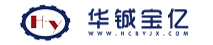
中國城市污水治理率由1995年的19.4%上升到2000年的47%,這個趨勢還會在今后幾年里繼續(xù)保持。即使發(fā)展了新的污水處理技術(shù),以極大限度地減少污泥的產(chǎn)生,污泥產(chǎn)量不斷增加的趨勢仍是不可阻止的。
污泥的成分非常復(fù)雜,含有很多病原微生物、寄生蟲卵及重金屬等,必須進(jìn)行適當(dāng)?shù)奶幚恚拍鼙WC污水的處理效果,避免更嚴(yán)重的二次污染。我國現(xiàn)階段污泥的處置方法普遍是堆積,填埋。這些污泥的堆放不僅占用了大量的土地,而且還將對環(huán)境產(chǎn)生巨大的危害。用 的技術(shù)對污泥進(jìn)行無害化處理,使其達(dá)標(biāo)排放回歸大自然,這將是目前急待解決的課題;同時(shí)也將實(shí)現(xiàn)污水廠對污水、污泥徹底處理,不再留尾巴。
污泥焚燒需要耗費(fèi)大量重油而不經(jīng)濟(jì),并造成大氣污染,浪費(fèi)資源,焚燒這種不得已而為之的方法已越來越不被人們采用。但可以采用高溫堆肥技術(shù)對城市污泥進(jìn)行無害化處理,但由于堆肥占地面積大,處理時(shí)間長,所以歐洲等發(fā)達(dá) 現(xiàn)逐漸采用污泥干化技術(shù)處理污泥,使污泥處理達(dá)到工廠化、自動化、高效化等特點(diǎn)。
1 污泥干化方法比較
1.1 滾筒干化器
滾筒干化器是一個水平直接干化系統(tǒng)。煙氣在爐膛內(nèi)加熱后輸入干燥器,和濕污泥直接接觸,完成熱交換。這套系統(tǒng)有三個主要不足:含氧量高,有失火和爆炸的危險(xiǎn);大量氣體被送入氣味控制系統(tǒng),氣體消耗量大:能耗高。
1.2 流化床
在流化床干燥器的整個底部斷面均勻地吹進(jìn)流化氣
體,使其內(nèi)部形成流化層。隨著污泥逐漸干化,密度減小,升到上部,然后隨上部抽走的氣體而抽出流化床。因污泥的成分決定其流化特性,這套系統(tǒng)對污泥的成分變化非常敏感,常導(dǎo)致流化床內(nèi)的熱交換不能順利進(jìn)行。流化床及管道的磨損很嚴(yán)重。這套系統(tǒng)的能耗也很高。
1.3 薄膜干化器
這套間接干化系統(tǒng)可跨越塑性階段來干化污泥。污泥被投入快速旋轉(zhuǎn)的機(jī)器中(一般轉(zhuǎn)速為100RPM,外徑線速度為8m/s)。污泥被甩到殼體的內(nèi)壁上,形成一層薄膜,殼體外部通入蒸汽或熱油加熱干燥污泥。刀片將污泥刮下來,送出干化器。當(dāng)污泥干性成分大于80%時(shí),設(shè)備磨損很嚴(yán)重。目前污泥干化很少采用此形式。
1.4 臥式圓盤干化器
圓盤式干化機(jī)只能采用蒸汽這種標(biāo)準(zhǔn)加熱介質(zhì),設(shè)計(jì)壓力在蒸汽一側(cè)正常達(dá)到8-12巴,它的構(gòu)造為一個固定體形成一個水平外殼,其內(nèi)部旋轉(zhuǎn)部分由一個管狀空心軸,軸上固定一些空盤,盤中充滿蒸汽等組成,還有一些攪拌葉片用于輸送物料。熱媒介通過中心軸進(jìn)入圓盤,同時(shí)被分配到旋轉(zhuǎn)體中,其原理是由于冷凝產(chǎn)生真空使其流動,因此每個盤充滿蒸汽,保證具有完全的加熱表面,使其達(dá)到較大溫度。該方法的缺點(diǎn):干化產(chǎn)品的含塵量極大,須另加單獨(dú)的造粒系統(tǒng)。用于完全干化時(shí),設(shè)備極易磨損。由于我國污泥中含砂量大,對設(shè)備磨損嚴(yán)重。使用壽命只能達(dá)到2萬小時(shí)。
2 立式多盤干燥器的研究
采用晶核涂層式造粒技術(shù),利用污泥特殊的蒸發(fā)曲線,制備城市污水污泥的硬質(zhì)顆粒,使污水處理廠在實(shí)現(xiàn)污水達(dá)標(biāo)排放的同時(shí),能安全無二次污染,并且節(jié)約能源,生產(chǎn)污泥顆粒化產(chǎn)品是本項(xiàng)目的基本原理?,F(xiàn)分析如下:
2.1 污泥蒸發(fā)脫水特征
經(jīng)過實(shí)驗(yàn)及研究分析得出:污泥干化能耗與污泥含水率的關(guān)系曲線。可見脫水污泥含水率由80%到60%這一段,所消耗能量小,同樣含水率在35%以下繼續(xù)干化消耗能量也小。污泥在含水率60-35%之間,為污泥的塑性階段,這階段污泥的流體特性類似膠水,膠狀,粘稠,很難處置,這階段干化消耗能量急劇增加,并且很難干化。根據(jù)上述特性,干化污泥要避開污泥塑性階段。要充分利用污泥干化特性,盡量在含水率60%以上,35%以下干化,我們把含水率80-60%之間干化叫半干化,含水率35%以下烘干為完全干化。
本研究的關(guān)鍵技術(shù)是分別采用完全干化方式,對城市污水污泥進(jìn)行顆粒化。因而,該技術(shù)有明顯的節(jié)能效果,可稱之為高效污泥干化技術(shù)。
2.2 晶核涂層技術(shù)
再循環(huán)的干化后的小顆粒,在外層不斷涂覆機(jī)械脫水濕污泥薄層。已經(jīng)干化的物質(zhì)形成一個內(nèi)核,濕污泥不斷涂覆,從而形成顆粒。這個顆粒形成的過程十分重要,因?yàn)橥扛埠蟮念w粒外面是濕的,而內(nèi)部卻是干的,送入干化機(jī)后將完全干化。
采用晶核涂層技術(shù)的主要優(yōu)點(diǎn):
①克服污泥粘結(jié)特性,由于有晶核支持,到粉碎分離,不會越攪越粘。
②增大蒸發(fā)表面積,提高熱效率。
③避免傳統(tǒng)污泥烘干中形成的巧克力夾心式顆粒,即外表干化,里面心是軟的,不易進(jìn)一步干化的狀態(tài)。
2.3 立式多盤干化機(jī)工藝研究
通過對污泥干化的所有流程的研究,其設(shè)計(jì)工藝流程如下。
污水廠的污泥運(yùn)輸?shù)轿勰嗵幚韽S,傾倒在“污泥接收槽”中,污泥通過”污泥接收槽”底部的破拱裝置及多螺旋污泥輸送機(jī)輸送到“污泥儲存?zhèn)}”中,通過污泥儲存?zhèn)}底部的破拱裝置及污泥泵輸送到”污泥涂層機(jī)”與回填料(含水率為10%)的混合,該設(shè)備保證混合均勻,位于盤式干燥機(jī)的頂部。涂層機(jī)內(nèi),再循環(huán)的干化后的小顆粒,在外層不斷涂覆機(jī)械脫水濕污泥薄層。已經(jīng)干化的物質(zhì)形成一個內(nèi)核,濕污泥不斷涂覆,從而形成顆粒。這個顆粒形成的過程十分重要,因?yàn)橥扛埠蟮念w粒外面是濕的而內(nèi)部卻是干的,送入造粒機(jī)后將會完全干化。使含水率達(dá)到35%從而避開污泥的塑性階段,進(jìn)入該盤式干燥機(jī)。
2.4 工作原理及結(jié)構(gòu)
立式多盤干化機(jī)是一個間接的預(yù)混合立式多級轉(zhuǎn)盤造粒機(jī),是干化和造粒一步完成的工藝。產(chǎn)出的顆粒干性成分可達(dá)90%。
該設(shè)備內(nèi)部是由一系列的水平放置的圓盤組成,通過一個閉循環(huán)的熱油系統(tǒng)加熱圓盤。該干燥器上面一層是小圓盤,第二層為大圓盤,中間有孔,而后小盤大盤依次交替排列。操作時(shí)位于干燥器中心的主軸在電機(jī)帶動下,連同固定在主軸上的耙臂、耙葉一起轉(zhuǎn)動。
干燥物料由加熱介質(zhì)經(jīng)盤面?zhèn)鲗?dǎo)的熱量加熱升溫后,由小加熱盤外緣跌落到下一層大加熱盤外緣下一層小加熱盤內(nèi)緣盤面上。如此內(nèi)外交替,物料逐層自上而下移動,被加熱干燥。然后在下一層加熱盤上被耙葉刮到底部卸料口處連續(xù)排出,成為合格的干燥產(chǎn)品。汽化的濕分由干燥器頂部出口自然排除或由抽風(fēng)機(jī)引出。
3 結(jié)論
對立式多盤干燥機(jī)進(jìn)行研究發(fā)現(xiàn)該設(shè)備具有如下的優(yōu)點(diǎn):
3.1 堅(jiān)硬的圓狀顆粒
無塵;徹底殺滅病原體;處理安全簡便;能更加改良土壤性;粒徑分布范圍窄;無須特殊的粒度分配設(shè)備。
3.2 干燥和造粒一步完成
無須獨(dú)立的造粒機(jī),所需設(shè)備更少,操作及維護(hù)費(fèi)用更低,更安全。
3.3 靈活
安全,適合于處理各種污泥:城市及工業(yè)污泥,初級,生物處理,生污泥,消化污泥等。
3.4 安全
造粒機(jī)中氧氣含量非常低;平穩(wěn)及低溫干燥;只有無塵顆粒才能消除污泥顆粒處置過程中的粉塵爆炸的危險(xiǎn)。
3.5 熱能消耗低
蒸發(fā)過程無須流動空氣-間接式干燥的優(yōu)點(diǎn);熱交換效率高。
3.6 電能消耗低
特殊的干燥/造粒機(jī)設(shè)計(jì);低摩擦,無腐蝕。
3.7 設(shè)備緊湊
立式布置,減少土建工作量;干燥/造粒過程集于一個工藝過程中。蒸汽處理單元-間接干燥的另一優(yōu)點(diǎn)。
3.8 維修成本低
簡單即是美-減少了輔助設(shè)備;使用經(jīng)過應(yīng)用實(shí)踐證明的材料;維修人員容易接近運(yùn)轉(zhuǎn)部件;無在其它裝置中常見的磨損及腐蝕問題。
3.9 自動化程度高
3.10 對環(huán)境友好
除臭率高。產(chǎn)生臭氣經(jīng)過生物除臭系統(tǒng)除臭,除臭率很高,運(yùn)行成本低。
無噪音。因?yàn)椴幌裰苯痈稍镄枰笮凸娘L(fēng)機(jī),噪音主要為電機(jī)驅(qū)動裝置,系統(tǒng)可安靜運(yùn)行,完全可達(dá)到 要求,并且噪音等級可通過車間隔音來控制。
無灰塵。因?yàn)榇烁稍餅殚g接干燥及輕柔干燥,不會產(chǎn)生很多粉塵,同時(shí)干燥機(jī)內(nèi)有輕微的副壓,并且系統(tǒng)在車間外有除塵系統(tǒng),因此灰塵不會溢出到環(huán)境中。零排放系統(tǒng):無噪音,無氣味,無粉塵。
因此,立式多盤干燥機(jī)是污泥脫水技術(shù)較理想的設(shè)備。