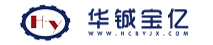
傳統(tǒng)的污泥處理處置技術(shù)復雜,處理設備多樣。其中,污泥干化耦合發(fā)電技術(shù)作為 鼓勵發(fā)展的一種污泥處理處置技術(shù),在國內(nèi)污泥處理市場占據(jù)重要地位。該技術(shù)利用電廠的熱源介質(zhì)對污泥進行干化,再協(xié)同燃煤焚燒發(fā)電,實現(xiàn)污泥無害化、穩(wěn)定化、減量化、資源化的“四化”目標,同時提升并利用污泥的熱值,降低電廠的煤炭消耗,減少碳排放。
污泥干化過程中產(chǎn)生的揮發(fā)性有機化合物如烷類、芳烴類、脂類以及惡臭氣體如NH3、H2S等的處理。不同于廢水和廢固的治理,這些惡臭氣體易逃逸、擴散性強、影響范圍廣、收集治理難度大。在已有的污泥干化項目應用中,無可避免地會有臭氣治理不理想的現(xiàn)象,這種現(xiàn)象同時也存在于其他污泥處理工程中,如污泥厭氧消化、污泥堆肥等。一方面,污泥存儲、干化、輸送等各個工藝環(huán)節(jié)都會產(chǎn)生惡臭廢氣,廢氣中含有的惡臭氣體如NH3、H2S等成分,雖然閾值較低,但是很容易引起周邊人員的身體不適;另一方面,臭氣的收集及處理系統(tǒng)的選擇存在不合理性。
臭氣的收集及處理技術(shù)的選擇直接影響著臭氣治理的效果。本文基于華東某電廠200t/d污泥干化耦合發(fā)電項目,介紹了污泥圓盤干化系統(tǒng)的設計、臭氣的收集及技術(shù)的選擇,結(jié)合本工程實際運行情況,提出改進建議,為類似工程項目提供借鑒。
1 臭氣處理工藝比選
1.1 臭氣處理方法分類
臭氣處理的方法主要包括:物理法、化學法和生無法。其中,物理法包括活性炭吸附法和吸收法;化學法包括等離子法、氧化法和焚燒法;生物法包括:生物過濾法、生物洗滌法及植物液法。
1.1.1 活性炭吸附法
活性炭吸附法一般適用于惡臭組分濃度較低,廢氣量大的環(huán)境,對苯系物及硫化物具有較好的脫除效果。
1.1.2 等離子法
等離子法是利用高壓電磁脈沖電暈放電,產(chǎn)生大量的高能電子、O、OH等活性粒子,將惡臭物質(zhì)進行氧化降解為微小或無害化的物質(zhì)。
1.1.3 焚燒法
焚燒法是利用高溫作用下,臭氣被分解產(chǎn)生CO2和H2O,達到除臭的效果。
1.1.4 生物過濾法
生物過濾法是利用附著在填料上的微生物作用,將臭氣物質(zhì)作為營養(yǎng)物質(zhì)進行吸收消化,進而達到對惡臭氣體的去除效果。但是,生物除臭效果較差,需結(jié)合活性炭法才可滿足深度脫臭的要求。
1.2 臭氣處理方法的選擇
主要從投資成本、運行成本、除臭效果、技術(shù)成熟度和除臭技術(shù)在應用過程的不利影響等方面進行綜合評判,選取合適的除臭技術(shù)。
從投資成本分析,新建除臭系統(tǒng)會增加整個項目的成本,而利用電廠鍋爐進行焚燒時,只需考慮污泥干化地點到鍋爐之間的管道成本,本項目利用玻璃鋼材質(zhì)風管進行輸送,且兩者之間的距離較短,成本投入較小。
從系統(tǒng)運行成本來看,活性炭法具有一定的使用周期,運行一段時間后,活性炭吸附效果下降,需定期更換活性炭材料,增加運行維護成本;生物過濾法在使用過程中也需定期更換填料。等離子法的電耗則相對較大;利用電廠進行焚燒臭氣,工藝簡單,電耗低,維護簡單,處理效果明顯且穩(wěn)定。
從除臭效果分析,無論是活性炭法、等離子法、生物濾池法,還是氧化法,對臭氣成分的處理具有選擇性,對臭氣濃度也有要求。對于鍋爐而言,幾乎不存在這樣的限制,鍋爐溫度高達1000℃,廢氣中的臭氣能完全被分解產(chǎn)生CO2和H2O。
從臭氣處理成熟度上考慮,各種技術(shù)在臭氣處理方面都有較多的應用,尤其是利用電廠鍋爐對臭氣進行焚燒。從除臭技術(shù)的不利影響來看,活性炭吸附需要考慮炭脫附,等離子法會產(chǎn)生臭氧污染,生物過濾法可能會因填料的腐化產(chǎn)生新的臭氣污染,而利用電廠鍋爐進行焚燒,臭氣成分被徹底分解,不會產(chǎn)生新的污染問題,且在處理過程中不會對鍋爐的原有系統(tǒng)產(chǎn)生不利影響。
綜上,利用電廠的鍋爐對污泥干化系統(tǒng)產(chǎn)生的臭氣進行焚燒處理是較佳選擇。
2 工程案例
2.1 工程概況
華東某電廠現(xiàn)役二、三期4×330MW燃煤機組,采用亞臨界汽包鍋爐汽輪發(fā)電、雙曲線冷卻塔-循環(huán)水冷卻、電除塵-氣力干除灰、水冷渣-鏈條式輸送、石灰石-石膏濕法脫硫,該機組于2005年投運。
為滿足電廠發(fā)展戰(zhàn)略及當?shù)丨h(huán)保需求,電廠接納當?shù)匚鬯畯S轉(zhuǎn)運來的板框壓濾污泥,其含水率在55%~65%之間。
根據(jù)當?shù)匚勰嗵幚硖幹玫囊?,電廠規(guī)劃建設2條污泥干化生產(chǎn)線,單條污泥干化生產(chǎn)線處理規(guī)模為每天100t含水率60%污泥。污泥消納采用的技術(shù)路線:首先通過圓盤干化技術(shù)將污泥的含水率干化至35%,然后干化后的污泥輸送至輸煤皮帶于燃煤混合后,作為燃料進入爐膛燃燒發(fā)電。
其中,圓盤干化系統(tǒng)由幾個子系統(tǒng)組成,包括濕污泥存儲與輸送系統(tǒng)、干化系統(tǒng)、干污泥存儲輸送系統(tǒng)、干污泥上料摻配系統(tǒng)、蒸汽輸送及疏水回用系統(tǒng)、廢氣收集處理系統(tǒng)、冷凝廢水處理系統(tǒng)、循環(huán)冷卻水系統(tǒng)及DCS控制系統(tǒng)。
2.2 圓盤干化系統(tǒng)臭氣源分析
圓盤干化系統(tǒng)廢氣主要產(chǎn)生于3個過程:儲存過程、輸送過程及干化過程。首先,濕污泥料倉內(nèi)的污泥存儲過程中,發(fā)生消化反應,產(chǎn)生以NH3、H2S為主的惡臭氣體,同時產(chǎn)生少量的醇類、胺類等有機臭氣。污泥輸送過程,由于污泥發(fā)生擾動,污泥與污泥之間裹挾的臭氣被釋放,成分與儲存過程產(chǎn)生的臭氣相似。
污泥干化過程中,產(chǎn)生的廢蒸汽臭氣濃度較高,成分較復雜,一方面污泥中原來含有的低沸點的臭氣成分被釋放;另一方面,高分子氣體被分解產(chǎn)生含臭味的低分子氣體。
2.3 圓盤干化系統(tǒng)臭氣收集及處理工藝
整套系統(tǒng)以定點微負壓和整體微負壓相結(jié)合的方式進行臭氣收集。
定點負壓是在系統(tǒng)運行下,保證干化機內(nèi)部-100~500Pa的微負壓,濕/干污泥儲存及輸送設備內(nèi)部微負壓,避免臭氣向周圍環(huán)境逃逸。但是,在污泥卸料和輸送過程中臭氣無可避免地會從設備內(nèi)逃逸到廠房內(nèi),故廠房內(nèi)采取整體微負壓設計,維持廠房內(nèi)機械排風,自然進風,避免臭氣進一步擴散到周邊環(huán)境。結(jié)合現(xiàn)場情況,臭氣的收集工作主要分為三部分。
部分:兩條生產(chǎn)線的干化工藝尾氣,通過除塵冷凝后通過同一臺離心風機輸送至鍋爐前端的送風機入口。
第二部分:濕污泥卸料車間、污泥干化車間、濕污泥/干污泥料倉、濕污泥輸送、干污泥輸送等設備相對集中,利用同一離心風機將臭氣收集并輸送至鍋爐前端的送風機入口。
第三部分:干污泥上料系統(tǒng)中污泥輸送距離長度達300m,輸送高度32m,利用同一臺離心風機收集上料系統(tǒng)設備內(nèi)部臭氣,并將收集的臭氣輸送至鍋爐前端的送風機入口。污泥干化系統(tǒng)產(chǎn)生的所有臭氣送入鍋爐進行焚燒處置。
2.4 圓盤干化系統(tǒng)臭氣處理效果
根據(jù)現(xiàn)場測定,污泥干化生產(chǎn)車間周邊環(huán)境無臭味逃逸,滿足《惡臭污染物排放標準》惡臭污染物濃度限制要求。車間內(nèi)有毒有害氣體及粉塵等衛(wèi)生條件滿足《工業(yè)企業(yè)設計衛(wèi)生標準》以及《工作場所有害因素職業(yè)接觸限值》等相關(guān)標準。電廠大氣污染物排放也符合相關(guān)標準要求。
3 結(jié)論與建議
3.1 結(jié)論
整個污泥圓盤干化系統(tǒng)可以將污泥的含水率從60%降至35%,各子系統(tǒng)穩(wěn)定運行,同時干污泥輸送系統(tǒng)的設計實現(xiàn)了長距離及較高高度輸送,系統(tǒng)運行過程中廠房周邊臭氣排放滿足相關(guān) 標準,廠房內(nèi)臭氣有效抽吸處理,保證系統(tǒng)運行時人員健康。
利用電廠鍋爐對污泥在存儲、輸送、干化過程中產(chǎn)生的廢氣進行焚燒,可有效分解廢氣中的臭氣組分,同時可節(jié)約電廠的投資及運行成本。另外,對于電廠的鍋爐及超低排放環(huán)保設備的運行不會產(chǎn)生影響。
3.2 建議
廠房內(nèi)部臭氣收集效果具有一定的局限性,通過增加換氣次數(shù)進行廠內(nèi)臭氣的收集有明顯效果,但相應地會增加風機功耗,如果風機能耗有較大限制,則應嚴格控制系統(tǒng)設備的密封性和微負壓狀態(tài),減少設備本體及連接件臭氣的逃逸及無組織排放。通過本項目在運行過程中的調(diào)整,每小時8~10次換氣量能達到 的效果。
利用定點抽吸方式,針對污染臭氣源進行定點抽吸,能有效防止臭氣向四周擴散,同時減少系統(tǒng)抽風量,降低風機運行能耗。