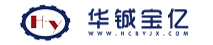
冶金生產(chǎn)過程中產(chǎn)生的污泥主要有煉鐵高爐瓦斯泥、煉鋼轉(zhuǎn)爐除塵污泥以及各軋鋼工序產(chǎn)生的化學(xué)污泥等。由于各生產(chǎn)工序生產(chǎn)工藝不同,故產(chǎn)生的污泥性質(zhì)差別較大。目前,國內(nèi)冶金企業(yè)污泥綜合利用一般是根據(jù)不同污泥的性質(zhì)進(jìn)行分類回收,煉鋼瓦斯泥多采用浮選精選的方法進(jìn)行提煉,提煉后含鐵量高的污泥送燒結(jié)或球團(tuán)配料,剩下含鐵量低的污泥送往廠外制磚,如武鋼、馬鋼等采用該方法。煉鋼轉(zhuǎn)爐污泥多采用濃縮后直接送至燒結(jié)一混圓筒進(jìn)行配料或脫水后送料場配料,如濟(jì)鋼、柳鋼等即采用該方法。軋鋼化學(xué)污泥采用脫水外運(yùn)處理,如唐鋼即采用該方法??傮w來說,冶金污泥回收利用非常普及,但或多多少存在因污泥外運(yùn)而帶來的二次污染,且污泥利用率不高。
鄂城鋼鐵廠燒結(jié)分廠擬將各分廠的生產(chǎn)污泥混合后制成污泥膏用于燒結(jié),并成功進(jìn)行了生產(chǎn)實(shí)踐。
1 項(xiàng)目背景
鄂城鋼鐵廠主要由煉鐵分廠、煉鋼分廠、電爐分廠、小型分廠、中型軋鋼分廠、棒材分廠、線材分廠、燒結(jié)和焦化分廠。根據(jù)污泥性質(zhì)不同可將其生產(chǎn)污泥分為四大類,即煉鐵高爐瓦斯泥、煉鋼轉(zhuǎn)爐污泥、電爐污泥及軋鋼污泥。該廠原有污泥處理設(shè)施是將轉(zhuǎn)爐污泥濃縮后送24㎡燒結(jié)機(jī)一混圓筒配料,其他污泥均脫水后送原料廠配料或外運(yùn)填埋。該系統(tǒng)可回收冶金污泥量為3×104t/a,環(huán)境和經(jīng)濟(jì)效益顯著,盡管如此,仍有大量生產(chǎn)污泥未被利用。
隨著企業(yè)的不斷發(fā)展,電爐廠異地改造,與之配套的小型連軋生產(chǎn)線也投產(chǎn)運(yùn)行,4號(hào)1860煉鐵高爐和90㎡燒結(jié)機(jī)相繼建成投產(chǎn),一方面生產(chǎn)污泥量大幅度增加,另一方面90㎡燒結(jié)機(jī)的建成投產(chǎn)也使燒結(jié)消化污泥的能力大幅度增加。由此,結(jié)合 的污泥脫水技術(shù),提出一種全新的污泥處理工藝,即將廠區(qū)所有生產(chǎn)污泥進(jìn)行收集、濃縮、脫水后制成污泥膏直接用于燒結(jié)混合圓筒配料。
2 基本設(shè)計(jì)參數(shù)
2.1 污泥量
各分廠的污泥排放量見下表:
污泥來源 | 含水污泥量 | 干泥量(t/a) | 備注 |
煉鐵廠高爐瓦斯泥 | 160m3/h | 13400 | 連續(xù)排放 |
二煉鋼轉(zhuǎn)爐及線材污泥 | 450m3/d | 19000 | 間歇排放 |
電爐廠化學(xué)污泥 | 50m3/d | 2000 | 間歇排放 |
小型廠 | 160m3/d | 5600 | 間歇排放 |
中型軋鋼廠外排污泥 | 120m3/d | 4000 | 間歇排放 |
四號(hào)高爐瓦斯泥 | 36m3/h | 7100 | 連續(xù)排放 |
合計(jì) | 5484m3/d | 51100 |
2.2 污泥性質(zhì)
各類污泥的主要成分見下表:
污泥名稱 | TFe | SiO2 | C | CaO |
軋鋼污泥 | 69.55 | 1.6 | 1.96 | 0.6 |
瓦斯泥 | 23.89 | 4.32 | 47.3 | 2.80 |
轉(zhuǎn)爐污泥 | 56.03 | 22.80 | 4.1 | |
電爐污泥 | 22.34 | 7.0 | 3.02 | 24.0 |
2.3 處理后污泥膏含水量的確定
在燒結(jié)生產(chǎn)過程中,一般要求燒結(jié)混合料含水量在(6.5±0.3)%,故需噴水調(diào)整濕度,通常采用噴濕污泥的方式,既可以補(bǔ)充水分,又可以利用污泥,但由于未經(jīng)處理的污泥含固率較低,從而使污泥利用量受到限制,因此提高污泥利用率的關(guān)鍵在于怎樣降低污泥含水率。根據(jù)鄂鋼生產(chǎn)的實(shí)際情況,燒結(jié)生產(chǎn)混合料中的混勻礦、煤粉等物料自身的含水率通常比生產(chǎn)要求的(6.5±0.3)%還要高,真正能消化污泥的是返礦,燒結(jié)分廠燒結(jié)返礦用量為120t/h,如果忽略返礦的含水率,則干污泥總量為51100t/a;每天利用干污泥量為154.8t(按年生產(chǎn)330d計(jì));每小時(shí)利用干污泥量為6.5t;與返礦混合后混合料含水率按6.5%計(jì),則需水量為9t;脫水后污泥膏含水率為58%。
根據(jù)以上計(jì)算,考慮到返礦含水率不可能為零,同時(shí)考慮安全設(shè)計(jì)系數(shù),脫水后污泥含水率計(jì)算值暫取35%,運(yùn)行時(shí)根據(jù)實(shí)際情況進(jìn)行控制。
2.4 設(shè)計(jì)規(guī)模
污泥量為296m3/h。由于廠區(qū)生產(chǎn)污泥排放的間歇性,工程設(shè)計(jì)處理規(guī)模為400m3/h。
3 工藝方案的確定
3.1 污泥收集與輸送
針對冶金生產(chǎn)污泥的不同性質(zhì)及各生產(chǎn)工序污泥間歇排放的特點(diǎn),結(jié)合鄂鋼廠區(qū)總圖布局的實(shí)際情況,將距燒結(jié)分廠較近的煉鐵高爐瓦斯泥直接泵送至污泥處理站。煉鋼轉(zhuǎn)爐污泥由于流動(dòng)性差,輸送比較困難,采用氣力輸送方式。其他分廠的生產(chǎn)污泥采用分段加壓、逐級(jí)輸送的方式運(yùn)至污泥處理站。
污泥輸送管道架空敷設(shè),所有彎頭均采用45°彎頭,且設(shè)空氣清掃管。煉鋼轉(zhuǎn)爐及連鑄污泥采用循環(huán)回流、連續(xù)輸送的方式,以避免間歇運(yùn)行造成管道堵塞。
3.2 污泥處理工藝流程
廠區(qū)生產(chǎn)污泥→砂水分離器→污泥濃縮池→混合池加入絮凝劑→脫水間→螺旋輸送機(jī)→污泥切割機(jī)→燒結(jié)配料皮帶。
各分廠的生產(chǎn)污泥收集至污泥處理站后先經(jīng)砂水分離器去除粗顆粒固體后自流至重力濃縮池濃縮,然后泵提至混合池,同時(shí)投加絮凝劑進(jìn)行充分?jǐn)嚢?,混合液?jīng)螺桿泵加壓至螺旋離心脫水機(jī)脫水,濃縮池上清液及濾液回用于生產(chǎn),脫水后的污泥膏利用螺旋輸送機(jī)和切割機(jī)直接送至燒結(jié)配料皮帶輸送機(jī),與混合料混合利用。
3.3 設(shè)計(jì)要點(diǎn)
(1)污泥輸送管路必須考慮沖洗系統(tǒng)和檢修口,以防止管路堵塞。
(2)脫水機(jī)的選擇是關(guān)鍵,經(jīng)過充分論證、比較和考察后決定采用螺旋離心脫水機(jī)作為污泥濃縮脫水設(shè)備,螺旋離心脫水機(jī)具有以下特點(diǎn):進(jìn)泥和出泥均為連續(xù)運(yùn)行,有利于污泥膏直接與燒結(jié)配料皮帶輸送機(jī)上的混合料混合。脫水后污泥的含水率可以通過調(diào)整離心脫水機(jī)的轉(zhuǎn)速自行調(diào)節(jié),便于污泥膏的制備;便于自動(dòng)化運(yùn)行和清潔生產(chǎn)。
(3)由于螺旋離心脫水機(jī)對進(jìn)料介質(zhì)要求較高,故污泥進(jìn)入脫水機(jī)后需進(jìn)行充分?jǐn)嚢?,盡量保證污泥進(jìn)料基本穩(wěn)定,使脫水機(jī)穩(wěn)定運(yùn)行。
(4)污泥膏投加前加切割機(jī)攪細(xì),均勻投加以便于燒結(jié)混料。
3.4 主要建(構(gòu))筑物及設(shè)備
(1)污泥濃縮池
污泥濃縮池采用地上高架式,鋼混結(jié)構(gòu),尺寸為16.0m×6.5m,有效高度為3.5m,濃縮池底部為污泥提升泵房、高壓沖洗泵房、加藥間和控制室。
(2)污泥混合池
非標(biāo)鋼結(jié)構(gòu)設(shè)備,配用攪拌機(jī)功率為7.5kW。
(3)臥式螺旋離心脫水機(jī)
4臺(tái)。配用電機(jī)功率為45kW,轉(zhuǎn)速為3000r/min,處理量為35m3/h,PLC控制。
(4)螺旋輸送機(jī)
2臺(tái)。螺旋輸送機(jī)圓筒直徑為450mm,長度根據(jù)現(xiàn)場實(shí)際需要確定,配用電機(jī)功率為0.55kW。
(5)污泥切割機(jī)
2臺(tái)。非標(biāo)設(shè)備,配用電機(jī)功率為0.55kW。
4 經(jīng)濟(jì)技術(shù)分析
工程總投資為1860萬元,處理后噸泥回收成本為13.46元,毛收益為1022萬元/a(按鄂鋼內(nèi)部核算價(jià)為200元/t污泥計(jì)算),則每年凈收益為953.2萬元。
5 存在的問題及分析
(1)廠區(qū)軋鋼污泥采用間歇方式輸送,污泥濃縮池進(jìn)水負(fù)荷不穩(wěn)定造成了濃縮池出水水質(zhì)不穩(wěn)定,有跑泥現(xiàn)象發(fā)生,針對這種情況,廠方正在著手將軋鋼污泥間歇輸送方式改為循環(huán)回流連續(xù)輸送方式。
(2)經(jīng)離心脫水機(jī)脫水后的污泥膏直接送至燒結(jié)配料皮帶輸送機(jī)與燒結(jié)礦混合,易產(chǎn)生揚(yáng)塵,揚(yáng)塵粘附在污泥切割機(jī)出口造成堵塞,必須人工定期清除,還有待進(jìn)一步改進(jìn)。
(3)污泥處理系統(tǒng)與皮帶輸送機(jī)原采用聯(lián)鎖控制方式,由于污泥處理系統(tǒng)開停機(jī)延時(shí)時(shí)間較長,皮帶輸送機(jī)停機(jī)后脫水機(jī)仍有部分污泥排至皮帶,造成皮帶上污泥膏堆積,為解決該問題,改自控為人工調(diào)度,這給生產(chǎn)管理帶來不便。
6 結(jié)語
該工程于2005年10月正式投產(chǎn)運(yùn)行,先后進(jìn)行了增加砂水分離器和增加一臺(tái)螺旋離心脫水機(jī)等技術(shù)改造,兩年多的實(shí)際運(yùn)行表明,將冶金生產(chǎn)混合污泥經(jīng)螺旋離心脫水機(jī)脫水制成污泥膏直接用于燒結(jié)混合配料的處理工藝是成功的。該技術(shù)不僅改變了過去分質(zhì)處理利用帶來的生產(chǎn)管理復(fù)雜性,避免了常規(guī)板框或帶機(jī)脫水及污泥汽車運(yùn)輸造成的二次污染,同時(shí)也給企業(yè)自身帶來了巨大的經(jīng)濟(jì)效益,是冶金污泥綜合利用技術(shù)的一次革新。