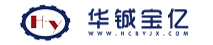
由于碟式分離機(jī)分離因數(shù)高,生產(chǎn)能力大,常用于分離高度分散的物系,如密度相近的液體所組成的乳濁液以及高粘度液相中含細(xì)小顆粒所組成的液-固二相懸浮液等,因此在化工、醫(yī)藥、石油、交通、食品、輕工以及生物工程等行業(yè)有著廣泛的應(yīng)用。化工行業(yè)如PTA工藝中,由于母液催化劑回收單元含有大量草酸鹽沉淀,就是利用碟片式離心機(jī)加以分離回收的。本文對化工單元噴嘴碟式離心機(jī)進(jìn)行液固分離過程分析并建立工藝流程模型,同時(shí)對不同轉(zhuǎn)速下離心機(jī)內(nèi)部流體的流速進(jìn)行分析研究。
1 碟式離心機(jī)分離影響因素淺析
1.1 碟式離心機(jī)分離基理
離心澄清是在高度分散的懸浮液中,將極細(xì)的固體顆粒從液相中分離的沉降過程。
1.2 碟式離心機(jī)分離影響因素
臨界粒徑與進(jìn)料量、漿料粘度、旋轉(zhuǎn)速度以及碟片的結(jié)構(gòu)參數(shù)等有關(guān),因此在不改變離心機(jī)結(jié)構(gòu)參數(shù)的條件下,轉(zhuǎn)速、漿料粘度、進(jìn)料量以及碟片數(shù)都是影響分離效率的主要因素。增加轉(zhuǎn)速可以使臨界粒徑減小,提高分離效果,還可以減小臨界粒徑,提高分離效率;降低懸浮液的粘度同樣可以降低臨界粒徑,增大分離效率。
針對轉(zhuǎn)速的影響,有研究指出,并不是轉(zhuǎn)速越快,分離效率越高,因?yàn)楫?dāng)轉(zhuǎn)速非常高時(shí),離心機(jī)內(nèi)部在靠近碟片處的高的流體速度所形成的對流可能對碟片上分離的固體顆粒造成沖擊,離心效果反而下降。
隨著轉(zhuǎn)速的增加,碟片內(nèi)流體徑向速度方向隨轉(zhuǎn)速增大逐漸好轉(zhuǎn),周向速度則隨轉(zhuǎn)速增大而增大,當(dāng)轉(zhuǎn)速n=3000和n=3300時(shí),其流體徑向速度向下,說明流體對顆粒產(chǎn)生向下作用,利用顆粒沿碟片向下分離至噴嘴處,轉(zhuǎn)速越高,流體向下的徑向和周向速度越大,分離效果越好。
2 碟式離心機(jī)工藝流程模型建立
2.1 工作原理
碟式離心機(jī)中具有再循環(huán)裝置,由噴嘴出來的一部分濃縮物料被排走,一部分再循環(huán)至轉(zhuǎn)鼓底部,再循環(huán)流不進(jìn)入碟片進(jìn)行分離,只是進(jìn)入轉(zhuǎn)鼓底部特殊的分布器,再通過再循環(huán)管送到噴嘴附近。進(jìn)料則是通過頂部進(jìn)料管進(jìn)入轉(zhuǎn)鼓底部的分布器,并通過碟片上的進(jìn)流孔進(jìn)入碟片進(jìn)行分離,因此被送到噴嘴處的再循環(huán)物料不會干擾進(jìn)料的離心分離,進(jìn)料在進(jìn)入碟片分離后,被分離固體經(jīng)過高速旋轉(zhuǎn),沿著碟片向下分離至噴嘴處,與循環(huán)回來的物料在噴嘴處匯合,而澄清的分離液則向上溢流進(jìn)入出料管,從離心機(jī)頂部出料。離心機(jī)通過不斷的循環(huán)回流使得底流的固含量達(dá)到平衡。在實(shí)際操作過程中,底部常會有可降低噴嘴處固含量的一股補(bǔ)充酸。
2.2 ASPENPLUS工藝模型建立
根據(jù)離心機(jī)內(nèi)部物料工藝流動過程,可利用ASPENPLUS軟件建立工藝模擬流程。
模擬流程主要由兩個模塊組成,Split分離模塊和Mixer混合器模塊。其中Fin為離心機(jī)進(jìn)料流量;Fdown為離心機(jī)底部出料流量;Fup為頂部溢流量;Fmakeup為底部補(bǔ)充流量。物性方法則根據(jù)所模擬物料性質(zhì)來確定,流體分級定義為MIXCISLD。
其中Split1(B1)模塊的分離比率主要體現(xiàn)在固體經(jīng)碟片分離后的比率,MIX模塊體現(xiàn)了在噴嘴處的混合作用,Split2(B2)模塊主要體現(xiàn)從噴嘴出來的流體的循環(huán)比率,因此應(yīng)用該離心機(jī)ASPENPLUS流程模型對現(xiàn)場進(jìn)行分析模擬時(shí)需采集現(xiàn)場的各個流股的進(jìn)出流量、組分以及溫度、壓力數(shù)據(jù)對其模型進(jìn)行靜態(tài)模擬,計(jì)算出不同工況下的固體分離率。如正常操作工況、進(jìn)料流量不同工況、進(jìn)料固含量(分離固體組分)不同工況、影響粘度的不同溫度工況、離心機(jī)不同轉(zhuǎn)速工況、不同碟片數(shù)安裝工況、不同底部流量等,得到不同工況下Split(B1)固體分離的分離效率,給實(shí)際離心機(jī)的操作提供參考意見。
在應(yīng)用模型對實(shí)際工況進(jìn)行分析時(shí),應(yīng)根據(jù)實(shí)際情況改變模型參數(shù),并與實(shí)際情況相結(jié)合,達(dá)到診斷“瓶頸”的作用。以改變離心機(jī)進(jìn)料固含量為例,模型Split模塊中輸入的分離效率如果不變,而實(shí)際工程操作分析值大部分時(shí)間情況下低于該模型計(jì)算的底部固含量模擬值,這說明離心機(jī)進(jìn)料固含量增高會造成碟式離心機(jī)分離效率降低。
3 結(jié)論
(1)轉(zhuǎn)速、漿料粘度、進(jìn)料量以及碟片數(shù)都是影響分離效率的主要因素,另外,在增加碟式離心機(jī)轉(zhuǎn)速時(shí),還應(yīng)考慮碟片間流態(tài)對顆粒分離造成的影響。
(2)通過碟式離心機(jī)的工作原理分析建立ASPENPLUS工藝流程模擬模型,在模型應(yīng)用過程中,需針對工藝工程中的實(shí)際工況,與模型進(jìn)行結(jié)合,主要通過調(diào)節(jié)Split模塊來分析判斷離心機(jī)分離影響因素,以達(dá)到診斷“瓶頸”的作用。