīng)槽底部進(jìn)行曝氣。原水進(jìn)入主反應(yīng)槽,經(jīng)過陶瓷平板膜過濾后進(jìn)入處理水箱,反洗泵從處理水箱抽水定時對膜片進(jìn)行反洗,實驗裝置保持間歇運行,每抽吸11min反沖洗1min。在處理水箱和主反應(yīng)槽上設(shè)有取樣口,定時監(jiān)測反應(yīng)槽中濃縮液和出水的水質(zhì)。
1.4 水質(zhì)分析方法及儀器
主要檢測水質(zhì)指標(biāo)及分析方法均按照 標(biāo)準(zhǔn)分析方法:油,紫外分光光度法;SS,抽濾-烘干稱量法;pH,鉑勒SX823便攜式pH計;溫度,泰州奧特XMTA-7411K智能型溫控儀。
2 結(jié)果與討論
2.1 運行條件的確定
陶瓷膜運行一段時間后,采油廢水中的油滴、懸浮顆粒等雜質(zhì)會吸附或沉積在膜表面或膜孔內(nèi),使得膜孔徑變小甚至堵塞,此時的跨膜壓差趨于增大??缒翰钭鳛槟み^濾過程的推動力,對其膜通量起決定性作用。因此,通過測定陶瓷膜的跨膜壓差確定較佳的反應(yīng)條件。確定較佳反應(yīng)條件過程中,選用的原水均為浮選機前的管道水,運行周期為每正常運行11min后反沖洗1min,反沖洗水量為進(jìn)水流量的2倍。
2.1.1 曝氣量
在膜通量為15L/(㎡·h)時,曝氣量分別為0,0.5和1L/min的情況下,隨著曝氣量的增加,跨膜壓差的變化幅度越來越小。曝氣向陶瓷膜表面提供不穩(wěn)定流的形式,增強主反應(yīng)槽內(nèi)液體的流動性,氣流和水流的沖刷作用減輕了陶瓷膜表面油及懸浮物等污染物的聚集,減緩了陶瓷膜表面的污染情況。因此,本實驗采用曝氣的方式,較佳曝氣量為1L/min,氣水比為4:1。
2.1.2 膜通量
膜通量表示的是陶瓷膜在過濾采油廢水時的滲透能力,膜通量越大代表單位時間內(nèi)所處理的水量越大,但膜污染的速率也隨之增大。因此,本實驗需在保證陶瓷平板膜裝置穩(wěn)定運行的前提下,確定較佳膜通量,使其達(dá)到較大的處理效能。
本實驗選取膜通量分別為15,22.5,30,45L/(㎡·h),曝氣量為1L/min。當(dāng)膜通量為15和22.5L/(㎡·h)時,陶瓷膜裝置的跨膜壓差變化較小,此時陶瓷膜表面雖有油及懸浮物等污染物粘結(jié),在反沖洗作用下,膜的表面得到了一定程度的恢復(fù),從而保證了實驗裝置的正常運行。但膜通量為15L/(㎡·h)時,處理水量較小,無法充分發(fā)揮陶瓷平板膜的過濾性能;30L/(㎡·h)的膜通量超出了本實驗所用陶瓷平板膜的承載力,在其超負(fù)荷運行的情況下,膜污染迅速,污染物大量積聚在膜表面,堵塞了膜表面的孔洞,此時反沖洗作用難以滿足膜表面恢復(fù)的要求,實驗裝置無法正常運行。因此,本實驗較佳的膜通量為22.5L/(㎡·h)。
2.1.3 溫度
本實驗所取原水溫度為47~50℃,在輸送到實驗裝置的過程中,由于熱量的散失,水溫會下降到室溫??紤]到生產(chǎn)的實際情況,通過主反應(yīng)槽的加熱棒及溫控儀進(jìn)行溫度的控制,使其在20~50℃變動。實驗分別在20,30,40,50℃下進(jìn)行,觀察跨膜壓差的變化,選取較佳反應(yīng)溫度。隨著溫度的增加,跨膜壓差變化幅度逐漸減低。這主要是由于在不同溫度下,采油廢水的粘度和擴散系數(shù)不同。隨著溫度的升高,采油廢水的粘度下降,擴散系數(shù)增大,降低了過濾過程中的傳質(zhì)阻力,從而減小了濃差極化的影響,減緩了膜表面的污染速度,使得實驗裝置能夠更為穩(wěn)定地運行。采油廠原水溫度為47~50℃,因此在50℃的反應(yīng)溫度時,既保證了跨膜壓差穩(wěn)定及膜污染速度的降低,又無需再對原水進(jìn)行加熱,避免產(chǎn)生不必要的消耗。
2.2 陶瓷膜的污染和清洗
采用酸性溶液對污染現(xiàn)象較重的膜片進(jìn)行清洗。為了確定清洗的效果,利用蒸餾水測定了陶瓷平板膜清洗前后膜通量的恢復(fù)率。結(jié)果表明:污染膜片在0.05mol/L的HCl或HNO3溶液中浸泡12h后,過濾性能恢復(fù)較好,膜通量的恢復(fù)率均在96%以上,其中經(jīng)0.05mol/L的HNO3溶液浸泡12h后的膜片,膜通量恢復(fù)率達(dá)97.2%。
2.3 陶瓷膜運行穩(wěn)定性
實驗分別在裝置A、B中進(jìn)行,裝置A為浮選前水樣,裝置B為浮選后水樣,投加藥劑為FeCl3+PAM,FeCl3投加量為20mg/L,PAM投加量為1.5mg/L,反沖洗水量為進(jìn)水流量的2倍,曝氣量為1L/min,正常運行11min后反洗1min,每48h排空一次。裝置以6d為一個周期,運行4個周期,每個周期結(jié)束后進(jìn)行化學(xué)藥劑清洗(0.05mol/L的HCl浸泡膜12h),清洗結(jié)束后繼續(xù)運行。
在實驗條件下,利用陶瓷平板膜代替采油廠原始處理工藝中的浮選、粗濾、精濾步驟(方案一)或粗濾、精濾步驟(方案二),均能得到較好的處理效果,且跨膜壓差穩(wěn)定,系統(tǒng)未出現(xiàn)嚴(yán)重的膜堵塞現(xiàn)象,運行穩(wěn)定。其中出水中的含油量及SS均小于1mg/L,出水水質(zhì)優(yōu)于SY5329-94《碎屑巖油藏注水水質(zhì)推薦指標(biāo)及分析方法》中回注水水質(zhì)A1級標(biāo)準(zhǔn)。較原有處理工藝,系統(tǒng)表現(xiàn)出更高的處理效能,由于省略了氣浮、粗濾及精濾工藝,減小了占地及土建費用,處理后出水能夠直接用于低滲透地層的回注,因此,該工藝可以應(yīng)用于油田回注水處理中。
3 結(jié)論
(1)利用陶瓷平板膜處理采油廢水,出水中SS及含油量均小于1mg/L,出水水質(zhì)優(yōu)于油田回注水水質(zhì)A1級標(biāo)準(zhǔn)。
(2)利用陶瓷平板膜處理采油廢水較佳運行條件為:曝氣量為1L/min,膜通量為22.5L/(㎡·h),運行溫度為50℃。
(3)利用0.05mol/L HCl或HNO3的溶液對污染后的膜片進(jìn)行浸泡清洗,膜片過濾性能恢復(fù)較好,膜通量的恢復(fù)率均在96%以上。
(4)利用陶瓷平板膜處理采油廢水,系統(tǒng)長期運行穩(wěn)定,出水可用于低滲透地層的回注,且較原有工藝節(jié)約了占地及土建費用,具有較好的應(yīng)用前景。