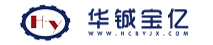
在工業(yè)化生產(chǎn)過(guò)程中存在著許多的液-固、液-液、液-液-固分離物料,特別是液-固、液-液兩相密度差很小或固體顆粒較小的情況下,僅僅采用重力沉降是不能滿足要求的,而采用離心分離的方法就很容易得到解決。離心分離可實(shí)現(xiàn)連續(xù)操作、增大生產(chǎn)能力、提高分離效果、降低勞動(dòng)強(qiáng)度以及提高生產(chǎn)效率等。碟式分離機(jī)具有較高的分離因數(shù),可用來(lái)進(jìn)行凈化、澄清和濃縮分離,是高性能的分離機(jī)械,廣泛應(yīng)用于石油化工、醫(yī)藥、輕工、船舶、食品等行業(yè)。國(guó)外碟式分離機(jī)的發(fā)展迅速,如瑞典Alfalaval和德國(guó)Westfalia的碟式分離機(jī)在分離技術(shù)方面具有國(guó)際領(lǐng)先水平。我國(guó)碟式分離機(jī)是從六十年代初開始,在引進(jìn)、測(cè)繪國(guó)外碟式分離機(jī)的基礎(chǔ)上逐步發(fā)展起來(lái),消化吸收了國(guó)外先進(jìn)技術(shù),并通過(guò)不斷改進(jìn)創(chuàng)新,形成了具有自主技術(shù)的碟式分離機(jī)系列化產(chǎn)品。但實(shí)際生產(chǎn)過(guò)程中經(jīng)常會(huì)出現(xiàn)物料不同分離效果不理想的情況,本文主要從碟式分離機(jī)的自身結(jié)構(gòu)、使用工況及過(guò)程工藝參數(shù)來(lái)分析影響分離效果的因素。
一、碟式分離機(jī)分離原理
碟式分離機(jī)轉(zhuǎn)鼓內(nèi)有一組碟片,把轉(zhuǎn)鼓空間分成許多薄層分離空間,從而大大縮短沉降距離,改善和提高分離效果。
物料經(jīng)進(jìn)料管沿轉(zhuǎn)鼓中心進(jìn)入分配器,通過(guò)分配器孔進(jìn)入碟片,液體以薄層在碟片間沿徑向流動(dòng),輕相流向轉(zhuǎn)鼓中心經(jīng)輕相流道由輕液向心泵排出,重相流向轉(zhuǎn)鼓壁經(jīng)重相流道由重液向心泵排出,沉渣沉積在轉(zhuǎn)鼓壁上經(jīng)活塞排渣間歇排出。
二、影響分離效果的因素
2.1 分離機(jī)自身結(jié)構(gòu)的影響
2.1.1 分離因數(shù)
分離因數(shù)是指顆粒在離心力場(chǎng)中沉降速度與在重力場(chǎng)中沉降速度的比,分離因數(shù)是分離機(jī)分離性能的重要指標(biāo),分離機(jī)的分離因數(shù)越高,物料就越易被分離,分離效果越好。其計(jì)算公式如下:
F=w2R/g
式中:w-分離機(jī)的回轉(zhuǎn)角速度(r/s)
R-分離機(jī)的內(nèi)半徑(m)
S-重力加速度,g=9.81m/s2
從上式可以看出,提高轉(zhuǎn)速比增大轉(zhuǎn)鼓直徑更有利于提高分離因數(shù)。例如,針對(duì)含某菌絲的物料進(jìn)行分離時(shí),由于菌絲顆粒度在0.5~1μm之間較難分離,采碟式分離機(jī),其分離因數(shù)高達(dá)10000以上,能夠?qū)⒕z從發(fā)酵液中分離出來(lái),而用其他離心機(jī)就很難達(dá)到要求。
2.1.2 碟片分配孔
對(duì)于液-液分離,碟片分配孔的位置是影響輕、重相分離效果的一個(gè)重要參數(shù)。分配孔位置偏向中心或偏離中心,物料進(jìn)入分配孔就容易破壞已形成的分離液界面,影響分離效果。分配孔位置偏向中心,輕相就會(huì)含較多的重相組分,相反分配孔位置偏外,重相就會(huì)含較多的輕相組分。
2.1.3 碟片間距
碟片間距應(yīng)使物料中的顆粒在碟片間運(yùn)動(dòng)時(shí)來(lái)得及穿過(guò)液流面達(dá)到上碟片的下表面;同時(shí)在碟片表面沉降臨界直徑的顆粒不會(huì)重新被液流所帶走。
2.1.4 碟片半錐角
碟片半錐角即碟片母線與軸線的夾角α應(yīng)滿足tanα>f的條件,f為沉渣對(duì)碟片表面的摩擦系數(shù)。α角太小,顆粒貼在碟片下表面不能分離,一般在30°~45°范圍內(nèi)。
2.1.5 碟片表面粗糙度
液體在高速旋轉(zhuǎn)的轉(zhuǎn)鼓內(nèi)流動(dòng)是較為復(fù)雜的湍流流動(dòng),碟片表面的粗糙度影響液體的流動(dòng),表面摩擦系數(shù)f增大也將阻礙顆粒在表面向外圓的移動(dòng)。表面的粗糙度越大,摩擦系數(shù)增加,流動(dòng)阻力增大,改變顆粒在碟片間流動(dòng)的路線,就會(huì)導(dǎo)致一些理論上能分離出來(lái)并能到達(dá)上碟片下表面的顆粒不能到達(dá)碟片外圓,而被液流帶走,影響分離效果。例如碟片在實(shí)際生產(chǎn)中采用旋薄技術(shù)成形,碟片的內(nèi)外表面比采用沖壓成形碟片光滑,較大限度地降低碟片表面粗糙度對(duì)流體的影響。一般來(lái)說(shuō),碟片內(nèi)外表面經(jīng)拋光處理后,其粗糙度不大于1.6μm。
2.2 分離機(jī)的使用工況及過(guò)程工藝參數(shù)的影響
2.2.1 重力環(huán)口徑
調(diào)整重力環(huán)口徑就是改變重相出口口徑,調(diào)整輕、重相的分離界面,使物料進(jìn)入碟片分配孔分離時(shí)不致破壞已形成的分離界面,以達(dá)到較佳的分離效果。重力環(huán)口徑變大,由于輕、重相離心液壓的平衡,分離界面往碟片外移動(dòng),輕相中含重相就越少;反之重力環(huán)口徑變小,分離界面往碟片中心移動(dòng),重相液含輕相就越少。
2.2.2 液位環(huán)口徑
調(diào)整液位環(huán)口徑就是改變輕相出口口徑,調(diào)整輕、重相的分離界面,使物料進(jìn)入碟片分配孔分離時(shí)不致破壞已形成的分離界面,以達(dá)到較佳的分離效果。液位環(huán)口徑變小,由于輕、重相離心液壓的平衡,分離界面往碟片外移動(dòng),輕相中含重相就越少;反之液位環(huán)口徑變大,分離界面往碟片中心移動(dòng),重相中含輕相就越少。
2.2.3 出口壓力
出口壓力用來(lái)調(diào)整輕、重相的分離界面,增加輕相的壓力就會(huì)將分離界面向重相層方向移動(dòng),得到澄清的輕相。反之,增加重相的壓力就會(huì)將分離界面向輕相層方向移動(dòng),得到澄清的重相。
2.2.4 排渣時(shí)間間隔
對(duì)于間隙排渣碟式分離機(jī),其排渣時(shí)間間隔要根據(jù)物料含固量的多少來(lái)確定,如人工除渣分離機(jī)要定期進(jìn)行清渣處理,部排或全排分離機(jī)要定期進(jìn)行排渣操作,否則固相會(huì)積滿渣腔,甚至?xí)氯g隙,影響分離效果。
2.2.5 物料分離溫度
溫度對(duì)物料分離的影響是很大的,物料黏度是隨溫度變化而變化的。溫度升高,物料的粘度降低,越有利于物料的分離;溫度降低,物料的粘度升高,就會(huì)影響物料的分離。因此溫度的控制有利于分離過(guò)程的穩(wěn)定,應(yīng)避免產(chǎn)生波動(dòng)。尤其對(duì)粘度隨溫度變化較大的物料,溫度的控制至關(guān)重要,例如重油的分離溫度在95℃~98℃、植物油的分離溫度在85℃~95℃,才能使碟式分離機(jī)達(dá)到較佳的分離效果。
2.2.6 物料的攪拌
懸濁液的分離需進(jìn)行充分?jǐn)嚢?,混合均勻,同時(shí)使固體顆粒均勻分散在料液中。對(duì)于在生產(chǎn)過(guò)程中形成的顆粒狀物質(zhì),攪拌緩和均勻不致使形成顆粒被打碎而影響分離效果。選擇合適的攪拌速度和攪拌翅對(duì)物料的分離效果起著重要的作用。例如在植物油精煉中的水化脫膠過(guò)程中,植物油碟式分離機(jī)是利用植物油中磷脂等膠溶性雜質(zhì)的親水性,吸水凝聚成顆粒去除植物油中膠溶性雜質(zhì),植物油進(jìn)碟式分離機(jī)分離前,經(jīng)水化罐并不斷攪拌使磷脂充分凝聚,若攪拌不充分,磷脂不能完全凝聚,或者攪拌劇烈,磷脂凝聚成的顆粒易被打碎,經(jīng)分離后磷脂(即重相)含油率28%~32%。若通過(guò)水化罐的減速機(jī)將攪拌速度控制在70~90r/min,經(jīng)分離后磷脂(即重相)含油率降至25%~28%。因此通過(guò)對(duì)水化過(guò)程攪拌強(qiáng)度的控制,來(lái)提高碟式分離機(jī)的分離效果,提高植物油精煉率。
2.2.7 進(jìn)料穩(wěn)定性
保持進(jìn)料穩(wěn)定很重要,必須避免產(chǎn)生波動(dòng),進(jìn)料的穩(wěn)定在一定程度上保證了分離界面的恒定,一旦產(chǎn)生波動(dòng)就會(huì)破壞分離界面,影響分離效果。
三、結(jié)束語(yǔ)
碟式分離機(jī)對(duì)物料分離效果的好壞,是各種參數(shù)相互制約的結(jié)構(gòu),液體在碟片間流動(dòng)情況及粒子在碟片間運(yùn)動(dòng)情況相當(dāng)復(fù)雜,不僅受到離心加速度的影響,同時(shí)還受到哥氏加速度及液體粘滯阻力的影響。分離機(jī)自身結(jié)構(gòu)的影響還需要在實(shí)際應(yīng)用過(guò)程中不斷探索和積累經(jīng)驗(yàn),根據(jù)不同物料確定其結(jié)構(gòu)。同時(shí)分離機(jī)的使用工況及過(guò)程工藝參數(shù)需要進(jìn)行調(diào)整,選擇合適的工況以及合理的工藝參數(shù)才能達(dá)到較佳的分離效果。