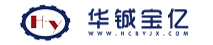
碟式分離機(jī)是一種立式離心機(jī),轉(zhuǎn)鼓裝在立軸的上端,由電動(dòng)機(jī)通過(guò)傳動(dòng)裝置驅(qū)動(dòng)而高速旋轉(zhuǎn),其轉(zhuǎn)速一般在6000~12000r/min之間。由于碟式分離機(jī)工作轉(zhuǎn)速很高,轉(zhuǎn)鼓部件的質(zhì)量偏心會(huì)引起分離機(jī)工作時(shí)的強(qiáng)烈振動(dòng),因此,轉(zhuǎn)鼓部件裝配后應(yīng)進(jìn)行動(dòng)平衡校正,并在規(guī)定的部位去重。通常,第一次的去重量希望小一點(diǎn),以便今后復(fù)較動(dòng)平衡時(shí)有去重的地方,這就必須提高轉(zhuǎn)鼓部件內(nèi)各零件的加工精度。轉(zhuǎn)鼓內(nèi)裝有進(jìn)料分配器和一組層疊在一起的碟形零件----碟片,碟片上點(diǎn)焊有間隔片或間隔條,使組裝在一起的碟片與碟片之間保持很小的間隙。需要分離的物料(懸浮液或乳濁液)通過(guò)位于轉(zhuǎn)鼓中心的進(jìn)料管加入轉(zhuǎn)鼓,經(jīng)進(jìn)料分配器上的分配管均勻地分布到各碟片中間。當(dāng)懸浮液(或乳濁液)在碟片之間的間隙中高速旋轉(zhuǎn)時(shí),因密度不同被分離為重相和輕相,重相在離心力作用下向碟片大端滑移,脫離碟片,積聚在轉(zhuǎn)鼓內(nèi)壁直徑大的部位,形成沉渣(或液層)。輕相則向碟片小端滑移,經(jīng)出液口排出轉(zhuǎn)鼓。碟片的作用是縮短固體顆粒(或液滴)的沉降距離,擴(kuò)大轉(zhuǎn)鼓的沉降面積,提高分離機(jī)的生產(chǎn)能力。
1 碟片的加工工藝分析
由上述可見(jiàn),碟片作為轉(zhuǎn)鼓部件內(nèi)數(shù)量較多的零件(一般為80~150片左右),它的加工精度直接影響到轉(zhuǎn)鼓的動(dòng)平衡和分離機(jī)的使用性能,因此各分離機(jī)生產(chǎn)廠家都十分重視碟片的加工工藝。
碟式分離機(jī)內(nèi)的碟片呈錐形,大端或小端有凸緣,凸緣上開(kāi)有裝配時(shí)定位用的鍵槽。錐面中性層處開(kāi)有供物料通行的進(jìn)液孔,不同用途的分離機(jī)進(jìn)液孔的數(shù)目各不相同,國(guó)產(chǎn)碟片式分離機(jī)的孔數(shù)一般為3~8個(gè)。為了保證裝配后兩碟片間有供分離物料通行的間隙,碟片的錐面焊有間隔片或間隔條。由于碟式分離大多用于食品、醫(yī)藥和化工行業(yè),因此,碟片大多用奧氏體不銹鋼制作,常用的材料有1Cr18Ni9、0Cr18Ni9等,材料的厚度一般為0.5~2mm。根據(jù)碟片的結(jié)構(gòu)形狀及設(shè)計(jì)要求,碟片加工時(shí)常用到的工序有強(qiáng)力旋壓、沖裁、點(diǎn)焊、拋光等。
由于碟片是薄壁件,加工過(guò)程中非常容易變形,因此,各加工工序中變形的控制是保證碟片加工精度的關(guān)鍵所在。下面就強(qiáng)力旋壓和拋光工序作一些分析。
1.1 碟片的強(qiáng)力旋壓
強(qiáng)力旋壓是碟片的成形工序,也是決定碟片質(zhì)量的主要工序。工件旋壓前應(yīng)正確選取旋輪與胎模間的間隙。碟片強(qiáng)力旋壓時(shí),材料每點(diǎn)的變形對(duì)其它未變形部分的影響很小,變形后工件的凸緣尺寸基本上保持原有尺寸。
實(shí)際加工中,由于毛坯的厚度存在偏差,旋輪運(yùn)動(dòng)副中也存在誤差,實(shí)際間隙需在理論計(jì)算值的基礎(chǔ)上作修正,不然碟片的凸緣易起皺(俗語(yǔ)稱(chēng)為“起木耳邊”)、前傾或后倒,并使碟片貼模不好----產(chǎn)生較大的回彈。
所采購(gòu)的板材批次不同,板料厚度會(huì)有偏差,每次旋壓前應(yīng)對(duì)板料毛坯進(jìn)行實(shí)測(cè),取得平均數(shù)據(jù),計(jì)算出碟片的理論壁厚,調(diào)整旋輪與胎模間的間隙時(shí),應(yīng)在理論壁厚的基礎(chǔ)上適當(dāng)減去補(bǔ)償量(不同的旋壓機(jī)補(bǔ)償量是不一樣的,需經(jīng)過(guò)試模取得數(shù)據(jù)),這樣才能旋壓出合格的碟片。
另外,主軸的轉(zhuǎn)速會(huì)影響旋壓件成形表面的粗糙度,選擇轉(zhuǎn)速時(shí)應(yīng)避開(kāi)共振區(qū)。
1.2 碟片的拋光
拋光是碟片加工工藝流程中另一重要工序,碟片的表面質(zhì)量主要通過(guò)拋光工序獲得。碟片的加工工藝流程中一般需安排兩次拋光,第一次安排在點(diǎn)焊之前,對(duì)碟片的內(nèi)外錐面作一次整體的拋光;第二次安排在點(diǎn)焊之后,可拋出間隔片或間隔條的表面,順帶去除點(diǎn)焊時(shí)可能產(chǎn)生的毛刺。
目前不銹鋼零件常用的拋光方法有機(jī)械拋光、電解拋光、電化學(xué)拋光等,每種拋光方法各有優(yōu)缺點(diǎn)。碟片拋光用的較多的是機(jī)械拋光法,有些分離機(jī)生產(chǎn)廠家直接采用手工機(jī)械拋光,具體操作方法:工人手持工件,纖維或布拋光輪加上相應(yīng)的拋光膏,將工件壓在旋轉(zhuǎn)的拋光輪上進(jìn)行拋光,可達(dá)到Ra0.8μm的表面粗糙度。這種拋光法的優(yōu)點(diǎn)是對(duì)設(shè)備要求低,操作簡(jiǎn)單,拋光速度快;缺點(diǎn)是勞動(dòng)強(qiáng)度大,碟片容易產(chǎn)生不規(guī)則變形,影響零件的精度。如果條件允許,可制作一些簡(jiǎn)單的胎模,拋光時(shí)將碟片固定在胎模上進(jìn)行,以防碟片受力變形。也可設(shè)計(jì)專(zhuān)用的拋光機(jī)對(duì)碟片進(jìn)行拋光。
近年來(lái)也有一些分離機(jī)生產(chǎn)廠家嘗試用電化學(xué)拋光的方法對(duì)碟片進(jìn)行拋光。電化學(xué)拋光是利用金屬電化學(xué)陽(yáng)極溶解原理進(jìn)行修磨拋光的,碟片基本上不受外力的作用,拋光過(guò)程不會(huì)產(chǎn)生變形,但需合理選擇電解拋光液的配方、電流密度、拋光溫度及拋光時(shí)間等參數(shù)。
2 結(jié)論
由此可見(jiàn),強(qiáng)力旋壓參數(shù)與拋光方法對(duì)碟片的加工質(zhì)量起著決定性的作用,必須合理選擇。但要加工出高質(zhì)量的碟片,除了需重視上述的工序之外,還應(yīng)注意各道工序中定位基準(zhǔn)的選擇,盡量統(tǒng)一基準(zhǔn),以保證進(jìn)液孔及間隔點(diǎn)或間隔條的幾何精度,使碟片組裝成碟片組后能有較高的裝配精度,進(jìn)而保證轉(zhuǎn)鼓的裝配精度,減小不平衡去重量。