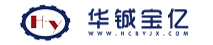
1 離心機(jī)主電機(jī)系列故障經(jīng)過(guò)
1.1 第一次離心機(jī)主電機(jī)故障停車(chē)及處理經(jīng)過(guò)
該離心機(jī)為德國(guó)威斯伐利亞離心機(jī),型號(hào)為UCC450-00-32,第一次故障發(fā)生在4月14日凌晨0:30分,車(chē)間班組巡檢發(fā)現(xiàn)離心機(jī)自停,并顯示“轉(zhuǎn)鼓主機(jī)失效”報(bào)警信息,發(fā)現(xiàn)主電機(jī)發(fā)燙,現(xiàn)場(chǎng)有燒焦的糊味。電工檢查確認(rèn)主電機(jī)抱軸,盤(pán)車(chē)不動(dòng)。遂將離心機(jī)斷電,緊急聯(lián)系拆運(yùn)搶修,解體打開(kāi)電機(jī)前后端蓋,發(fā)現(xiàn)軸承抱死,軸承內(nèi)沒(méi)有潤(rùn)滑油,軸承端蓋內(nèi)孔損壞,測(cè)量軸直線(xiàn)度,撓度為3~5mm,并發(fā)現(xiàn)軸有裂紋現(xiàn)象,采取的措施是在裂紋處用液壓鋸將電機(jī)軸割開(kāi)一分為二,兩處軸頭端面切削為錐形端面,軸心處做連接螺栓,以實(shí)現(xiàn)軸向定位,兩半軸采用J507焊條進(jìn)行堆焊后,車(chē)削加工處理,更換工廠提供的SKF6210軸承兩套,軸承內(nèi)加注二硫化鉬鋰基脂,電機(jī)組裝完畢后,于4月17日進(jìn)行回裝,在檢查了各裝配精度及要求后,開(kāi)啟運(yùn)行離心機(jī),運(yùn)行正常。
1.2 第二次離心機(jī)主電機(jī)故障停車(chē)及處理經(jīng)過(guò)
4月28日凌晨5:00,班組巡查發(fā)現(xiàn)離心機(jī)主電機(jī)再次出現(xiàn)故障,現(xiàn)象與之前完全一樣,水洗后離心機(jī)無(wú)法啟動(dòng),顯示屏報(bào)警信息仍是“轉(zhuǎn)鼓主機(jī)無(wú)效”,機(jī)電儀等相關(guān)人員確認(rèn)離心機(jī)主電機(jī)抱軸,第二次拆走維護(hù),檢查后與第一次癥狀一樣,測(cè)量軸的撓度為0.2mm,采取措施是車(chē)削去除0.25mm材料,之后刷鍍0.25mm,恢復(fù)軸原先尺寸,前軸承由6210球軸承更換為NU210滾柱軸承,后軸承為6210軸承,并加注3#鋰基潤(rùn)滑脂,至29日回裝,22:30分離心機(jī)開(kāi)啟運(yùn)行,設(shè)備運(yùn)行平穩(wěn),狀態(tài)正常。
1.3 第三次離心機(jī)主電機(jī)故障停車(chē)及處理經(jīng)過(guò)
5月2日班組巡檢發(fā)現(xiàn)離心機(jī)停車(chē),無(wú)法再次啟動(dòng),亦無(wú)法水洗。當(dāng)時(shí)顯示屏顯示“Failure solids conveyor”。機(jī)電儀三方確認(rèn)離心機(jī)主電機(jī)軸斷裂,軸頭斷裂,軸承保持架散架,軸承內(nèi)沒(méi)有潤(rùn)滑油,軸承端蓋損壞,因電機(jī)主軸已無(wú)法使用,需加工一新軸,材質(zhì)為27SIMn,電機(jī)前軸承安裝NU210滾柱軸承,后軸承安裝6210球軸承,至5月6日離心機(jī)主電機(jī)組裝完畢,空試10小時(shí),測(cè)試正常后裝機(jī)投用,7日上午離心機(jī)開(kāi)啟運(yùn)行,運(yùn)行狀態(tài)及數(shù)據(jù)正常。
1.4 第四次離心機(jī)主電機(jī)故障停車(chē)及處理經(jīng)過(guò)
5月15日18:00左右,運(yùn)行班組巡檢再次發(fā)現(xiàn)離心機(jī)自停,遂對(duì)自停原因進(jìn)行檢查,將離心機(jī)擋板及齒輪箱端蓋打開(kāi)發(fā)現(xiàn)主電機(jī)斷裂,轉(zhuǎn)鼓盤(pán)車(chē)不動(dòng),皮帶解除后對(duì)離心機(jī)轉(zhuǎn)鼓進(jìn)行盤(pán)車(chē),轉(zhuǎn)鼓回轉(zhuǎn)正常,鑒于多次故障,第四次故障后,經(jīng)過(guò)技術(shù)分析討論后,采購(gòu)新電機(jī),組裝后試運(yùn)行正常,目前運(yùn)行至今。
2 離心機(jī)主電機(jī)系列故障原因分析
此次離心機(jī)系列故障從4月14日第一次故障至5月15日第四次故障停車(chē),出現(xiàn)四次系列故障停車(chē),從中可發(fā)現(xiàn)四個(gè)共同點(diǎn),即四次均出現(xiàn)了電機(jī)前端軸承抱死、軸承無(wú)油、前端軸承均出現(xiàn)高溫、故障前工藝流程未有大的變動(dòng)等共性問(wèn)題;四個(gè)不同點(diǎn),即軸承型式、軸承潤(rùn)滑、軸、斷口在四次故障中有所不同。前三次故障為原電機(jī)軸,第四次故障為加工的新軸;端口位置不同表現(xiàn)為第一次斷軸位置在電機(jī)前軸承外,第二次斷軸位置在前軸承位上。
第一次斷軸從斷口觀察,其瞬斷區(qū)和擴(kuò)展區(qū)較為明顯,可判定為疲勞斷裂,第二次斷軸其端口因軸頭磨損其瞬斷區(qū)和擴(kuò)展區(qū)不明顯。電機(jī)主軸斷裂無(wú)外乎幾方面因素所致:1、軸材料問(wèn)題;2、軸加工問(wèn)題;3、軸承問(wèn)題;4、安裝問(wèn)題;5、載荷問(wèn)題;6、潤(rùn)滑問(wèn)題;7、失穩(wěn)問(wèn)題;8、異物卡阻問(wèn)題;9、皮帶問(wèn)題;10、差速器問(wèn)題?,F(xiàn)一一分析如下:
2.1 軸材料問(wèn)題
本次離心機(jī)系列故障前兩次表現(xiàn)為軸承損壞,但與軸本身都有關(guān)系,第一次故障檢查后已發(fā)現(xiàn)軸有裂紋,且軸撓度達(dá)3~5mm,但軸未斷裂,說(shuō)明原電機(jī)軸強(qiáng)度是沒(méi)有問(wèn)題的,即使在軸承抱死、軸嚴(yán)重彎曲的情況下,軸的材料強(qiáng)度依然保證了離心機(jī)的運(yùn)轉(zhuǎn)。但是第一次處理過(guò)程中軸經(jīng)過(guò)割裂、堆焊、車(chē)削處理,已改變軸的力學(xué)性能。其焊材與母材熔合后的材料力學(xué)已發(fā)生了改變,其強(qiáng)度、剛度、韌性、抗剪切力等力學(xué)指標(biāo)一定改變,在第二次故障處理過(guò)程中,經(jīng)過(guò)車(chē)削和刷鍍后,力學(xué)性能再次發(fā)生改變;在第三次加工新軸過(guò)程中,并沒(méi)有采用常用的45#鋼,而是采用的27SIMn,軸材質(zhì)又發(fā)生了改變,當(dāng)然其力學(xué)性能也隨之改變,更換新軸后其剛度、強(qiáng)度是否符合要求,安全裕度是否符合要求,P、S、H等這些易引起軸斷裂的有害材料成分及SI、Mn等有益成分是否符合要求等并未進(jìn)行檢測(cè)分析,所以我們有理由懷疑軸的材料不符合要求是導(dǎo)致第二次斷軸的這一重要論斷。
2.2 軸加工問(wèn)題
前三次故障處理過(guò)程都涉及到軸的加工,第一次涉及車(chē)、銑、鉆加工、電氣焊加工,第二次涉及車(chē)削加工、刷鍍;第三次涉及車(chē)削加工,在每一加工過(guò)程中極易造成應(yīng)力集中問(wèn)題的出現(xiàn),譬如說(shuō)在熱加工過(guò)程中如何控制馬氏體的形成,降低焊接殘余應(yīng)力、避免應(yīng)力集中,危險(xiǎn)截面的出現(xiàn),車(chē)削加工中如何控制車(chē)削量、何處設(shè)計(jì)退刀槽,每一次的車(chē)、銑、鉆、焊、鍍都是對(duì)軸的“傷筋動(dòng)骨”的手術(shù),特別是軸表面加工處理,因軸的表面是受應(yīng)力較大區(qū)域,軸中心受應(yīng)力較小,在前兩次軸的處理過(guò)程中,加工過(guò)程中都涉及到不同材料的疊加,在其結(jié)合面,仔細(xì)觀察第一次斷口的表面特征,會(huì)發(fā)現(xiàn)軸的中心為瞬斷區(qū),裂紋發(fā)生和擴(kuò)展正處于兩種材料的結(jié)合部,在第一次故障后已發(fā)現(xiàn)軸有裂紋,盡管軸已彎曲3~5mm,但因原軸的材料強(qiáng)度、韌性較好,未發(fā)生斷裂,在第一、二次經(jīng)過(guò)堆焊、車(chē)削、刷鍍過(guò)程中,軸的內(nèi)部危險(xiǎn)裂紋并未徹底消除,反而出現(xiàn)了在經(jīng)過(guò)第二次軸的加工修復(fù)后,第三次出現(xiàn)了端軸事故,可以這么說(shuō),前三次離心機(jī)故障是軸的強(qiáng)度、韌性、抗剪切力不斷劣化的一個(gè)過(guò)程,只是在第三次軸以斷裂的破壞形式出現(xiàn),所以說(shuō),軸的加工處理是導(dǎo)致軸斷裂的一個(gè)重要因素。
2.3 軸承問(wèn)題
在三次電機(jī)軸處理過(guò)程中,軸承都出現(xiàn)了無(wú)油抱死粘連情況,并更換了不同型號(hào)軸承,軸承全部為正規(guī)渠道提供,前期通過(guò)外觀檢查、狀態(tài)及溫度檢測(cè),可以排除軸承的質(zhì)量問(wèn)題。每次離心機(jī)故障,檢查軸承全部抱死、無(wú)油,這說(shuō)明軸在斷裂前軸承溫度異常高,但在日常檢測(cè)過(guò)程中卻未發(fā)現(xiàn),實(shí)際上軸在斷裂前是一個(gè)快速劣化過(guò)程,從危險(xiǎn)裂紋的形成、擴(kuò)展直至斷裂這個(gè)過(guò)程很短,在這個(gè)過(guò)程中因?yàn)檩S的扭轉(zhuǎn)導(dǎo)致軸不同心可使支撐位軸承溫度急劇升高,特別是在第二次斷軸過(guò)程中,斷口正處于軸承內(nèi)圈位置,更是導(dǎo)致了軸承的高溫,軸承內(nèi)的潤(rùn)滑油在高溫下發(fā)生泄漏甚至汽化,橡膠材質(zhì)的油封高溫下出現(xiàn)焦化現(xiàn)象,這也就是為什么斷軸后操作工現(xiàn)場(chǎng)聞到“糊味”的原因。所以軸的劣化、扭轉(zhuǎn)是導(dǎo)致軸承損壞的原因,這是一個(gè)因果關(guān)系,而不是軸承的缺陷導(dǎo)致軸的斷裂。
2.4 安裝問(wèn)題
安裝設(shè)計(jì)有兩個(gè)問(wèn)題,一是電機(jī)皮帶輪與轉(zhuǎn)鼓皮帶輪的對(duì)中,另一個(gè)是電機(jī)底板的平面度。對(duì)于皮帶輪的對(duì)中,是由皮帶輪在電機(jī)軸上的位置及電機(jī)的相對(duì)位置決定的,可調(diào)整量非常有限,對(duì)中要求是盤(pán)車(chē)過(guò)程中,皮帶應(yīng)正確入皮帶輪槽內(nèi),外緣與輪槽無(wú)過(guò)渡擠壓,盤(pán)車(chē)聯(lián)動(dòng)運(yùn)轉(zhuǎn)靈活;皮帶的張緊度以按壓皮帶中部,其撓度在20mm左右為宜,電機(jī)底板平面度以水平儀檢測(cè)為準(zhǔn)。在歷次離心機(jī)檢修過(guò)程中,電機(jī)底板及皮帶輪基本按照上述原則進(jìn)行。假設(shè)電機(jī)與轉(zhuǎn)鼓皮帶輪不在一個(gè)垂直立面上,若錯(cuò)位距離較小,則皮帶輪的外緣會(huì)出現(xiàn)磨損,錯(cuò)位距離較大,則離心機(jī)在開(kāi)車(chē)過(guò)程中,就極有可能發(fā)生皮帶轉(zhuǎn)動(dòng)脫落或斷裂的情況,但這兩種情況都沒(méi)有發(fā)生,在第一次斷軸過(guò)程中,對(duì)每條皮帶進(jìn)行擦拭檢查,除了第一次斷軸后,有一條皮帶因軸斷裂出現(xiàn)磕碰損傷外,其它皮帶均處于正常可用范圍,因此可排除此安裝問(wèn)題。
2.5 載荷問(wèn)題
在前兩次軸的加工過(guò)程中,因軸材料特別是危險(xiǎn)截面上的材料發(fā)生了改變,且車(chē)、銑、焊、鍍等加工工藝已改變了材料的力學(xué)性能,特別是第二次采用27SIMn材質(zhì)加工新軸過(guò)程中,未對(duì)軸加工前后進(jìn)行熱處理、表面強(qiáng)化處理及化學(xué)處理措施,以提高軸的抗疲勞和抗剪切強(qiáng)度。由于受條件所限,未對(duì)加工后的軸進(jìn)行材料成分分析及力學(xué)性能測(cè)試。從離心機(jī)的運(yùn)行參數(shù)分析,從4月14至5月15日離心機(jī)運(yùn)行期間,處理泥量基本上在7~12立方每小時(shí)范圍內(nèi),系列故障之前處理泥量長(zhǎng)期在12~16立方每小時(shí)范圍內(nèi),說(shuō)明外部載荷并沒(méi)有額外增加,可排除載荷問(wèn)題引起的故障。
2.6 潤(rùn)滑問(wèn)題
整個(gè)離心機(jī)系統(tǒng)有5處潤(rùn)滑點(diǎn),在運(yùn)行檢測(cè)過(guò)程中并未出現(xiàn)轉(zhuǎn)鼓前后軸承端溫度升高跡象,基本上在40℃左右,所以離心機(jī)本體內(nèi)因潤(rùn)滑不暢導(dǎo)致轉(zhuǎn)矩增大進(jìn)而電機(jī)斷軸的可能性也可以排除。
2.7 失穩(wěn)問(wèn)題
離心機(jī)是通過(guò)介質(zhì)密度不同產(chǎn)生不同的離心力實(shí)現(xiàn)泥水分離,所以對(duì)轉(zhuǎn)子的動(dòng)平衡是有要求的,離心機(jī)在出廠前對(duì)螺旋、轉(zhuǎn)鼓分別進(jìn)行動(dòng)平衡測(cè)試,并且組裝完畢后還需要對(duì)整體進(jìn)行平衡測(cè)試。失穩(wěn)是不是導(dǎo)致電機(jī)軸斷裂的主因,可通過(guò)假設(shè)法反推一下:假設(shè)離心機(jī)轉(zhuǎn)子不平衡度增大,則離心機(jī)本體、轉(zhuǎn)鼓前后軸承端及電機(jī)的震動(dòng)和烈度一定能通過(guò)測(cè)振儀檢測(cè)出來(lái),但這與我們實(shí)際檢測(cè)數(shù)據(jù)是不符的,在提高離心機(jī)震幅、烈度及溫度的檢測(cè)力度與檢測(cè)頻度,不同人員不同儀器對(duì)比檢測(cè),震幅檢測(cè)數(shù)據(jù)基本在0.02~0.05mm區(qū)間波動(dòng),符合震幅小于0.06mm的優(yōu)良運(yùn)行狀況;另外烈度的檢測(cè),廠家要求是12mm/s以下,實(shí)際檢測(cè)數(shù)據(jù)都在2~5mm/s波動(dòng),截獲的烈度數(shù)據(jù)7.2mm/s,也是完全滿(mǎn)足廠家運(yùn)行要求的;二是甩泥環(huán)處4條螺栓沖刷導(dǎo)致的離心機(jī)失穩(wěn)也是不太可能的,甩泥口和分離水口的甩泥環(huán)、螺栓、堰板等受到固液介質(zhì)的沖刷是正常的。實(shí)際上,螺栓沖刷較甩泥環(huán)出泥導(dǎo)致的轉(zhuǎn)子不平衡度要小很多,在每一次出泥瞬間,出泥是通過(guò)下端的一個(gè)甩泥環(huán)實(shí)現(xiàn)的,此處甩泥環(huán)積聚的污泥較多,在轉(zhuǎn)鼓高速旋轉(zhuǎn)的過(guò)程中,此處產(chǎn)生的不平衡力較之螺栓堰板沖刷引起的不平衡度要大很多,因此通過(guò)分析推理可排除失穩(wěn)問(wèn)題引起的主電機(jī)斷軸這一論斷。
2.8 異物卡阻問(wèn)題
離心機(jī)主要處理浮選產(chǎn)生的浮渣、底泥、剩余活性污泥及隔油池內(nèi)浮渣、底泥,通過(guò)管道進(jìn)泥罐攪拌均勻后,進(jìn)離心機(jī)轉(zhuǎn)鼓前要通過(guò)3道過(guò)濾器過(guò)濾,所以出現(xiàn)異物卡阻導(dǎo)致斷軸的可能性非常小,且在歷次離心機(jī)檢查維護(hù)過(guò)程中均未出現(xiàn)異物卡阻問(wèn)題 ,故此項(xiàng)原因可排除。
2.9 皮帶及差速器問(wèn)題
皮帶問(wèn)題在2.4 安裝問(wèn)題中已闡述,此處不再贅述。關(guān)于差速器問(wèn)題導(dǎo)致斷軸的可能性也非常小,如果說(shuō)差速器內(nèi)出現(xiàn)偏心軸承損壞或軸套開(kāi)裂等嚴(yán)重情況,會(huì)立刻出現(xiàn)兩種后果,一是轉(zhuǎn)鼓盤(pán)車(chē)異響,二是盤(pán)車(chē)卡阻,但這兩種情況在系列故障中都沒(méi)有出現(xiàn),且每次電機(jī)安裝后離心機(jī)都能實(shí)現(xiàn)開(kāi)車(chē),運(yùn)行檢測(cè)中也未發(fā)現(xiàn)數(shù)據(jù)及聲音異常。所以說(shuō)差速器問(wèn)題引起的斷軸可能是不存在的。
綜合以上問(wèn)題研判,此次離心機(jī)系列故障是由電機(jī)主軸引起的,從第一次軸彎曲3~5mm到第二次軸彎曲0.2mm,再到第三次軸發(fā)生斷裂破壞,這一過(guò)程是有著前后緊密聯(lián)系的,在前三次故障處理過(guò)程中,因?qū)S的加工處理及過(guò)程控制不當(dāng)導(dǎo)致了軸強(qiáng)度、剛度改變,在第三次事故中以疲勞斷裂的破壞形式出現(xiàn),在第四次故障即第二次電機(jī)斷軸過(guò)程中,因?qū)S材料選型、加工處理不當(dāng)才導(dǎo)致了第二次電機(jī)斷軸的發(fā)生。
3 預(yù)防性措施
由于離心機(jī)的技術(shù)集成度高,對(duì)運(yùn)行和維護(hù)有嚴(yán)格要求,對(duì)材料加工和安裝有嚴(yán)格限定,所以在日常操作中,應(yīng)嚴(yán)格按照操作手冊(cè)進(jìn)行,特別是設(shè)備開(kāi)停車(chē)過(guò)程中,做好設(shè)備和管道的清洗工作;在日常維護(hù)中,應(yīng)按照廠家的維護(hù)手冊(cè)做好設(shè)備的潤(rùn)滑保養(yǎng),狀態(tài)檢測(cè)及清理盤(pán)車(chē)等工作,涉及軸的加工修復(fù)等改變材料屬性及力學(xué)性質(zhì)時(shí),應(yīng)謹(jǐn)慎處理,做好材料選型、加工處理、力學(xué)校核試驗(yàn)等工作。
4 結(jié)論
自動(dòng)離心脫水機(jī)的平穩(wěn)運(yùn)行至關(guān)重要,在運(yùn)行、維護(hù)及故障處理過(guò)程中,只有嚴(yán)格按照操作及維護(hù)手冊(cè),做好日常維護(hù)保養(yǎng)及運(yùn)行,在故障處理中做好故障綜合研判和技術(shù)分析,才能確保故障的有效解決,從而保證離心機(jī)的安穩(wěn)長(zhǎng)期運(yùn)行。