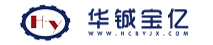
碟式離心機(jī)因其高轉(zhuǎn)速、高效率、大處理量等優(yōu)點,在石油、化工、醫(yī)療和環(huán)保等領(lǐng)域被廣泛使用,其碟片間流場內(nèi)沉降分離過程是影響碟式離心機(jī)分離性能的關(guān)鍵。碟式離心機(jī)碟片間的薄層多相流動主導(dǎo)著碟式離心機(jī)性能。
對于碟片間薄層流場的流動特性,國際上不少學(xué)者利用理論計算和試驗嘗試探究其流動規(guī)律。本文研究主要針對離心力場下薄層流場內(nèi)的兩相沉降過程,以多相流理論為基礎(chǔ),建立碟式離心機(jī)碟片間隙內(nèi)流場及多組碟片間薄層流場的三維流動模型,并以CFD模擬,通過理論計算懸浮液內(nèi)顆粒的受力情況及沉降速度,結(jié)合數(shù)值模擬分析多組碟片間薄層流場內(nèi)兩相流動性;通過對比輕、重相的相對流動性,研究了離心力場下薄層流場內(nèi)重相在連續(xù)相的沉降過程。研究結(jié)果對優(yōu)化碟式離心機(jī)結(jié)構(gòu)、提高離心機(jī)的性能、拓展離心機(jī)新的應(yīng)用、實現(xiàn)技術(shù)突破,具有重要的意義。
1 離心力場下薄層流動模型及可行性驗證
1.1 碟式離心機(jī)轉(zhuǎn)鼓內(nèi)薄層流動模型
碟片間薄層流場結(jié)合了超重力沉降和淺池原理,即懸浮液中的顆粒在離心場下作沉降運(yùn)動,其生產(chǎn)能力正比于沉降面積。此流動過程的優(yōu)勢是利用碟片將沉降池均分為若干薄層流動場,以此降低離心機(jī)內(nèi)懸浮液的沉降高度,在一定的離心機(jī)高度下增加碟片數(shù),從而增加沉降面積,進(jìn)而加速懸浮液在離心場下的沉降過程,有效地提高了離心機(jī)的離心分離性能。
通過CFD模擬研究轉(zhuǎn)鼓內(nèi)薄層流場,并做假設(shè)如下:
(1)轉(zhuǎn)鼓內(nèi)充滿液體且流動穩(wěn)定;
(2)液相為連續(xù)不可壓縮流體;
(3)固相為密度均勻等粒徑球形顆粒,且運(yùn)動過程中不發(fā)生絮凝、破碎和變形;
(4)不考慮重力;
(5)不考慮沉渣擠壓作用帶來的熱影響。
使用ANSYS15.0前處理軟件ICEM建立5層碟片間兩相流動區(qū)域及轉(zhuǎn)鼓成渣腔的三維流動模型,進(jìn)料口與定距筋條作網(wǎng)格局部加密處理,以提高結(jié)構(gòu)化網(wǎng)格質(zhì)量。
1.2 流動模型的邊界條件
根據(jù)OCM305標(biāo)準(zhǔn)碟式離心機(jī)分離處理5號噴氣燃料油(RP-5),相關(guān)標(biāo)準(zhǔn)依據(jù)國內(nèi)航空使用的重煤油標(biāo)準(zhǔn)。碟式離心機(jī)轉(zhuǎn)鼓內(nèi)的主要結(jié)構(gòu)及重煤油的相關(guān)物理特性見下表:
碟片組高度(m) | 0.11 | 油相密度(kg/m3) | 814 |
碟片厚度(mm) | 0.3 | 水相密度(kg/m3) | 998.2 |
碟片錐角(°) | 45 | 水粒徑(μm) | 10 |
轉(zhuǎn)鼓內(nèi)徑(mm) | 235 | 流量(m3/h) | 1 |
油相黏度(mPa·s) | 6.919 | 水相體積分?jǐn)?shù)(%) | 1 |
水相黏度(mPa·s) | 1.003 | 轉(zhuǎn)速(r/min) | 6000~10000 |
研究碟式離心機(jī)碟片間兩相流動場,由于無需考慮渦黏性各項同性假設(shè),湍流模型比雷諾應(yīng)力模型更加精準(zhǔn)。在碟片間兩相流動場中,物料受離心作用處于高速旋轉(zhuǎn)運(yùn)動且其流場為強(qiáng)制渦。因此模擬中采用RSM湍流模型,其計算原理是質(zhì)量守恒方程、動量守恒方程、應(yīng)力運(yùn)輸方程。碟片間兩相流動屬于多相流動,采用Eulerian模型能夠精準(zhǔn)地研究碟片間兩相流動性及其分離性能。計算模型對兩相間的相互作用,計算模型中不僅包含了不同相間的相對運(yùn)動,而且不同相間相對運(yùn)動的速度大小不同,因此計算模型能夠比較全面地分析碟片間兩相流動過程。
1.3 數(shù)值模擬的可行性驗證
對碟式離心機(jī)的理論分析和模擬研究均是建立在一定的假設(shè)基礎(chǔ)上,與實際分離情況并不完全吻合,需要進(jìn)行數(shù)值模擬的可靠性驗證,驗證試驗?zāi)軌虺浞挚紤]到理論、模擬中忽略到的相關(guān)影響因素,因此是研究中不可或缺的一部分。由于碟式離心機(jī)轉(zhuǎn)鼓內(nèi)碟片間薄層流場的復(fù)雜流動性,一般儀器均無法對轉(zhuǎn)鼓內(nèi)部流動進(jìn)行準(zhǔn)確的實時測量。
因此通過對含水煤油的試驗?zāi)M,根據(jù)全自動微量水分測定儀測出進(jìn)出口的水分含量,并計算出離心機(jī)的分離效率,計算結(jié)果對轉(zhuǎn)鼓轉(zhuǎn)速及進(jìn)料量對分離效率的影響進(jìn)行討論,根據(jù)試驗結(jié)果來驗證數(shù)值模擬方法的可靠性。
測試在相同進(jìn)料量下,不同轉(zhuǎn)速的分離效率。由測試結(jié)果可知,碟式離心機(jī)的分離效率與轉(zhuǎn)速成正比,模擬與試驗的分離效率值有所偏差,且轉(zhuǎn)速越大偏差值越小。存在偏差的原因在于試驗物料含雜雜質(zhì),且不是單一粒徑,轉(zhuǎn)速較小時小粒徑的重相較難進(jìn)行離心沉降分離,而隨著轉(zhuǎn)速增加,模擬與試驗的偏差值逐步減小,兩者的平均偏差為26.6%,在試驗誤差范圍內(nèi),證明了數(shù)值模擬具有較好的可靠性。
測試在同一轉(zhuǎn)速下,不同進(jìn)料量的分離效率。由測試結(jié)果可知,碟式離心機(jī)的分離效率與流量成反比,碟式離心機(jī)的進(jìn)料量越大,分離效率越低;模擬與試驗的分離效率值有所偏差,且進(jìn)料量越大偏差值越大。物料的軸向進(jìn)料速度對碟片間薄層流場的沉降有所干擾,進(jìn)料量越大越不利于物料的離心沉降分離。存在偏差的原因在于試驗過程中流量計數(shù)值波動較大,數(shù)值模擬中主要取流量的平均值進(jìn)行計算。當(dāng)?shù)诫x心機(jī)處理量較小時,其模擬與試驗的偏差值也較小,兩者的平均偏差為18.7%,在試驗誤差范圍內(nèi),進(jìn)而表明了數(shù)值模擬的可靠性。
2 薄層流場內(nèi)顆粒的沉降速度
2.1 薄層流場內(nèi)顆粒的受力情況
通過建立離心機(jī)轉(zhuǎn)鼓內(nèi)薄層流場中分散相顆粒的分離模型,進(jìn)一步分析薄層流場內(nèi)分散相顆粒在離心力場下沉降分離的運(yùn)動情況。由于薄層流場內(nèi)的分散相顆粒粒徑很?。ㄒ话阍?/span>3~15μm),可忽略慣性力的影響;由于薄層流場內(nèi)分散相的濃度很低(一般不大于10%),可忽略顆粒間的相互作用以及其布朗運(yùn)動;由于薄層的流場的流速很大(一般在5000~12000r/min),且邊界層的厚度相對較小,相對于中層大流速可忽略其邊界層對離心機(jī)內(nèi)薄層流動的影響。因此研究碟式離心機(jī)內(nèi)薄層流場內(nèi)分散相顆粒,主要考慮其受到的離心力、重力、浮力、離心浮力、流體阻力作用。
經(jīng)測試,分散相顆粒的離心力和阻力與其在薄層流場內(nèi)徑向位置有關(guān)。
2.2 離心沉降速度的理論分析
在離心力場下顆粒做沉降運(yùn)動,分散相顆粒由中性進(jìn)料孔進(jìn)去碟片間薄層流場后做加速運(yùn)動,在連續(xù)相中所受阻力隨速度不斷增大,直到阻力與離心力相等時即達(dá)到重力沉降的飽和穩(wěn)態(tài)速度。
2.3 離心沉降速度的數(shù)值模擬
碟式離心機(jī)轉(zhuǎn)鼓內(nèi)流動分布符合旋轉(zhuǎn)流場的一般規(guī)律。物料在碟式離心機(jī)轉(zhuǎn)鼓內(nèi)的離心沉降過程是在多組碟片間薄層流場內(nèi)進(jìn)行的,物料由中性孔進(jìn)入碟片間薄層流場,由于輕重相所受離心力與密度差的影響,大部分輕相從碟片內(nèi)端出口流出,重相從碟片外端出口流出,從而完成了在碟片間薄層流場內(nèi)的離心沉降分離過程。
物料進(jìn)入中心孔后做加速沉降運(yùn)動,中心孔內(nèi)中心線上顆粒所受的離心浮力、離心力與阻力平衡,其沉降速度為零;由中性孔往大端,顆粒所受離心浮力與離心力不斷增大,在離心力場下的沉降速度沿碟片間薄層流場朝外;由中心孔往內(nèi)端,顆粒所受阻力大于離心浮力與離心力之和,在離心力場下的沉降速度沿碟片間薄層流場朝內(nèi)。研究結(jié)果表明,中心孔內(nèi)多層碟片間的進(jìn)料逐層增多,碟片間薄層流場內(nèi)物料的相對沉降速度往內(nèi)、外端逐漸增大。
碟式離心機(jī)內(nèi)轉(zhuǎn)鼓作逆時針旋轉(zhuǎn)運(yùn)動,物料由中性孔進(jìn)入碟片間薄層流場后做離心加速運(yùn)動直到相對穩(wěn)定速度,其相對穩(wěn)定速度小于碟片旋轉(zhuǎn)速度;沿碟片旋轉(zhuǎn)方向,定距筋條前側(cè)物料沿筋條側(cè)壁面往碟片內(nèi)端流動,定距筋條后側(cè)物料具有較好的跟隨性,其相對速度基本為零;相鄰兩個定距筋條中間區(qū)域薄層流場內(nèi),流體受水平剪切力作用,物料的相對穩(wěn)定速度大于碟片旋轉(zhuǎn)速度。研究結(jié)果表明,物料由中性孔進(jìn)入薄層流場內(nèi),在定距筋條外側(cè)物料流動相對滯后,在相鄰兩個定距筋條中間區(qū)域的物料流動超前于碟片旋轉(zhuǎn)運(yùn)動。
3 薄層流場內(nèi)輕重相分布情況
碟式離心機(jī)中性孔內(nèi)重相體積分布由 層往上逐步升高;中性孔內(nèi)中心線往碟片內(nèi)端的重相體積分布較小于中心線往碟片外端。研究結(jié)果表明,碟式離心機(jī)中性孔內(nèi)重相體積分布不均,中性孔上端重相體積分布較大,輕重相分界面較為明顯且徑向位置在中性孔中心線附近。
碟片間薄層流場內(nèi)輕重相形成較明顯的分界面,碟片間薄層流場內(nèi)向下表面往上重相體積分布逐步升高,大部分輕相沉積在薄層流場的下表面,重相堆積在薄層流場的上表面;碟片間薄層流場內(nèi)由碟片外端往碟片內(nèi)端重相體積分布逐步升高,大部分輕相從碟片內(nèi)端流出; 層碟片間薄層流場內(nèi)重相體積分布較大。研究結(jié)果表明,各層碟片間薄層流場內(nèi)重相體積分布不均,大量重相進(jìn)入 層碟片間薄層流場進(jìn)行離心沉降分離,碟片間薄層流場內(nèi)形成明顯的輕重相分界面,重相堆積在碟片下表面。
沿碟片逆時針旋轉(zhuǎn)方向,中性孔前后側(cè)的重相體積分布較小,往碟片外端的重相體積分布較大;定距筋條后側(cè)重相體積分布較小,定距筋條前側(cè)的重相體積分布較大;相鄰兩個定距筋條中間區(qū)域的薄層流場內(nèi),重相體積分布沿逆時針方向逐步減小,且碟片內(nèi)端重相體積分布較小。研究結(jié)果表明,碟片間薄層流場內(nèi)重相體積分布不均且輕重相分界面較為明顯,重相堆積在定距筋條前側(cè),中性孔前后側(cè)重相體積分布較小,大部分輕相從碟片內(nèi)端流出。
4 水滴粒徑對分離性能的影響
由于物料中液滴的粒徑大小不同,對碟式離心機(jī)分離效率的影響較大。在液滴粒徑為10~30μm的范圍內(nèi),分離效率隨液滴粒徑的增加而顯著增加。在粒徑達(dá)到30μm以后,離心機(jī)的分離能力達(dá)到了極限,輕相出口的重相體積分布不再隨粒徑增加而明顯增加。
5 結(jié)論
(1)轉(zhuǎn)鼓內(nèi)徑重相的離心力和阻力與其在薄層流場內(nèi)的徑向位置有關(guān),多層碟片間的進(jìn)料量自下往上逐層增大,碟片間薄層流場內(nèi)物料的相對沉降速度由中性孔向端口逐步增大。
(2)靠近碟片外端口物料流動具有相對滯后性,定距筋條間區(qū)域的物料流動超前于碟片旋轉(zhuǎn)運(yùn)動。
(3)碟式離心機(jī)中性孔內(nèi)重相體積分布不均,中性孔內(nèi)上端重相體積分布較大,輕重相分界面較為明顯且徑向位置在中性孔中心線附近。
(4)碟片間薄層流場內(nèi)重相體積分布不均且輕重相分界面較為明顯,重相堆積在定距筋條前側(cè),大部分輕相從碟片內(nèi)端流出。
(5)各層碟片間薄層流場內(nèi)重相體積分布不均,大量重相在 層碟片間薄層流場進(jìn)行離心沉降分離。