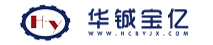
根據(jù)生態(tài)環(huán)境部污染控制規(guī)定,“石油開(kāi)采和聯(lián)合站貯存產(chǎn)生的油泥和油腳”“以礦物油為連續(xù)相配制鉆井泥漿用于石油開(kāi)采所產(chǎn)生的鉆井巖屑和廢棄鉆井泥漿”屬于《 危險(xiǎn)廢物名錄》(2022版)中“HW08廢礦物油與含礦物油廢物”類,油田含油污泥若處理不當(dāng),會(huì)產(chǎn)生嚴(yán)重的環(huán)境污染問(wèn)題。鑒于此,各油田均在嘗試開(kāi)發(fā)含油污泥處理技術(shù),由于含油污泥種類及油田環(huán)境的差異,采取的含油污泥措施也不盡相同。
1 國(guó)內(nèi)油田含油污泥處理技術(shù)現(xiàn)狀及存在的問(wèn)題
1.1 油田含油污泥處理技術(shù)現(xiàn)狀
(1)鉆井廢棄泥漿處理技術(shù)。在油田勘探開(kāi)發(fā)過(guò)程中,鉆井廢棄泥漿的產(chǎn)生量較大,不同的鉆井廢棄泥漿成分的差別也非常大。常用的各類處理方法各有優(yōu)缺點(diǎn),均沒(méi)有徹底解決鉆井廢棄泥漿或占地問(wèn)題,存在污染物轉(zhuǎn)移或隱患等問(wèn)題。固化處理工藝可以在短期內(nèi)取得令人滿意的效果,但是由于各種原因比如外界環(huán)境的侵蝕,會(huì)使得穩(wěn)定性變差,導(dǎo)致污染物質(zhì)浸出,對(duì)環(huán)境造成危害。
(2)含油污泥處理技術(shù)。目前國(guó)內(nèi)各油田對(duì)含油污泥的處理方法主要有高溫處理法、低溫冷處理法、萃取法、調(diào)質(zhì)-脫水法、調(diào)剖回注法、生物處理法、微波處理法、超聲波處理法、化學(xué)氧化法+微生物法修復(fù)技術(shù)等。每種處理方法都有各自的優(yōu)缺點(diǎn)和適用范圍,且由于含油污泥成分復(fù)雜,理化性質(zhì)存在差異性,在實(shí)際應(yīng)用中,處理處置要結(jié)合自身的經(jīng)濟(jì)技術(shù)條件來(lái)選擇處理方式。
1.2 存在的問(wèn)題
(1)近年來(lái),我國(guó)頒布了多部技術(shù)規(guī)范,對(duì)陸上油氣田企業(yè)含油污泥處理處置及污染控制提出了較高的要求,油田及相應(yīng)的技術(shù)服務(wù)企業(yè)需通過(guò)較長(zhǎng)時(shí)間學(xué)習(xí)、理解、消化相應(yīng)的技術(shù)條款。
(2)當(dāng)前國(guó)內(nèi)的研究較多集中在單一含油污泥處理技術(shù)上,但對(duì)分離后剩余的仍含有一定油類物質(zhì)的泥渣處理研究較少,再加上含油污泥處理成本普遍偏高,缺少對(duì)利用技術(shù)的深入探索和高附加值的深度處理,致使國(guó)內(nèi)含油污泥的處置程度普遍較低。
2 油田含油污泥特點(diǎn)及處理現(xiàn)狀
2.1 鉆井廢棄泥漿處理現(xiàn)狀
鉆井泥漿中以COD、重金屬鉻、pH值和石油對(duì)環(huán)境影響較大,其他污染物基本不超標(biāo),主要采用常規(guī)固化處理工藝,堆存量較大。對(duì)接收的廢棄優(yōu)質(zhì)鉆井泥漿進(jìn)行分類處理,經(jīng)振動(dòng)篩、離心機(jī)過(guò)濾后儲(chǔ)存作為可回用鉆井液使用;對(duì)接收的廢棄不可回收鉆井泥漿進(jìn)行固液分離,液相部分處理達(dá)標(biāo)后就地回注處理,固相部分制成免燒磚,用于井場(chǎng)建筑和鋪路。但由于固相含量較大,制磚、墊井場(chǎng)也只能利用一部分。
2.2 井下作業(yè)含油污泥處理現(xiàn)狀
井下作業(yè)含油污泥成分復(fù)雜,處理難度較大。
3 含油污泥處理技術(shù)研究
通過(guò)對(duì)國(guó)內(nèi)油田企業(yè)含油污泥處理技術(shù)進(jìn)行研究與對(duì)比,提出了熱相分離技術(shù)、“預(yù)處理+調(diào)質(zhì)+離心分離”減量化處理技術(shù)和“污油泥-氧化鈣”調(diào)剖體系處理工藝,僅供探討。
3.1 物理法
含油污泥拉運(yùn)至處理站后分類存放于固體接收池和流體污油池,其中流體含油污泥通過(guò)油泥輸送泵進(jìn)入油泥分離機(jī)進(jìn)行處理,固體含油污泥通過(guò)行吊和刮板輸送機(jī)進(jìn)入油泥分離機(jī)進(jìn)行處理。
3.2 焚燒處理工藝
焚燒處理工藝主要處理含油率小于5%的含油污泥,含油污泥經(jīng)預(yù)處理后運(yùn)至焚燒站晾曬場(chǎng),進(jìn)行自然晾曬,待水分蒸發(fā)至含水率小于40%后輸送至篩分裝置進(jìn)一步篩分,篩分出的少量砂石和雜物運(yùn)送至?xí)捍娉?。篩分出的含油污泥加入粘合劑攪拌均勻后,經(jīng)輸送裝置進(jìn)入成型機(jī)壓制成3~5cm的橢圓球狀體后,進(jìn)入焚燒爐焚燒。
3.3 熱解吸處理工藝
熱解吸技術(shù)是指通過(guò)熱交換的方式將污染介質(zhì)及其所含的污染物加熱到足夠的溫度(450~550℃),以使污染物從污染介質(zhì)上得以揮發(fā)或分離的過(guò)程。熱解吸過(guò)程中發(fā)生蒸發(fā)、蒸餾、沸騰和熱解等作用,通過(guò)調(diào)節(jié)溫度可以選擇性的移除不同的污染物。
3.4 “預(yù)處理+超聲-化學(xué)熱洗+脫水”處理工藝
井下作業(yè)含油污泥處理工藝采用“預(yù)處理+超聲-化學(xué)熱洗+脫水”處理工藝,但處理量較小,每小時(shí)處理含油污泥1m3左右,且對(duì)于復(fù)雜的污油泥,達(dá)不到預(yù)期處理效果。
3.5 “螺壓脫水+超熱蒸汽干化”處理工藝
油氣集輸污油泥處理工藝采用“螺壓脫水+超熱蒸汽干化”處理工藝,螺壓脫水機(jī)的處理能力為15m3/h,超熱蒸汽干化裝置的處理能力為600kg/h,處理后的干化殘?jiān)市∮?%,含油率小于1%。但該設(shè)備運(yùn)行過(guò)程中故障率較高,且該工藝未在密閉空間中運(yùn)行,會(huì)產(chǎn)生揮發(fā)性有機(jī)物。
3.6 熱相分離技術(shù)
3.6.1 原理
熱相分離技術(shù)是指通過(guò)熱交換的方式,將污染介質(zhì)及其所含的污染物加熱到足夠的溫度,以使污染物從污染介質(zhì)上得以揮發(fā)或分離的過(guò)程。
3.6.2 處理流程
污油泥經(jīng)過(guò)破碎篩分的物料,用工程車(chē)輛運(yùn)送至進(jìn)料撬,通過(guò)輸送機(jī)進(jìn)入核心熱相分離裝置。通過(guò)高溫間接加熱,使物料中的液相氣化,經(jīng)冷凝液化得到的油水混合物進(jìn)行油水分離,水相進(jìn)入水緩存箱,用作循環(huán)冷卻水使用,油相進(jìn)入油品儲(chǔ)存箱,固相排入還原土臨時(shí)堆場(chǎng),定期進(jìn)行回填處理。
3.6.3 先導(dǎo)實(shí)驗(yàn)效果
(1)先導(dǎo)實(shí)驗(yàn)裝置連續(xù)運(yùn)行8個(gè)月,設(shè)備運(yùn)行正常,向采油廠交油約2000t。
(2)處理后產(chǎn)生的殘?jiān)坏谌綑z測(cè),其石油類含量為1.07g/kg,重金屬因子含量滿足相關(guān)標(biāo)準(zhǔn)要求。
3.6.4 評(píng)價(jià)
(1)環(huán)境評(píng)價(jià):①經(jīng)過(guò)熱相分離技術(shù)處理后的固相含油率達(dá)0.3%~2.0%,廢氣通過(guò)凈化設(shè)備處理后,滿足相關(guān)標(biāo)準(zhǔn)的要求。②節(jié)約了暫存、堆放含油污泥所需的土地資源。③含油污泥通過(guò)熱相分離技術(shù)處理后,分解為原油、水和殘?jiān)糠治镔|(zhì)。水進(jìn)入系統(tǒng)回用:原油進(jìn)入集輸管道銷(xiāo)售;殘?jiān)舷嚓P(guān)環(huán)保要求,可用于通井修路等,既節(jié)約了購(gòu)買(mǎi)砂石料費(fèi)用,又實(shí)現(xiàn)了固體廢棄物的“減量化、資源化、無(wú)害化”處置要求。
(2)經(jīng)濟(jì)效益:經(jīng)濟(jì)效益主要包括環(huán)保節(jié)約費(fèi)用和原油回收效益兩個(gè)部分,按年處理63000t含油污泥計(jì)算,該技術(shù)產(chǎn)生的年經(jīng)濟(jì)效益約為3144.45萬(wàn)元。
(3)技術(shù)評(píng)價(jià):熱相分離技術(shù)已在油田公司進(jìn)行先導(dǎo)試驗(yàn),期間主要處置含油率大于5%的管線刺漏產(chǎn)生的污油泥,從處置效果看,該技術(shù)很適用此種污油泥。
3.7 “預(yù)處理+調(diào)質(zhì)+離心分離”減量化處理技術(shù)
在分析油田公司含油污泥組分特點(diǎn)的基礎(chǔ)上,針對(duì)性地進(jìn)行實(shí)驗(yàn),根據(jù)室內(nèi)研究結(jié)果提出了“預(yù)處理+調(diào)質(zhì)+離心分離”的技術(shù)路線,設(shè)計(jì)出中試設(shè)備并進(jìn)行中試試驗(yàn),通過(guò)處理油泥砂脫水達(dá)到75%以下。經(jīng)脫水后的污油泥量減少到原來(lái)的1/3左右,為后續(xù)的資源化利用和無(wú)害化處置提供了條件。
3.7.1 油泥組分
在油田企業(yè)多個(gè)污水罐、污水池提取含油污泥,外觀呈黑色的粘稠液體,經(jīng)多次取樣分析油泥pH值7~8,密度為1.03g/cm3,含水率85%~95%,固含率2%~7%,含油3%~8%。
3.7.2 室內(nèi)實(shí)驗(yàn)情況
室內(nèi)試驗(yàn)用污油泥取自油田公司聯(lián)合站,含液相(油、水)95%,當(dāng)溫度在65℃,加藥量在300~600mg/L的情況下,NYTS-Ⅱ高效老化污油脫水機(jī)完全適用于目前罐底污油泥處理的要求,可以有效地將油從含油污泥中分離開(kāi),還可以把泥砂減量化處理,具有處理效率高、速度快等特點(diǎn)。
3.7.3 中試試驗(yàn)
(1)工藝原理。本技術(shù)的基本原理是通過(guò)加熱、加藥、均相氣浮和高速離心等方法,改變油、水、砂的分布狀態(tài),降低原油對(duì)泥砂的包結(jié)黏度。通過(guò)機(jī)械篩選,使其大顆粒等雜物在進(jìn)入離心機(jī)前得以分離,減輕高速離心機(jī)的負(fù)荷,提高裝置的處理量,降低單位能耗,同時(shí)使被分離出來(lái)的泥砂含油量、含水率、污水含油率、凈化油含水率達(dá)到設(shè)計(jì)指標(biāo)。
(2)設(shè)備研制。根據(jù)室內(nèi)試驗(yàn)結(jié)果和工藝技術(shù)路線,設(shè)計(jì)出一套撬裝式污油泥處理設(shè)備,以滿足工業(yè)化生產(chǎn)的需要。
(3)污油池中上部懸浮油泥處理。對(duì)油田公司采油廠污油池中上部懸浮油層進(jìn)行處理,其中懸浮油層多為水和油泥聚合物組成,油質(zhì)黏度大,固相含量為3%。
3.8 “污油泥-氧化鈣”調(diào)剖體系
3.8.1 調(diào)剖體系主要原料
固化顆粒與水混合后,在緩凝劑影響下,與水發(fā)生水化反應(yīng),生成各種水化產(chǎn)物,由液態(tài)轉(zhuǎn)變?yōu)楣虘B(tài),主要形成硅酸鹽、鋁酸鹽和鐵鋁酸鹽。
水泥要選擇性能穩(wěn)定,抗硫耐高溫的水泥。膨潤(rùn)土具有規(guī)則的層狀結(jié)構(gòu),層與層之間可以吸附大量的水,使其體積膨脹15倍以上,吸水后的自身懸浮、分散支撐沉降的水泥顆粒,保持水泥體系的穩(wěn)定性。結(jié)合油田地層溫度高的特點(diǎn),單純用水泥與膨潤(rùn)土配合使用,調(diào)剖劑固化后在高溫下會(huì)發(fā)生強(qiáng)度減弱,需向其中加入二氧化硅防止固化后強(qiáng)度減弱,提高調(diào)剖劑抗高溫性能。粉煤灰也是理想的抗高溫填充劑。另外,氧化鈣固化后具有一定的膨脹性能,能防止調(diào)剖體系收縮,也能增強(qiáng)調(diào)剖體系與底層的膠結(jié)作用。
3.8.2 調(diào)剖體系基礎(chǔ)配方實(shí)驗(yàn)
在研發(fā)實(shí)驗(yàn)中,確定調(diào)剖體系的基礎(chǔ)配方為:清水500g+膨潤(rùn)土100g+氧化鈣80g+水泥80g+粉煤灰80g+GH-8緩凝劑8~9g。該調(diào)剖劑1m3的成本約為621元。該體系的稠化時(shí)間可調(diào)節(jié),固化后的抗壓強(qiáng)度達(dá)到2.5MPa以上。
在“污油泥-氧化鈣”調(diào)剖體系稠化時(shí)間達(dá)到要求的基礎(chǔ)上,觀察添加不同含量污泥對(duì)固化強(qiáng)度的影響。從實(shí)驗(yàn)數(shù)據(jù)得出:污油泥添加量越大,調(diào)剖體系固化后的抗壓強(qiáng)度越低。當(dāng)添加160g污油泥時(shí)體系的抗壓強(qiáng)度為1.3MPa,滿足調(diào)剖劑固化后的強(qiáng)度要求,確定“污油泥-氧化鈣”調(diào)剖體系配方為:清水500g+膨潤(rùn)土100g+氧化鈣80g+水泥80g+粉煤灰80g+GH-8緩凝劑9g+含油污泥160g。按照該配方計(jì)算1m3調(diào)剖劑的成本為635元左右。
3.8.3 實(shí)驗(yàn)結(jié)論及建議
(1)污油泥的平均固含量為62.8%,粒徑主要分布區(qū)間為0.9~1.6mm。大于1.6mm粒徑的顆粒占污油泥質(zhì)量的9.68%,大顆粒會(huì)影響泵注,在施工作業(yè)前對(duì)污油泥進(jìn)行過(guò)濾處理。
(2)污油泥中固含量高,對(duì)于嚴(yán)重漏失的溶洞型調(diào)剖井,堵漏階段可以考慮將過(guò)濾后的污油泥直接作為廉價(jià)調(diào)剖劑使用,1m3污油泥成本約為50元;在注入過(guò)程中起壓后根據(jù)本井地質(zhì)情況注入“污油泥-氧化鈣”調(diào)剖劑。
4 油田企業(yè)含油污泥處理思路
油田企業(yè)含油污泥來(lái)源和成分復(fù)雜,處理難度較大,成熟的油田含油污泥綜合處理技術(shù)亟待開(kāi)發(fā)推廣,油田企業(yè)含油污泥處理技術(shù)研究思路應(yīng)向減量化、無(wú)害化、資源化、綜合利用方向發(fā)展。
(1)由于各種處理工藝技術(shù)都有一定的適應(yīng)性和局限性,僅選用單一的技術(shù)很難使含油污泥處理達(dá)標(biāo),應(yīng)根據(jù)含油污泥的不同特性、含油量、來(lái)源及處理的難易程度,加以對(duì)比篩選和綜合考慮,將幾種技術(shù)聯(lián)合應(yīng)用,以提高處理的效果。
(2)拓展含油污泥的綜合利用領(lǐng)域,推廣含油污泥的生物處理技術(shù),培養(yǎng)既能破穩(wěn)又能降解的有機(jī)成分,還能將有害的金屬離子轉(zhuǎn)化為無(wú)害的微生物,降低含油污泥的毒害性。
(3)由于油田企業(yè)含油污泥具有臨時(shí)性和批量性的特點(diǎn),且收集、運(yùn)輸、除油和處理操作難度大,從經(jīng)濟(jì)效益的角度考慮,依托專業(yè)承包商處理含油污泥也是近年來(lái)利用比較多的處理模式。