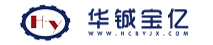
制藥生產(chǎn)的發(fā)酵料液有其特殊性,主要的特點是菌絲濃度高、黏度大。陶瓷膜在制藥生產(chǎn)中主要應(yīng)用在預(yù)處理方面,它可以得到澄清甚至是除菌的濾液,經(jīng)不斷地頂洗后渣體僅保留相當?shù)偷膯挝?,理論上可以得出比板框過濾更高的提取效率。國內(nèi)廠家也開發(fā)出了自己的產(chǎn)品,相對于國外同類產(chǎn)品具有價格低廉,配件供應(yīng)及時等優(yōu)勢。但如果在選型和設(shè)計上稍有失誤,便會在使用效果上大打折扣。
首先是管路系統(tǒng)設(shè)計不合理,一個膜殼組件里裝有19支長度為1m的膜芯,每支膜芯有19個孔,通道孔徑為4mm,每組3個膜殼串聯(lián),并聯(lián)3組,總面積為40.8㎡,總通道截面積為0.0136㎡。儲料罐的料液經(jīng)循環(huán)泵送往陶瓷膜再回流回料罐,為了保持2m/s的切面流速,每小時的回流量在100m3以上,這樣供料管和回流管的管徑就不得不做得很大,安裝時跨度大一點,光管路的死體積就會達到1m3以上,不利于提高收率。同時,回流量大也增加了料液與空氣的接觸機會,這對于易氧化的品種是極為不利的。這樣的設(shè)計也造成了在料液回流的過程中有相當一部分電能消耗在克服勢能的做功上,造成了浪費。
相比之下,國外同類產(chǎn)品的內(nèi)循環(huán)設(shè)計顯得高明。大部分料液在自身循環(huán),僅分出小部分料液回流,因此,只需用一臺小功率的輸送泵補充料液即可。這樣,供料管路和回流管路的管徑可以做得更小,減少了料液的死體積;料液和空氣接觸的機會也減少了,降低了氧化的可能性;電能無謂的浪費也減少了不少;料液儲罐和膜機組的距離也可以適當拉長,給設(shè)備安裝留下了更多的靈活余地??梢娨粋€小小的改動是有相當多的好處的。
其次,在膜芯通道孔徑的選擇上是值得探討的。膜芯一般長1000mm,當中分布著小孔徑的通道。如果膜芯采用7孔,通道孔徑為6mm,每個膜殼同樣裝19支膜芯,總面積只有22.6㎡,總通道截面積為0.0113㎡。同樣的設(shè)計,采用6mm膜芯時為了達到同樣的過濾面積,設(shè)備數(shù)量要增加1.8倍,泵的流量要增加1.7倍,表面上看,設(shè)備費用和運行費用均大大上升。但采用4mm通道的膜芯若使用不當,會有很大的風險。一般陶瓷膜都是帶渣運行的,制藥生產(chǎn)中發(fā)酵菌渣的黏度一般較大,有的還有絲狀的東西,發(fā)酵原料中也有不少顆粒雜質(zhì)。特別是越到后期,渣濃度越高,如不及時加水稀釋,很容易造成通道堵塞。堵塞后的結(jié)果是災(zāi)難性的,先要把大口徑的管道拆開,然后把一級級的膜組件卸下,堵塞不嚴重的還可以用高壓水槍沖通,嚴重的還要拆出在高溫中燒烤才能疏通,一個維修下來,工作量相當大。加水過早又會使濾液體積和操作時間大幅度增加,不利于提高收率。而6mm孔徑的孔道堵死的可能性就大為減少,即使堵死了,也容易沖通。因此,對于菌絲濃度高,黏度大的品種,還是推薦使用孔徑為6mm的膜芯,同時要采用有效的預(yù)過濾器濾除粗顆粒對膜芯加以保護。
再次,在選型和設(shè)計時還要考慮到方便維修和安裝。維修時從3m高的平臺上將重百來斤的組件抬上抬下,是相當累的,在上下鐵梯時還容易出工傷事故,少一級,安裝維修都方便許多。國內(nèi)的陶瓷膜既然維修頻率比國外高,做成三級對維修就更不方便了。同時級數(shù)過多,對于菌絲濃度高、黏度大的品種很容易因為阻力的增加而導致膜芯堵死,并且由于流體在經(jīng)過膜芯時因為阻力作用壓力逐級減少,膜滲透速度要慢得多,不利于充分發(fā)揮設(shè)備的生產(chǎn)能力。因此,對于菌絲濃度高、黏度大的品種以采取兩級串聯(lián)為佳。
在循環(huán)泵的選用上要引起重視,由于循環(huán)泵的流量大,又要帶渣運行,使用過程中噪聲大,機械密封也容易損壞,是一個維修頻率較高的地方。這么大流量的泵在輸送水時漏一點還可以容忍,在輸送料液時泄漏損失可就大了。同時過大的噪聲也是令人難以忍受的。因此這個泵一定要選好,同時要考慮到便于維修。
考慮到在制藥行業(yè)中用到陶瓷膜的地方往往是高附加值的產(chǎn)品,使用廠家更希望的是經(jīng)久耐用、性能優(yōu)越、故障率低的設(shè)備。國內(nèi)廠家要想在競爭中取勝,不僅需要成本優(yōu)勢,更需要以良好的設(shè)計、優(yōu)良的品質(zhì)來贏得市場的認可。使用單位的工藝人員也要和膜科研制造人員密切溝通,爭取使設(shè)備達到較佳的使用效果。