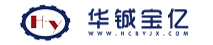
自來水廠產(chǎn)生的廢水主要來自沉淀池或澄清池的排泥水和濾池的反沖洗水。生產(chǎn)廢水經(jīng)過濃縮池處理后產(chǎn)生的污泥,如直接進(jìn)行脫水處理,其脫水效果很差,須進(jìn)行各種調(diào)理過程。污泥調(diào)理的方法較多,大體可以分為兩大類:化學(xué)調(diào)理和物理調(diào)理。加藥調(diào)理主要有石灰處理、酸處理、堿處理、高分子絮凝劑和無機(jī)混凝劑處理等;不加藥處理包括熱處理、冷凍處理等技術(shù),而混凝劑調(diào)理為較常用的污泥脫水前處理技術(shù)。
北京市第九自來水廠每天產(chǎn)生的含水率為98%~99%的濃縮污泥約1000t。污泥脫水采用離心方式,為了達(dá)到較好的泥水分離效果,污泥調(diào)理過程中投加了大量的PAM,但是脫水效率依然較低,泥餅含水率約為80%。由于脫濾液的水質(zhì)較差,而且受到高濃度PAM的污染,所以無法回用,只能直接排放,不僅浪費大量的水資源,并且嚴(yán)重污染了周圍河道。因此,本研究擬采用隔膜壓濾技術(shù),并篩選出與其相適宜的污泥調(diào)理技術(shù): ,實現(xiàn)污泥深度脫水,在污泥脫水過程中削減污泥量;第二,清液回用。隔膜壓濾機(jī)過濾壓力高,可以選用致密的濾布,通過濾布截留和濾餅層過濾,獲得清澈的濾液。因此,在保證污泥高效脫水的基礎(chǔ)上,達(dá)到回用污泥脫水清液的目的,從而實現(xiàn)水廠排泥水零排放。
1 試驗部分
1.1 水廠污泥基本情況介紹
第九自來水廠每天產(chǎn)生的含水率為98%~99%的濃縮污泥約1000t。污泥中主要成分為氫氧化鋁、氫氧化鐵、PAM和少量有機(jī)質(zhì)。污泥密度為1g/cm3。小試污泥除PAC與石灰復(fù)配試驗含水率為97.77%外,其他各組試驗污泥原始含水率均為98.4%。
1.2 污泥調(diào)理藥劑
3種無機(jī)混凝劑(氯化鐵、PAC和石灰)、1種有機(jī)混凝劑(PAM)。其中,氯化鐵和PAC均為液體藥劑,其質(zhì)量濃度和氧化鋁含量分別為38%和10%。
1.3 污泥調(diào)理和脫水試驗
1.3.1 小試
(1)污泥調(diào)理過程。
取500mL污泥置于1000mL塑料燒杯中。開啟攪拌裝置(ZR4-6混凝試驗攪拌機(jī)),在快攪速度為200r/min的條件下加入不同比例的氯化鐵、PAC和石灰等藥劑,30s后降速至100r/min攪拌2min,然后進(jìn)行SRF測定實驗。對于復(fù)配實驗,按按照試驗配比投加氯化鐵和PAC,然后加入石灰,繼續(xù)攪拌,直至大部分氫氧化鈣溶解。
(2)SRF的測定。
SRF試驗的操作如下:取待測污泥樣品100mL于量筒中,在恒定氣壓P=0.9MPa的條件下過濾(Jk-0.3型),每隔10s記錄一次濾液體積,直到漏斗中濾餅層出現(xiàn)裂縫為止,停止抽濾,利用差量法測定濾餅含水率,然后進(jìn)行污泥比阻測定。
1.3.2 中試
(1)中試裝置。
選用小型隔膜壓濾機(jī)及其配套設(shè)備,主要有空壓機(jī)(可提供壓力為8kg)、高壓清洗機(jī)、調(diào)理罐(配有可調(diào)速攪拌機(jī))和氣動隔膜泵。壓濾面積約為4.5㎡,濾室總?cè)萘考s為0.12m3,濾布孔徑為5μm。濾板材質(zhì)為增強(qiáng)聚丙烯,規(guī)格為0.8m×0.8m×0.03m。
(2)污泥的調(diào)理。
每次向污泥調(diào)理罐中裝入1t濃縮污泥。然后在攪拌條件下,按照一定量加入氯化鐵、PAC、石灰或者復(fù)配藥劑,持續(xù)攪拌5min開始進(jìn)料。
(3)壓濾操作過程。
開啟液壓裝置,將濾板壓緊,壓力為22~27kg保壓。整個壓濾過程包括注滿、低壓(0~8kg)壓濾和高壓(15~16kg)壓榨三步,每次進(jìn)料量為0.5~0.6t。其中注滿時間約為5min,低壓壓濾持續(xù)80min,高壓壓榨維持20min。退去液壓,打開濾板。
2 結(jié)果和討論
2.1 小試結(jié)果
2.1.1 單一藥劑投加對Zeta電位的影響
原始Zeta電位為-22.27mV。隨著氯化鐵投加量的增加,Zeta電位逐漸上升。當(dāng)氯化鐵和PAC投加量分別為0.24,0.15g/L時,Zeta電位出現(xiàn)0點??梢钥闯觯琍AC的電中和能力略高于氯化鐵。
2.1.2 單一藥劑投加對Zeta電位和污泥比阻的影響
根據(jù)實驗室小試結(jié)果顯示,PAM投加后形成絮體較大,但是由于其絮體強(qiáng)度不高,而且黏性較強(qiáng),在高壓條件下容易變形堵塞濾孔,從而并沒有有效改善污泥的高壓壓濾脫水性能。這說明單獨使用PAM作為隔膜壓榨的調(diào)理藥劑是不可行的。
隨著氯化鐵投加量的增加,SRF先降低后升高,在0.39g/L時,SRF出現(xiàn)極小值為9.3×1011m/kg,而此時污泥的Zeta電位為22.83mV。污泥脫水性的改善:一方面依靠無機(jī)混凝劑的電中和作用實現(xiàn)絮凝;另一方面污泥中存在混凝處理過程中投加的PAM和本身含有的黏性膠體顆粒物,使得污泥的黏性較高,投加無機(jī)混凝劑不但可以依靠形成的水解產(chǎn)物與PAM和黏性膠體物質(zhì)結(jié)合降低污泥的黏度,還可以提高污泥的絮體強(qiáng)度,減小其不可壓縮性來提高污泥脫水性。和氯化鐵的結(jié)果一致,隨著PAC的投加量逐漸增加,SRF先減小后增加,在0.32g/L時,SRF出現(xiàn)極小值為7.3×1011m/kg,該值小于投加氯化鐵的極小值。這可能是由于與PAC相比,氯化鐵具有更強(qiáng)的電中和能力,絮凝效果更好,所以效果優(yōu)于氯化鐵。然而,當(dāng)兩種混凝投加量繼續(xù)增加后,污泥脫水性能惡化,這因為過剩電荷導(dǎo)致污泥絮凝效果變差,小顆粒物質(zhì)增加。
污泥比阻的下降與石灰的投加量的增加呈線性關(guān)系,說明氫氧化鈣的投加明顯改善了污泥的過濾性能,加快了污泥過濾速率。這主要是由于石灰投加后可以起到一定絮凝架橋作用,另一方面可以支撐污泥絮體,從而形成多孔結(jié)構(gòu),減小濾餅層對水流的阻力,使得污泥排水能力提升。
2.1.3 復(fù)配投加對污泥脫水性的影響
從氯化鐵和PAC與石灰復(fù)配的試驗結(jié)果可以看出,在單獨使用氯化鐵之后污泥比阻降低時,繼續(xù)投加石灰可以進(jìn)一步降低污泥比阻,而且從感官來看,污泥的黏性明顯降低,泥餅和濾布的剝離效果較好。這可能是由于污泥首先通過氯化鐵的電中和作用實現(xiàn)凝聚,同時水解產(chǎn)生的沉淀使得污泥的黏性降低,再加入石灰可以起到骨架支撐作用,進(jìn)一步減小污泥的不可壓縮性,使得污泥的脫水性進(jìn)一步得到改善。同時投加0.32g/L的PAC和0.64g/L石灰可明顯提高污泥的過濾性能,其效果優(yōu)于先投加0.39g/L氯化鐵之后再加入等量石灰的效果。因為PAC改善污泥脫水性是不僅通過電中和絮凝作用,而且還通過吸附架橋來增強(qiáng)污泥絮體強(qiáng)度,并減小污泥黏性。
2.1.4 小試總結(jié)
按照污泥比阻SRF的大小將污泥分為三類:9.9×1011m/kg以上屬于難脫水污泥,3.9×1011~9.9×1011m/kg屬于中等可脫水污泥,3.9×1011m/kg以下屬于易脫水污泥。原始污泥的SRF為2.8×1012m/kg,屬難脫水污泥。單獨投加氯化鐵和PAC改善污泥的脫水性有限,在較優(yōu)投加量條件下,只可將污泥轉(zhuǎn)化為中等可脫水污泥,通過與石灰的復(fù)配投加后可將污泥轉(zhuǎn)化為易脫水污泥。
2.2 中試試驗結(jié)果
2.2.1 污泥脫水效果
單獨投加氯化鐵、PAC和石灰均可以實現(xiàn)有效脫水(污泥不會堵塞濾布)。單獨投加氯化鐵和PAC后污泥含水率較高,接近70%,二者分別與石灰復(fù)配后可有效降低污泥含水率,采用0.39g/L氯化鐵和0.32g/L PAC分別與0.64g/L石灰復(fù)配調(diào)理后,污泥含水率可降至60%左右。
2.2.2 水質(zhì)情況
對于所有中試試驗,除起始5min內(nèi),污泥清液濁度達(dá)7NTU以外,5min后壓濾全程清液濁度均<0.2NTU。從濁度來看,板框壓濾出水完全可以達(dá)到回用標(biāo)準(zhǔn)。整個壓濾過程可分為三個階段:充滿階段、濾餅層形成階段和壓緊階段。板框壓濾的充滿階段是依靠濾布來截留污泥固體,必然會導(dǎo)致一些固體顆粒無法截留,使得出水濁度偏高。5min后,污泥充滿濾室,會在濾布表面形成濾餅層,此時過濾方式發(fā)生轉(zhuǎn)化,由原來的依靠濾布截留轉(zhuǎn)化為憑借濾餅層過濾,從而濁度下降。
3 經(jīng)濟(jì)分析
采用離心機(jī)脫水后污泥含水率為80%,九廠每天產(chǎn)生含水80%的離心脫水污泥約90t,則年產(chǎn)生量為16425t。如采用板框壓濾機(jī)脫水后污泥含水率降至60%,意味著污泥量削減50%左右。若填埋處置的成本為300元(包含運費),一年節(jié)省污泥處置成本為900多萬。同時,隔膜壓濾清液可以實現(xiàn)回用,從而可節(jié)約大量水資源。
4 結(jié)論
本文結(jié)合使用高壓脫水技術(shù)及其適宜的污泥前調(diào)理過程對實現(xiàn)自來水廠污泥減量化和清液回用的可行性和效率進(jìn)行研究,結(jié)論如下:
(1)氯化鐵、PAC、石灰及其復(fù)配調(diào)理均可降低SRF。單獨投加氯化鐵和PAC調(diào)理的效果有限,只能將難脫水的原始污泥轉(zhuǎn)變?yōu)橹械瓤擅撍勰?,而單獨使用石灰會?dǎo)致脫水后絕干污泥量過大,故PAC和氯化鐵與石灰復(fù)配投加可更加高效地降低污泥比阻。
(2)中試結(jié)果顯示原始污泥脫水性較差,直接壓濾會堵塞濾布。氯化鐵、PAC、石灰及其復(fù)配進(jìn)行調(diào)理,均可實現(xiàn)污泥的有效脫水。但單獨投加氯化鐵或PAC后,脫水后的污泥含水率偏高,二者與石灰復(fù)配投加調(diào)理可進(jìn)一步降低污泥含水率。
(3)在所有中試試驗組中,除起始5min內(nèi),污泥清液濁度達(dá)到7NTU以外,5min后壓濾全程清液濁度均<0.2NTU。因此,隔膜清液可回用至飲用水處理過程中。