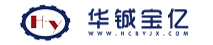
1 前言
煉油廠廢水處理過程不可避免地產(chǎn)生大量的隔油池底泥、溶氣浮選浮渣及剩余活性污泥等,它們統(tǒng)稱為煉油廠“三泥”。這些污泥由不同含量的油、水及固體物組成,是高濃度的污染物,對環(huán)境具有極大的危害性。國內(nèi)外廣泛研究的“三泥”無害化處理技術(shù),主要有焚燒、生物降解、溶劑萃取及送焦化處理等,然而這些技術(shù)在經(jīng)濟(jì)、技術(shù)及設(shè)備運(yùn)行維護(hù)等方面均存在諸多不足。國內(nèi)煉油廠一般采用濃縮-機(jī)械脫水-焚燒的方法處理含油污泥,焚燒每噸污泥的費(fèi)用高達(dá)300~500元,并且設(shè)備故障率高。近年來,某些煉油廠將機(jī)械脫水后的污泥直接送入焦化裝置,作為急冷油或作為急水使用。但這種方法具有一定的局限性,原因之一是污泥中仍含有大量水,易對焦化操作產(chǎn)生影響,焦化的處理能力低,不能將三泥全部處理掉;另外是某些煉油廠,或者焦化裝置生產(chǎn)高品級石油焦,或者沒有焦化裝置,無法采用此法對污泥進(jìn)行處理。多年來,國內(nèi)一直沒有一個技術(shù)與經(jīng)濟(jì)可行的處理手段,大多數(shù)企業(yè)仍采取將污泥轉(zhuǎn)移給小企業(yè)進(jìn)行處置的方式為主。由于環(huán)保法規(guī)的日趨嚴(yán)格,污泥處理成為企業(yè)環(huán)保達(dá)標(biāo)的難題之一,嚴(yán)重制約著企業(yè)生產(chǎn)的發(fā)展。
針對三泥處理問題,撫順石油化工研究院經(jīng)過多年探索性研究工作,開發(fā)成功了“熱萃取/脫水”處理技術(shù)。該技術(shù)從資源回收與環(huán)境保護(hù)的角度出發(fā),在脫除污泥中水分的同時,將固體物全部轉(zhuǎn)移至溶劑油中,使污泥在有價值組分得到了全部回收。萃取后的產(chǎn)物,因不含水分,既可以直接作為焦化的原料加以利用,同時也采用固液分離方式,進(jìn)行處理。固液分離后的溶劑油,無需再生,可直接回用于“熱萃取/脫水”裝置。形成的固體物,其體積僅為原污泥量的一小部分,可采用多種途徑加以利用,如按比例混入焦化原料中或采用輕溶劑洗脫,回收有和的組分;也可以作為燃料使用,其熱值高達(dá)8452.1Cal/g。試驗(yàn)結(jié)果表明,該技術(shù)處理效果穩(wěn)定、經(jīng)濟(jì)合理,與目前常規(guī)處理技術(shù)相比具有明顯的優(yōu)勢。
2 “三泥”物性指標(biāo)的分析
對于“三泥”中水分的分析,起初引用的方法是在105~110℃下的烘干法,而油含量的分析是以重量法為基礎(chǔ)的。烘干法雖然能測出樣品中的全部水分,但在測定過程中,不可避免地存在著有機(jī)質(zhì)的揮發(fā)、分解,使測定結(jié)果失真。根據(jù)中石化環(huán)保監(jiān)測總站建立的“石油化工廠廢渣中含水率測定方法”、“石油化工廠廢渣中含油量測定方法”、以及BG/T260-77,相應(yīng)建立了“煉油廠三泥中水分的測定方法”、“煉油廠三泥中石油醚萃取物的測定方法”、以及“600℃固體物灼燒殘?jiān)臏y定方法”等三個分析方法,作為污泥組成分析。其中含水率和石油醚萃取物均采用蒸餾法,比烘干法和重量法能更準(zhǔn)確測定出“三泥”中的水和油含量。采用上述分析方法,對數(shù)家煉油廠的三泥組成進(jìn)行了分析,結(jié)果如表1。
表1:不同煉油廠含油污泥組成分析結(jié)果
污泥來源 | 石油二廠 | 茂名石化 | 烏石化 | 上海煉油廠 |
含油率/% | 11.3 | 5.0~13.0 | 45.0 | 0.9 |
含水率/% | 84.4 | 80.0~90.0 | 43.9 | 95.9 |
600℃灼燒殘?jiān)?% | 1.1 | 2.0~4.0 | 7.6 | 2.1 |
從組成分析結(jié)果可知,由于污泥來源不同,其組成差別很大。另外,在分析中發(fā)現(xiàn),每一種污泥的三項(xiàng)組分之和,并不等于百分之百,說明污泥組成上還存在著非石油醚萃取物、且在600℃灼燒下易揮發(fā)的物質(zhì),將其定義為“揮發(fā)性物質(zhì)”。
3 試驗(yàn)內(nèi)容及結(jié)果
3.1 燒杯試驗(yàn)
通過間歇式燒杯試驗(yàn)考察了“熱萃取/脫水”技術(shù)的可行性,試驗(yàn)結(jié)果表明,在適當(dāng)?shù)牟僮鳁l件下,該技術(shù)可完全脫出污泥中水分,并回收污泥中的油,處理后的固體物僅為原污泥的一小部分,并具有可利用價值。燒杯試驗(yàn)過程:
(1)將一定比例的萃取溶劑油及污泥置入蒸餾燒瓶。
(2)用電爐加熱蒸餾瓶,使污泥中水分蒸發(fā),同時記錄餾出溫度及蒸餾瓶液體溫度。
(3)對蒸餾瓶蒸發(fā)出的水蒸氣及輕質(zhì)油蒸汽冷凝,收集并記錄餾出水及油的體積。
(4)從蒸餾瓶中移出脫水后的固體與溶劑油的混合物。
(5)采用抽濾設(shè)備對混合物進(jìn)行固液分離,并對固體物及溶劑油進(jìn)行稱重。
(6)分析脫出水中油含量及固體物組成等。
3.1.1 不同油/泥比的處理結(jié)果
表2:不同油/泥比對固體物組成的影響
溶劑油/污泥 | 固體物組成/% | |||
體積比 | 含油率 | 含水率 | 揮發(fā)性物質(zhì) | 灼燒殘?jiān)?/span> |
0.25/1 | 26.1 | 64.1 | 3.0 | 6.8 |
0.5/1 | 30.9 | 62.4 | - | 8.5 |
0.75/1 | 48.2 | 14.8 | 11.3 | 25.7 |
1/1 | 52.3 | 未檢出 | 24.5 | 23.1 |
2/1 | 53.0 | 未檢出 | 24.0 | 23.0 |
固體物中水分隨溶劑用量減少而增大。在油/泥比大于1的情況下,污泥脫水完全,固體物不含水,可燃性好。
3.1.2 溶劑循環(huán)使用的處理結(jié)果
在溫度一定及油/泥比固定為1/1的條件下,考察了溶劑油直接循環(huán)使用的可行性。新鮮溶劑油為茂名公司沙中二線油(沸程范圍約為212~320℃),處理對象分別為板框壓濾后的“三泥”(組成:油含量13.5%,固含量6.0%,水含量80.5%)及浮選池浮渣(組成:油含量10.3%,固含量3.4%,水含量86.3%)。溶劑油循環(huán)使用10次過程中,脫出水中油含量平均為31.3mg,固體物組成及固體物產(chǎn)率的分析結(jié)果如表3及表4。
表3:溶劑油循環(huán)使用時的固體物組成
三泥來源 | 固體物組成 | 10次循環(huán)范圍值 | 平均值 |
混合三泥 | 含油率/% | 56.7~64.3 | 61.2 |
含水率/% | 未檢出 | 未檢出 | |
揮發(fā)性物質(zhì)/% | 10.1~15.7 | 13.2 | |
灼燒殘?jiān)?/span>/% | 23.6~27.6 | 25.2 |
表4:溶劑油循環(huán)使用時污泥產(chǎn)固率測定結(jié)果
項(xiàng)目 | 混合三泥產(chǎn)固率/% | 浮渣產(chǎn)固率/% |
十次試驗(yàn)范圍值 | 12.8~17.6 | 7.0~8.1 |
平均值 | 15.2 | 7.6 |
無論是處理板框壓濾后的“三泥”,還是浮選池表面采集的浮渣,溶劑油直接循環(huán)使用后,在處理效果上均未產(chǎn)生明顯的變化,表明了該技術(shù)中所使用的溶劑無需頻繁再生,可直接循環(huán)使用。形成的固體物均不含有水分,可燃性好,并且固體物量-污泥相比分別減少了85%和92%。
3.2 小試處理裝置驗(yàn)證試驗(yàn)
3.2.1 工藝流程
根據(jù)燒杯試驗(yàn)結(jié)果及試驗(yàn)過程中確定的脫水溫度、溶劑比、脫水速率等參數(shù),設(shè)計(jì)了一套“熱萃取/脫水”小試連續(xù)處理裝置。污泥與溶劑油,首先在油漿罐內(nèi)混合成具有一定流動性的混合物。該混合物經(jīng)預(yù)熱后,進(jìn)入“熱萃取/脫水”塔,并在塔內(nèi)溫度作用下,同時進(jìn)行破乳、萃取和脫水三個過程。從“熱萃取/脫水”塔出來的水及輕質(zhì)溶劑油,經(jīng)油水分離后,水排出系統(tǒng),油返回油漿罐中。在水分脫出的同時,塔內(nèi)的固體物及溶劑油混合物,不斷地進(jìn)入沉降罐進(jìn)行固液分離。沉降后的固體物從裝置中排出,溶劑油直接返回油漿罐中,進(jìn)行下一次處理過程。
3.2.2 試驗(yàn)結(jié)果
小試裝置試驗(yàn)過程中所使用的溶劑為粗柴油,循環(huán)使用15次,處理對象為采自茂名公司煉油廠的浮油,其組成為含油量9.28%、含水量87.59%、含固量為3.13%。
試驗(yàn)過程中對操作條件進(jìn)行了考察并在較佳條件下進(jìn)行了穩(wěn)定性試驗(yàn)。試驗(yàn)結(jié)果驗(yàn)證了燒杯試驗(yàn)所得出結(jié)論:脫水完全徹底,溶劑油無需再生,可直接循環(huán)使用;沉降分離后的固體物中均未檢出水,含油量平均值為65.9%,熱值為8452.1 kCal/G;污泥產(chǎn)固率平均值為10.5%;脫除水含油量在10.0~28.8mg/L之間,水中COD為130mg/L。
3.3 固體物的處置
采用“熱萃取/脫水”技術(shù)處理后,污泥中的油及固體物全部轉(zhuǎn)移至溶劑油中,對于固體物的處置,可根據(jù)實(shí)際情況,采取如下幾個途徑加以利用。
固體物與溶劑油分離,直接作為焦化裝置進(jìn)料或急冷油,固體物轉(zhuǎn)化為焦炭,這樣做的缺點(diǎn)是,“熱萃取/脫水”裝置需要不斷補(bǔ)充新鮮溶劑油。
固體物與溶劑油實(shí)施固液分離,對溶劑油進(jìn)行循環(huán)使用。分離后的固體物,不僅體積非常少,而且具有較高的熱值(8452.1Cal/g),采用如下方式很容易實(shí)現(xiàn)無害化處理。
(1)焦化原料混合送至焦化裝置,形成有價值的產(chǎn)品。
(2)采用輕質(zhì)溶劑洗滌或蒸汽吹脫方式,將殘留的油提取出來,形成無害化固體。
(3)作為燃料使用,如煉油加熱爐、熱電廠其它加熱燃燒設(shè)備的燃料。
4 技術(shù)特點(diǎn)與經(jīng)濟(jì)分析
4.1 技術(shù)特點(diǎn)
含油污泥中的水,不僅決定污泥體積的大小,同時也是影響污泥處理的關(guān)鍵。不同來源的污泥,污泥中的存在形式也是不同的。煉油廠“三泥”經(jīng)加藥與機(jī)械脫水后,含水量一般在80%~85%左右。其中水的存在形式,除少量為游離水外,大部分是以間隙水和內(nèi)部結(jié)合水或附著水的形式,與固體物、油包裹在一起,并在固體物與油表面形成具有強(qiáng)烈憎油性的水化膜,常規(guī)的方法難以實(shí)現(xiàn)油、水及固體物的徹底分離。
“熱萃取/脫水”技術(shù),是一種控制水的溶劑萃取工藝,它不僅可以實(shí)現(xiàn)水與油及固體物的徹底分離,而且為污泥中有價值組分的全部回收與再利用打下良好的基礎(chǔ)。該技術(shù)中,溶劑油既是萃取介質(zhì),同時也是稀釋劑和傳熱介質(zhì)。通過脫水,破壞污泥中油及固體表面的水化膜,消除親水性界面對溶劑萃取的阻止作用,可以確保污泥充分地分散于溶劑中,增加油及固體與溶劑的接觸機(jī)會。脫水與萃取同時進(jìn)行,不僅可以提高萃取的傳質(zhì)效率,保證萃取效果的穩(wěn)定性,而且形成的固體物難溶于水,很容易加以處理和利用。而單純的溶劑萃取工藝,卻無法克服油及固體表面水化膜的影響,污泥在溶劑中聚集成團(tuán),無法分散,萃取過程中易形成乳化液,特別是預(yù)脫水后的污泥。
與焚燒及單純的溶劑萃取這兩種典型的工藝相比,“熱萃取/脫水”技術(shù)具有明顯的優(yōu)勢。
(1)可以回收污泥中的油。
(2)溶劑用量低,無需頻繁再生。
(3)處理效果穩(wěn)定。
(4)產(chǎn)生的固體物不含有水,體積僅為原污泥的一小部分,并且可以通過多種途徑加以利用,變廢為寶。
4.2 經(jīng)濟(jì)分析
“熱萃取/脫水”處理工藝的經(jīng)濟(jì)性,與待處理污泥中油及水的含量有直接關(guān)系。不同來源的含油污泥,其組成存在著很大的差異。經(jīng)濟(jì)估算以將不同組成的含油污泥徹底分離成油、水及固體三種獨(dú)立的產(chǎn)生為基礎(chǔ),并與焚燒處理相比較。焚燒處理含油污泥的費(fèi)用,在我國為300~500元/t污泥,在美國為500~1000美元/t污泥。
5 結(jié)論
“熱萃取/脫水”處理技術(shù),是一種 的煉油廠“三泥”無害化處理工藝,具有目前含油污泥常規(guī)處理技術(shù)無法比擬的技術(shù)和經(jīng)濟(jì)優(yōu)勢,該技術(shù)可以將污泥中水分完全脫出,并回收污泥中有價值組分,形成的固體物量僅為原污泥量的一小部分,且具有可利用價值。該工藝操作條件緩和,易于實(shí)現(xiàn)裝置化,可廣泛適用于石油開采及石油化工等行業(yè)的各種含油污泥處理,解決企業(yè)環(huán)保達(dá)標(biāo)問題。